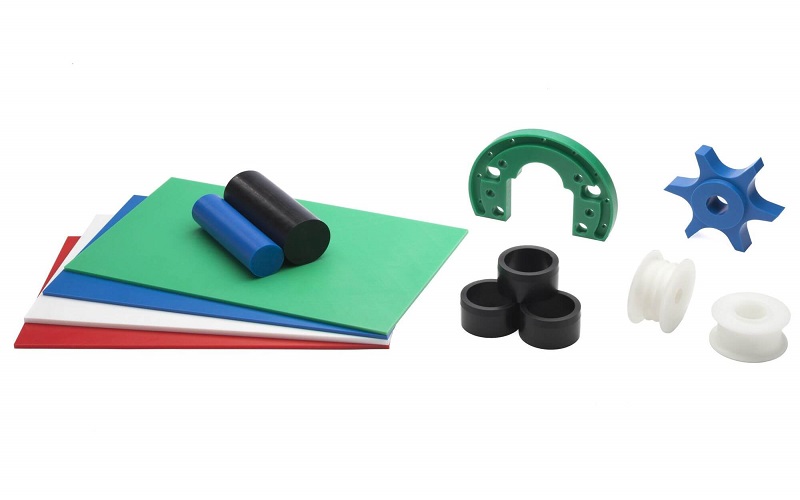
Share :
Share :
Injection molding is the process that enables manufacturers to manufacture parts in large quantities. It consists of manufacturing parts by injecting molten material into pre-made automotive injection mold. It is a general process to manufacture identical parts in huge quantities. Injection molding material includes glasses, metals, elastomers, and confections, but generally, it is used with thermoplastic and thermosetting plastic.
The first step of injection molding is to create the mold used to create the parts. Major molds are created from aluminum or steels, metals usually and precision machined to replicate the features of the products they produce.
Heating bands work on the technique of electric heating and they are used to melt the material in the barrel, and the molten metal or plastic is then filled in the mold cavity, where it dries and hardens, matching the shape of the mold. For an increase in the production of parts, the cooling time can be reduced by using cooling lines that can circulate water or oil to control the external temperature. Mold tools are placed on plate molds which open once the material dries and solidifies so that ejector pins can eject them.
Some molding defects are easier to stop than others. Some problems can be solved by adjusting the molding process without much expense of replacing or repairing the auto molds and other production equipment. One can easily counter several defects by adjusting the flow rate, temperature, and pressure of the mold.
Flow lines generally appear as a wavy pattern, often of a slightly different color than the other parts, and are mostly seen on the narrower sections of the molding component. They may also be seen as ring-shaped bands on a product’s surface near the entry points of the mold or “gates,” through which the molten material flows.
Flow marks do not affect the quality and design of the component. But are known to be fatal in the case of high-end consumer products such as sunglasses.
Burn marks are dark in color, either rust-colored or black, and these are the marks that form on the edges of the auto plastic parts. They can also form on the surface of the product being molded, which is not part of the product design. The marks are usually harmless, but at times they burn the plastic and degrade its quality.
One of the most common causes behind the burn marks is overheating, either resins or trapped air bubbles in the mold cavity during cycles. It can be a result of the high speed of the injections or overheating the material.
The vacuum voids are trapped in the finished product that hampers the finished look. Although the air bubbles are not considered a major defect, they may cause the final product to weaken during the product development. One of the reasons that cause air bubbles is insufficient pressure in plastic products, which means that the mold is not filled adequately due to the low volume production.
The air bubbles trapped in the mold are therefore not pushed out when the injection moulding automotive parts gets completely cooled, and it solidifies in the same form with bubbles in it.
Weld lines are those fine lines that are produced on the surface of the product during production. These fine lines occur when the molten plastic converges from distinct channels at certain points in the mold and creates a weak bond between each other. This results in the complete plastic product getting weakened at the weld line.
This problem occurs when the different parts of the products are cooled and then solidified unevenly during the processing of plastics. The resultant compression molding product then gets disfigured with several twists and bends. Plastic products generally cause warping because of the premature cooling rates associated with the raw materials used to produce the plastic bucket mold products
Sink marks are some small depressions that are caused by the plastic product. They usually happen when the inner component of the product solidifies rapidly and shrinks. Then the outer material of the product gets forced inwards due to shot weight. The marks occur because the molten plastic material cools down very quickly in the mold itself.
Hence the outward material gets pulled before it gets cooled completely and causes a recession. This usually occurs when the mold has thickened parts, and the plastic material gets cooled unevenly.
Discoloration is a defect caused when the finished plastic car parts are in a different color than it is expected to be. This discoloration is generally present only in some parts of the product or experiences just a few streaks of a different color on the component’s surface. The discoloration is purely superficial and does not affect the strength, operations of the functioning of the finished products.
This type of deformation in the plastic product may cause the product such as plastic molded chairs to weaken to a great extent. As the name suggests, it is caused due to a sudden jet of the molten materials when it enters the mold and gets cooled faster than the rest of the material. This can result from high injection pressure, which results in the squirting of the material into the mold through the gate instead of gradually filling the mold.
The jet of the molten plastic then starts cooling before the cavity is filled and thus leads to the formation of waves on the surface of the finished products.
Although there are several issues with the injection molding process, they can be solved easily. The upcoming part of this article aims to present some of the best solutions to common injection molding problems.
Short shots are one of the most common problems faced. It occurs when the mold cavity for the automotive interior plastics is not properly filled. This generally happens due to improper temperature, poor exhaust, uneven pressure, small gate size, premature melting of polymer, and so on.
Here are some of the proven remedies for this problem:
When air is trapped inside the cavity of the mould design, it creates bubbles, giving rise to the problem of air traps. This is mainly caused when the air cannot escape from various parts such as the ram, parting surface, or vent.
Here are some solutions for the problem of air traps:
When the plastic parts of the plastic mold design crack, then the problem of brittleness arises. It is generally caused due to inappropriate temperature, inaccurate runner system, and gate settings, amongst many other things. Here are some solutions for this problem:
Burn marks generally occur on 3d printing due to several reasons, including material degradation, very high melting temperature, improper design, and overcast screw speed. Here are some proven remedies to this problem:
Flash means the presence of excess plastic on the ejector part or mold parting of the stamping mold design. When the mold is defective, the melting conditions are not accurate, clamping force is inappropriate, or the exhaust system design is not proper. Here are some of the remedies:
Delamination occurs when the surface can be peeled in layers. It happens when more than the required release agent is used, when there is an inconsistent temperature, when the flow path and the injection mold gate design have sharp edges or angles. Here are some effective solutions to this problem:
Jetting is a spray trace caused when the size of the gate is very small, or the filling speed is very fast.
Here are some of the proven remedies:
Flow lines are another very common molding defect that forms a wavy line type pattern on the product’s surface. Flow lines occur when the material temperature or the custom plastic mold temperature is very low, the size of the gate is small, and so on.
The problem of fog arises when discoloration happens near the gate. There are several reasons for this problem, such as small gate size, small area of the break, large shear rate, and so on.
Here are some of the effective remedies:
Streaks are also a very common problem faced in injection mold design engineering. It occurs when there is too much moisture in the raw material or when the material has impurities, or when the temperature of the barrel is very high. Here are some solutions:
A lot of expensive errors can occur if injection molding is not done correctly. Quality issues in the final products can range in between some small surface issues to some serious defects that may hamper the safety of the user. Also, such defects can affect the performance and the functioning of the product. As a result, the customers may stop purchasing from a particular brand. Thus, it is quite important for plastic mold makers to ensure that the process is taking place without any errors. In this article, we have discussed some of the common advanced injection moulding problems and solutions.
Please contact us using the form below or emailing (harry@fowmould.com)