ABS (acrylonitrile-butadiene-styrene) and PP (polypropylene) are two common materials in modern manufacturing and daily life.
They are found in car parts, electronic casings, food containers, pipes, and countless other products, thanks to their distinct properties. But what exactly sets them apart, and why should you care?
Knowing the differences between abs plastic and pp plastic material helps in selecting the appropriate material. Manufacturers seeking to optimize product performance and consumers making informed purchases benefit from understanding each material’s strengths and weaknesses.
This comparison will cover performance, processing characteristics, and application scenarios, highlighting each plastic’s strengths and suitability.
Overview ABS Plastic and Polypropylene
Acrylonitrile Butadiene Styrene is produced by combining three monomers: acrylonitrile, butadiene, and styrene.
Each of these components contributes to ABS’s overall properties: acrylonitrile offers high hardness, strength, heat resistance, and corrosion resistance; butadiene provides impact resistance and toughness; and styrene contributes high surface gloss, easy colorability, and processability.
Adjusting the proportions of these components tailors ABS’s properties for different applications, such as high-impact, heat-resistant, or high-gloss ABS.
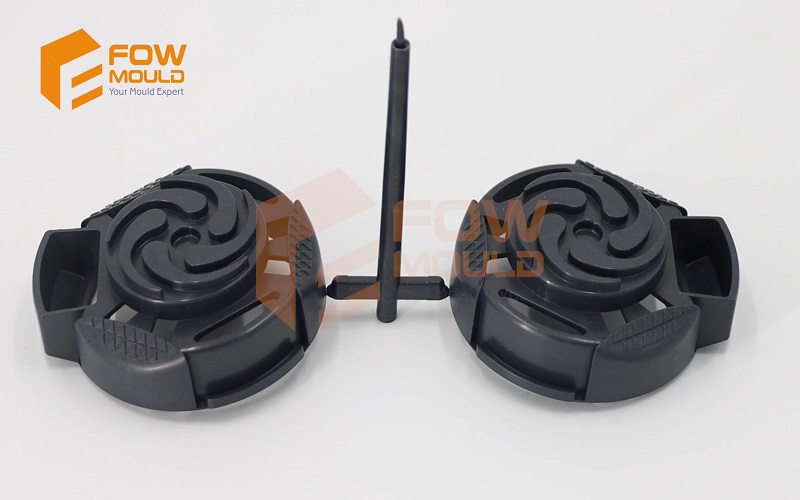
Polypropylene is a semi-crystalline thermoplastic polymer produced through the addition polymerization of propylene monomers.
Typically appearing as a white, waxy solid, it is non-toxic, odorless, transparent, and lightweight, making it the least dense among thermoplastic resins.
Depending on the spatial arrangement of the methyl side chains, it can be classified into three distinct types of polypropylene—isotactic, syndiotactic, and atactic—based on the spatial arrangement of its molecular structure.
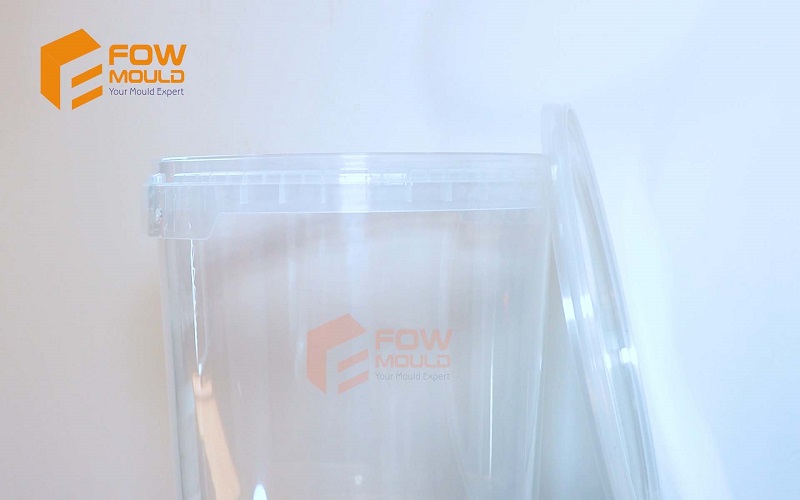
Performance Comparison of ABS and PP Materials
Performance characteristics like mechanical stress resistance, temperature tolerance, and chemical resilience are key when comparing polypropylene and abs.
Examining these aspects reveals how each material performs under various conditions.
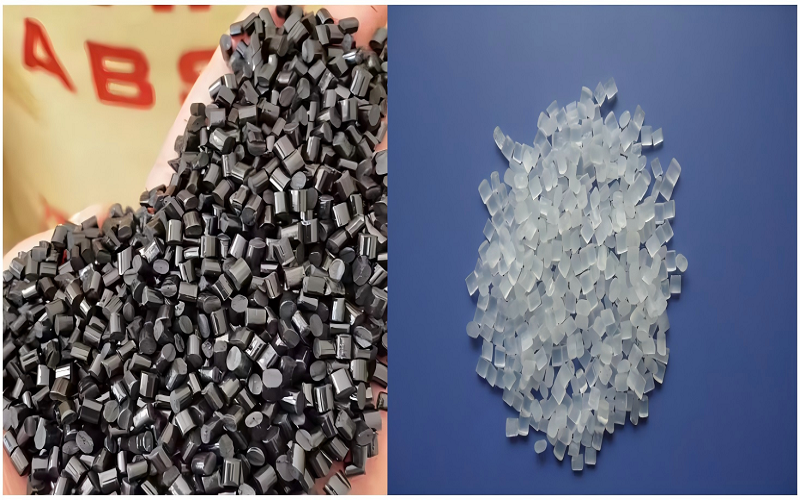
Mechanical Strength and Durability
Known for high impact resistance and excellent dimensional stability, ABS has a higher tensile strength than polypropylene, making it tougher and more impact-resistant. This makes ABS ideal for durable products like protective casings, automotive components, and LEGO bricks.
Although less strong than ABS, polypropylene offers greater flexibility and excels at resisting fatigue from repeated bending. Its semi-crystalline structure allows high flexibility and elongation at break, making PP suitable for hinges, flexible packaging, or ropes, where long-term durability is crucial.
ABS resists warping better than polypropylene, maintaining stability across a wide temperature range with less shrinkage during molding. However, PP’s flexibility and resilience make it ideal for applications requiring high flexibility and fatigue resistance.
Temperature Resistance and Thermal Properties
Temperature resistance is a critical factor when deciding between ABS and PP. ABS offers moderate heat resistance, with an operating range of 80–100°C before softening. Its glass transition temperature (Tg), the point at which it transitions from a rigid to a rubbery state, is around 105°C, while its high melting point ranges from 217–237°C.
However, prolonged exposure above 100°C can lead to deformation, restricting its suitability for high-temperature environments like under-hood automotive plastic parts or containers for boiling water.
Polypropylene, by contrast, outperforms ABS in heat resistance, comfortably managing temperatures from 100–120°C under light loads and up to 150°C for short-term use.
Its glass transition temperature is lower, typically around 0°C, reflecting its flexibility, but its melting point, though not as high as ABS, falls between 160–170°C.
This allows PP to endure boiling water and steam (up to 120°C continuously), making it a top choice for applications such as microwaveable containers, medical sterilization trays, and hot-fill packaging where sustained heat tolerance is essential.
Chemical Resistance
Polypropylene generally outperforms ABS in chemical resistance, especially against organic solvents. Its inert nature ensures it remains unaffected by harsh conditions, making it ideal for laboratory bottles, chemical piping, and battery casings.
ABS shows good resistance to various fluids, including water and many acids, but is sensitive to chemicals like acetone, alcohols, and oils. This sensitivity can cause ABS to swell, crack, or dissolve, limiting its use in environments with frequent exposure to aggressive chemicals.
Property | ABS | Polypropylene |
Density (g/cm³) | 1.05–1.18 | 0.90–0.92 |
Melting Point (°C) | 217–237 | 160–170 |
Heat Deflection Temperature (°C) | 80–100 | 100–120 |
Tensile Strength (MPa) | 40–50 | 25–35 |
Shrinkage Rate (%) | 0.4–0.9 | 1.0–2.5 |
Moisture Absorption (%) | <1 (requires drying) | Very low (<0.1) |
ABS vs PP:Applications
Both two materials have a wide range of various applications ,helps determine which material suits your needs.
Typical Uses of ABS Plastic Products
The blend of impact strength, toughness, and aesthetic versatility makes ABS ideal for applications that require high performance and durability, such as automotive, electronics, medical, and consumer products.
In the automotive industry, it is used for dashboard components, bumper trims, and interior panels due to its impact resistance and structural integrity. Its ease of painting and plating also enhances vehicle aesthetics.
In electronics, ABS is used for household appliances like computer keyboards and TV casings. LEGO bricks rely on ABS for precision molding, vibrant color retention, and toughness, ensuring secure connections and durability.
ABS shines in products where mechanical performance and visual quality are non-negotiable, often justifying its slightly higher cost.
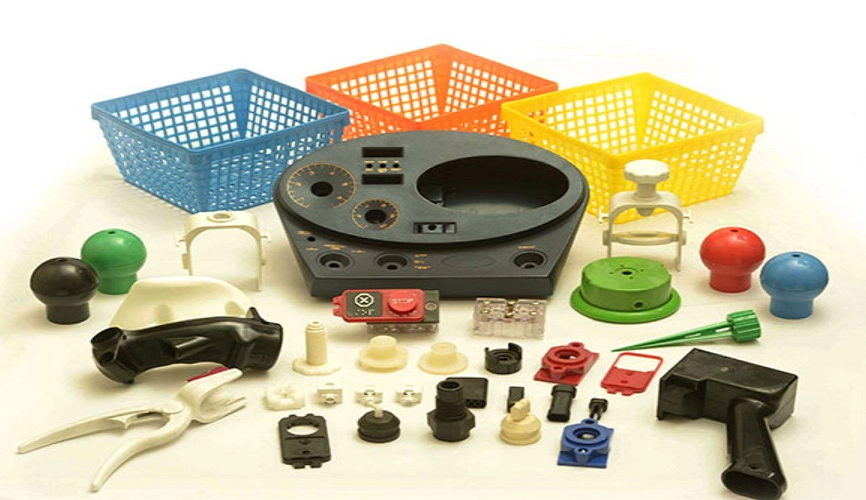
Typical Uses of PP Plastic Products
PP is mainly used for applications that require high flexibility and low weight, such as packaging, textiles, furniture, and household products.
In the food industry, PP’s resistance to heat and chemicals makes it ideal for microwaveable containers, reusable lunch boxes, and yogurt tubs, ensuring safety and longevity with hot or acidic contents.
In construction and textiles, PP is used for pipes and fittings due to its corrosion resistance and ability to handle hot water (up to 120°C).
Additionally, PP is spun into fibers for carpets, ropes, and non-woven fabrics like reusable bags or medical masks, leveraging its flexibility, fatigue resistance, and low density for lightweight yet sturdy textiles.
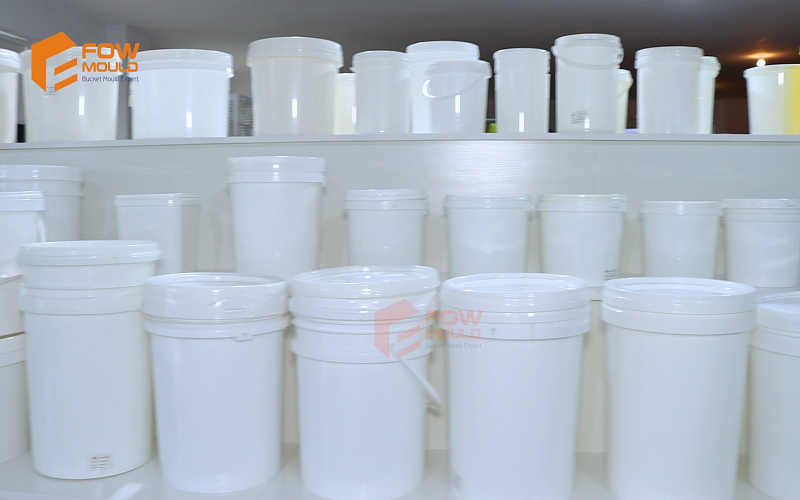
Differences In Processing Methods Between PP and ABS
The distinct physical properties and chemical properties of ABS and PP lead to significant differences in their processing methods, impacting how each material is shaped into final products.
Primary Methods
ABS Injection molding is the most common technique for ABS material, ideal for producing complex, precise components like electronic housings and automotive parts.
ABS also supports extrusion, thermoforming, and is widely used in 3D printing via fused deposition modeling (FDM) for creating detailed, durable prototypes.
Polypropylene is processed through injection molding (e.g., container lids), extrusion (e.g., pipes and films), and blow molding (e.g., bottles). Its semi-crystalline nature also makes it suitable for fiber spinning in textiles.
Processing Conditions
ABS, with a melting temperature of 217–237°C, requires elevated mold temperatures (50–80°C) during molding processfor surface smoothness and dimensional stability. For 3D printing, acrylonitrile butadiene styrene needs a heated bed and an enclosed build chamber to prevent warping from thermal contraction.
PP has a lower melting point (160–170°C), with processing temperatures ranging from 200–250°C. It typically requires lower mold temperatures, making it less demanding on equipment than ABS.
Processing Characteristics
ABS’s amorphous structure ensures uniform shrinkage during cooling, making it ideal for high-precision parts. Post-processing, it delivers a high-gloss surface and supports treatments like painting, bonding, and electroplating. However, ABS is sensitive to processing temperatures and must be carefully controlled to avoid thermal decomposition.
PP is straightforward to process, benefiting from a low melting point and excellent flowability, reducing energy consumption and making it suitable for large-scale production. Its semi-crystalline structure imparts superior toughness, though the cooling process requires careful management of crystallization to avoid stress concentration.
PP’s low surface energy results in poor adhesion and paintability, often requiring surface treatments to enhance bonding. Additionally, its high plastic shrinkage rate can lead to dimensional inaccuracies, particularly in thicker parts, posing challenges for precision molding.
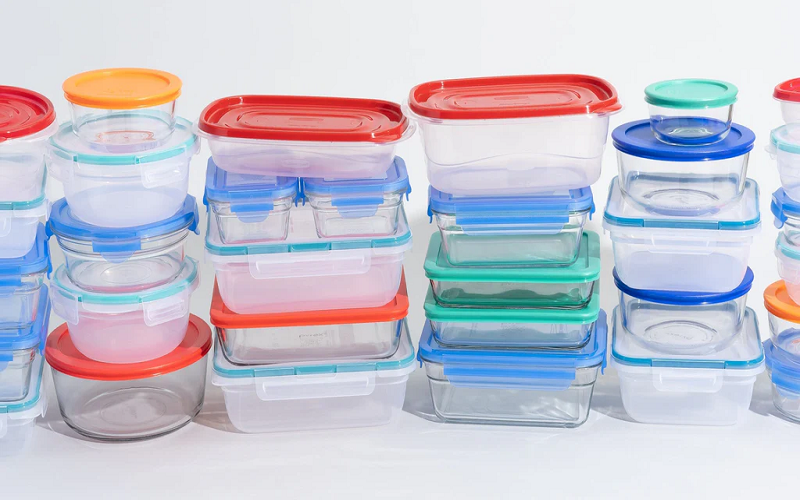
PP vs ABS:Advantages and Disadvantages
Both PP and ABS have their own advantages and disadvantages. Knowing these helps in making an informed decision about which material suits your specific needs.
Advantages Of ABS Plastic
ABS plastic’s high strength and hardness make it suitable for products needing to withstand external forces or high temperatures. It has excellent impact resistance, a smooth surface, and good UV resistance. ABS is also easy to process into complex shapes using methods like injection molding, extrusion, and blow molding.
ABS is aesthetically appealing due to its smooth, glossy finish, making it easy to color and paint. Additionally, ABS offers good electrical insulation properties, unaffected by temperature, humidity, and frequency.
Disadvantages Of ABS Plastic
Despite its advantages, ABS plastic has drawbacks. Its heat resistance is relatively poor, with a maximum operating temperature of around 80°C, making it unsuitable for high-temperature environments. The complex production process leads to higher costs compared to other plastics. Additionally, ABS is highly flammable and requires careful handling for fire safety.
Advantages Of PP Plastic
Polypropylene is lightweight, making it easy to transport and install. It has excellent chemical resistance, able to withstand acids, alkalis, and salts, making it durable in harsh chemical environments. PP can handle higher temperatures, with a maximum operating temperature of around 100°C, making it suitable for high-temperature applications.
PP is environmentally friendly and non-toxic, ideal for food contact products like containers and cups. Its smooth surface makes it easy to clean and maintain.
Disadvantages Of PP Plastic
Polypropylene has lower impact resistance and a less glossy surface, making it less suitable for high-load scenarios. Its hardness is also lower compared to ABS, making it unsuitable for applications requiring high strength.
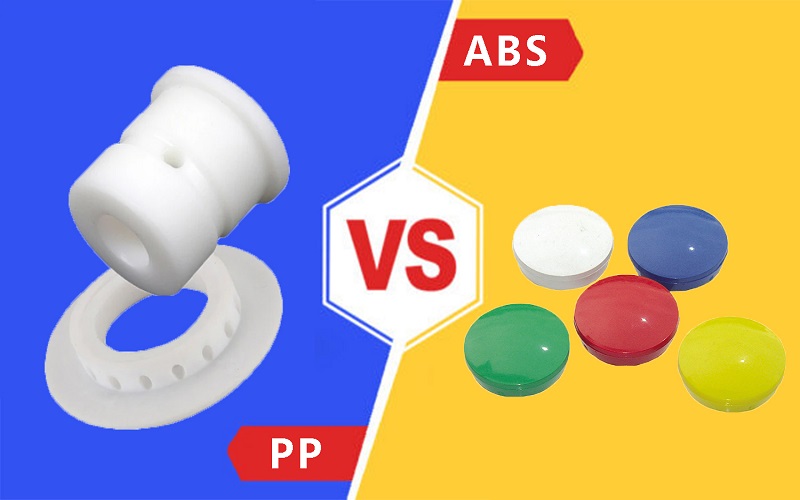
How To Choose Between PP and ABS?
Choosing between PP and abs requires careful consideration of specific application needs.
If your product needs to withstand significant external forces or internal pressure, or if a high level of aesthetic appeal is required, ABS may be the better choice. Its high strength, impact resistance, and excellent mechanical properties make it ideal for applications demanding durability and visual quality.
However, if your product will be used in high-temperature environments or exposed to harsh chemicals, PP might be the better option. Its superior better chemical resistance and higher temperature tolerance make it ideal for such conditions.
For eco-friendly applications, such as food packaging or medical devices, PP is the popular plastic due to its non-toxic composition, proven safety for human contact, and alignment with stringent environmental and safety standards,addressing the common question: “Is polypropylene safe?” with a resounding yes..
Cost is another critical consideration. PP typically offers a more economical solution than ABS, making it an attractive choice for budget-sensitive projects, particularly in high-volume production like disposable goods or utilitarian packaging.
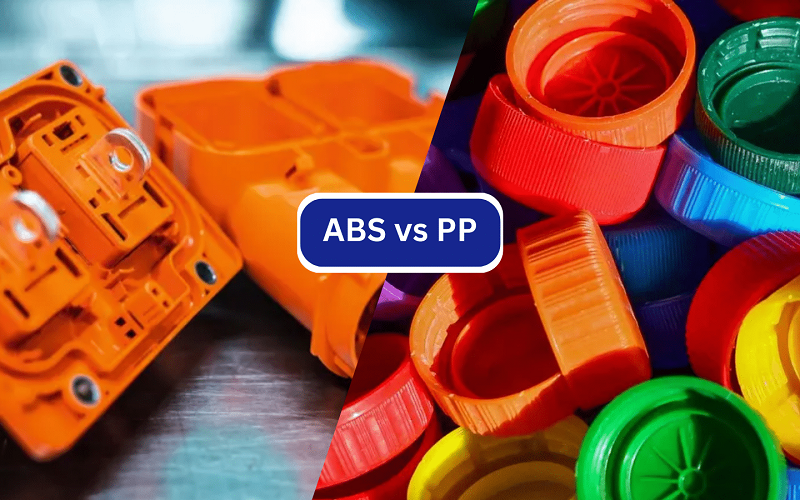
Summary
Polypropylene and ABS plastic each bring unique strengths and weaknesses to the table. ABS excels in impact resistance, mechanical strength, and aesthetic appeal, making it ideal for products requiring durability and a polished finish.
On the other hand, PP offers superior chemical resistance, flexibility, and cost-effectiveness, making it suitable for a wide range of practical applications.
As you consider which material to use, reflect on the specific requirements of your project. Whether you need a plastic that can withstand mechanical stress or one that can handle high temperatures and chemicals, understanding the main differences between pp and abs plastic will guide you to the best choice for your needs.