As modern manufacturing increasingly demands environmental protection and resource conservation, Foam injection molding has gained attention in the manufacturing world .
This article will explore in detail the principles of injection molding foam, the process flow, and application examples, providing a reference for professionals looking to embark on foam plastic injection molding projects.
What Is Foam Injection Molding?
Foam injection molding involves incorporating blowing agents like azodicarbonamide or inert gases into plastics such as polystyrene, acrylonitrile-styrene, polyethylene, and polypropylene.
This mixture is melted in the injection molding machine’s heated barrel and injected into a mold where it expands to form a foamed product.
Foam injection molding differs from standard injection molding in that it uses pressure control to prevent the material within the heated barrel from foaming prematurely.
Instead, the molten material is injected into the mold, which is at atmospheric pressure.
Once injected, the material expands due to the blowing agent’s action, filling the mold cavity to create the foamed product.
Foam molding technology is a one-step process that offers high production efficiency and yields high-quality products.
It is particularly suited for complex shapes and precision-sized foam plastic products and is also the primary method for producing structural foam.
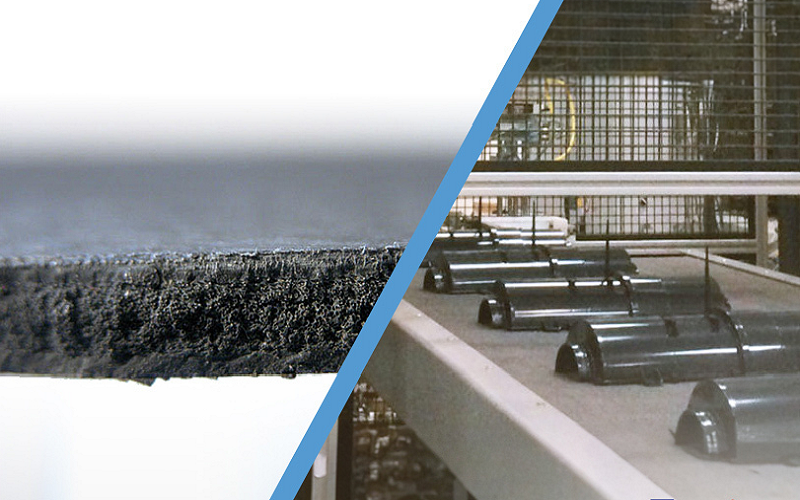
Why Use Foam Injection Molding?
Foam injection moulding technology allows for control of the dimensional accuracy of parts within 0.001 mm to 0.01 mm, and even below 0.001 mm in some cases.
Compared to traditional injection molding processes, parts produced by this technology exhibit superior mechanical properties and dimensional stability, along with high dimensional precision and repeatability, with small tolerance ranges.
This process not only enables the production of lightweight and high-strength plastic products but also enhances product performance while reducing material consumption and production costs.
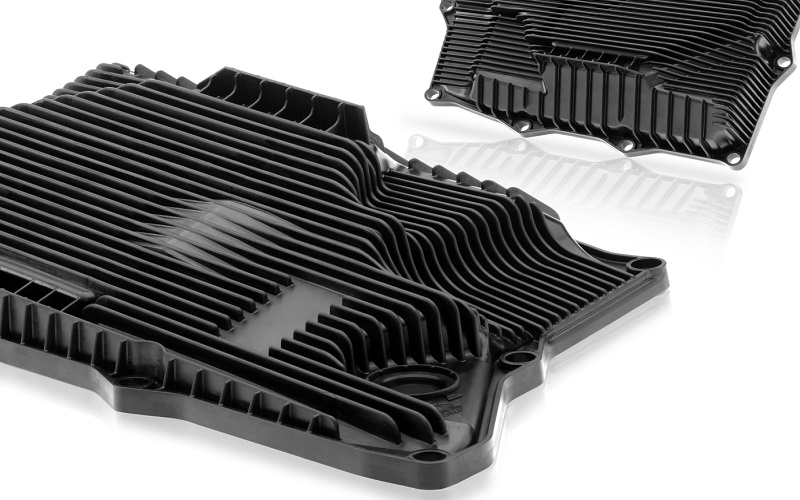
What Are The Types Of Foam Injection Molding?
Foam injection molding technologies can be differentiated by how the foam structure within the polymer is created, primarily defined by the type of blowing agent and the process specifics.
Physical Foaming Method
Simply put, this involves using physical processes to foam plastics, typically through three main approaches:
- Dissolving inert gas into the plastic melt or paste under pressure, then decompressing to release the gas, creating bubbles and causing foaming within the plastic.
- Evaporating low boiling point liquids that have been dissolved into the polymer melt, turning them into gas and thus causing the plastic to foam.
- Adding hollow spheres to the plastic to create a foamed structure through foaming.
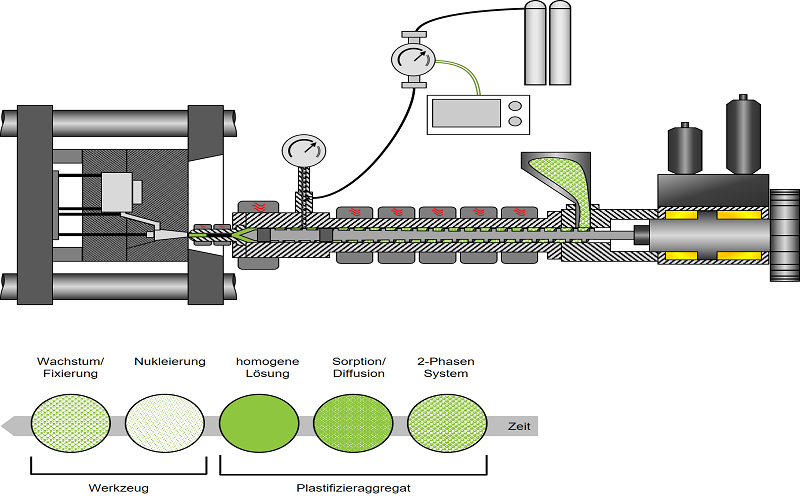
Chemical Foaming Method
The chemical foaming method uses chemical reactions to generate gas that causes the plastic to foam: heating the chemical blowing agents mixed into the plastic causes them to decompose and release gas, leading to foaming.
Additionally, foaming can occur through the release of gas from chemical reactions between different components of the plastics.
The process of foam injection molding with chemical blowing agents is essentially the same as the general injection molding process.
The heating, temperature rising, mixing, plasticizing, and the majority of the foaming expansion occur within the injection molding machine.
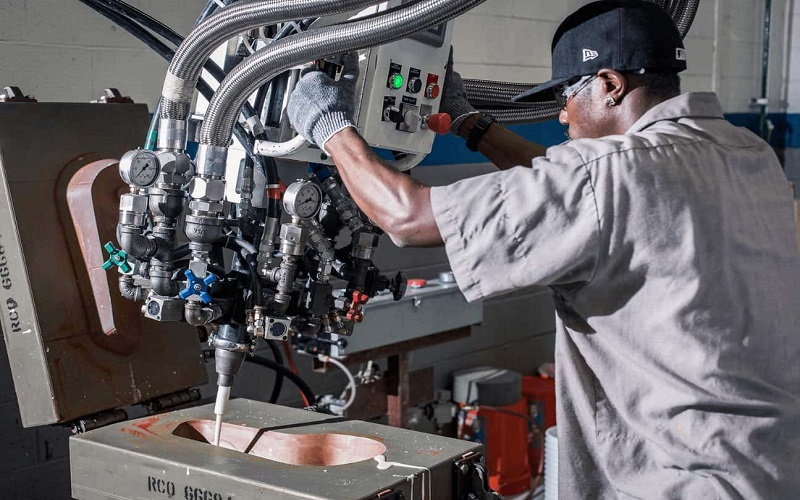
Structural Foam Molding
Structural foam molding, a type of chemical foaming, uses chemical blowing agents (CBAs) or physical blowing agents (PBAs) to achieve a microcellular (foam) structure.
It retains many advantages of traditional injection molding while avoiding some of the problems encountered in traditional molding processes, such as insufficient product strength, long production cycles, and low molding rates.
Additionally, using structural foam technology allows for the molding of large and complex products, the use of low-cost molds, and the operation of multiple cavities at the same time, thereby reducing production costs of the products.
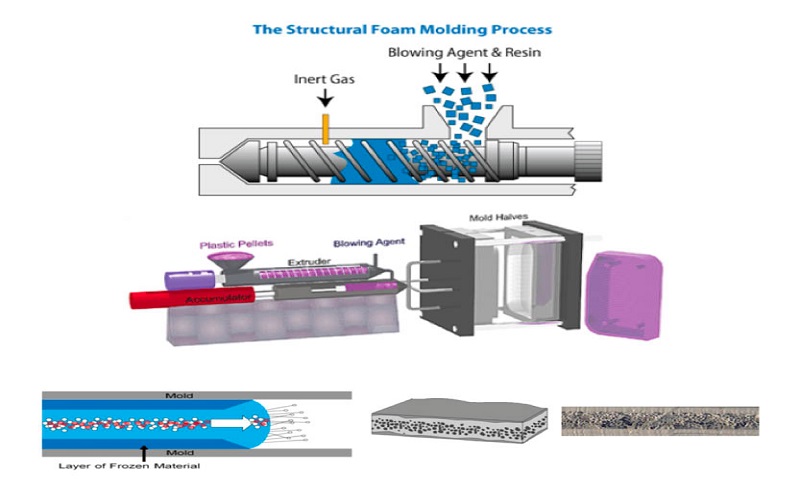
What Are The Characteristics Of Foam Plastic Injection Molding?
Foam plastic molding distinguishes itself as a unique manufacturing process with a set of specialized attributes that define its role in the production landscape.
- The density of the molded products is between 0.2 to 1.0 g/cm3
- Capable of producing thick-walled products
- Able to achieve foamed products with high-density surfaces and low-density cores
- Can produce foamed products with surfaces that have wood grain or marble-like patterns
- The products are lightweight and inexpensive
- Able to be produced in a variety of colors
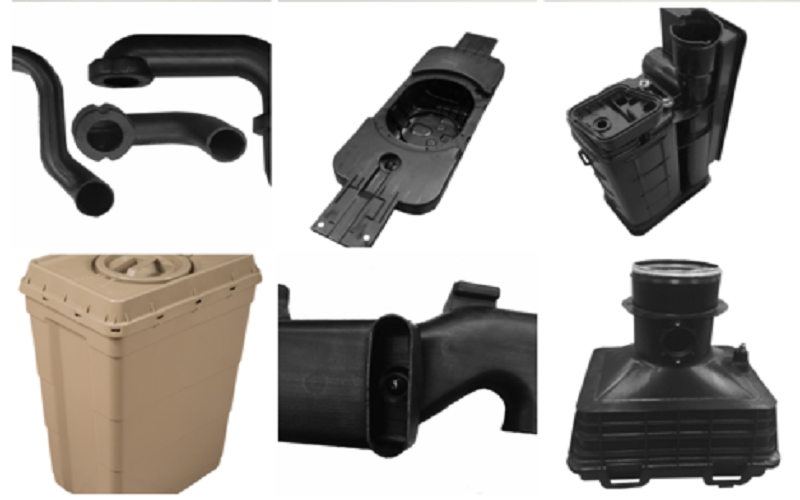
How Does Foam Molding Process Works?
The injection foaming process is primarily determined based on the properties of the raw materials, the structure of the molding equipment, and the requirements of the product.
Polymers and various additives (including chemical blowing agents) are mixed evenly and then added to the plasticizing barrel of the injection molding machine, where they are heated, plasticized, and further mixed uniformly.
The mixture is then injected into the mold cavity at high pressure and speed.
As the plastic melt enters the mold cavity and the pressure suddenly drops, a large amount of supersaturated gas in the melt separates out, forming numerous bubbles.
The foam expands within the mold cavity and cools to set. Finally, the mold is opened to remove the foamed product.
Material drying has a significant impact on the quality of injection-molded foamed products, especially for materials prone to hydrolysis like foam polycarbonate (PC).
Poor drying can also affect the strength of the product. For materials that require long drying times and high drying temperatures, regular checks of the drying equipment are necessary.
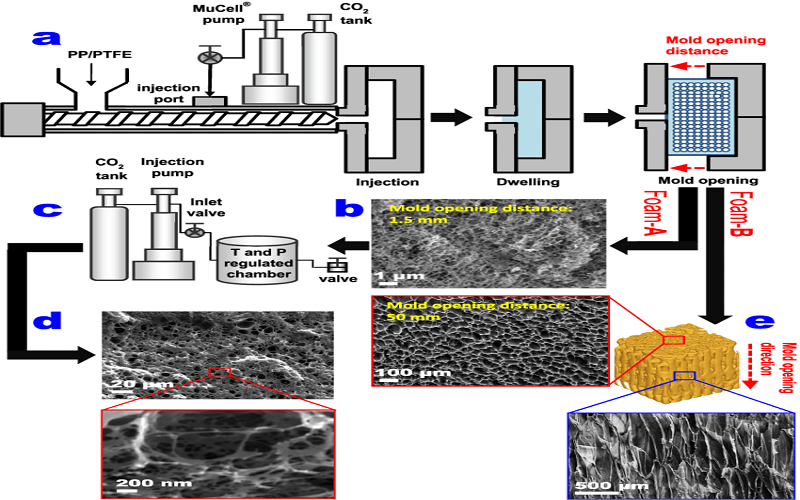
Applications Of Injection Molded Foam
As a lightweight technology with numerous advantages in cost and processing, foam plastic products have been applied in various fields such as automotive, home appliances, construction, and consumer goods.
Automotive Industry
Foam moulding materials hold an undeniable position in the automotive industry.
For instance, they are used in car seats, steering wheels, door linings, roof linings, and central control panels.
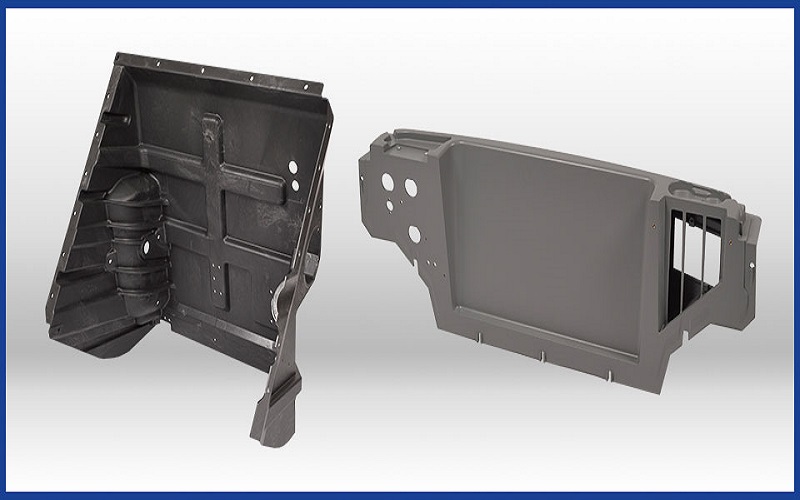
Home Appliances
In the realm of home appliances, foam injection moulding materials are primarily used as packaging materials.
In some electrical appliances, foam is used for insulation layers and padding.
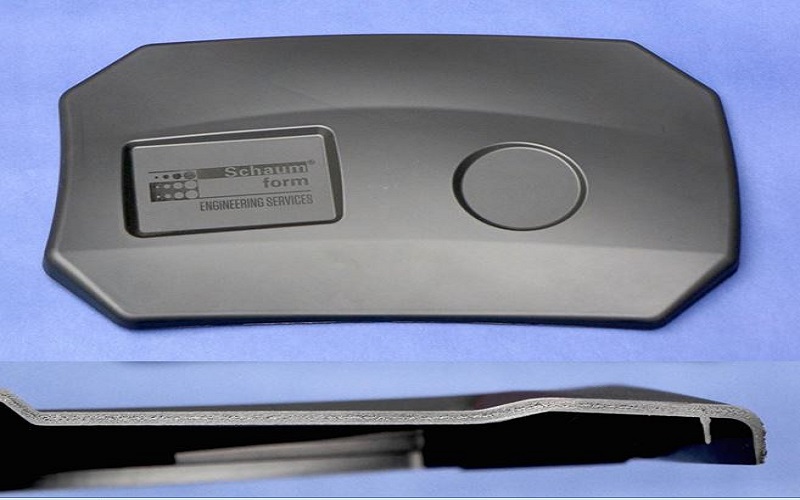
Construction Industry
With the increasing focus on environmental protection and energy needs, foam plastic molding materials are becoming increasingly popular for their insulating properties.
Examples include thermal insulation materials, sound-absorbing materials, and soundproofing materials.
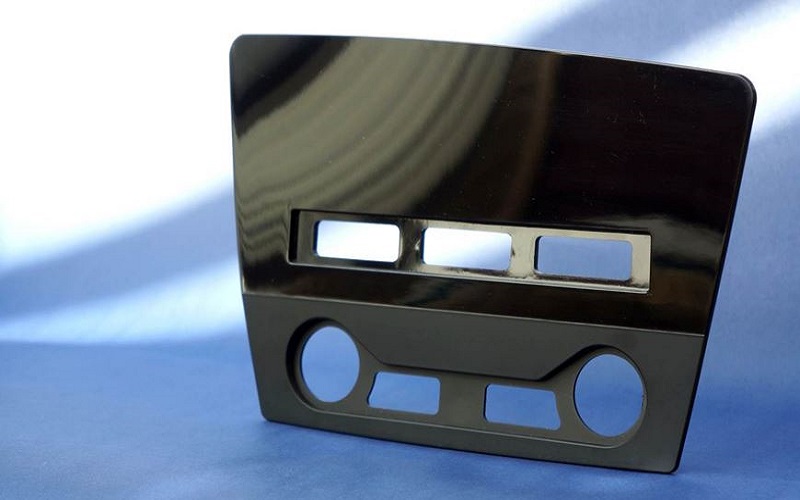
Sporting Goods
The lightweight, soft, and waterproof properties of foam molding materials make them particularly suitable for manufacturing sports equipment.
Examples include sports shoes, protective gear, and swimming aids.
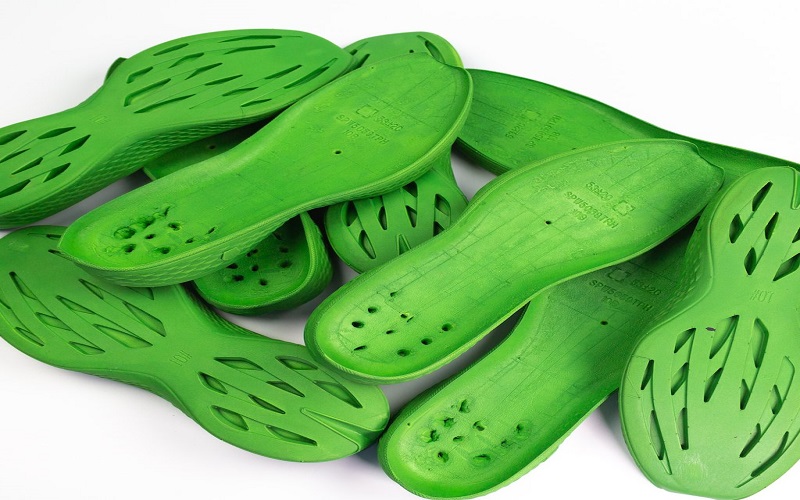
Conclusion
In summary, foam plastic injection molding is a versatile and highly efficient process. Its diverse applications and the benefits it offers make it a preferred choice for meeting modern manufacturing needs.
If you’re interested in exploring foam injection molding projects, you can contact us.
FOWMOULD offer customized, one-stop injection molding services tailored to meet the specific needs of their clients, providing expert solutions across a wide range of applications.