When shopping for a phone case, we often notice in the product details that its material is listed as TPU. However, for many people, what TPU actually is—along with its properties and range of applications—remains a mystery.
Join us as we unveil the secrets of TPU material, guiding you to a deeper understanding of this remarkable material and effortlessly transforming you into a TPU expert!
What Is Thermoplastic Polyurethane (TPU)?
Thermoplastic Polyurethane (TPU) is a unique blend of rubber and plastic, known for its high elasticity, strength, and excellent processing capabilities.
The three basic raw materials required to produce a TPU are: A polyol or long-chain diol A chain extender or short-chain diol A diisocyanate It is a linear segmented block copolymer composed of soft and hard segments.
When a polyaddition reaction occurs between a diisocyanate and one or more diols in a specific way, it produces TPU.
The molecular structure allows TPU to behave like both an elastomer and a thermoplastic elastomer, depending on the conditions .
By varying the ratio, structure, and molecular weight of the reaction compounds, an enormous variety of different TPU can be produced.
A standout feature of TPU is its reversible cross-linking through intermolecular hydrogen bonds. These bonds weaken when heated or dissolved, making the material moldable. Upon cooling or solvent evaporation, the bonds re-form, restoring the material’s original properties.
This unique characteristic makes TPU an ideal candidate for various applications, ranging from defense to food industries.
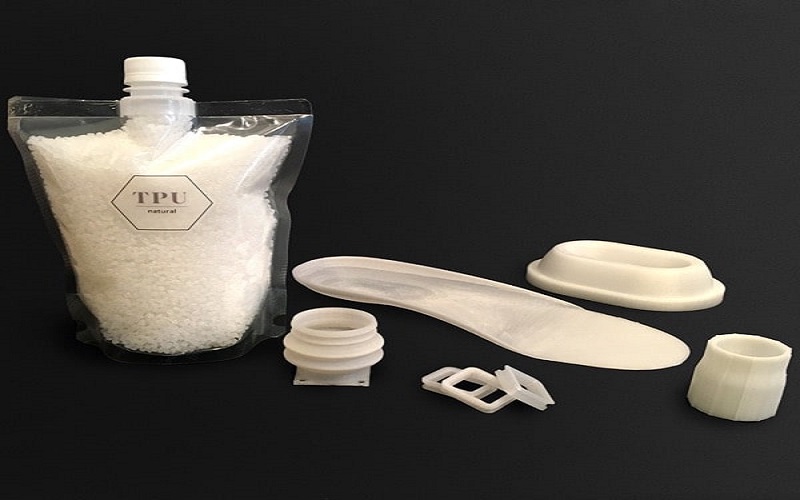
Key Properties of TPU
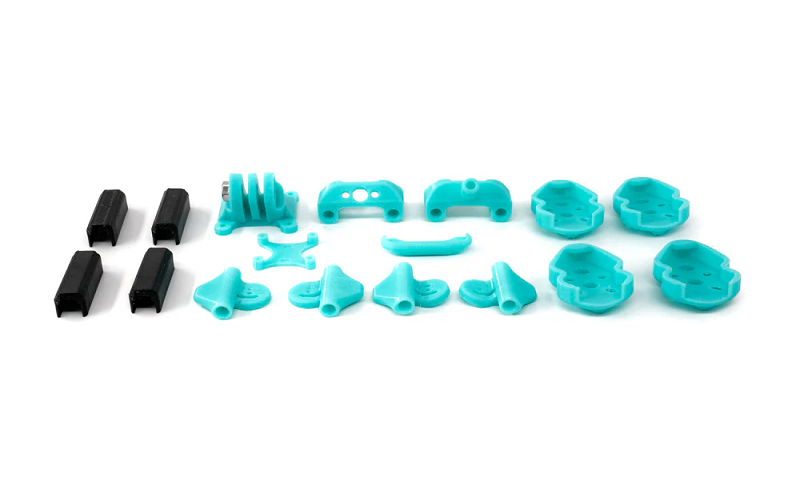
As we all know, abrasion resistance, tear resistance, flexural strength are excellent; high tensile strength, large elongation, long-term compression permanent deformation rate is low, etc. are the significant advantages of TPU.
Abrasion resistance
TPU is renowned for its exceptional abrasion resistance, outperforming natural rubber by more than fivefold.
This makes it the abrasion resistant material of choice for applications where durability and wear resistance are critical, such as in shoe soles and industrial parts, especially when using TPU powders.
Chemical resistance
TPU resists oils, greases, and many solvents, maintaining its integrity in harsh environments. This property is valuable in automotive and industrial uses.
Low-Temperature Flexibility
TPU remains flexible and functional down to -50°C, enabling it to replace PVC in cold environments where PVC becomes brittle.
TPU’s resilience in extreme cold makes it suitable for applications in arctic and cold weather gear, ensuring performance where other materials fail.
Elasticity And Toughness
The elasticity and toughness of TPU are unmatched, with a hardness range from Shore A 60 to Shore D 80, maintaining high elasticity across this spectrum. TPU boasts a tensile strength of up to 70 MPa and an elongation at break of up to 1000%.
Hydrolysis resistance
TPU offers excellent hydrolysis resistance, particularly in the polyether-based variants, which remain stable for 1 to 2 years without significant degradation. Polyester-based TPUs, however, can decompose under prolonged exposure to water, especially at higher temperatures.
Polyether-based TPUs are more suitable for applications involving regular water contact.
Biomedical Properties
TPU’s outstanding biocompatibility makes it ideal for medical applications. It is non-toxic, non-allergenic, non-irritating, and free of pyrogens. These properties enable TPU to be used in medical devices, protective gear, and hygiene products, ensuring safety and comfort for users.
TPU Properties Table | |
---|---|
Properties | Value |
Density(g/cm³) | 1.10–1.25 |
Melting Point(°C) | 150–230 |
Tensile Strength(MPa) | 20–50 |
Elongation at Break(%) | 300–800 |
Glass Transition Temperature(°C) | -40~-20 |
Shrinkage Rate(%) | 0.35-0.83 |
Types of TPU
TPU is primarily categorized into two types based on the structure of the soft segments: polyester-based and polyether-based. Each type offers distinct advantages and is suited for different applications.
These types will be explored in the following subsections.
Polyester-Based TPU
Polyester-based TPU’s remarkable mechanical properties and superior abrasion resistance make it ideal for demanding applications in the automotive and consumer goods industries.
However, these grades may hydrolyze and are less cost-effective than alternatives.
Polyether-Based TPU
Polyether-based TPU’s high resistance to hydrolysis makes it suitable for moisture-prone environments. It also maintains flexibility at low temperatures, enhancing usability in colder climates.
Common applications include medical devices, automotive parts, and underwater products.
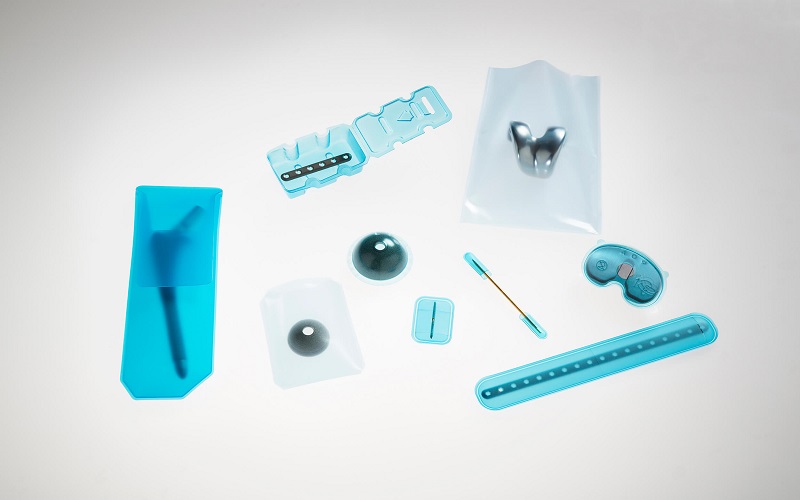
How TPU Plastic is Processed?
TPU can be processed using standard thermoplastic techniques and equipment, making it versatile for various manufacturing methods. The primary techniques to shape TPU into useful products include injection molding, extrusion, calendering, and blow molding.
Injection Molding
Injection molding, one of the most common methods for processing TPU, involves melting TPU pellets at high temperatures and injecting them into a mold at the mold temperature to cool and solidify into the desired shape through tpu injection molding.
Below is an example of injection molding parameters for a soft TPU (Shore A 85):
Drying temperature & time: 100°C, 3 hours
Cylinder temperature: 170°C (feed) – 190°C (nozzle)
Mold temperature: 25°C
Injection pressure: 80 MPa
Holding pressure: 40 MPa
Cooling time: 15 seconds
For hard TPU (Shore D 50), the temperature and pressure will be increased appropriately, e.g. barrel temperature to 200-220°C and mold temperature to 40-50°C.
Extrusion Molding
Extrusion molding forces heated and plasticized TPU pellets through a die to form thin films with smooth surfaces and stable physical properties, suitable for packaging, footwear, and automotive interiors.
Compression Molding
Calendering passes heated TPU pellets through rotating rollers to produce thin films, ensuring uniformity and smoothness for high-quality applications like clothing fabrics and waterproof materials.
Blow molding
Blow molding produces tubular TPU products by extruding molten TPU into a tube and expanding it with compressed air to form a film. This technique creates large, durable products like packaging materials, tents, and inflatable toys requiring toughness and impact resistance.
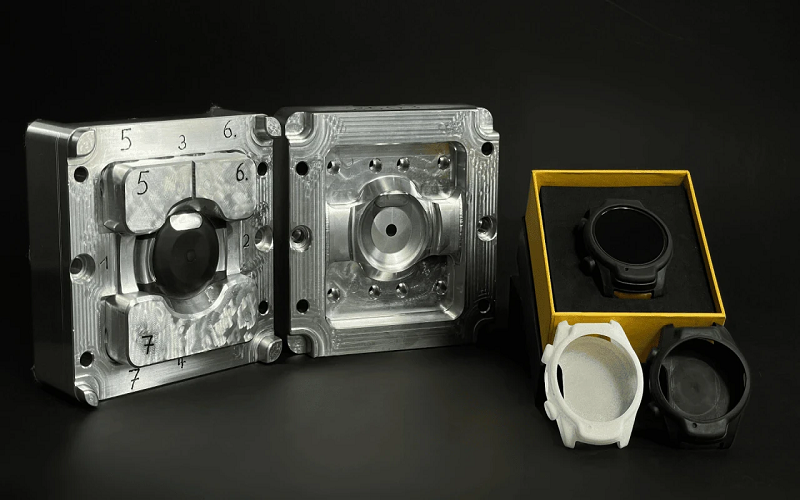
Applications of TPU Material
TPU’s versatility extends across many industries, from footwear to medical devices, showcasing its adaptability and performance in various fields.
Footwear
In footwear, TPU is used for shoe soles, midsoles, and uppers due to its flexibility, abrasion resistance, and cushioning properties, providing comfort and durability for athletic and casual shoes.
Consumer Electronic
TPU is well known for its applications in wire and cable jacketing, hose and tube, in adhesive and textile coating applications, and as an impact modifier of other polymers.
TPU is also a popular material found in flexible outer cases of devices like mobile phones and keyboard protectors.
Sporting Goods
In sporting goods, TPU is used in protective gear, inflatable products like rafts, and performance apparel. Its elasticity and resilience make it ideal for products requiring flexibility and impact resistance, such as ski boots and sports equipment.
Medical Devices
TPU’s biocompatibility, flexibility, and sterilizability make it suitable for medical applications like tubing, catheters, wound dressings, and wearable medical devices.
Industrial Applications
TPU is used in conveyor belts, hoses, seals, and gaskets due to its resistance to abrasion, chemicals, and harsh environments. It’s also employed in wire and cable sheathing for its toughness and flexibility.
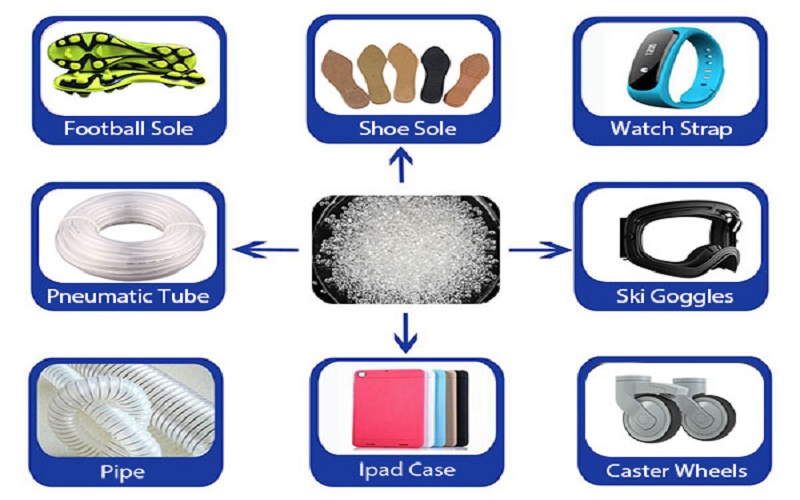
Is TPU Material Safe?
When addressing the question “Is TPU safe?”, Thermoplastic Polyurethane (TPU) is generally regarded as safe for most applications, though its safety hinges on specific use cases, production methods, and adherence to regulatory standards.
Medical-grade TPUs, designed for biocompatibility, undergo rigorous testing (e.g., ISO 10993) to ensure they are safe for prolonged human contact, making them ideal for devices like catheters and implants. In consumer products such as phone cases and footwear, TPU’s safety is enhanced by its absence of harmful plasticizers like phthalates, unlike PVC, posing minimal risk during normal use.
However, during high-temperature processing (e.g.,TPU injection molding), proper ventilation is essential to mitigate potential VOC emissions, which could otherwise affect air quality or worker health if uncontrolled.
Ultimately, the answer to “Is TPU safe?” depends on its intended application and certification—when produced and used correctly, TPU offers a reliable, safe material choice across diverse industries.
Key Differences Between TPE And TPU
When comparing TPE vs TPU, the differences lie in their composition, properties, and applications.
TPE, a broad family of thermoplastic elastomers like styrene-based copolymers (e.g., SBS, SEBS), offers softness, elasticity, and cost-effectiveness, making it ideal for soft grips, toys, and budget-friendly products, though it has moderate strength and chemical resistance.
In contrast, TPU, a specific type of TPE made from polyurethane with a block copolymer structure, boasts superior tensile strength, excellent abrasion and chemical resistance, and a wider hardness range (Shore A 60 to Shore D 50), suiting it for durable applications like phone cases, footwear soles, and medical tubing—albeit at a higher cost and with stricter processing needs.
Ultimately, in the TPE vs TPU debate, TPE excels in flexibility and affordability, while TPU stands out for toughness and performance in demanding conditions.
Understanding the differences between tpe and tpu will help you select the right material to fit specific applications.
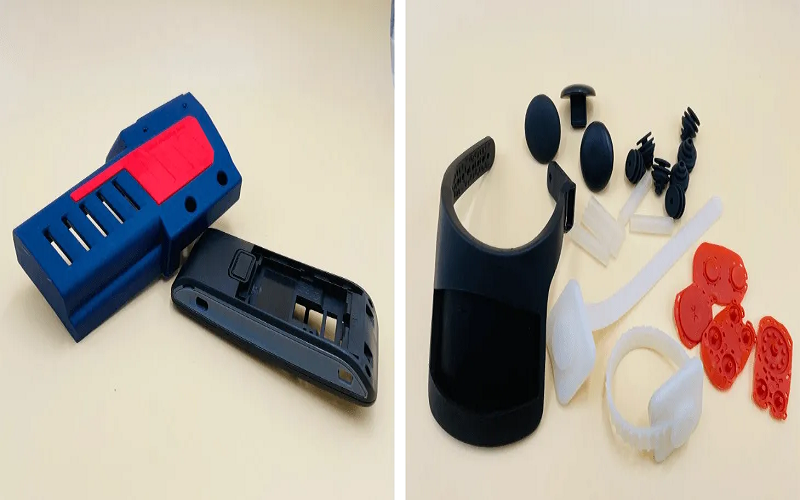
Summary
In summary, while both TPU and silicone offer unique advantages, their distinct properties cater to different applications and requirements.
Its unique properties, such as abrasion resistance, low-temperature performance, and biocompatibility, make it a valuable choice for applications ranging from footwear to medical devices.
While TPU offers environmental benefits like recyclability, its overall sustainability is limited by energy-intensive processing. Nevertheless, with proper use and certification, TPU proves to be a safe and effective material for many applications.