With the advancement of modern technology, the application of plastics has greatly expanded, especially in industries such as construction, furniture, electronics, appliances, and daily necessities, where they are gradually replacing traditional materials.
However, as organic polymer materials, the flammability of plastics poses a significant fire hazard to humanity.
Therefore, the development and application of fire retardant modification technology for plastics have become an important means to enhance the safety performance of plastic products.
The demand for fireproof plastic has increased dramatically.
In this article, we will delve into the principles and practices of flame retardants in plastic, as well as how they help maintain the performance of plastic products while increasing their safety and environmental friendliness.
What Is Fire Retardant Plastic?
Fire retardant plastics are achieved by incorporating flame retardant components into the plastic processing system, with the aim of imparting flame retardant properties.
In modern processing techniques, plastic flame retardancy technology is mainly divided into two types: additive and reactive.
Reactive flame retardancy technology involves introducing flame retardant elements during the plastic processing phase.
On the other hand, additive flame retardancy technology entails adding flame retardants during the molding and processing of plastic resins.
Typically, this approach uses a primary fire retardant supplemented by various other types of fire retardants, forming a composite fire retardant system.
In modern fire retardant plastic processing techniques, the additive approach is predominantly used.
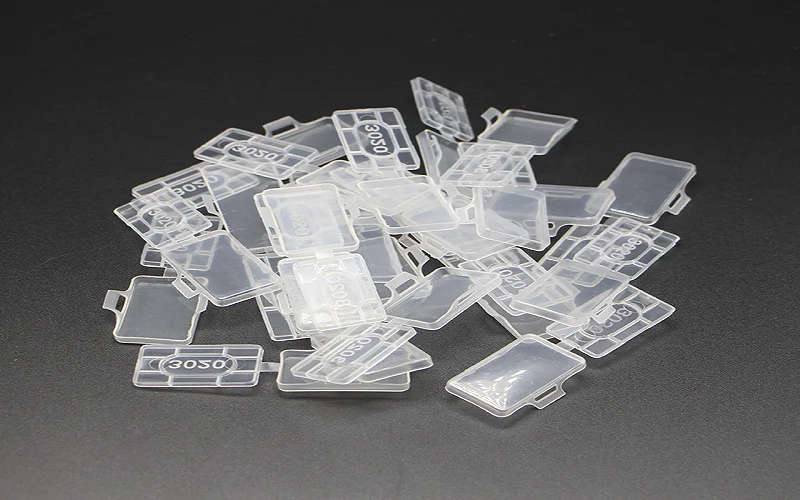
Classification of Fire Retardant
A fire retardant is an additive incorporated into plastic materials, primarily functioning to enhance the combustion threshold of plastics by inhibiting the burning process.
This substance can slow down or prevent the spread of flames, thereby improving the material’s safety performance when exposed to a fire source.
Below are the three main categories of flame retardants for plastics:
1.Classification by fire retardant elements
Based on the flame-retardant elements contained, flame retardants can be classified into several categories including halogen, phosphorus, nitrogen, sulfur, phosphorus-halogen, phosphorus-nitrogen, silicon, antimony, boron, and aluminum-magnesium based flame retardants.
Among these, halogen-based flame retardants are one of the largest in production volume in the world.
They are characterized by their low addition levels and significant fire resistant effects, holding an important position in the field of flame retardancy.
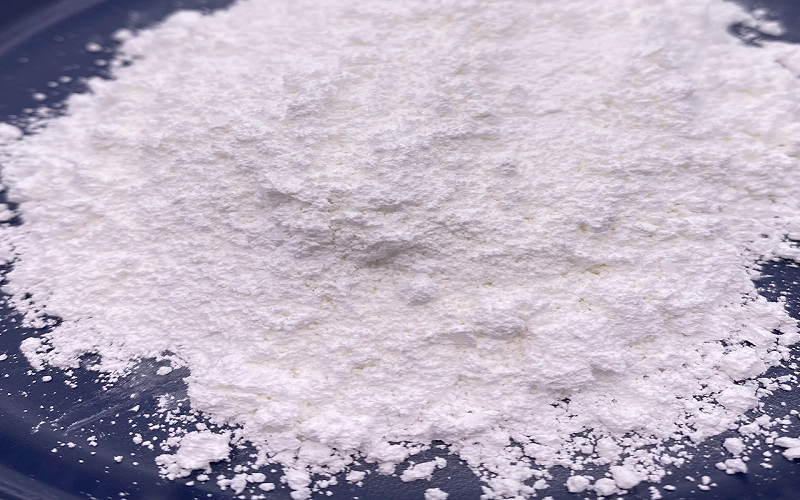
2.Classification by the method of use of fire retardants
Flame retardants can be classified into two types based on their mode of application: additive flame retardants and reactive flame retardants.
Reactive fire retardants can form copolymers with monomers or graft onto polymers, thereby imparting durable flame retardancy to the material.
The advantages include good stability, long-lasting flame retardant effect, low toxicity, and minimal impact on the properties of plastics, making them an ideal type of fire retardant.
However, their drawbacks are inconvenience in application, limited variety, and currently, they only account for about 10%-20% of the total usage of flame retardants.
Reactive fire resistants are mainly used in thermosetting plastics and sometimes in thermoplastic plastics.
Some reactive flame retardants can also be used as additive flame retardants.
Additive fire retardants are mixed into plastics before processing and are physically dispersed in the mixture.
They are characterized by ease of use and broad applicability, currently accounting for 80%-90% of the total flame retardant usage.
However, they generally have poor compatibility with polymers, requiring larger amounts to achieve effective fire retardancy, and may reduce the mechanical properties of polymer materials.
Additive fire resistants are commonly used in thermoplastic plastics.
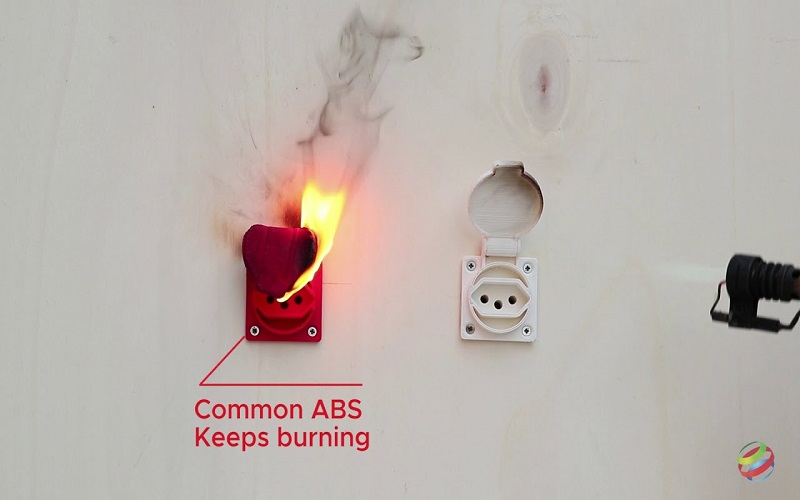
3.Classification according to fire retardant composition
Based on the composition of flame retardants, they can be categorized into two main types: inorganic flame retardants and organic flame retardants.
(1)Inorganic Flame Retardants
There are many types of inorganic flame retardants, each with different functions.
Some can be used alone to show flame retardancy, such as red phosphorus
Some are used in combination with halogen-containing organic flame retardants to exhibit flame retardancy, such as Sb2O3 (antimony trioxide).
Others serve both as fillers and demonstrate flame retardancy by decomposing to release crystal water, like aluminum hydroxide.
Inorganic flame retardants have advantages like good thermal stability, non-toxicity, no production of corrosive gases, non-volatility, smoke suppression, long-lasting effects, and cost-effectiveness.
However, they can have negative impacts on the processing and molding properties of polymer materials, as well as on their physical and electrical properties.
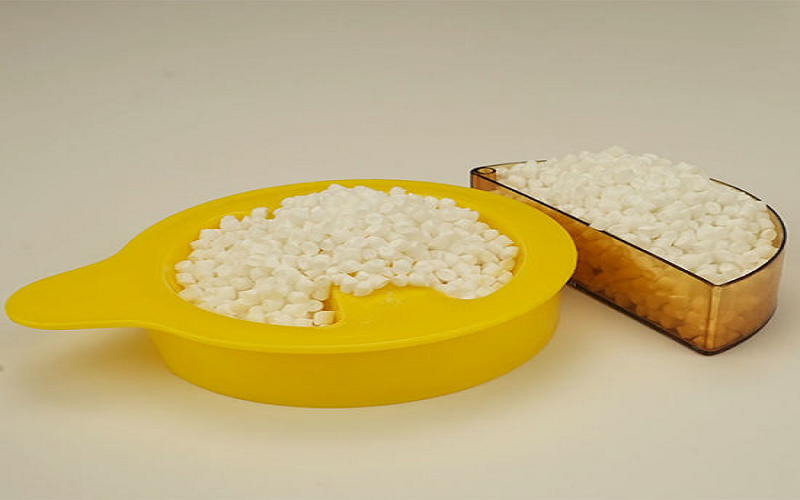
(2) Organic Flame Retardants
There are also many types of organic flame retardants. When subdivided by compound type, the main categories are phosphorus-based and halogen-based flame retardants.
Phosphorus-based flame retardants can be further divided into halogen-free and halogen-containing retardants, while halogen-based flame retardants can be divided into chlorine-based and bromine-based retardants.
Phosphorus-Based Flame Retardants | Halogen-Based Flame Retardants | ||
Type | Name | Type | Name |
Non-Halogenated | Tris(octyl) phosphate |
Chlorinated | Chlorinated Paraffin |
Tributyl phosphate | Chlorinated Polyethylene | ||
Octyl diphenyl phosphate | Hexachlorocyclopentadiene | ||
Halogenated | Tris(chloroethyl) phosphate |
Brominated | Tetrabromobutane,Hexabromobenzene |
Tris(2,3-dibromopropyl) phosphate | Hexabromocyclododecane | ||
Tetrabromobisphenol A | |||
Tris(2,3-dichloropropyl) phosphate | Decabromodiphenyl ether |
Organic flame retardants, particularly brominated organic retardants, are favored due to their effective flame retardancy, low required quantities, and minimal impact on the properties of plastic products.
Despite issues such as toxicity, higher smoke generation, and the release of highly corrosive hydrogen halide gases, they remain widely used and important flame retardants in current applications.
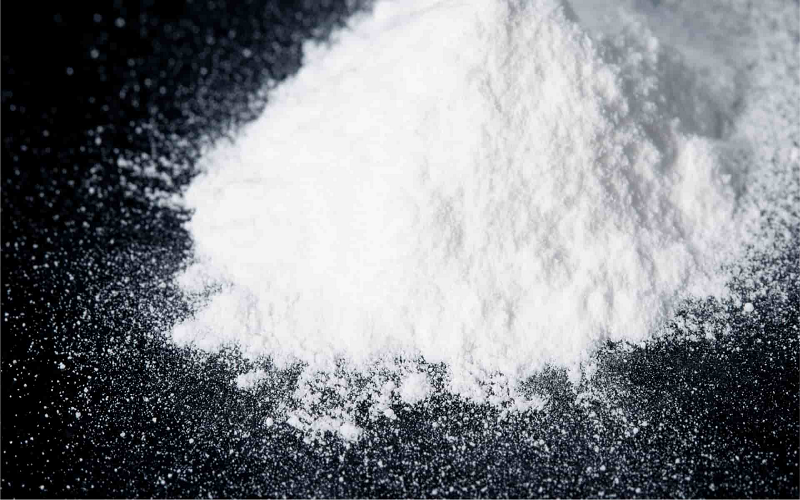
Working Principle Of Fire Retardant For Plastic
Firstly, the dehydration action of the decomposition products of fire retardants causes organic materials to carbonize, thereby preventing combustion.
Plastic combustion is a process of decomposition and burning, and elemental carbon typically does not undergo flame-producing evaporative combustion or decomposition combustion.
Therefore, if the thermal decomposition of the material can be rapidly carried out, moving past the combustible stage straight to carbon, combustion can be prevented.
Secondly, fire retardants decompose at the burning temperature of plastics, forming a non-volatile protective film on the surface.
This film acts as a barrier to air, thereby inhibiting combustion.
Additionally, dispersing the heat of combustion and diluting combustible materials are other ways to achieve flame retardancy.
As a large amount of combustion heat is absorbed, the temperature of the plastic is lowered, thus slowing down the decomposition, evaporation, and burning processes.
On the other hand, the flame retardant system in plastics can decompose to produce non-combustible gases, thereby diluting the combustible gases and achieving the purpose of flame retardancy.
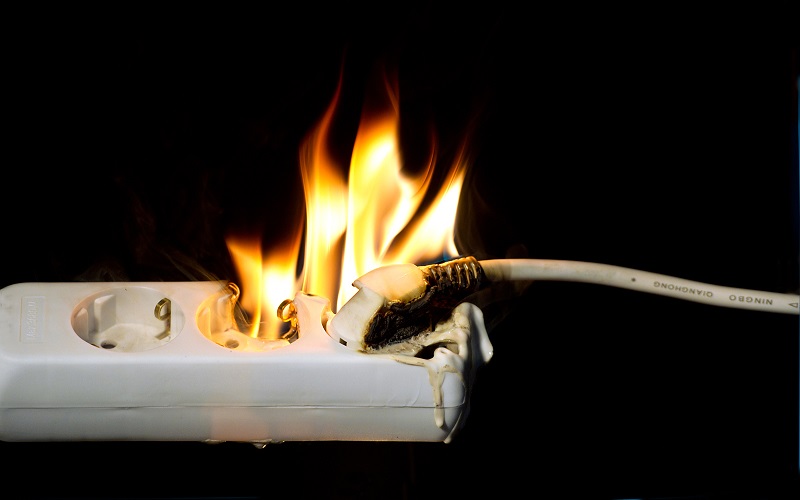
Common Fire Retardant Plastics
Injection molding manufacturers often use flame retardants to modify the flame retardancy of plastics.
Here are some of the most commonly used flame retardant plastics:
Fire retardant PC/ABS
To meet fire safety requirements in certain application areas, PC/ABS alloys must possess good flame retardancy.
For instance, in new energy vehicle charging piles and certain electronic and electrical flame retardancy levels, they need to reach V-0.
For PC/ABS blends, bisphosphate and phosphate oligomers with good thermal stability, such as BDP, demonstrate excellent flame retardancy.
Key manufacturers of non-halogen flame retardant PC/ABS include Covestro, SABIC, LG Chem, Kumho Petrochemical, Wanhua Chemical, and Luxi Chemical.
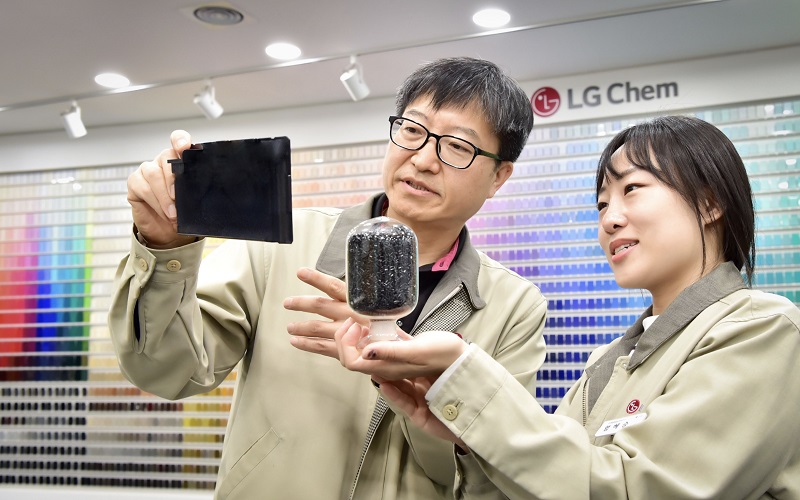
Fire retardant PP
PP is a polymer material with high demand in production and life due to its low production cost, excellent mechanical properties, and good corrosion resistance, meeting many requirements in the plastics application field.
However, as a flammable material with a limited oxygen index (LOI) of about 18% and a fast burning rate, PP’s safety is low, and its application range is restricted.
Therefore, it’s necessary to modify PP materials to enhance their flame retardancy.
Brominated alkyl phosphate flame retardants significantly improve flame retardancy while also improving the rheology and processing performance of PP with minimal impact on its physical and mechanical properties.
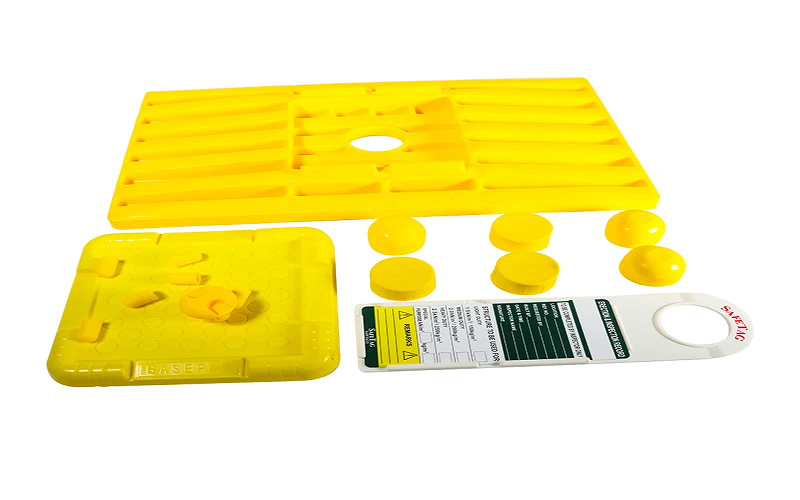
Fire retardant PC
Polycarbonate has an LOI of 21%–24%, and the material itself can reach UL94 V-2 level flame retardancy.
However, this is insufficient for special areas requiring higher flame retardancy, such as electronics, electrical, and automotive fields, where PC flame retardancy is required to reach V-0.
In flame retardant PC, sulfonate flame retardants, exemplified by potassium perfluoroalkylsulfonate (PPFBS), are most effective.
Adding a small amount (below 0.5%) of sulfonate flame retardants can significantly improve PC’s flame retardancy, achieving a V-0 flame retardancy level at 1.6–3.0mm.
Moreover, the modified PC maintains physical and mechanical properties comparable to general PC while remaining transparent.
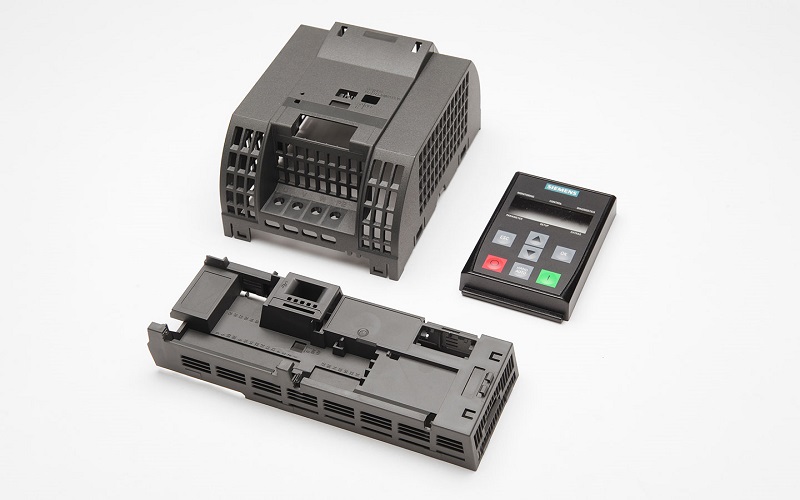
Fire retardant PA
Unmodified PA has a UL94 V-2 level flame retardancy and an LOI of 20%–22%.
In contact with open flames, it burns rapidly, releasing a lot of heat, and the molten material can drip, facilitating further spread of fire.
To prevent fire hazards, there are clear flame retardancy requirements for PA composites used in automotive and electrical products in the industry, generally needing to achieve UL94 V-0 level.
Halogen-based flame retardants are widely used in PA due to their good compatibility and high flame retardancy efficiency. In non-halogen flame retardant PA, different flame retardants are used.
Pure PA typically requires 12-15% MCA for flame retardancy. For PA/GF systems, due to the “wick effect,” more efficient flame retardants like aluminum diethylphosphinate (ADP) are used, supplemented by MPP and others for synergistic and cost-reduction effects.
There are also flame retardant PA products compounded with magnesium hydroxide and aluminum hydroxide.
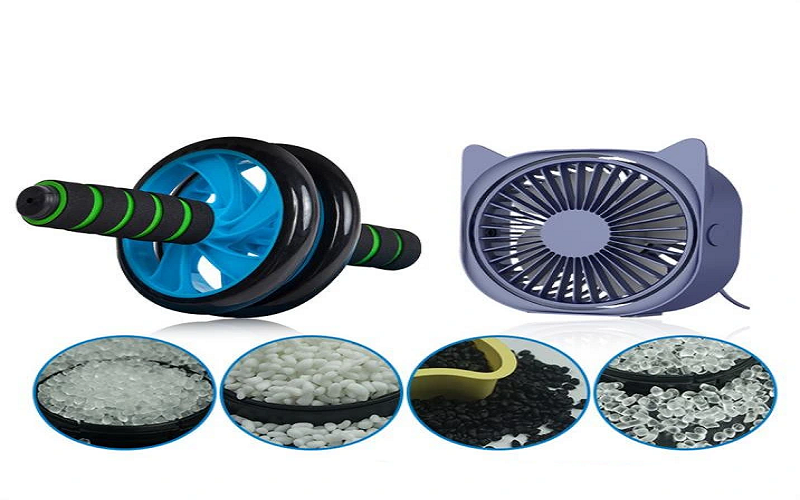
Standards for Flame Retardant In Plastic
The flammability UL94 rating is the most widely applied standard for assessing the flammability of plastic materials.
It evaluates the material’s ability to extinguish after being ignited.
The flame retardant grades are ranked from lowest to highest as follows: HB < V-2 < V-1 < V-0 < 5VB < 5VA, with a brief explanation below:
The lowest flame retardant level in the UL94 standard. It requires that for samples 3-13mm thick, the burning rate is less than 40mm/min.
For samples less than 3mm thick, the burning rate is less than 75mm/min; or the sample extinguishes before the 100mm mark.
After two 10-second burn tests on the sample, any remaining flame and afterglow extinguish within 60 seconds. Dripping particles may ignite cotton.
After two 10-second burn tests on the sample, any remaining flame and afterglow extinguish within 60 seconds. Dripping particles should not ignite cotton.
After two 10-second burn tests on the sample, any remaining flame and afterglow extinguish within 30 seconds. Dripping particles should not ignite cotton.
After five 5-second burn tests on the sample, any remaining flame and afterglow extinguish within 60 seconds.
Dripping particles should not ignite cotton. Block samples are allowed to be burned through.
After five 5-second burn tests on the sample, any remaining flame and afterglow extinguish within 30 seconds.
Dripping particles should not ignite cotton. Block samples are not allowed to be burned through.
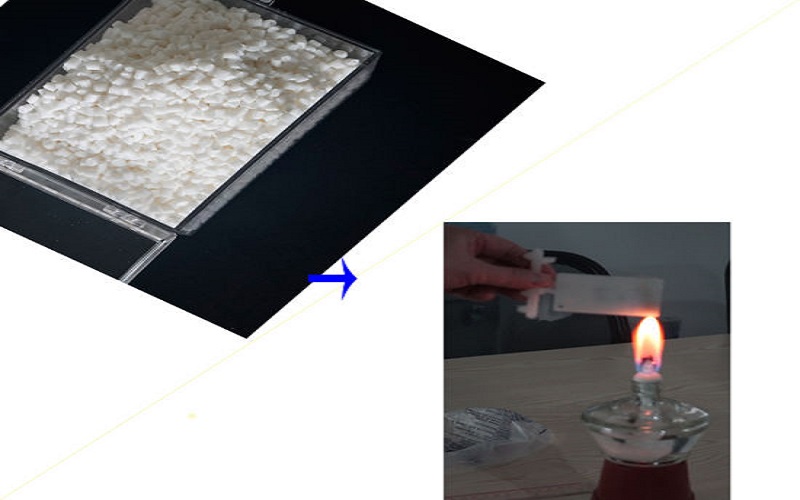
Conclusions
Fire retardants are indispensable additives in plastics, significantly enhancing safety by reducing flammability.
These retardants create efficient, effective, and sustainable flame retardant solutions for a variety of applications.
As the demands of new industry developments rise and environmental awareness in human society strengthens, plastic flame retardants will also seek new paths for green development.