As the manufacturing industry continues to pursue lightweight, durability, and cost-effectiveness, ABS injection molding technology maintains a significant position globally.
ABS molding is known for its energy efficiency and versatility, making it suitable for applications across automotive, commercial, and electrical sectors.
From automotive components to household appliance casings and toy manufacturing, ABS has become an indispensable material in modern manufacturing due to its superior mechanical properties and surface quality.
This article will delve into the ABS injection molding process, technical points, and its application value, providing practical references for industry practitioners.
What Is ABS Plastic?
ABS (Acrylonitrile Butadiene Styrene) is a polymer made from the copolymerization of three monomers: acrylonitrile (23-41%), butadiene (10-30%), and styrene (29-60%).
As a significant thermoplastic polymer, it is widely used in many fields due to its excellent physical properties, processing performance, and cost-effectiveness.
Its performance characteristics include high impact resistance, wear resistance, and corrosion resistance, making ABS plastic crucial in industries such as automotive, electronics, and home appliances.
ABS plastic initially developed from modified PS, and with its unique toughness, rigidity, and hardness, its usage has become comparable to PS, and its application range has far exceeded PS, evolving into an independent plastic variety.
Since 2000, ABS has been reclassified as a general-purpose plastic, firmly holding the position of the fifth-largest general-purpose plastic variety.
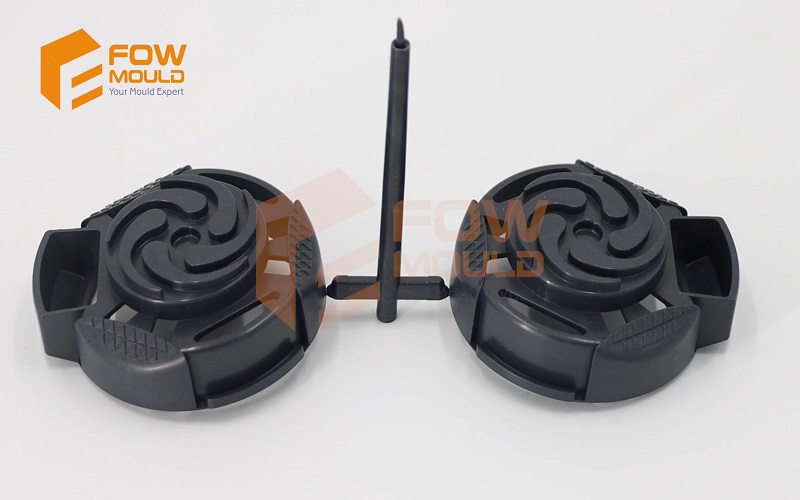
Properties Of ABS Material
ABS plastic integrates the combined properties of its three components: acrylonitrile (A) imparts chemical resistance, high temperature resistance, and surface hardness; butadiene (B) contributes high elasticity and toughness; and styrene (S) enhances thermoplastic processability and improves electrical properties.
Mechanical Properties
ABS plastic exhibits excellent mechanical properties, notably its superior impact strength, enabling its use at extremely low temperatures.
It offers good wear resistance, excellent dimensional stability, and oil resistance, making it suitable for bearings under moderate loads and low speeds. While its creep resistance surpasses that of PSF and PC, it is lower than that of PA and POM.
Thermal Properties
ABS, a heat-resistant thermoplastic, is renowned for its heat stability. Its heat deflection temperature spans from 93°C to 118°C, with an potential increase of about 10°C following annealing.
Even at -40°C, ABS maintains its toughness, ensuring reliable performance across a temperature range of -40°C to 100°C.
Electrical Properties
ABS plastic boasts excellent electrical insulation, which remains largely unaffected by temperature, humidity, or frequency, ensuring consistent performance across diverse environments.
Chemical Resistance
ABS is resistant to water, inorganic salts, alkalis, and various acids, but it is soluble in ketones, aldehydes, and chlorinated hydrocarbons. Exposure to glacial acetic acid, vegetable oils, or similar substances may cause stress cracking.
ABS Material Properties Table | |
Properties | Value |
Density(g/cm³) | 1.05~1.18 |
Modulus Of Elasticity(GPa) | 2 |
Poisson’s ratio | 0.394 |
Hygroscopicity(%) | <1 |
Melting Temperature(℃) | 217~237 |
Thermal Decomposition Temperature(℃) | >250 |
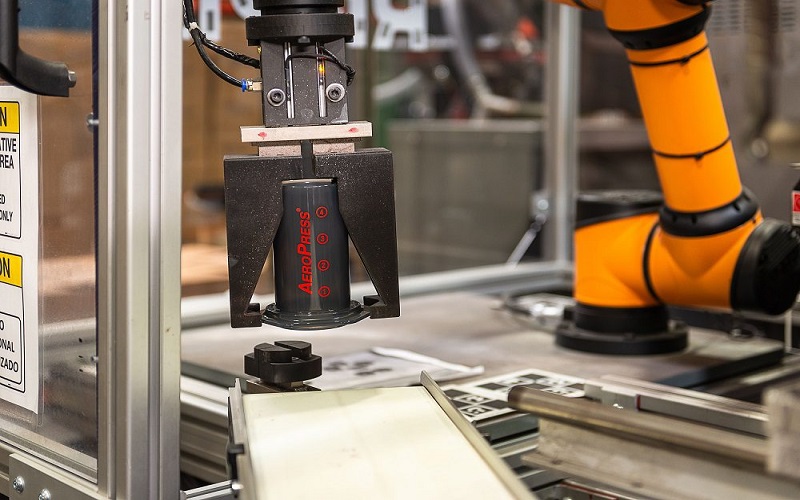
Which Products are suitable for ABS injection molding
Injected Molded ABS Parts have become more and more common in life. Most plastic housings are made of ABS, such as household appliances, electronic products, game consoles, water purifiers, as well as industrial exterior parts, automotive interior parts, high-end garden planters, supermarket shelves, etc.
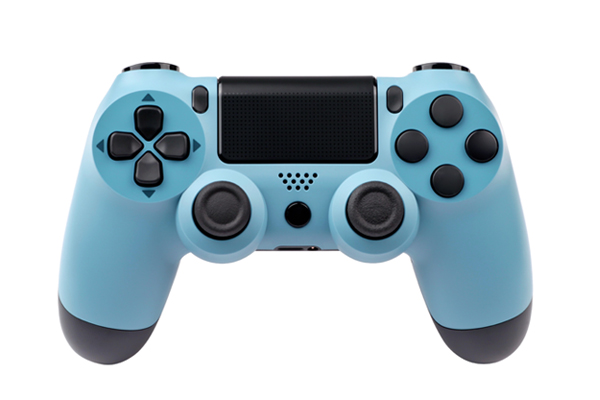
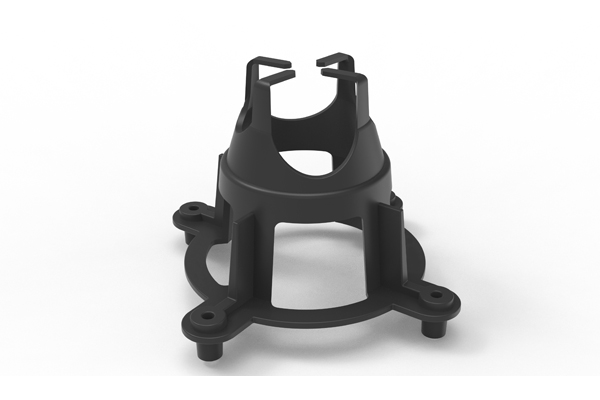
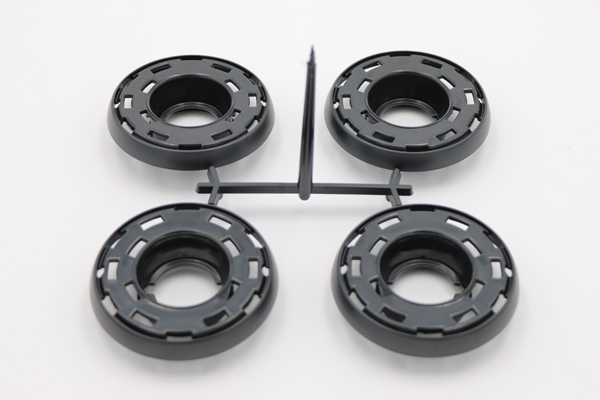
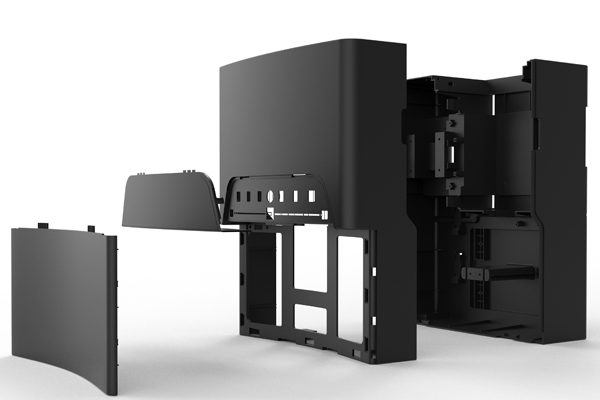
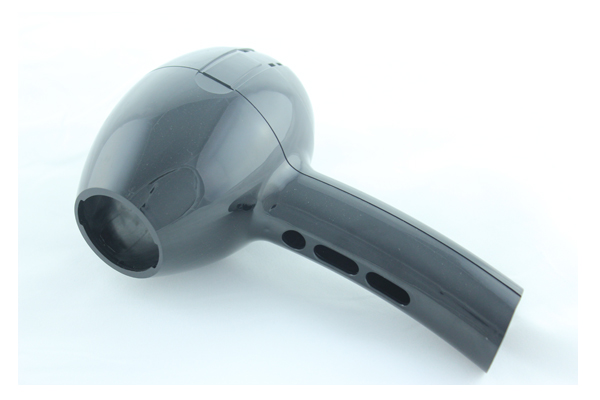
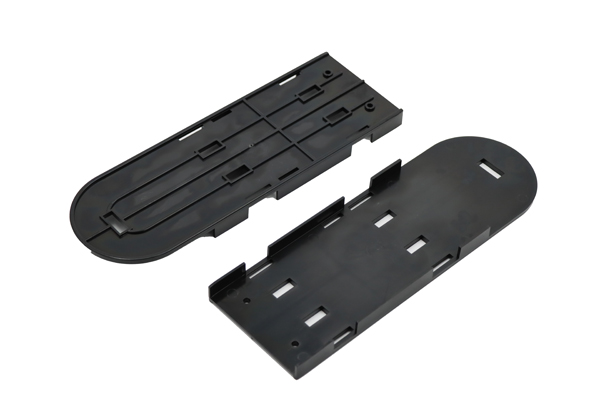
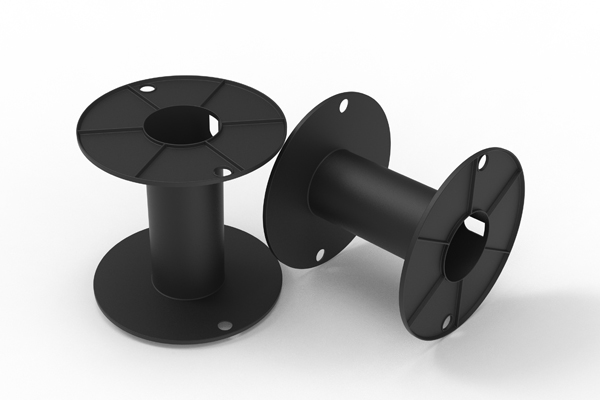
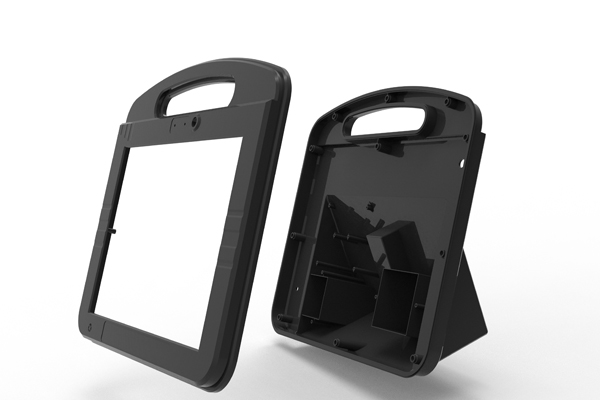
ABS Plastic Parts Design
- ABS Material Type
- Cavity Number
- Shrinkage
- Gate Type
- Mould Type
- Mould Steel
- Tonnage of Machine
- Thickness
- Draft Angle
- Runner Type
According to the complexity of the structure of the ABS product mold to do different processing arrangements, if the mold structure is simple, as long as the CNC milling, EDM processing can be completed mold, if the mold structure is more complex, will carry out a series of processing technology.
For example, CNC, EDM, Deep hole Drill, Lathe, Grinding Machine, Wire-Electrode Cutting, CMM, Polish and Injection.
ABS Material Type: Different ABS material, the MFI is different, which will affect the size and position of the gate runner.
Mould Cavity: Different number of cavities will affect the choice of gate position, usually the number of cavities will be selected according to the size of the injection molding machine.
Shrinkage: The shrinkage rate of different sizes of ABS products will be a little different, the common range is 0.4-07%, 0.5% is recommended.
Runner Type: Hot runner or cold runner.
Mould Type: Two-plate mold or Three-plate mold
Mould Steel: Different mold steel has different mold life, usually we recommend 718 as the mold steel for ABS products.
Tonnage of Machine: When injecting ABS plastic, the injection volume per shot is only 75% of the standard injection volume.
Thickness: The wall thickness of ABS products is 1-4mm, and the minimum wall thickness should not be less than 1mm.
Draft Angle: ≥1.5°, the draft angle not only affects the mold release, but also the appearance and assembly of the product. The side wall of plastic parts with skin pattern, sandblasting and other appearance treatment should take a draft angle of 2°~5° according to the specific situation.
When designing ABS plastic molding parts, it is essential to incorporate appropriate draft angles and optimize wall thickness to ensure easy ejection from molds and minimize defects.
Gate Type: The runner part is as short as possible to save material cost.
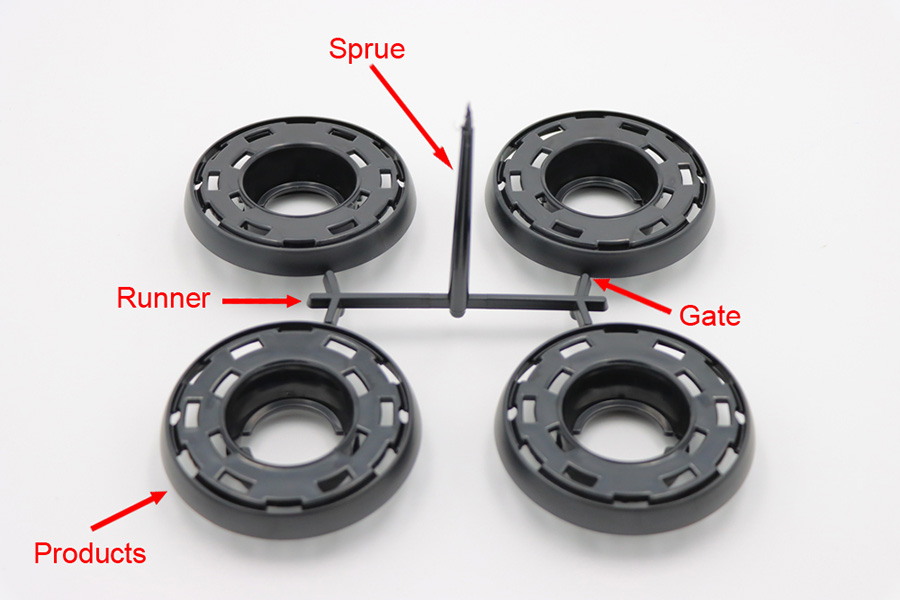
ABS Injection Molding Process
Drying Of ABS Plastic Material
ABS plastic is hygroscopic, which means it can absorb moisture from the air, sufficient drying and preheating before processing, not only to eliminate water vapor caused by the surface of the product smoky bubble, silver, but also help plasticization, reduce the surface color of the parts and cloud pattern. ABS raw materials to control the moisture below 0.13%.
The drying conditions before injection are: 2~3h at 75~80℃ during the dry season or winter, 4~8h at 80~90℃ during the rainy days in summer, and longer drying time of 8~16h if the parts have to achieve a particularly good gloss or the parts themselves are complicated.
It is advisable to convert the hopper of the machine into a hot air hopper dryer so that the dried ABS does not reabsorb moisture in the hopper, but this type of hopper should be monitored for humidity to prevent overheating of the material in case of occasional interruptions in production.
The proportion of recycled material should not exceed 30%, and recycled material should not be used for plating grade ABS.
ABS Molding Process Temperature
The relationship between temperature and melt viscosity of ABS plastic is different from that of other amorphous plastics.
Once it reaches the plasticization temperature (the temperature range suitable for processing, such as 220-250℃), if we continue to raise the temperature blindly, it will lead to the thermal degradation of ABS, which is not very heat resistant, and increase the melt viscosity, make injection more difficult, and decrease the mechanical properties of the parts.
Therefore, although the injection temperature of ABS must be higher than that of polystyrene and other plastics, it cannot have a more relaxed temperature range like the latter.
In some injection molding machines with poor temperature control, when a certain number of injected molded abs parts are produced, more or less yellow or brown coke particles are found embedded in the parts, and it is difficult to remove them by adding new material to the empty injection.
The reason for this is that ABS plastics contain butadiene, which causes degradation and carbonization when a plastic particle adheres firmly to some hard-to-wash surface in the screw tank at high temperatures and is subjected to prolonged high temperatures.
Since high temperature operation can be a problem for ABS, it is necessary to limit the furnace temperature in each section of the barrel. Of course, the applicable furnace temperature varies for different types and compositions of ABS.
For example, for plunger type machines, the furnace temperature is maintained at 180-230°C; for screw machines, the furnace temperature is maintained at 160-220°C.
In particular, it is worth mentioning that ABS is sensitive to changes in various process factors due to its high processing temperature. Therefore, the temperature control of the front end of the barrel and the nozzle part is very important.
It has been proven that any small change in these two parts will be reflected in the part. The greater the temperature variation, the greater the defects such as fusion seam, poor gloss, flying edge, sticky mold, and color change.
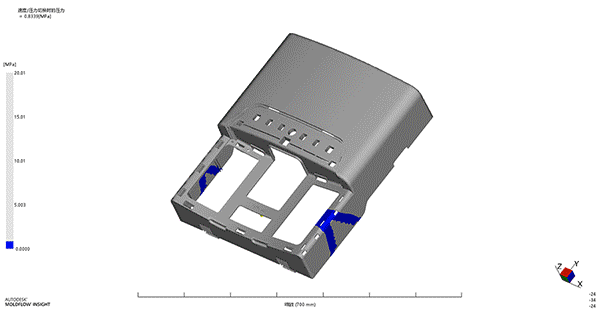
ABS Injection Molding Pressure
Because of the viscosity of ABS, higher injection pressures are usually needed; The molten ABS is injected into a mold cavity at high injection molding pressure, filling the entire mold space.However, lower pressures may be suitable for smaller, simpler, or thicker ABS products.
During the injection process, the pressure in the cavity at the moment of gate closure often determines the surface quality of the product and the degree of silver wire defects.
If the pressure is too low, the plastic shrinks and has a greater chance of disengaging from the cavity surface, resulting in a hazy surface. Pressure is too large, the plastic cavity surface friction is strong, easy to cause sticky mold.
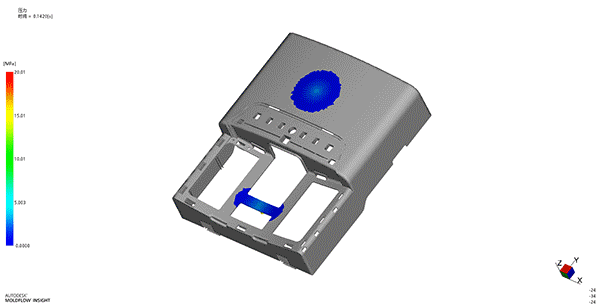
ABS Injection Molding Speed
ABS material with medium injection speed is better. When the molding speed is too fast, the plastic is easy to scorch or decompose and precipitate vaporized products, so that defects such as fusion seam, poor gloss and redness of plastic near the gate appear on the parts.
However, in the production of complex and thin wall injection molded parts, it is still necessary to ensure a high enough injection molding speed, otherwise it is difficult to fill.
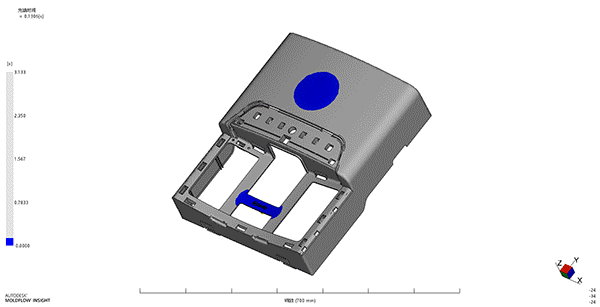
ABS Material Quantity Control
The molding temperature of ABS is relatively high, and the mold temperature is also relatively high. When producing parts with large projection area, the fixed mold temperature should be 70~80℃ and the moving mold temperature should be 50~60℃.
In order to shorten the production cycle and maintain the relative stability of mold temperature, cold water bath, hot water bath or other mechanical shaping method can be used to compensate for the time of cold fixing in the cavity after the parts are taken out.
ABS Material Quantity Control
When injecting ABS plastic into general injection molding machine, each injection volume is only 75% of the standard injection volume.
In order to improve the quality and dimensional stability of the parts, surface gloss and uniformity of color, it is appropriate to require an injection volume of 50% of the standard injection volume.
Plastic Injection Molding Machine Selection
Standard plastic injection molding machine can be used (screw L/D ratio 20:1, compression ratio more than 2, injection pressure more than 150MPa).
If the use of color masterbatch or product appearance requirements are high, the use of a smaller diameter screw. The clamping force is determined according to 4700~6200t/m2, depending on the plastic grade and product requirements.
Main Problems Of ABS products
Whitening
1.The product package slanting top when out of the mold, after the ejected buckle position pulling white.
2.Bad polishing, local sticky mold, slight deformation of the mold, sticky mold parts pull white.
3.Improper ejector layout, slight deformation out of the mold caused by pulling white.
4.deformation of the ejector plate or injection molding machine top stick length, resulting in unbalanced ejections and pull white.
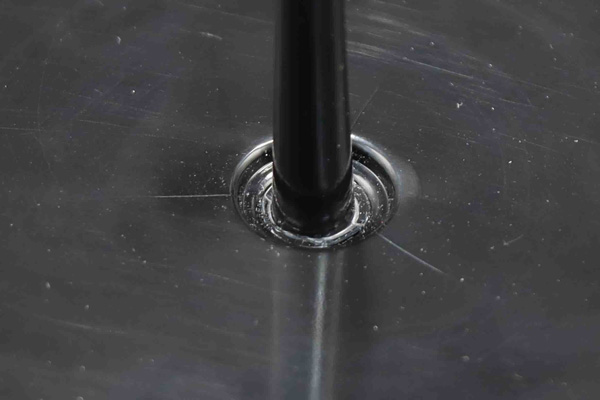
Weld Lines
1.The temperature is low when fusing.
2. the syringe needle is too high, resulting in local glue bit is too thin, the periphery of the first fill, to the center of the intersection to produce fusion line.
3.Multi-point into the pouring produce fusion line
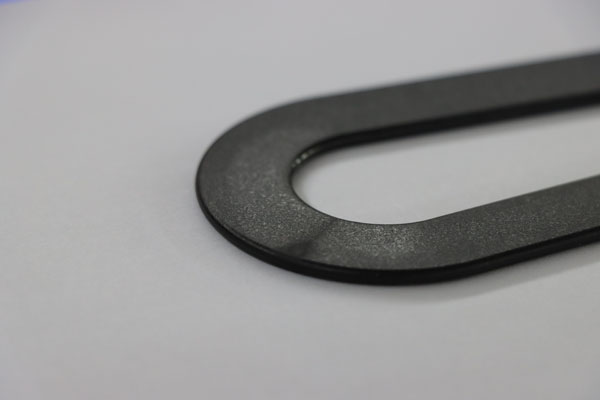
Mold Sticking
1.Bad polishing leads to sticky mold such as tendon position and inlay column position.
2.Deep tendon position does not get enough cooling.
3.Drawing slope is too small.
4.The surface of the skin pattern and sparkle pattern is too rough.
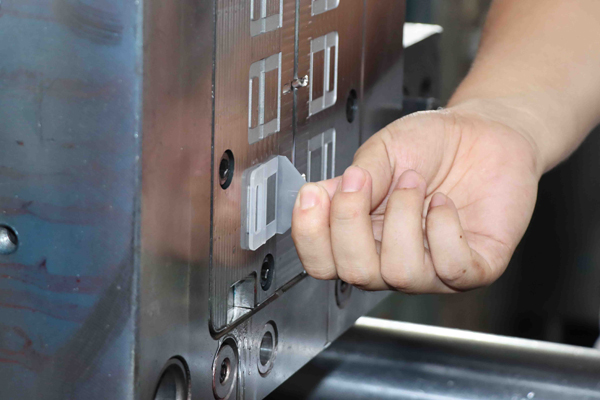
Air Trapping
1. no exhaust, or exhaust too little, exhaust slot is too shallow.
2. multi-point into the pouring, fusion line near the trapped gas (exhaust inserts, exhaust steel, etc.).
3. go unbalanced glue, package glue.
4. Glue material is easy to decompose.
5. The insert structure and eject structure are too little, and the exhaust of insert and eject is limited.
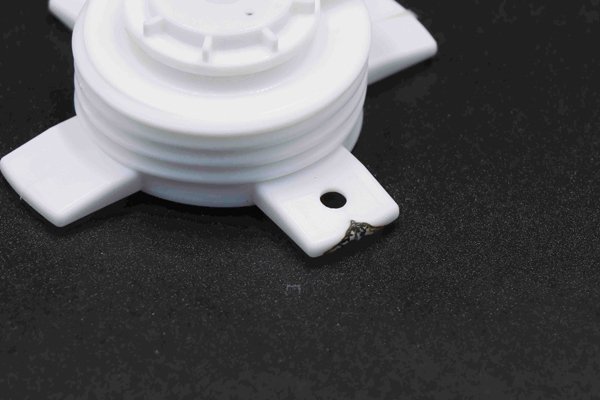
Deformation
1.The holding pressure is too large, the internal stress is large, and the deformation is large within 24h after leaving the mold.
2.Uneven cooling, resulting in warpage.
3.Unreasonable gate position, uneven pouring volume, stress concentration.
4.Local sticking to the mold when leaving the mold leads to pulling deformation.
5.Mold cavity deformation (polishing deformation).
6.The ejector structure is unreasonable, the ejector pin is not under the maximum clamping force, and the ejector is deformed.
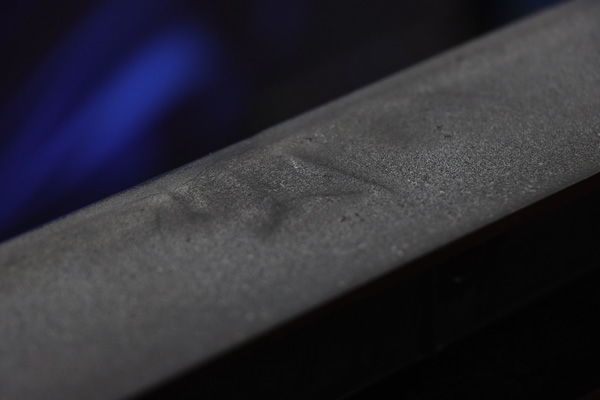
Wrinkling
1.Poor quality of ABS material.
2.Mixed with other plastic material.
3.Mixed with sprue material.
4.Mixed with recycle material.
Cold material
1.There is residual material and rubber powder at the gate pull off.
2.The injection molding machine nozzle is eccentric at the main stream ballway R with cold material.
3.Hot nozzle cold material.
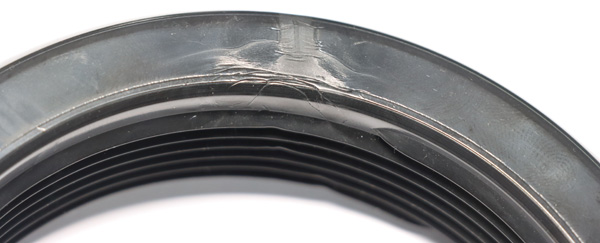
Conclusion
ABS injection molding holds a pivotal role in manufacturing due to its exceptional material properties and process versatility.
Its key advantages—superior impact strength, heat resistance, chemical resistance, and excellent surface finish—make it ideal for diverse applications, ranging from automotive components to consumer goods.
Critical technical aspects, such as raw material drying, mold design, parameter optimization, and post-processing control, directly influence product quality and production efficiency.
For the manufacturing industry, ABS injection molding not only drives the development of high-performance products but also enhances production competitiveness through cost-effectiveness and processing ease.
If you’re ready to launch a new ABS injection molding project, contact FOWMOULD today! We offer tailored ABS molding solutions and provide free quotes in the shortest time possible!