HDPE and ABS are two widely used plastic materials in modern manufacturing, but what exactly sets them apart? And which types of projects are they best suited for?
In the following content, we will delve into HDPE vs ABS, providing a comprehensive analysis of their performance and practical applications, helping you make an informed decision when selecting the right material for your project.
What Is HDPE?
HDPE (High-Density Polyethylene) is a thermoplastic resin produced by polymerizing ethylene monomers through low-pressure processes, such as Ziegler-Natta or metallocene catalysts.
Its molecular structure is primarily linear, with very few branches, resulting in higher density (0.940–0.970 g/cm³), as well as enhanced crystallinity and rigidity.
HDPE offers excellent resistance to acids and alkalis, outstanding electrical insulation properties, and retains good toughness even at low temperatures.
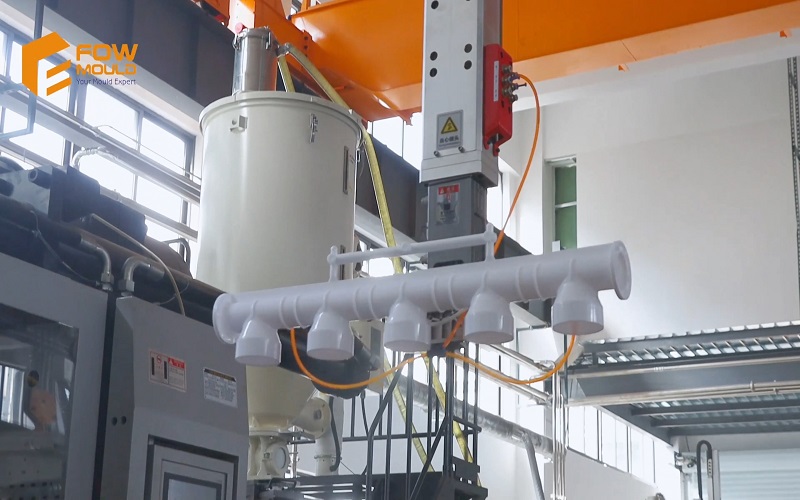
What Is ABS?
ABS material is a terpolymer composed of three monomers: acrylonitrile (A), butadiene (B), and styrene (S).
It is one of the most widely used and highly produced polymers. ABS plastic combines the shared properties of its three components—acrylonitrile, butadiene, and styrene—resulting in excellent mechanical and thermal properties.
With an elastic modulus of 2.2 GPa, ABS maintains stable performance across a temperature range of ‒40°C to 100°C.
Acrylonitrile contributes chemical resistance, heat resistance, and surface hardness; butadiene provides high elasticity and toughness; while styrene enhances the thermoplastic’s ease of processing and improves electrical properties.
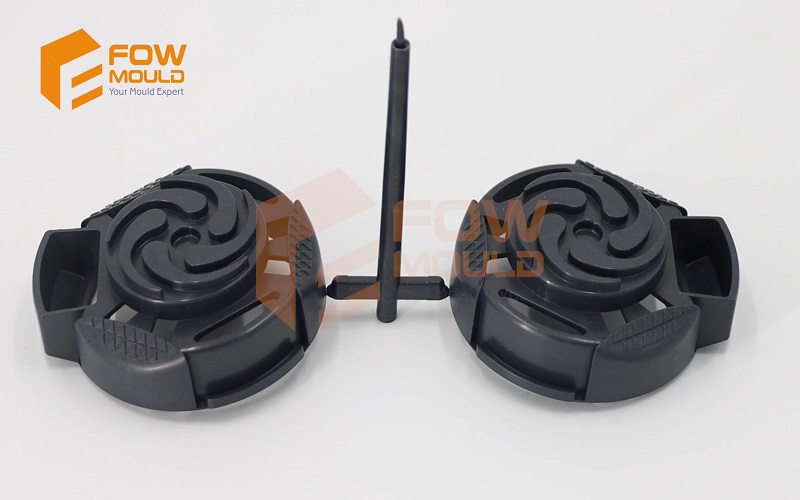
HDPE vs ABS:Property Comparison
Below is a table comparing the physical properties of HDPE and ABS:
Properties | HDPE | ABS |
Density(g/cm3) | 0.941-0.960 | 1.05-1.18 |
Melting Point(℃) | 142 | Amorphous (No clear melting point) |
Tensile Strength(MPa) | 20-37 | 40-50 |
Water Absorption(%) | <0.01 | 0.2–0.4 |
Shrinkage(%) | 1.5–3.0 | 0.4–0.9 |
Impact Strength (J/m) | 117 | 400 |
Heat Deflection Temp (℃) | 300 | 250 |
In terms of physical properties, HDPE exhibits excellent flexibility and electrical insulation, with strong surface hardness and good tensile strength.
It also retains a certain level of resistance even in low-temperature environments.
On the other hand, ABS offers high strength and toughness, a glossy surface finish, and is easy to color and coat. It also boasts good mechanical strength and electrical properties.
Regarding chemical performance, HDPE has strong chemical stability.
At room temperature, it is insoluble in any organic solvents and is highly resistant to corrosion from acids, alkalis, and various salts.
ABS resin is resistant to water, inorganic salts, alkalis, and acids.
It is insoluble in most alcohols and hydrocarbon solvents, but it dissolves easily in aldehydes, ketones, esters, and certain chlorinated hydrocarbons.
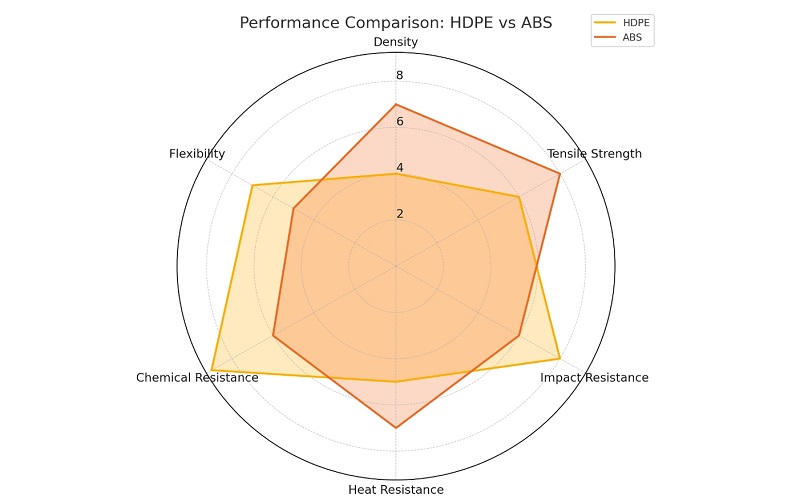
The Manufacturing Method Of HDPE and ABS Material
Processing Methods of HDPE
- Extrusion
HDPE grades used in extrusion typically have a melt index below 1 and a medium-to-wide molecular weight distribution (MWD).
This method is ideal for producing pipes, profiles, and sheets with excellent durability and flexibility.
- Blow Molding
Over one-third of HDPE sold in the United States is used in blow molding applications.
These include manufacturing bottles for bleach, motor oil, detergents, milk, and distilled water, as well as large-scale items like refrigerator liners, automotive fuel tanks, and drums.
This method excels in producing hollow products with high strength and chemical resistance.
- Injection Molding
Widely utilized, HDPE molding is used to create a variety of items ranging from reusable thin-walled beverage cups to 5-gallon containers.
This method is favored for its ability to produce lightweight, precise, and durable products efficiently.
Processing Methods of ABS
- Injection Molding
This is the most common processing method for ABS. It involves heating ABS resin to a temperature of 200°C to 230°C and injecting it into molds.
Maintaining the mold temperature between 45°C and 55°C ensures a smooth, glossy surface finish.
ABS Injection molding is widely used to produce automotive parts, electronic housings, and consumer goods.
- Extrusion Molding
ABS extrusion molding is primarily used for producing pipes, sheets, plates, and profiles.
During processing, the barrel temperature is controlled between 210°C and 235°C, the T-die temperature is maintained at 230°C to 235°C, and the roller temperature is set between 90°C and 100°C.
- 3D Printing
In 3D printing, ABS is commonly used with Fused Deposition Modeling (FDM) technology.
Printing ABS requires a relatively high print bed temperature and an enclosed printing environment to prevent warping and cracking during the cooling process.
Common Applications Of HDPE And ABS
Due to the differences in the properties and processing methods of HDPE vs ABS, their applications also vary significantly.
Applications of HDPE
- Packaging Materials: plastic bags, plastic films, and shrink wraps
- Food Containers: plastic bottles, food storage buckets, and food-grade containers
- Construction Materials: water pipes, drainage pipes, chemical pipelines, agricultural films, and waterproof membranes
- Medical Equipment: medical tubing, surgical instruments, and medical packaging
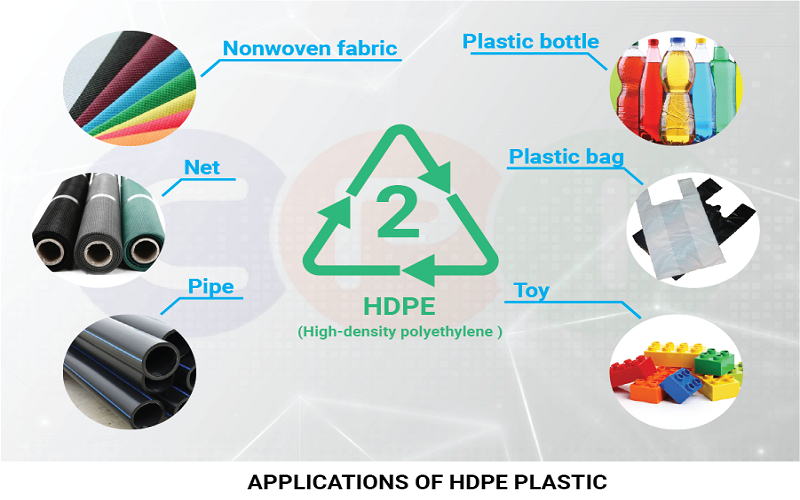
Applications of ABS
- Engineering Plastics: PC/ABSalloys
- Automotive Industry: dashboards, exterior panels, interior trim panels, and bumpers
- Electronics and Appliances: computer casings, keyboards, and printer housings
- Construction Industry: ABS pipes, sanitary fittings, and decorative panels
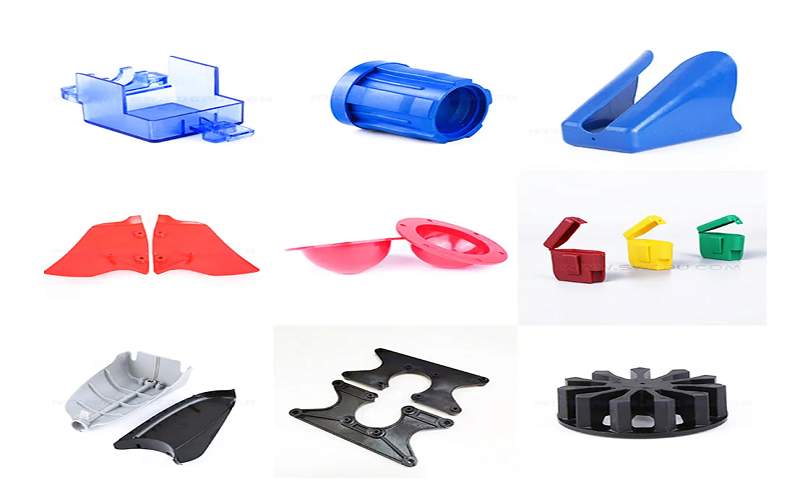
ABS vs HDPE:Environmental Impact
HDPE is a highly recyclable plastic, known for its durability and chemical stability, making it an ideal choice for manufacturing reusable products such as plastic bottles, containers, and pipes.
Its recyclability and wide range of applications contribute to reducing environmental waste.
In contrast, the production of ABS plastic requires significant amounts of petroleum resources and generates substantial greenhouse gases and chemical byproducts, leading to a negative environmental impact.
Additionally, ABS has a long degradation time, accumulating in landfills or the natural environment for extended periods.
This not only consumes valuable land resources but also poses a risk of releasing harmful substances, which can disrupt ecosystems.
Overall, HDPE holds a slight advantage in terms of environmental performance, particularly in its lower impact on the environment and higher recyclability.
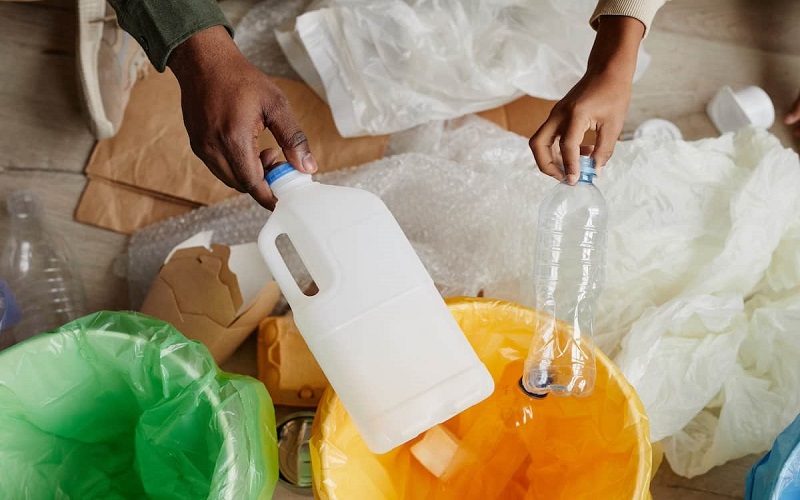
Which is Safer,HDPE or ABS?
HDPE is a non-toxic, odorless material that is resistant to acids, alkalis, and organic solvents, and it typically does not release harmful substances under normal usage conditions. Additionally, HDPE has been approved by regulatory bodies such as the FDA for direct food contact, making it widely regarded as a food-safe material.
It is commonly used for food containers, bottles, and packaging.
ABS, under normal usage conditions, also exhibits good durability and stability, and the material itself is considered safe.
However, untreated ABS is generally not suitable for direct food contact.
At high temperatures, especially above its melting point (approximately 105°C), ABS may release small amounts of volatile organic compounds (VOCs), which pose a potential safety risk.
As a result, ABS is less suitable than HDPE for applications involving high temperatures or direct contact with food.
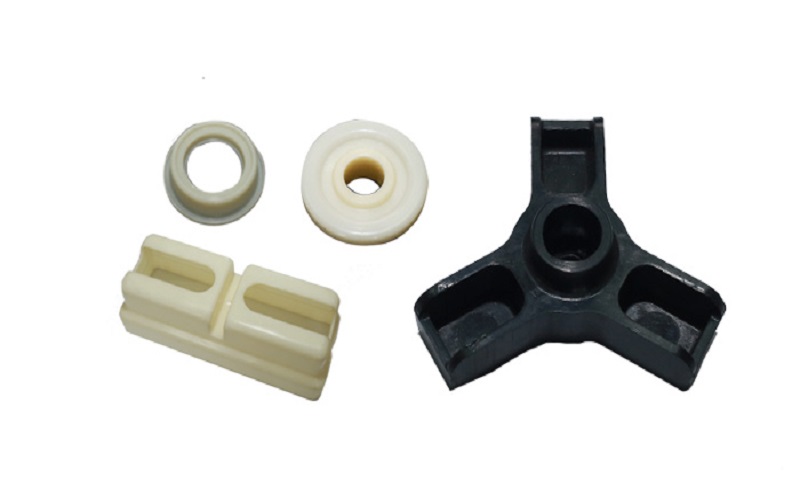
Conclusion
When deciding between HDPE vs ABS plastics, it is essential to consider the specific application requirements.
If you need a material with high strength and excellent chemical resistance, HDPE may be the better choice.
On the other hand, if heat resistance and toughness are priorities, ABS could be the more suitable option.
If you’re looking to start an HDPE or ABS plastic injection molding project, don’t hesitate to contact FOWMOULD.
We are the most trusted plastic injection molding manufacturer in China!