Molded foam is a type of polyurethane foam produced through specific molding processes, occupying a significant position in manufacturing due to its high precision and diverse performance capabilities. With decades of experience in the foam injection molding industry, we have honed our expertise to deliver reliable and innovative solutions.
Compared to traditional foam, molded foam can precisely shape complex forms, providing consistent density and structure, making it a crucial material for meeting modern production demands.
Its unique production process—injecting raw materials into molds and then expanding and solidifying—differs from traditional pouring or spraying methods, not only enhancing product consistency but also expanding design possibilities.
This article aims to explore how molded foam, through its technical advantages and application flexibility, drives the continuous development of the manufacturing industry in terms of efficiency, innovation, and lightweight design.
What Is Molded Foam?
Molded foam is a type of foam created through a specialized molding process where liquid foam material is poured into a mold, allowed to expand, and then harden. This method enables the production of complex shapes and intricate designs that are challenging to achieve with other types of foam.
Molded foam can be made from a variety of materials, including polyurethane and expanded polystyrene (EPS), each offering unique properties suited to different applications.
The versatility of molded foam makes it a popular choice in a wide range of industries. In packaging, it provides maximum protection for delicate items during shipping. In product design, it allows for the creation of ergonomic and aesthetically pleasing components.
The manufacturing process itself is highly adaptable, accommodating a variety of designs and specifications, which is why molded foam is commonly used in automotive, medical, electronics, and aerospace applications.
This ability to expand and conform to specific shapes and sizes underscores the material’s broad utility and importance in modern manufacturing.
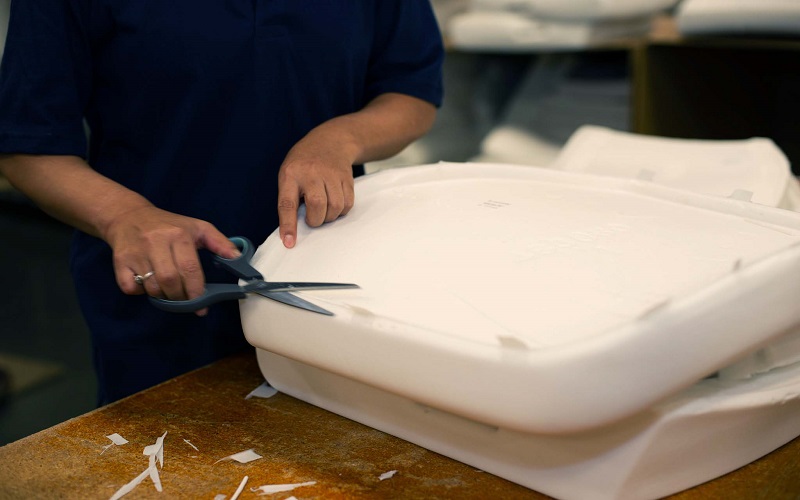
Benefits Of Molded Foam
Molded foam offers numerous benefits over other types of foam, making it a preferred material in many industries. One of its primary advantages is its durability.
Molded foam is highly resistant to compression and deformation, ensuring that it maintains its shape and provides consistent performance over time. This makes it ideal for applications where maximum protection is required, such as in packaging and automotive seating.
Another significant benefit is its customizability. Molded foam can be designed and manufactured to meet specific requirements, allowing for tailored solutions that address unique challenges.
Whether it’s creating ergonomic seating for vehicles or protective casings for medical devices, the ability to customize molded foam ensures that it meets the precise needs of each application.
Additionally, molded foam is often lighter in weight compared to other foam types. This lightweight nature is particularly advantageous in industries like aerospace and automotive, where reducing weight can lead to improved fuel efficiency and performance.
The combination of durability, customizability, and lightweight properties makes molded foam an ideal material for a wide range of applications.

Properties of Molded Foam Products
Molded foam is distinguished in manufacturing by its unique production process and material properties. Here, we provide an overview of its core characteristics and how it maintains the function and aesthetics of the client’s concept.
Customers can expect high reliability and quality from our molded foam products, ensuring satisfaction with the end results.
High-Precision Molding Capability
Molded foam can accurately replicate complex geometrical shapes and intricate designs through its molding process. The use of molds ensures high dimensional consistency and surface quality, meeting the precision demands of applications such as automotive interior components or custom packaging pads.
This precision makes molded foam an advantageous material for manufacturing scenarios that require detailed structures and seamless integration.
Adjustable Density and Hardness
The density and hardness of molded foam can be flexibly controlled by adjusting the raw material ratios and foaming conditions. This flexibility enables a wide spectrum of performance, from low-density (around 10 kg/m³) soft foams to high-density (over 100 kg/m³) rigid materials.
Soft molded foam is perfect for comfort in seating, whereas rigid versions are apt for structural components requiring support, showcasing its diverse adaptability.
Lightweight and Durable
Molded foam is renowned for its lightweight nature while maintaining excellent durability. Its porous structure renders it much lighter than traditional solid materials while retaining adequate strength and impact resistance.
It also boasts strong resistance to water, oil, and chemical corrosion, ensuring long-term durability in various environments. This makes it particularly suitable for lightweight designs and applications requiring high durability.
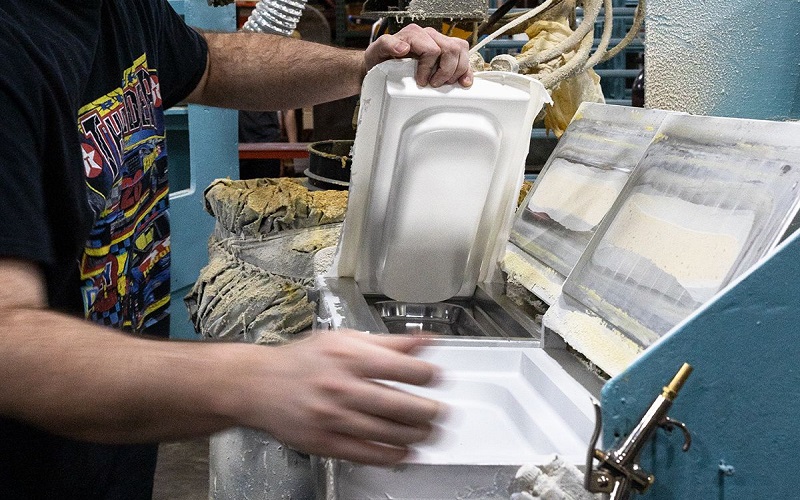
Applications Of Molded Foam Products
Molded foam is used across a variety of industries, leveraging its unique properties to meet specific production and product demands. Our commitment to improving customer experiences ensures that our solutions address specific needs, such as noise reduction and patient comfort in medical equipment.
We support clients through the entire development process of custom foam products, managing various project needs from initial design to manufacturing. Whether for consumer goods or specialized OEM parts, our expertise allows us to handle both small-scale and extensive production requirements.
Automotive Applications
In automotive manufacturing, molded foam is indispensable for creating interior components that balance comfort, safety, and efficiency. Flexible molded foam is employed in seats, headrests, and armrests, delivering ergonomic support and resilience tailored to driver and passenger needs.
Semi-rigid and rigid variants shape dashboards, door panels, and roof liners, aiding in noise, vibration, and harshness (NVH) reduction while maintaining low vehicle weight—a crucial factor in fuel efficiency and electric vehicle design, as specified by original equipment manufacturers.
Molded polyurethane foam seats, for example, are engineered to precise specifications, ensuring durability and comfort over thousands of miles.
Medical Devices
In healthcare manufacturing, molded foam plays a critical role where precision and biocompatibility are paramount.
Flexible polyurethane foam is used in orthopedic supports, such as wheelchair cushions and prosthetic liners, providing pressure relief and comfort for patients. Rigid molded foam serves as protective casing or packaging for equipment like diagnostic tools and surgical instruments, ensuring sterility and safety during transport.
Its adaptability allows manufacturers to create ready product design ergonomic designs that improve usability and patient outcomes, providing a significant advantage.
Electronics and Packaging
The electronics industry relies heavily on molded foam for protective packaging and component support.
Custom-molded foam inserts safeguard delicate devices like circuit boards, smartphones, and precision instruments during shipping and storage, offering superior shock absorption and vibration dampening. Its ability to be shaped into intricate contours ensures a snug fit, minimizing movement and damage.
Molded foam with antistatic properties also protect sensitive electronic components from electrostatic discharge in manufacturing environments, enhancing product reliability.
Aerospace
In aerospace manufacturing, molded foam excels in weight reduction without compromising strength. Rigid molded foam is integrated into structural components like interior panels and insulation layers, reducing aircraft weight while maintaining thermal and acoustic performance.
Durability under extreme conditions, such as temperature fluctuations and vibrations, makes it ideal for cabin interiors and cargo holds. Molded foam panels, for instance, help optimize fuel efficiency in commercial jets while meeting stringent safety standards.
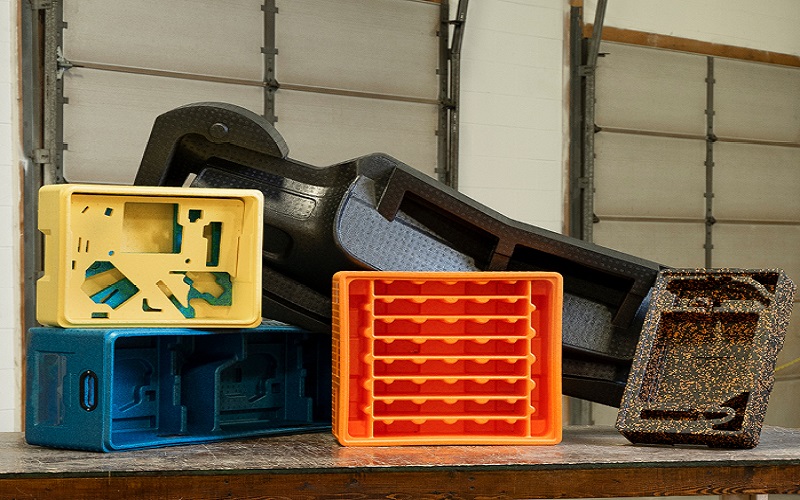
How To Create Custom Molded Foam Parts
Creating custom molded foam parts involves several critical steps, each designed to ensure that the final product meets specific requirements and performs as intended. The process begins with the design phase, where the part’s specifications and applications are carefully considered. Designers use advanced software to create detailed models, taking into account factors such as shape, size, density, and material properties.
Once the design is complete, the next step is prototyping. A prototype is created to test the design and verify that it meets the required specifications. This stage is crucial for identifying any potential issues and making necessary adjustments before full-scale production begins. Prototyping often involves creating a small batch of parts using the same materials and processes that will be used in the final production run.
After the prototype has been tested and approved, the manufacturing process begins. Custom molded foam parts are produced by pouring liquid foam material into a mold, where it expands and hardens into the desired shape. This molding process ensures high precision and consistency, allowing for the creation of complex and intricate designs.
Throughout the manufacturing process, strict quality control measures are implemented to ensure that each custom part meets the highest standards of performance and durability.
This includes testing for dimensions, appearance, and physical properties to ensure that the final product meets all required specifications. By following these steps, manufacturers can create custom molded foam parts that are tailored to specific applications and deliver reliable performance.
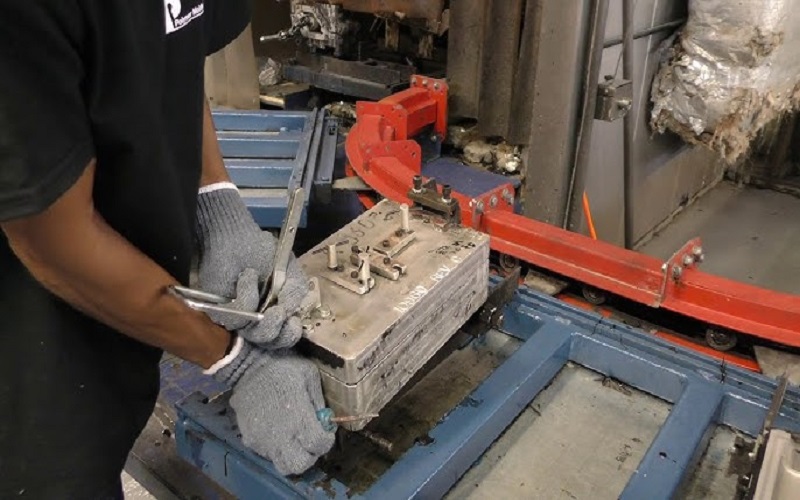
Custom Molding Services Of Molded Foam Parts
Custom molding services for molded foam parts provide consumers with high-precision, tailored solutions, utilizing materials like polyurethane foam to produce components that meet specific requirements. As a leader in the foam injection molding industry, we leverage our expertise, innovative capabilities, and extensive experience to deliver exceptional results.
Injection molding manufacturers leverage advanced mold design and foam injection molding technologies to production foam parts with precise shapes and optimized performance, widely applied in industries such as automotive, electronics, healthcare, and consumer goods. Our ability to fabricate and machine custom molded foam parts using advanced technology ensures that we meet diverse client specifications and maintain high-quality standards in the finished products.
By flexibly adjusting foam density (from soft 10 kg/m³ to rigid over 100 kg/m³) and hardness, these services cater to diverse needs, from soft cushioning to robust support. Additionally, the services emphasize quality control, with rigorous testing to verify part durability and performance, ensuring a low defect rate.
Their cross-industry adaptability enables custom molding services to swiftly respond to demands ranging from prototype development to large-scale production, while optimizing material use, reducing waste, and enhancing cost-efficiency.
Therefore, selecting a manufacturing team that combines technical expertise and industry experience is crucial. An exceptional team should not only possess state-of-the-art equipment and innovative mold design capabilities but also deeply understand client needs, offering end-to-end support from concept to finished product.
They should be adept at meeting diverse industry standards—such as lightweight requirements in automotive or biocompatibility in healthcare—while prioritizing sustainable practices, like using bio-based foams or optimizing recycling processes.
Partnering with such a team ensures that molded foam parts achieve an optimal balance of performance, efficiency, and environmental responsibility, driving lasting value for product development and market competitiveness.
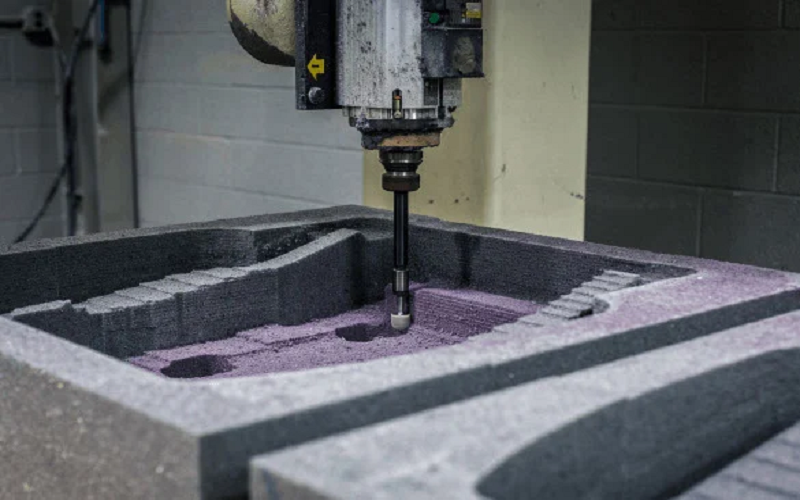
Summary
Molded foam has revolutionized various industries by providing versatile, precise, and durable solutions. Its ability to be customized for specific applications, whether in automotive, medical, electronics, or aerospace industries, showcases its immense potential.
Thinking inside the box can help address complex challenges such as noise, vibration, and thermal issues effectively while enhancing overall product design.The high precision, adjustable density, lightweight, and durability of molded foam make it a superior choice for modern manufacturing needs.
As we look to the future, the continued innovation in molded foam technology will undoubtedly drive further advancements in manufacturing. Embracing this material’s capabilities will pave the way for more efficient, sustainable, and high-performance products, solidifying molded foam’s role as a cornerstone of industrial innovation.