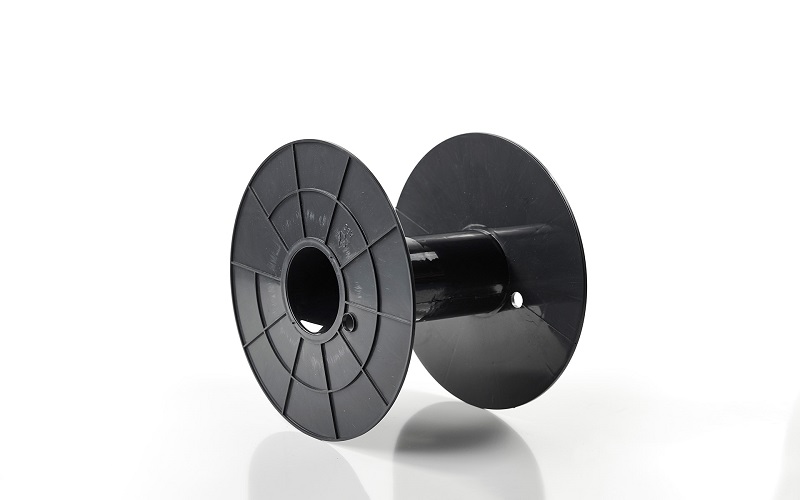
CNC machining is one of the most flexible and widely used manufacturing processes that continue to gain prominence around the world. Manufacturing companies which supply plastic injection molding service, big and small, are slowly adopting the technology for a number of reasons as they position themselves to take full advantage of industrial automation. However, despite its great popularity and reputation, not many people who wish to adopt it know exactly how it works, and this has been a cause for confusion when they try to assimilate it into their process without first understanding how it works.
We are going to explore CNC machining for mold making and how it works, the processes involved, the materials that are used, and how it compares with other forms of manufacturing. For those that have been considering adopting the technology, this could serve you well.
Source: Pinterest
Just like any other process used in manufacturing, there is an order to how CNC machining operates. It goes through well laid down steps that has to be followed if the production is to be a success. These steps include the following.
Designing in CAD: This is the first step in the entire process. It is where the workpiece intended for use is designed using a Computer-Aided Program. There are many CAD programs out there that can be used to get this done. Once the mould design is complete, it is these files and the specifications written into them that will be fed into the CNC machines as the commands to be executed.
Conversation: With the ready CAD file fed into the machine, the file has to be converted into a format that the CNC machine will understand and interpret. To change the CAD file into a CNC-compatible file requires a conversion software called the Computer-Aided Manufacturing program (CAM). The process doesn’t take long, and once the conversation is complete, the file can be saved in the CNC machine and can be accessed at a later date when the need arises.
Machine Preparation: With all the files in place, the machine now has to be warmed up and made ready for work. This is done by a technician who checks if the files are loaded into the machine corresponds to what he has on the display. They also have to align the tools and check if they are in good condition. Anything that needs to be added is attached at this stage, and after another thorough check, things are ready for execution.
Execution: The final part is the most important one as this is where the design comes to life. With everything in position, the operator can now initiate the production process and leave the rest to the machine, which will reproduce the end product based on the strict specifications of the file that was fed into it. Depending on the type of CNC machine in use and the size of the product, the time it takes varies.
Source: Pinterest
Precision Machining is another variation of the basic CNC machining that is more accurate, and for this reason, it is usually relied upon by original equipment manufacturers when it comes to creating products that have never been made before. It is a princess where the machine takes a workpiece and shaves it to the desired shape with very minimal errors.
The process is run by CAM and CAD software that is fed into the machine in different stages. It is the most precise cutting mechanism, and for this, it makes use of the best cutting tools that money can buy. The process is so reliable that it is used in industries that make surgical instruments, aerospace parts, solar and wind components, and other essential parts used in machines and equipment utilized by people in their day-to-day activities.
The materials used in precision CNC machining services are more varied compared to other processes. This makes it a more viable and flexible option that gives manufacturers a wider base to work with. Some of the common materials used for precision machining include aluminum, stainless steel, brass, alloy steel, mild steel, POM, ABS, polycarbonate, PEEK, nylon, glass, graphite, among many other materials.
Source: Pinterest
CNC machine types come in varying shapes and sizes depending on the task they are cut out for. Some are multi-purpose with the ability to be used in many ways. The following are some of the most common CNC machines
Plasma-Cutting Machine: These are machines used for cutting using a special plasma torch that is hot enough to cut through metals in a very clean and precise manner. The temperatures of a plasma beam can vary between 10,000 – 50,000 degrees, depending on the size of the machine.
Milling Machine: These are machines that are equipped with drilling and cutting tools used to alter the shape of workpieces using a computer-aided program. The materials are dropped inside the milling machine, and the cutting and drilling tools handle the rest. CNC milling machines come in three to six-axis configurations.
Lathe Machine: Lathe Machines have the ability to rotate materials while making alterations to them. They come with a fewer number of axles, making them smaller and more compact, making them portable and easy to use. A lathe is what they come equipped right in their centers, whose purpose is for manipulating and moving materials that are added into the machine. These movements are controlled by a computer program.
Laser-Cutting Machine: This is a laser cutting machine that uses a laser beam to cut through tough materials. They are not as strong or hot as plasma torches, but they offer some high level of accuracy. However, they use a lot of energy to cut through things and should only be used when necessary.
CNC Electric Discharge Machine: An EDM machine uses electric sparks to manipulate raw materials into any shape using a special programmable code that’s fed into the machine beforehand. This electrical discharge has erosive power that’s responsible for deforming materials that are exposed to it. The time and the strength of the EDM vary from one machine to another.
Source: Pinterest
CNC machining is transforming manufacturing, and it is the future no matter the many eagles you look at it. The ability to integrate them automation has opened up the door to many possibilities that have ensured manufacturers get as many options at their disposal as possible, and this is beneficial both for them and the consumers.
There are many reasons that make CNC machining a better option already; being profitable, fast, efficient, and flexible are just some of the few. With time, as more developments keep rolling in, this will become better and cheaper to the point where even the small companies will be able to afford the best machines money can offer. There will be more optimizations and the ability to speed up things, especially with the improvement and integration of 3D printing.
CNC machining has come a long way and still has a lot more ground to cover in the future. Technological advances keep coming out every year, and CNC machining is at the center of everything right now. The benefits the process brings to the table are hard to ignore. If you have been thinking of setting up CNC machining in your plant, then don’t hesitate to drop us a call, and we will guide you through the entire process. For more information, check out our website at your own convenience.
Please contact us using the form below or emailing (harry@fowmould.com)