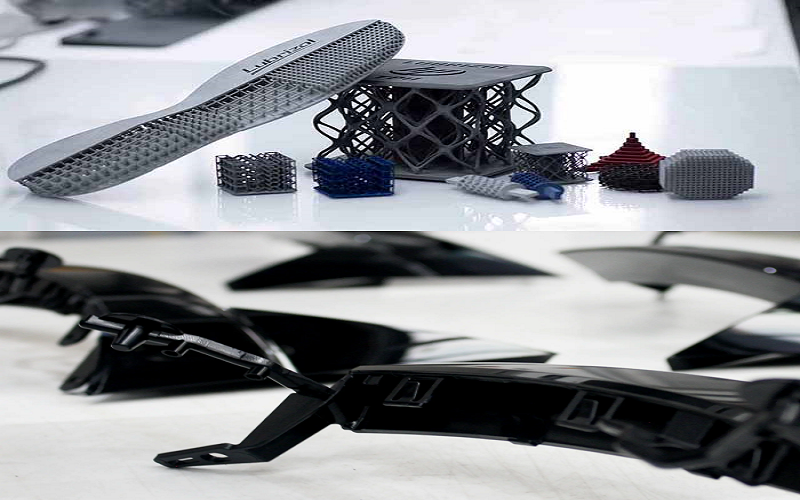
Share :
Share :
One of the most preferred manufacturing methods when it comes to the manufacture of plastic products is injection molding. This manufacturing is highly embraced and is designed to ensure that businesses get exactly what they expect. Injection molding is one of the plastic manufacturing processes that feature incredible efficiency and accuracy.
It comes with great advantages that businesses enjoy working with. However, you need to ensure that you work with qualified injection molding manufacturers when it comes to this process. There are different options for you to work with to ensure that you get the best plastic injection molding service.
If you are wondering what injection molding is, then you have come to the right place. Plastic injection molding is a manufacturing process that features the use of injection molds. In this process, you work with mold designs where the molten plastic material is injected into to begin the production process.
When the molten material is introduced, it takes the shape of the mold and results in your final product. At this stage, the product is allowed to cool to ensure that your products feature incredible durability and endurance. Plastic injection molding is an incredible manufacturing process that comes with different advantages you can take advantage of.
In the injection molding process, the mold is one of the most integral parts of the production process. The mould design should be done right with a keen concentration on other aspects of the manufacturing process. Injection molds are designed to be the determinant of the quality and design of the products you invest in.
They are primarily used to help your products take shape and ensure that you are investing in products that will meet your needs. You need to ensure that the mold-making and design process is done accurately for the best results. Working closely with your chosen injection molding manufacturers will give you the best results when it comes to injection molds. They will take into account your product design and develop a working mold that is designed to cater to your needs.
Injection molds are made in a variety of ways to ensure that they offer the perfect results when in use. These manufacturing processes are designed to present different advantages and will be used in varied applications. Some of the manufacturing processes you can expect in the mold making process include:
CNC machining for mold making is one of the most advanced and relied upon methods. A lot of manufacturers work with advanced technology that controls the movements and operations of the mills, lathes, and other machines.
In this manufacturing process, the mold design and mold-making processes are highly automated. The use of computer-aided design software otherwise known as CAD comes in handy during this process. After the design process, the mantle is then taken to computer-aided ( CAM ) software where all the instructions are acted upon.
This process features the use of electrodes that are fabricated out of graphite or copper. These electrodes are used to obtain the desired shape. Once that is done, it is then mounted in an EDM machine and submerged in dielectric fluid.
This process results in the formation of the old you will be using in the injection molding process. The electrical discharge machining process comes in handy when looking to achieve complex mold designs. This process is designed to ensure that you get the exact mold design with ease.
When it comes to plastic injection molds, you need to ensure that you invest in the right option to meet your needs. These molds will be the base of your products and should be designed to ensure that they deliver your desired results. With this in mind, there are a few things you need to consider when investing in plastic molds. These things include:
The molds used in the injection molding process can be manufactured using a variety of materials. The type of material you choose will highly depend on the kind of products you are working on producing. The different types of materials come with varied aspects that are designed to be used in different applications.
For instance, if you are working with bulk products you would need materials that can accommodate the weight and offer accurate results. On the other hand, with smaller products, lighter materials would work just fine. With this in mind, the best thing to do is consult with your manufacturer who will help guide you. They will advise you on the best material or combination of materials following the products you are looking to invest in.
The wall thickness of your mold is an important aspect for you to consider and ensure that it is done right. Your manufacturers know the best way to ensure that the wall thicknesses of your mold are perfect to meet your needs. When it comes to the thickness of the walls found in the injection molds, the aim is uniformity.
These walls should feature a consistent thickness that allows for the injected material to flow uniformly. If some parts are thicker than others, this will result in deformities once the product is manufactured. The injection manufacturers you choose to work with will ensure that they feature the perfect thicknesses to meet your needs.
Ribs are added to the mold when the walls being featured are thinner and are designed for smaller products. These ribs are designed to ensure that the products form accurately and result in efficient items you can work with.
They are also designed to reduce any risks of deformation which is an important aspect. When working with injection mold manufacturers, they’ll help advise on the need for ribs in your molds. This is why working with a qualified plastic injection molding manufacturer is essential.
Mold shrinkage is something that happens a lot of times and should be taken into consideration. Normally, the shrinkage that is expected is always about 20% by volume. However, this shrinkage normally affects some materials that you use. For instance, with crystalline and semi-crystalline materials, you can expect more thermal shrinkage.
On the other hand, amorphous materials will experience less shrinkage. This goes to show that the extent of the shrinkage experienced is highly dependent on the type of materials you are working with. Your manufacturers will however have ways to help minimize the extent of the shrinkage experienced despite the kind of materials you are using.
The size and design of the products you are looking to manufacture will play a big role when it comes to the manufacture of plastic molds. Your mold should feature the exact dimensions you are looking to be working with. This will ensure that you are investing in quality products designed to meet your needs.
On the other hand, the design of your products should also feature when it comes to mold design. With this in mind, you can create molds that feature the exact designs you expect on your products. The design will also help determine the manufacturing method that will be used.
Injection molds are an important aspect when it comes to the injection molding process. They are designed to be an integral part that determines the result of the products you invest in. Building molds to be used in the plastic injection molding process will require you to consider a few aspects that will ensure you end up with the best results. Working closely with an injection molding manufacturer will improve your chances of investing in quality molds for your products.
Please contact us using the form below or emailing (harry@fowmould.com)