Understanding the basics of injection mold design is crucial for anyone involved in the manufacturing process of plastic parts. Injection mold design is a complex process that requires a deep understanding of the properties of different materials, the mechanics of the molding machine, and the functional requirements of the final product. The design process involves numerous considerations, from material selection and wall thickness to the location of gates and ejector pins. By mastering these aspects, one can ensure a smooth manufacturing process, minimize defects, and produce high-quality plastic parts.
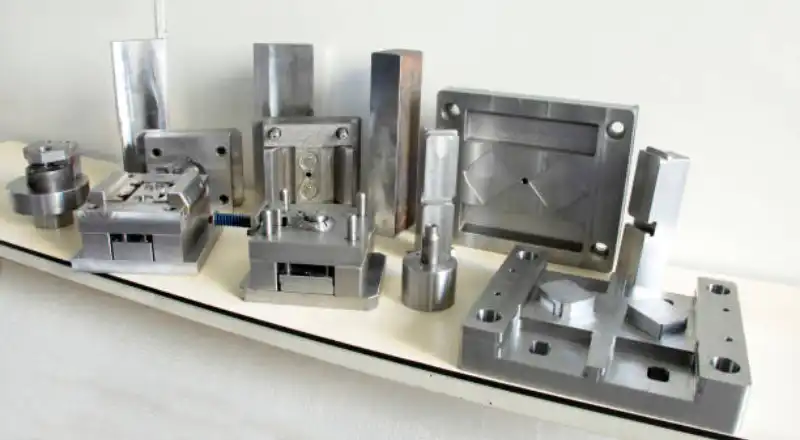
Applications of Injection Molding
Injection molding is a versatile manufacturing process used in a wide range of industries. From automotive and aerospace to consumer products and medical devices, injection molding is used to create complex, high-quality parts in large volumes. The process is favored for its ability to produce parts with intricate geometries, excellent surface finish, and high repeatability. With the right injection mold design, manufacturers can create anything from tiny Lego pieces to large car panels.
- Automotive Industry
- Medical Field
- Consumer Electronics
- Packaging Industry
- Toy Industry
- Aerospace and Defense
- Construction Industry
Injection Molding Process
- Product Conceptualization: This initial stage involves identifying the product requirements, objectives, and specifications. This process should consider the product’s primary function, its interaction with other components (if applicable), and user experience and aesthetics.
- Material Selection: Selecting the appropriate plastic material depends on the product’s durability, flexibility, and thermal and chemical resistance requirements. Common materials used include polymers like polyethylene, polystyrene, or nylon. The material selection will also impact other design choices and the performance of the finished product.
- Preliminary Mold Design: Using the product specifications, mold designers start by creating a 3D model of the mold using computer-aided design (CAD) software. This model shows the shape and size of the mold and includes details of the cavity, core, gating system, ejection system, and cooling system.
- Simulation and Optimization: By using software like Computer-Aided Engineering (CAE), designers can simulate the flow of molten plastic into the mold, which helps identify potential issues such as air pockets, uneven filling, or warpage. The mold design can be refined and optimized based on the simulation results.
- Finalize Design: Once the design and simulation are satisfactory, they finalize the mold’s design. Factors like gate location, ejector pin placement, parting line location, and draft angles are reviewed and adjusted if needed.
- Mold Fabrication: The detailed mold design is now sent for manufacturing. This process may involve CNC machining or Electrical Discharge Machining (EDM) to create a high-precision mold from durable materials like steel or aluminum.
- Mold Testing: After fabricating the mold, it undergoes testing by creating sample parts. These parts help verify the quality of the mold and identify any necessary design changes. If problems are found, the mold may return to the manufacturing process for adjustments.
- Final Production: Once the mold passes all tests, it moves into the actual production operation. The injection molding machine uses the mold to produce the plastic parts, which are then inspected for quality.
Injection Mold Design Considerations
Designing a mold for injection molding is a complex task that requires a deep understanding of the molding process, the properties of the plastic material, and the functional requirements of the part. Some of the key considerations in injection mold design include the choice of material, the design of the part, the location of the gates and ejector pins, and the prevention of defects. By carefully considering these factors, designers can create a mold that produces high-quality parts with minimal waste and downtime.
Material Choices
The choice of material is one of the most important decisions in injection mold design. The material must be suitable for the molding process, have the necessary physical and chemical properties for the part, and be cost-effective. Common materials used in injection molding include polymers such as polyethylene, polystyrene, and polycarbonate, as well as engineering plastics like nylon. The choice of material can have a significant impact on the design of the mold, the molding process, and the quality of the final part.
Material | Characteristics |
ABS (Acrylonitrile Butadiene Styrene) | ABS is known for its toughness, gloss, and resistance to temperature changes, making it ideal for products needing high durability. |
Polypropylene (PP) | PP is lightweight, has excellent chemical resistance, and is great for packaging and living hinges. |
Polyethylene (PE) | PE is highly versatile and comes in various densities. It’s often used in plastic film applications. |
Polystyrene (PS) | PS is available in both a general-purpose form and a high impact form. It’s often used in disposable cutlery and CD cases. |
Polycarbonate (PC) | PC is strong, has high impact resistance, and transparency. Used in products like bullet-proof glass and eyewear. |
Polyethylene Terephthalate (PET) | PET is known for its clarity, toughness, and resistance to gases and moisture. It’s widely used in beverage bottles. |
Polyvinyl Chloride (PVC) | While PVC is harder to process, it’s highly versatile and used in everything from pipes to cable insulation. |
Nylon (Polyamide) | Nylon is strong and temperature resistant, often used in gears and bearings. |
Acetal (Polyoxymethylene, POM) | Acetal offers high stiffness and friction resistance, often used in gears and fasteners. |
Polyurethane (PU) | PU is highly resilient and flexible, often used in foam and adhesive applications. |
Wall Thickness
The wall thickness of the part is another critical consideration in injection mold design. The thickness of the walls can affect the flow of the plastic in the mold, the cooling time, and the strength and appearance of the part. A uniform wall thickness is generally recommended to ensure even cooling and minimize warping and sink marks. However, the ideal wall thickness can vary depending on the material, the part design, and the molding process.
Resin Types | Wall Thickness (inches) |
ABS (Acrylonitrile Butadiene Styrene) | 0.045 – 0.140 |
Polypropylene (PP) | 0.025 – 0.150 |
Polyethylene (PE) | 0.030 – 0.200 |
Polystyrene (PS) | 0.035 – 0.150 |
Polycarbonate (PC) | 0.040 – 0.150 |
Polyethylene Terephthalate (PET) | 0.030 – 0.125 |
Polyvinyl Chloride (PVC) | 0.025 – 0.150 |
Nylon (Polyamide) | 0.030 – 0.115 |
Acetal (Polyoxymethylene, POM) | 0.030 – 0.120 |
High Impact Polystyrene (HIPS) | 0.040 – 0.150 |
Bosses
Bosses are protruding features on a part that are used for mounting or assembly. In injection mold design, bosses must be carefully designed to ensure they can be molded accurately and without defects. This often involves adding radii to the base of the bosses to reduce stress concentrations, and ensuring the wall thickness of the bosses is less than the wall thickness of the part to prevent sink marks.
Ribs
Ribs are thin, raised features on a part that are used to increase its stiffness without adding much weight. In injection mold design, ribs must be carefully designed to ensure they can be molded accurately and without defects. This often involves adding draft angles to the ribs to facilitate ejection, and ensuring the wall thickness of the ribs is less than the wall thickness of the part to prevent sink marks.
Parting Lines
The parting line is the line where the two halves of the mold meet. In injection mold design, the location of the parting line can affect the appearance and functionality of the part. Designers must carefully consider the location of the parting line to minimize its impact on the part and ensure it does not interfere with the function of the part.
Gates
The gate is the point where the plastic enters the mold. The location and design of the gate can have a significant impact on the flow of the plastic in the mold, the quality of the part, and the ease of ejection. In injection mold design, the gate must be carefully located to ensure even filling of the mold and minimize defects. Different types of gates, such as edge gates and tunnel gates, can be used depending on the part design and molding process.
Gate Type | Description |
Sprue Gate | Simple and inexpensive, the sprue gate is ideal for single cavity molds where the gate marks are not a concern. |
Edge Gate | Standard in many applications, the edge gate is placed on the edge of the part, offering good control over the flow of material. |
Submarine (or Tunnel) Gate | Used for automatic degating, the submarine gate allows the material to flow underneath the part and into the cavity. |
Fan Gate | The fan gate is wider than a conventional edge gate, allowing for a larger volume of material to be injected speedily. It reduces stress and provides an even packing pressure. |
Ring Gate | Typically used in cylindrical or spherical objects, the ring gate ensures even flow and minimizes weld lines. |
Diaphragm Gate | Used for hollow, circular parts like bottle caps, the diaphragm gate ensures an even flow of material and reduces weld lines and internal stresses. |
Tab Gate | Used for large parts, the tab gate helps avoid jetting, though it requires an additional step to remove the tab gate from the molded part. |
Hot Tip Gates | Commonly used in hot runner systems, the hot tip gate reduces stress and improves part finish but may leave a small visible gate mark. |
Disc Gate | Used for larger parts with a flat surface, the disc gate provides improved control over the filling process, which can reduce the occurrence of defects like warping and shrinkage. |
Guideline for Gate Location | Description |
Gate Away from the Wall | Gates should be located away from a part’s thickest areas to reduce the occurrence of sink marks due to slower cooling rates. |
Uniform Filling | To facilitate even and efficient filling, gates should be positioned to minimize flow length and ensure simultaneous filling of different sections. |
Avoid Intersections and Corners | Avoid placing the gate at corners, intersections, or abrupt changes in thickness. Such locations could cause material pressure loss or stresses, leading to deformations or cracks. |
Minimize Visibility | Place gates in locations where vestiges (marks left by gates) are either invisible or least noticeable in the final product for aesthetic appeal. |
Avoid Hindrance in Functionality | Gate placement should not interfere with the part’s functionality or present problems during assembly processes. |
Anticipate Shrinkage and Warping | Consider how gate positioning could influence the rate of cooling, and consequently, the shrinkage and warping of the part. |
Air Venting | Gates should be placed to allow any trapped gases and air to escape during the molding process. |
Ease of Degating | If manual gate removal is necessary, gate positions should be easily accessible. |
Ejector Pins
Ejector pins are used to eject the part from the mold once it has cooled and solidified. The location and size of the ejector pins can affect the appearance and quality of the part. In injection mold design, the ejector pins must be carefully located to ensure they do not leave visible marks on the part and do not interfere with the function of the part.
Sink Marks
Sink marks are depressions in the surface of the part that occur when the part cools and shrinks unevenly. They are often caused by variations in wall thickness, with thicker areas cooling and shrinking at different rates than thinner areas. In injection mold design, sink marks can be minimized by ensuring a uniform wall thickness and by carefully designing features such as bosses and ribs.
Textures
Textures can be added to the surface of the part to improve its appearance or functionality. In injection mold design, textures must be carefully considered to ensure they can be accurately reproduced in the mold. The choice of texture can affect the flow of the plastic in the mold, the ease of ejection, and the appearance of the part.
Accurate Tolerances
Maintaining accurate tolerances is crucial in injection mold design. The tolerances can affect the fit, function, and appearance of the part. Designers must carefully consider the tolerances in the design of the mold, taking into account the properties of the material, the molding process, and the functional requirements of the part.
Shut-Off Angles
Shut-off angles are used in the mold to prevent plastic from flowing into certain areas. In injection mold design, shut-off angles must be carefully designed to ensure they effectively block the flow of plastic and do not cause defects or damage to the mold.
Draft Angle Orientation
The draft angle is the angle of the walls of the part relative to the direction of ejection. In injection mold design, the draft angle must be carefully considered to ensure the part can be easily ejected from the mold. The draft angle can also affect the appearance and functionality of the part.
FAQ
What are the common defects in injection mold design and how can they be prevented?Common defects in injection mold design include sink marks, warping, and short shots. These defects can often be prevented by careful design of the mold, including considerations of wall thickness, gate location, and material selection.How does injection mold design affect the final product quality?The design of the injection mold directly impacts the quality of the final product. Factors such as wall thickness, gate location, and material choice can influence the appearance, strength, and functionality of the molded part. A well-designed mold ensures even cooling, minimizes warping, and reduces the risk of defects like sink marks.What are the challenges in maintaining critical tolerances in injection mold design?Maintaining critical tolerances is essential for the fit, function, and appearance of the molded part. Challenges arise due to material shrinkage, variations in the molding process, and tool wear. It’s crucial to account for these factors in the design stage and to work closely with the molder to ensure consistent production.
Conclusion
Understanding the intricacies of injection mold design is pivotal for producing high-quality plastic parts. From material selection to the nuances of gate location and wall thickness, every aspect plays a vital role in the final product’s quality and functionality. By considering the factors discussed in this guide and partnering with experienced molders, one can optimize the design process, reduce the risk of defects, and ensure the successful production of top-tier plastic components.
Choosing FOWMould
When diving into the world of injection mold design, partnering with a reputable company like FOWMould can make all the difference. With their expertise in mold design and manufacturing, they offer invaluable insights and guidance throughout the design process. Their commitment to quality and precision ensures that your designs are not only functional but also cost-effective and efficient. By choosing FOWMould, you’re investing in a partnership that prioritizes excellence in every facet of injection molding.