Injection molding, a cornerstone of modern manufacturing, is widely utilized across industries such as automotive, electronics, and medical devices, with its essence lying in the precise transformation of molten plastic into high-quality parts.
At the heart of this process is the gate—the critical “throat” connecting the mold to the product. It not only regulates the flow and filling of plastic but also directly impacts the appearance, strength, and production efficiency of the final part.
It not only regulates the flow and filling of plastic but also directly impacts the appearance, strength, and production efficiency of the final part.
To meet diverse part requirements and material properties, engineers have developed various gate types, each with distinct characteristics and applications.
This article aims to systematically explore the common types of gate in injection molding, dissecting their design principles, advantages, disadvantages, and application scenarios.
It seeks to help readers understand how gate selection serves as a pivotal step in enhancing product quality and process efficiency.
Understanding Injection Molding Gates
An injection molding gate is an opening that controls the flow of molten plastic into the mold cavity.
It acts as a bridge between the runner system and the mold cavity, ensuring that the molten plastic fills the cavity efficiently and uniformly.
The primary purpose of an injection molding gate is to regulate this flow, which is crucial for achieving high-quality molded parts.
Controlling flow through the gate prevents defects like air entrapment, which can cause surface blemishes and compromise the part’s integrity.
A well-designed gate ensures even spread of molten plastic within the mold, preventing premature hardening and avoiding issues like shrinkage or voids.
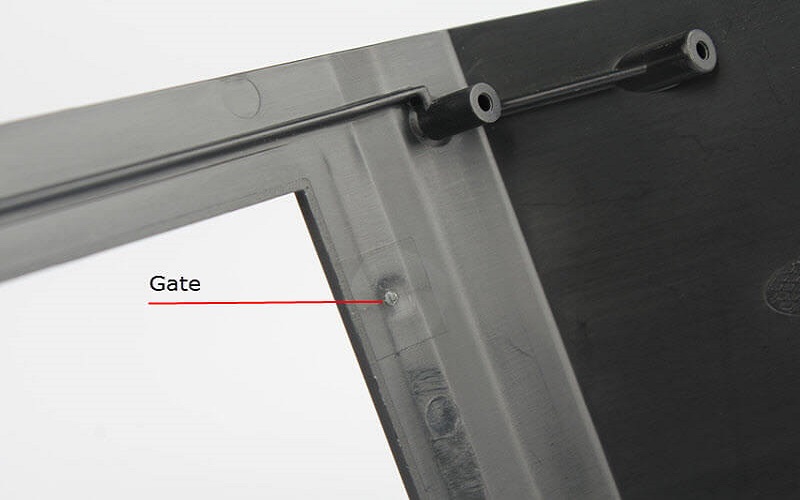
Selection Of Injection Molding Gate Placement
The placement of gates in injection molding is a critical decision that influences part quality, mold performance, and production efficiency.
An optimally positioned gate ensures smooth material flow, minimizes defects, and balances aesthetic and functional requirements. Below are key principles and considerations for selecting the ideal gate location:
Gates should be positioned at the thicker sections of the molded part, allowing molten plastic to flow from thick to thin areas, minimizing pressure loss. The plastic melt should enter the cavity swiftly via the shortest path, with minimal heat and pressure loss, to complete the injection process efficiently.
Gates should be located where they can be easily removed from the part, while avoiding any adverse impact on appearance, such as the formation of flow marks.
The gate position should enable the molten plastic to flow evenly into the cavity in a direction parallel to the mold, facilitating effective venting of trapped gases.
Gate placement should prevent weld lines or flow marks from forming in critical areas of the part, which could compromise its strength.
In multi-cavity molds, the size and position of gates should be determined based on their distance from the main runner and the dimensions of the molded parts.
Gates should be positioned to avoid direct impact of molten plastic on fragile mold cores, inserts, or sliders, preventing deformation of the part.
Gate placement should account for varying shrinkage rates in the transverse and longitudinal directions of the part, ensuring consistent temperature and pressure of the melt entering each cavity from different gates, thus achieving uniform shrinkage across all cavities.
Runner transitions should feature smooth, curved contours, and the connection to the gate should be machined with a slanted surface to enhance the flow of the molten plastic.
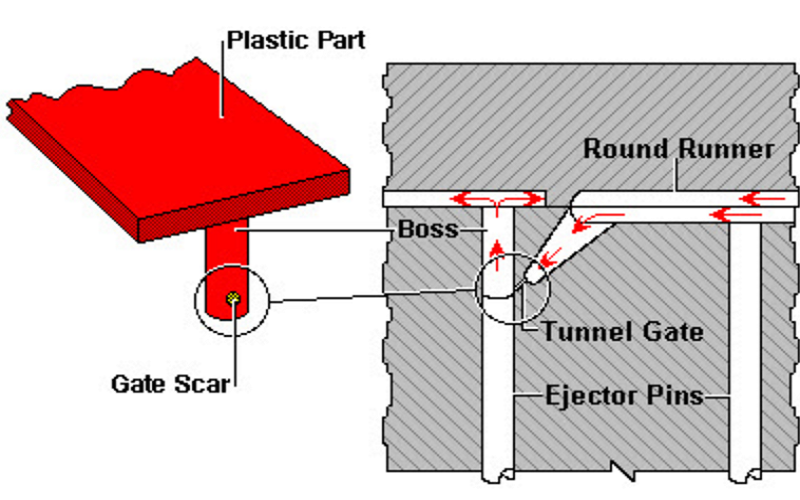
What Is The Role of Gating Injection Molding?
Gates play a critical role in the injection molding process by controlling the flow rate of molten plastic into the mold cavity.
This regulation ensures the plastic completely and uniformly fills the cavity, reducing the likelihood of defects. The gate’s small cross-section accelerates the molten plastic, aiding in the quick and efficient filling of the mold.
Once the mold is filled, the gate solidifies first, sealing to prevent the molten plastic from flowing back out. This sealing action is crucial for maintaining the pressure within the mold cavity, ensuring that the final product is free from defects like shrinkage or voids.
The high shear rate at the gate also improves the flow properties of the molten plastic, enhancing the quality of thin-walled or finely detailed parts.
Selecting an appropriate gate design helps avoid unsightly marks on the finished product. Optimizing gate placement and design can lead to better results in your injection molding projects, ensuring high-quality and aesthetically pleasing molded parts.
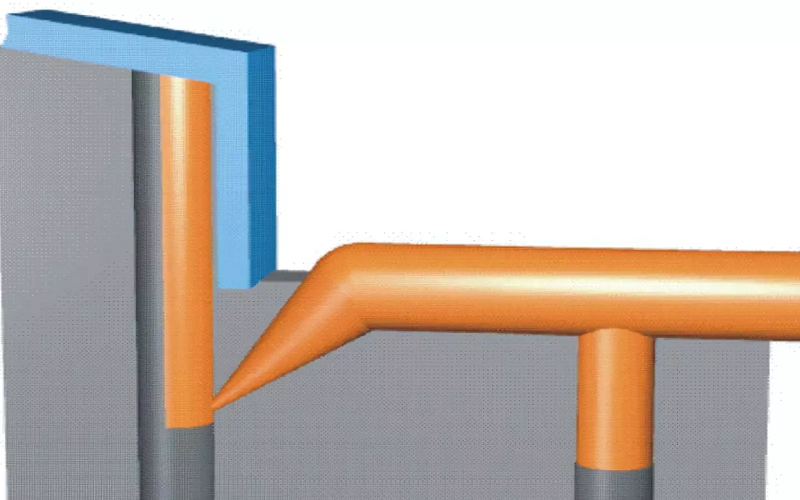
Common Types Of Gates In Injection Molding
Choosing the rightinjection molding gate types influences the mold filling process, part quality, and production efficiency.
There are several types of injection molding gates, each with unique characteristics and suitable applications.
Knowing these types helps make informed decisions, optimizing your molding process and achieving superior results.
Each type will be discussed in detail, highlighting their advantages, disadvantages, and ideal applications.
Direct Sprue Gate
There are several types of injection molding gates, each with unique characteristics and suitable applications.
Knowing these types helps make informed decisions, optimizing your molding process and achieving superior results.Each type will be discussed in detail, highlighting their advantages, disadvantages, and ideal applications.
Direct or sprue gate are economical and simple, often located at the parting line of the mold. In sprue gates, molten plastic flows directly into the mold cavity, ensuring even filling and minimizing the risk of defects.
These gates are characterized by a straightforward design, low injection pressure, and high tensile stress, making them suitable for manufacturing large parts or high-volume materials.
Commonly used in products like household appliances and consumer electronics, direct gate or sprue gates offer fast injection and efficient production. However, one notable disadvantage is that they can leave visible marks on the finished parts, which may affect the product’s aesthetic appeal.
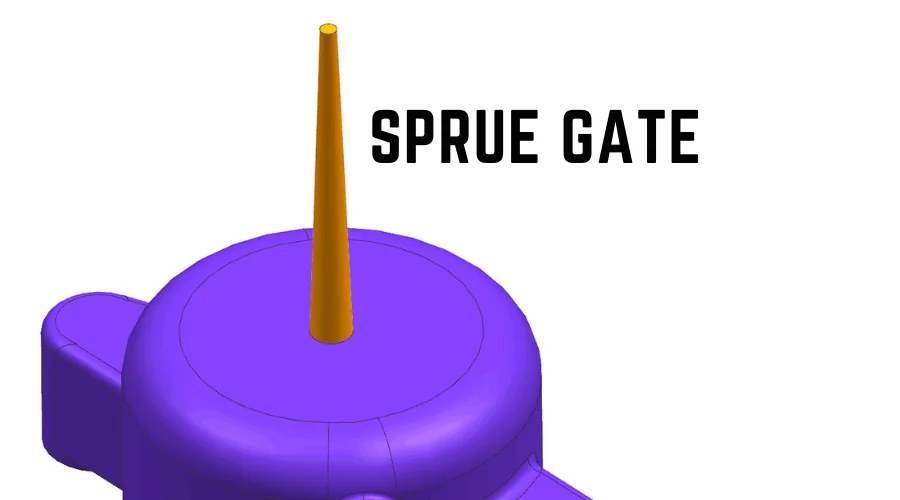
Edge Gates
Edge gates, also known as tab gates, are a specific type of injection molding gate that evolved from the side gate.
They are particularly suitable for producing thin-walled parts or those with intricate features due to their ability to minimize shear stress during the filling process.
These tab gates are located at the edge or parting line of the mold, allowing the plastic to flow directly into the cavity from the side, which helps reduce the material flow distance and leave smaller gate marks.
Despite their advantages, tab gates can create weld lines or knit lines, which are less desirable in the final product. The typical depth range for a tab gate is between 0.5 mm to 2 mm, making it a versatile option for various applications.
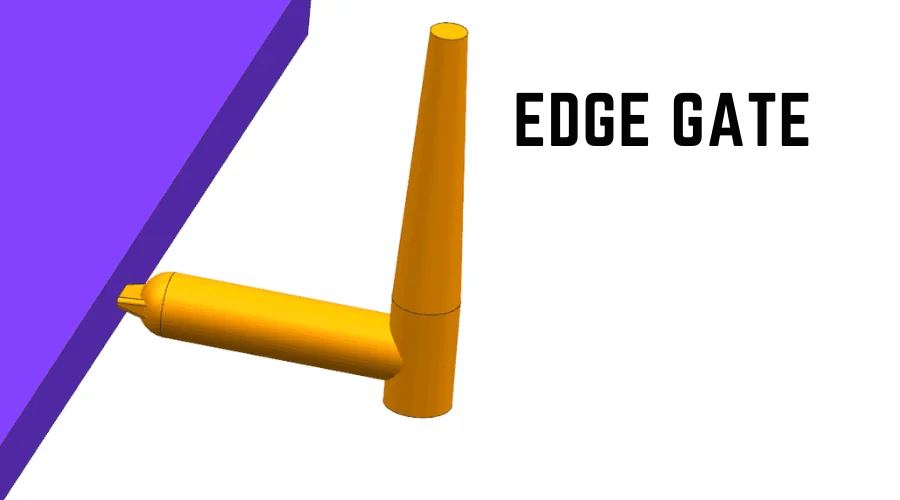
Submarine Gates
Submarine gates are located below the mold parting line, which helps reduce visible marks on the finished parts. These gates fill the cavity from below the parting line, ensuring effective flow and enhancing the aesthetic quality of molded parts. Submarine gates are ideal for small components, allowing for automatic trimming upon ejection.
Flexible placement options make submarine gates suitable for parts with complex geometries, providing improved flow and reducing the risk of defects. The angled submarine gate design ensures easy separation and efficient production.
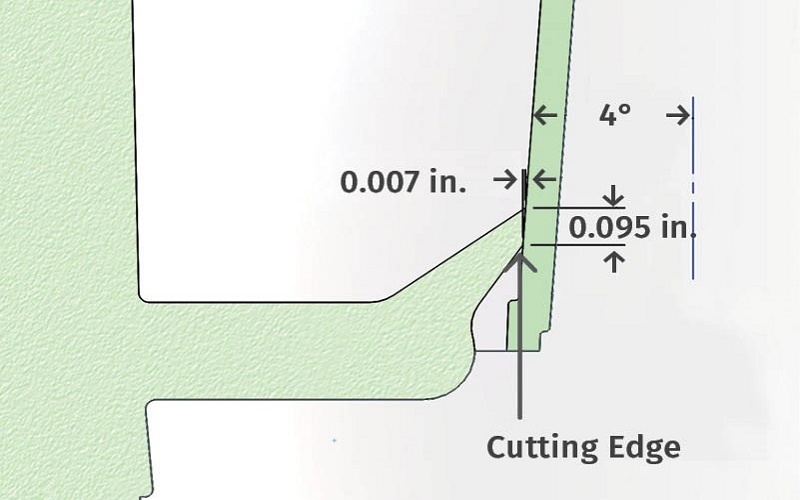
Diaphragm Gates
Diaphragm gates use a diaphragm valve to control the flow of molten plastic, allowing for significant amounts of plastic to enter the mold and ensuring even distribution.
These diaphragm gate are more complex and expensive compared to other types, but they are particularly useful for larger parts that require consistent filling.
Their ability to facilitate a high flow of molten plastic makes diaphragm gates suitable for applications where uniform filling and high-quality finishes are essential.
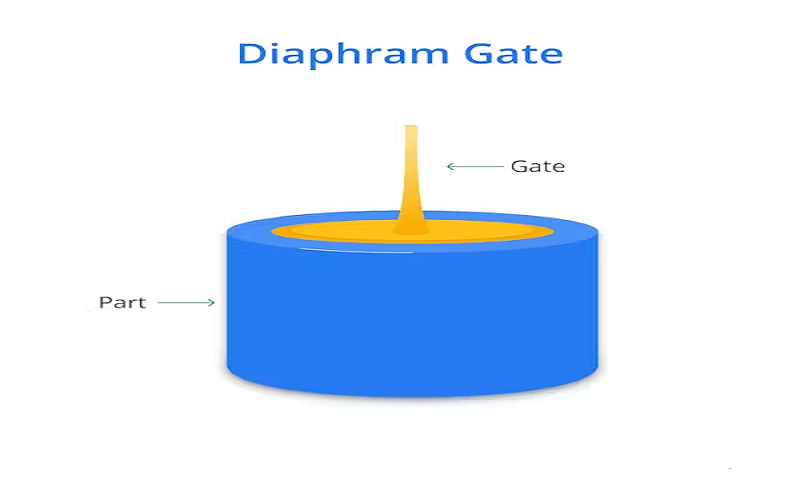
Hot Runner Valve Gates
Hot runner valve gates offer precise control over molten plastic flow, making them ideal for complex parts with intricate geometries. The valve pin, typically made of steel or ceramic, regulates the plastic’s passage into the cavity, enhancing overall part quality.
These gates are compatible with various resin types, providing flexibility in material choice and improving the accuracy of the injection molding process. Although they come with higher complexity and costs, the benefits of hot runner valve gates in terms of control and quality are significant.
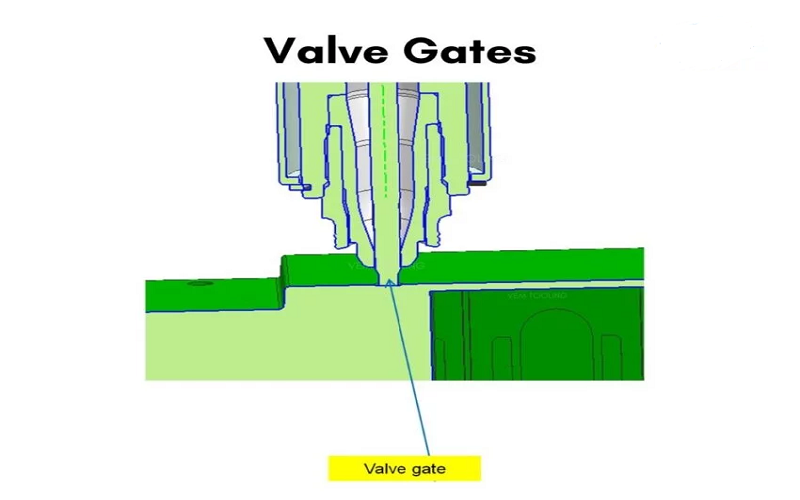
Fan Gates
Fan gates resemble a fan or wedge-like shape, facilitating discrete gate locations and smooth surface finishes. These fan gate are advantageous for producing parts that require a clean finish, making them ideal for aesthetic applications.
However, fan gates can result in uneven cavity filling, potentially affecting part quality. They are particularly suitable for molding applications involving polycarbonate plastics due to their molding capabilities.
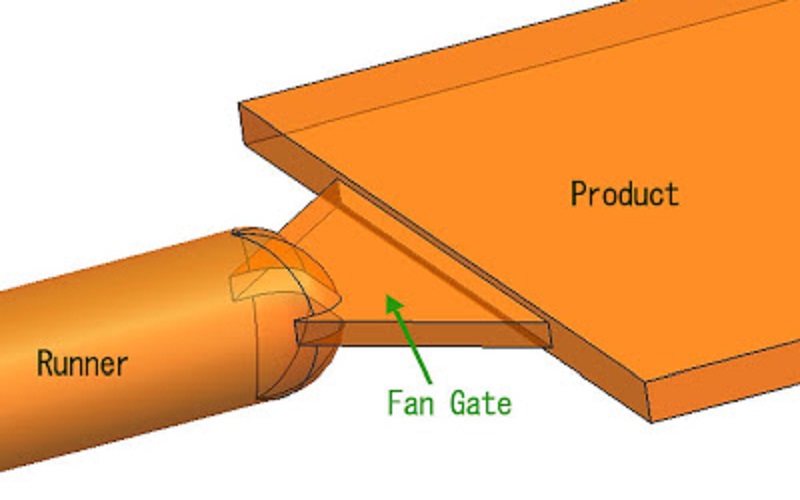
Pin Gates
Pin gates provide a small, accurate opening that minimizes waste and is often used for highly detailed, thin-walled components. Typically located near the ejector pins on the B-side of the mold, pin gates split the flow of molten plastic in several directions, ensuring precise filling.
The size of the pin gate is essential to avoid stress. It also plays a key role in ensuring proper mold opening. These gates are ideal for precise, thin-walled parts, allowing for minimal waste during the injection process and providing a clean finish.
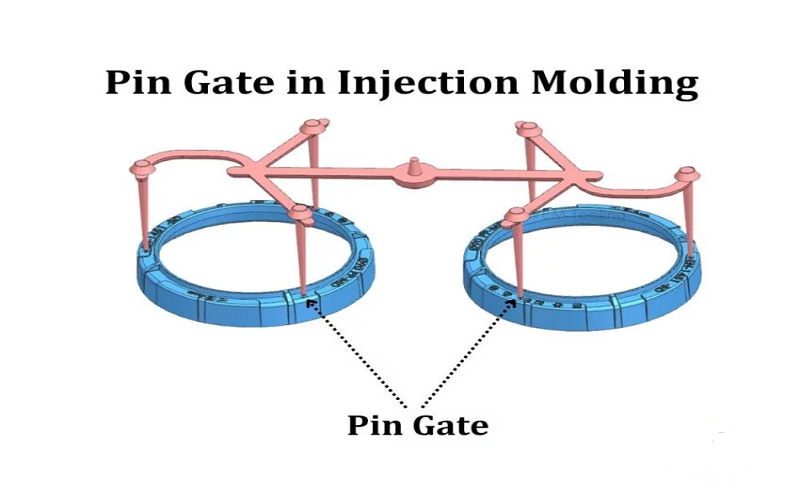
Factors to Consider When Choosing A Gate Type
Selecting the right gate type depends on various factors, including the desired appearance of the product, the constraints of size and shape, and the type of plastic used. Each of these factors plays a critical role in determining the most suitable gate for a particular application.
Key factors to consider when choosing a gate type include part design and geometry, material properties, and production volume and cost.
Part Design and Geometry
Part design and geometry significantly influence the choice of gate type. For example, small components often use submarine gates due to their design requirements, while more complex parts may require multiple gates to ensure even distribution of molten material. Consider factors such as part size, shape, and intricate features when selecting the gate type.
Place the gate in the deepest cross-section of the mold to optimize filling efficiency and enhance part structural integrity. Proper gate location ensures uniform filling, reduces voids, and minimizes defects.
Material Properties
Consider material properties, including flow characteristics, processing temperatures, and viscosities, when selecting a gate type. Different plastics have varying requirements, and the gate must accommodate these to ensure efficient flow and filling.
Gate dimensions significantly impact filling efficiency and material flow during the injection process. A smaller gate can enhance visual quality but may lead to longer fill times, risking structural integrity.
Production Volume and Cost
Gate selection can lead to higher upfront costs due to complex tooling requirements. Overall cost-effectiveness should be taken into account.
This includes considerations for tooling, production efficiency, and secondary operations such as gate removal or finishing. Gate design directly influences throughput and cycle times, affecting overall production volume.
High-volume production typically benefits from gates that enable rapid filling and cooling, improving efficiency and reducing labor costs. A well-calculated gate size aids in controlling pressure in the mold and prevents material wastage.
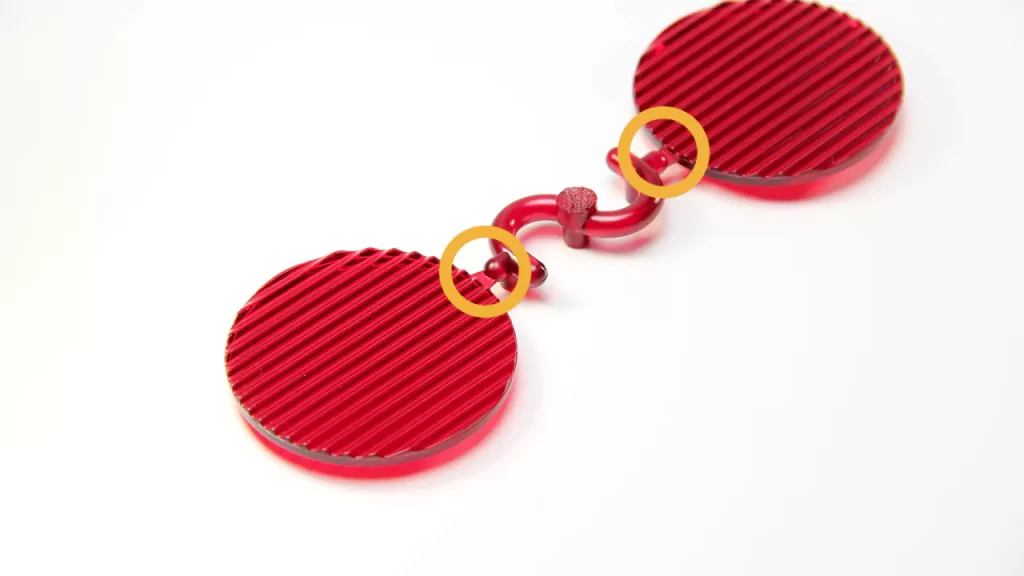
Best Practices for Injection Mold Gate Design
Best practices in injection mold gate design focus on optimizing the gate’s size, shape, and location to control pressure and temperature of the molten plastic during the injection process. Improper gate design can significantly increase the likelihood of defects, making strategic planning crucial.
Place gates in areas that minimize flow-related defects and enhance overall part aesthetics. Fan gates, for instance, are designed to reduce cosmetic flaws by placing gate marks in less visible areas.
Optimizing Gate Size and Shape
Factors affecting gate size and shape include part geometry, filling requirements, and aesthetics. The specific needs, size, complexity, design, and type of plastic material also play a crucial role in determining gate size. A gate that is too large can lead to excessive waste and increased production costs, while a gate that is too small can increase flow pressure and risk defects.
Submarine gates facilitate easy ejection of finished parts, enhancing overall efficiency. Hot runner valve gates provide a smooth and glossy surface finish, ideal for high-quality applications, while pin gates leave a small mark, not affecting the overall appearance and providing a clean finish.
Parts with complex geometries often require multiple gates for uniform filling, ensuring quality.
Strategic Gate Location
Considerations for gate placement include ensuring simultaneous filling of all cavity corners and facilitating easy mold removal. To minimize visible defects, place gates to reduce weld lines in the final product. Compound gates can be effective for large or flat plastic parts, allowing efficient filling and reduced defects.
Strategic gate placement reduces defects during the injection molding process, maintaining product integrity.
Venting and Flow Patterns
Hot runner valve gates maintain molten plastic temperature and pressure for even mold filling, optimizing flow patterns. Venting and flow patterns are critical for preventing defects in the injection molding process. Weld lines are visible seams that form when molten plastic flow fronts meet. They can impact both the strength and aesthetics of a part.
Strategies to minimize air traps and weld lines include optimizing gate design and ensuring proper venting during the injection molding process.
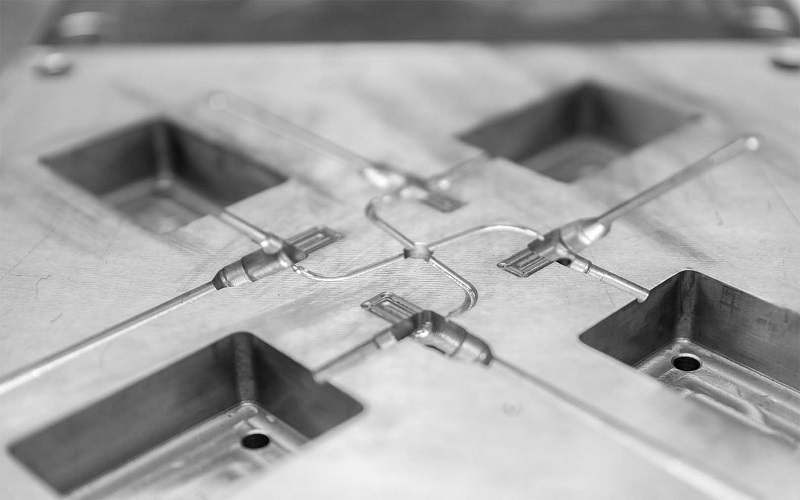
Summary
Understanding and selecting the right injection molding gate is crucial for achieving high-quality molded parts.
The gate’s design, size, shape, and placement significantly influence the injection molding process, affecting the final product’s appearance and structural integrity.
By considering factors such as part design, material properties, and production volume, you can optimize gate selection and design to enhance efficiency and reduce defects.
Applying best practices in gate design, including strategic placement and optimizing size and shape, will lead to superior results in your injection molding projects.
With the knowledge gained from this guide, you are well-equipped to tackle common gate-related issues and ensure the success of your molding endeavors.