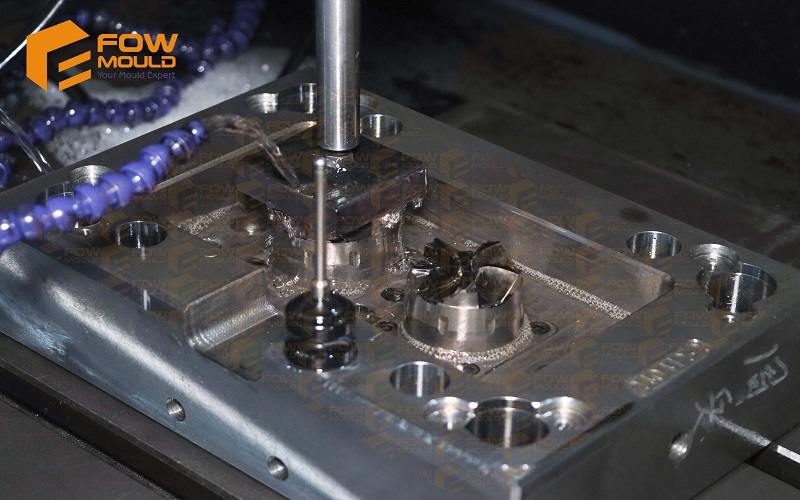
As a business, one of the most important aspects to consider is where you’ll be getting your products. This is especially true when it comes to different plastic products that you may require for your business operations. The production of these plastic products is usually outsourced to manufacturing companies to ensure that the products are of high quality.
These manufacturing companies will use different processes depending on the specific needs you want. Some of the most relied on processes include injection molding and extrusion molding. However, for most businesses, these terminologies may not mean much and it may be quite confusing to understand their differences.
This is why it is always best to work with a qualified molding manufacturer to ensure that you get the best services. With them, you’ll be in a better position to understand which production process works best for you. Getting to know the difference between injection molding and extrusion molding will help you better decide which process to work with.
Source: www.idc-online.com
Injection molding was started in the 19th century and was used as a simple manufacturing process for buttons, combs, and other simple plastic products. However, since then, this manufacturing process has greatly evolved and is more efficient.
Additionally, it features the manufacture of more complex plastic products. The injection molding process features the use of an injection molding machine that comes with different crucial parts. These parts come in handy when it comes to the manufacturing process. They include:
When it comes to the injection molding machine, the injection unit is a vital part that plays a crucial function. The injection unit is a syringe-like part that is used to introduce molten material into the mold cavity. Using this injection unit makes the process easier and allows for faster manufacturing processes.
One of the best ways to ensure that your manufacturing process goes well is to ensure that the molds are secure. This is where the clamping unit comes in. It features a hydraulic lift that allows it to move in and out facilitating the opening and closing of the mold cavity.
The mold cavity varies depending on the specific product to be manufactured. It is an essential part seeing as without it the manufacturing process would not result in quality products.
With the different parts in the injection molding machine, you find that the process itself features a few cycles you should keep in mind. They include.
Source: www.creativemechanisms.com
The first place to start for any serious manufacturer is at the product design stage. This is where the groundwork is laid and foundations are set up. As the customer, you’ll need to work closely with your manufacturer and designers. This is the part you need to ensure that you are actively participating to ensure that your product design turns out as it should. With the right collaborations, you’ll easily achieve the right product designs.
After the product design is complete, it is then up to the designer to work on the mold design. The design needs to depict the product design worked on earlier to ensure that the results are as required. Mold design is essential to avoid making irreversible mistakes.
With the mold design, the mold-making process then commences giving the injection molding a structure and base. Without the mold, the process would not be of any use to businesses in need of plastic products. The mold-making process will feature the use of engineering expertise to ensure that the design is translated to its physical equivalent. This is an important step when it comes to this manufacturing process.
After the mold is done, it is then attached to the injection molding machine and secured firmly with the use of the clamping unit. The injection molding unit then introduces molten material into the mold. To make this process easier the injection unit is designed to dispense just the right amount of molten material. It does this by dwelling on the mold to absorb any excess molten material. Once the molten material is in the mold, it is allowed to cool taking the form of the mold that is being used. Once the product is formed, the clamping unit releases, and the mold opens releasing and ejecting the end product.
The injection molding process is a great manufacturing option for you to consider. It features great advantages that you should consider getting onto. These advantages include:
Source: medium.com
Low labor cost
Injection molding is an extension of automation in the manufacturing industry. Most of the process takes place and is run by the machine itself. Having one employee to keep an eye on the processes will suffice. This helps reduce the cost of labor and investing in more employees.
Design flexibility
When it comes to injection molding, you have unlimited design options to work with. All you need to to ensure that your mold design features the exact design you want. This gives you great flexibility to come up with amazing designs.
Enhanced strength
When working with injection molding, it is possible to add fillers during the process. These fillers come in handy to enhance the strength of your plastic products.
Like any other manufacturing process, injection molding also features a few disadvantages that you should consider. They include:
Source: www.3erp.com
High tooling cost
When starting your first batch of manufactured plastic products, the price will be higher given that you’ll have to cater for a mold. However, once that is done you can use the same molds for subsequent productions unless you plan on changing the design.
Higher costs incurred in smaller productions
Injection molding is a great option for those looking to manufacture plastic products in bulk. This makes smaller productions more expensive to work with.
Source: confocal-manawatu.pbworks.com
The extrusion molding process is mainly used when it comes to the manufacture of 2d shapes. It is a great plastic manufacturing process to consider. It features the use of a 2d die where the molten plastic material is passed through. In the die, the molten plastic material is allowed to cool forming a solid shape. The shape formed by the cooled plastic material is dependent on the shape of the 2d die being used.
As with the other molding machines, the temperature to be used here will be normal. The heater keeps heating the plastic until the plastic extruder successfully inserts the wire into it. Colorants and UV inhibitors, in liquid or pellet form, are commonly used and can be inserted into the resin until it enters the hopper. The material comes into contact with the screw on reaching the feed throat near the rear of the barrel. The plastic resin is forced forward into the barrel by the spinning screw, which is heated to the ideal melt temperature for the resin.
Some of the advantages that come with using the extrusion molding method include:
Source: plastrading.com
Source: techminy.com
The extrusion molding process also comes with a few downsides that you should keep in mind. Some of the disadvantages associated with this manufacturing process include:
Source: www.teamrapidtooling.com
When it comes to the differences between the injection molding process and the extrusion molding process, there is not a lot to consider. They include:
Injection molding features the need for an intricate product design while the extrusion molding process does not feature such designs
The extrusion molding process is used for 2-dimensional shapes while injection molding is more complex catering to the 3-dimensional shapes.
Injection molding and extrusion molding are great ways to manufacture different plastic products. Take your time to consider working with a qualified mold manufacturer who will ensure that you invest in the right processes. Pay attention to the processes to ensure you get the basics of what it all entails.
Please contact us using the form below or emailing (harry@fowmould.com)