As an efficient and precise manufacturing technique, injection molding is widely used for producing various plastic products. The choice of injection molding materials directly determines the product’s performance, cost, and application range.
Common injection molding materials are mostly thermoplastics due to their ability to melt when heated and solidify when cooled, making them highly suitable for the demands of the injection molding process. Some injection moldable plastics also offer excellent corrosion resistance, making them suitable for harsh environments.
These materials each have their own advantages, capable of meeting diverse requirements from everyday consumer products to high-performance industrial components.
Below, we introduce several common injection moldable plastics and their characteristics to help understand their important role in the injection molding industry.
What Are Injection Molded Plastics?
Injection molded plastics are a category of thermoplastics that can be melted, reshaped, and solidified multiple times without significant degradation. This characteristic makes them highly versatile for various manufacturing applications, from automotive parts to consumer goods.
The injection molding process itself involves melting the plastic, injecting it into a mold under high pressure, and allowing it to cool and solidify into the desired shape.
One of the key advantages of injection moldable plastics is their efficiency in mass production.
These plastics can be produced in large quantities with minimal waste, making them an ideal choice for industries that require high volumes of precise, complex parts.
Their ability to maintain their properties through multiple heating and cooling cycles further enhances their versatility and utility in manufacturing.
Additionally, some injection molded plastics have a large operating temperature range, making them suitable for both high and low-temperature applications.
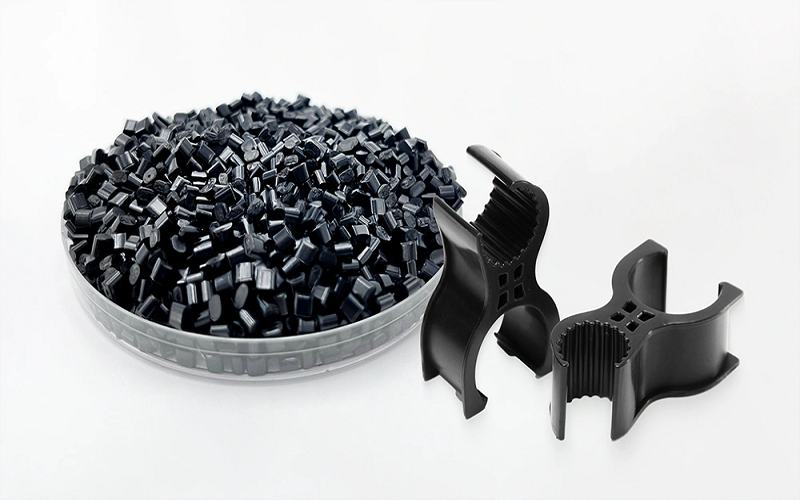
Key Properties of Injection Molding Materials
The key to the widespread use of injection moldable plastics lies in their unique properties. Plastic’s heat resistance is paramount, as these plastics must withstand the heating and cooling cycles of the injection molding process without breaking down.
This attribute ensures that they can be used repeatedly to produce consistent, high-quality parts. Additionally, their mechanical properties, such as tensile strength, stiffness, and flexibility, are crucial for meeting specific application requirements.
Injection moldable plastics also boast exceptional dimensional stability, allowing them to maintain their shape and size even under varying temperatures and loads. This is particularly important for applications that demand precise and reliable components.
Moreover, their thermoplastic nature means they can be melted and reshaped multiple times without significant degradation, making them highly adaptable for various manufacturing needs.
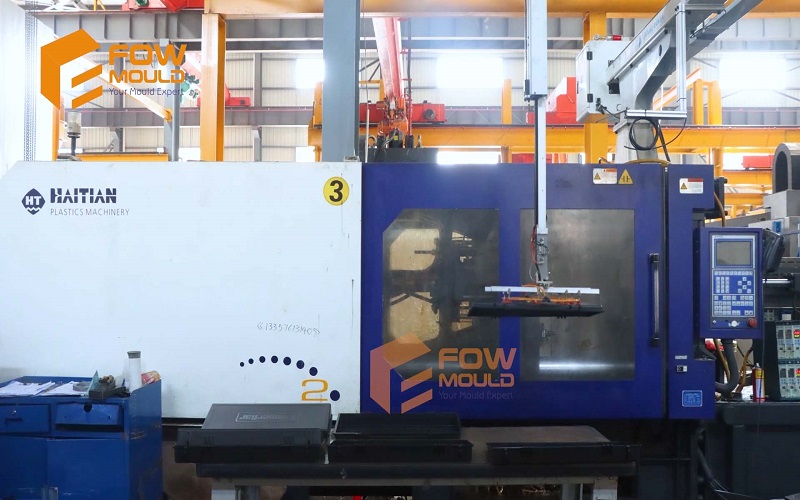
Common Materials For Plastic Injection Molding
The base materials used for plastic injection molding generally are referred to as thermoplastic polymers.
Below, we explore some of the most common 5 heat resistant plastics employed in injection molding, highlighting their unique properties and applications.
Polyethylene (PE)
Polyethylene (PE) is a low-cost plastic known for its versatility and ease of processing, which allows for efficient manufacturing.
It exhibits excellent chemical resistance, making it suitable for various environments. PE’s flexibility and toughness contribute to its wide range of utilizations, including packaging, containers, and household items due to its durability.
PE is categorized into different densities, such as high-density and low-density, which influence its hardness and flexibility.

Polypropylene (PP)
Polypropylene (PP) is known for its high melting point, which allows it to maintain structural integrity under elevated temperatures.
It exhibits good chemical resistance, making it suitable for applications that involve exposure to various chemicals.
PP’s flexibility enhances its usability in various applications, including packaging and automotive parts. The combination of high melting point, chemical resistance, and flexibility makes PP ideal for use in automotive parts and consumer goods.
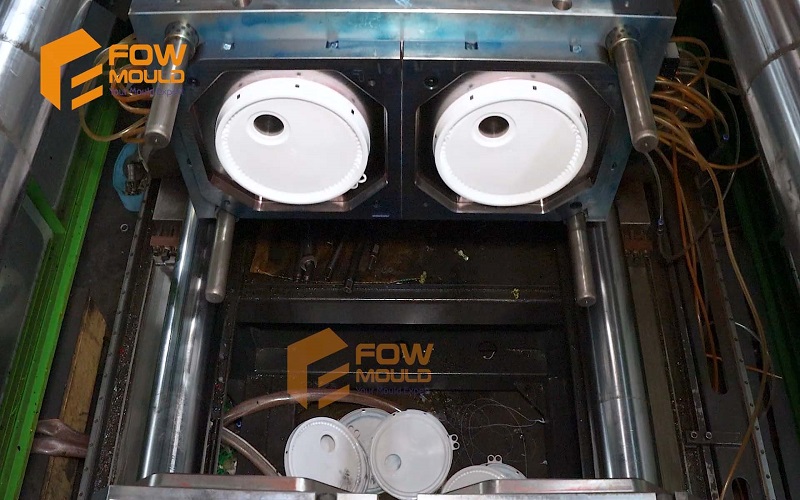
Acrylonitrile Butadiene Styrene (ABS)
Acrylonitrile Butadiene Styrene (ABS) is an engineering-grade thermoplastic known for its strength and impact resistance.
ABS is tough, relatively inexpensive, and exhibits good resistance to heat, oil, acids, and alkalis.
Its styrene content provides a glossy, attractive finish to molded parts, while its butadiene content ensures excellent toughness even at low temperatures.
ABS is widely used in electronic components, keyboard keys, automotive parts, and consumer goods.
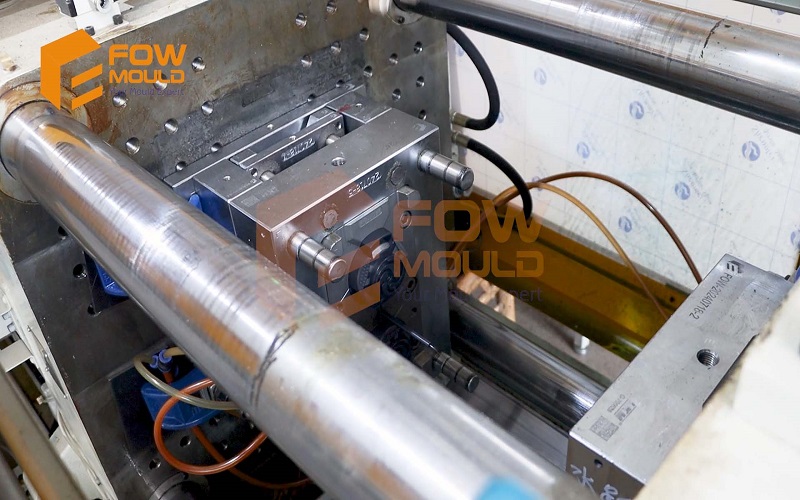
Polycarbonate (PC)
Polycarbonate (PC) is a high-performance thermoplastic known for its durability and versatility in various applications.
It offers high impact resistance, allowing it to withstand significant force without cracking or breaking. PC also possesses excellent optical clarity, making it suitable for applications where transparency is essential.
Common uses of PC include safety equipment such as helmets and goggles and electronic components like light covers and housings.
Nylon (Polyamide)
Nylon, or polyamide, exhibits heat resistance, allowing it to withstand high temperatures while maintaining structural integrity. With a typical melting point around 220°C (428°F), it provides excellent thermal stability.
Nylon’s tensile strength makes it suitable for applications where durability and resistance are essential, such as automotive components and industrial uses. While nylon can endure higher temperatures for short-term exposure, exceeding the maximum temperature for extended periods can result in degradation.
Nylon’s advantages over metals include comparable strength at a fraction of the weight, making it a cost-effective alternative.
Factors to Consider When Choosing Injection Moldable Plastics
Choosing the right injection moldable plastic is crucial as it directly impacts the performance, cost, and manufacturability of the final product.
Several key factors must be evaluated to ensure the chosen material aligns with the project’s requirements.
Selecting the best heat resistant material involves considering factors beyond just the melting point, such as environmental conditions and specific application requirements.
These factors include thermal properties, chemical and environmental resistance, mechanical properties, and specific application needs.
Thermal Properties
Thermal properties are critical in determining a plastic’s suitability for high-temperature applications. Key parameters like heat deflection temperature, continuous service temperatures, and glass transition temperature help assess a plastic’s heat resistance. For instance, the continuous-use temperature that defines heat-resistant plastics is above 150°C (302°F).
Heat stabilizers and additives can further enhance plastic’s heat resistance.
Chemical, Environmental, and Heat Resistance
Chemical and environmental resistance are vital considerations. Parts exposed to solvents or oils need resistant plastics like PP, while ABS might degrade under similar conditions.
UV stability is essential for outdoor applications to prevent degradation, and moisture resistance is crucial for environments where water exposure is a concern.
Mechanical Properties
Mechanical properties such as tensile strength, flexibility, and wear resistance determine a plastic’s suitability for various applications. For instance, nylon’s flexibility increases when exposed to heat, making it more pliable.
Reinforcing agents can significantly enhance the mechanical properties of plastics, ensuring they meet the demands of high-stress or impact applications.
Application Requirements
Specific application requirements, such as electrical insulation, weight, and flame retardancy, play a crucial role in material selection. High-temperature polymers like PPS and PEI are used in electrical applications to ensure reliability and performance in demanding environments.
Lightweight plastics like PE are ideal for portable products, while flame-retardant materials are critical for safety in certain applications.
Choosing an injection molding plastic involves balancing these factors against the specific demands of the part and production process.
Collaboration between designers, engineers, and material suppliers is often necessary to optimize performance while managing costs and constraints.
With advancements in polymer blends and sustainable options, the range of choices continues to expand, offering greater flexibility for modern injection molding applications.
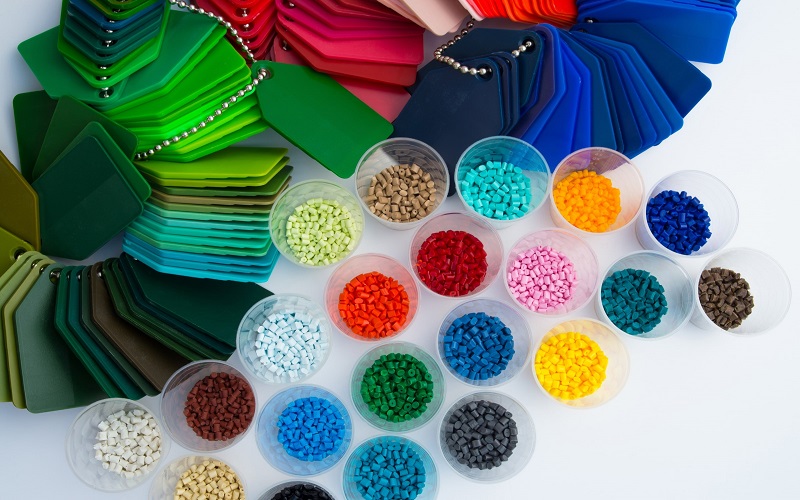
Enhancing Performance of Injection Moldable Plastics
Enhancing the performance of injection moldable plastics often involves incorporating additives and reinforcements. These enhancements can improve properties like thermal resistance, mechanical strength, and overall durability, making the plastics more suitable for specific applications.
High temperature plastics often require specific additives and reinforcements to enhance their thermal resistance and mechanical properties.
Additives
Additives play a significant role in enhancing plastic properties. Common additives include flame retardants, thermal stabilizers, and antioxidants, which improve the thermal behavior of heat-resistant plastics.
For instance, thermal stabilizers and antioxidants can enhance the heat resistance of nylon, making it more suitable for high-temperature applications.
Reinforcements
Reinforcing materials such as glass and carbon fibers are crucial for enhancing mechanical strength and thermal stability. Glass fibers improve thermal resistance, though they may reduce mechanical strength.
Carbon fibers, known for their superior mechanical properties, are preferred for high-performance applications due to their excellent strength-to-weight ratio.
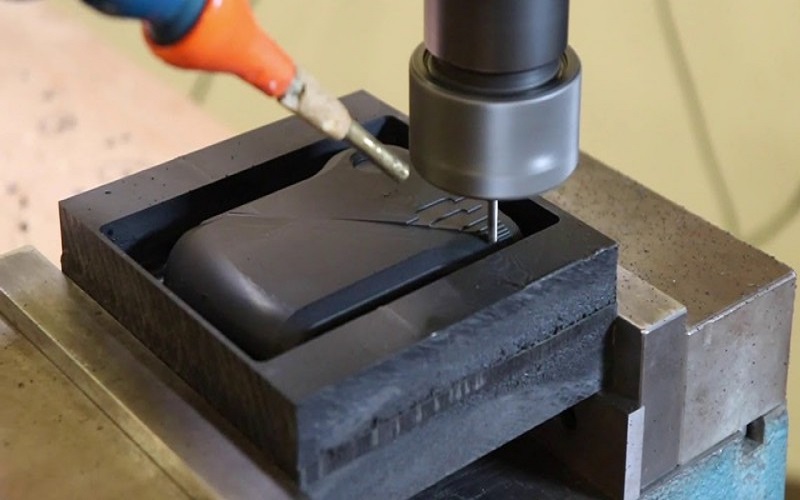
Applications of Plastic Materials For Injection Molding
Injection moldable plastics are used extensively across various industries due to their versatility and durability.
They are prevalent in the automotive, electronics, and consumer goods sectors, where their unique properties meet the demands of different applications.
Certain high-performance thermoplastics can withstand temperatures as high as 310°C for short durations, making them suitable for various demanding applications.
Automotive Industry
In the automotive industry, heat-resistant plastics like nylon are used for under-the-hood applications such as engine fan shrouds, intake manifolds, and valve covers. Nylon’s heat resistance and wear resistance make it suitable for these demanding environments.
Electronics
In electronics, injection moldable plastics are used for durable components like housings and connectors. Nylon, for instance, is used for wire and cable insulation as well as electrical connectors due to its excellent insulative properties.
Consumer Goods
Injection moldable plastics are also widely used in consumer goods, from kitchenware to toys. Nylon’s heat resistance allows it to be utilized in products such as ironing board covers, demonstrating its suitability for various consumer applications.
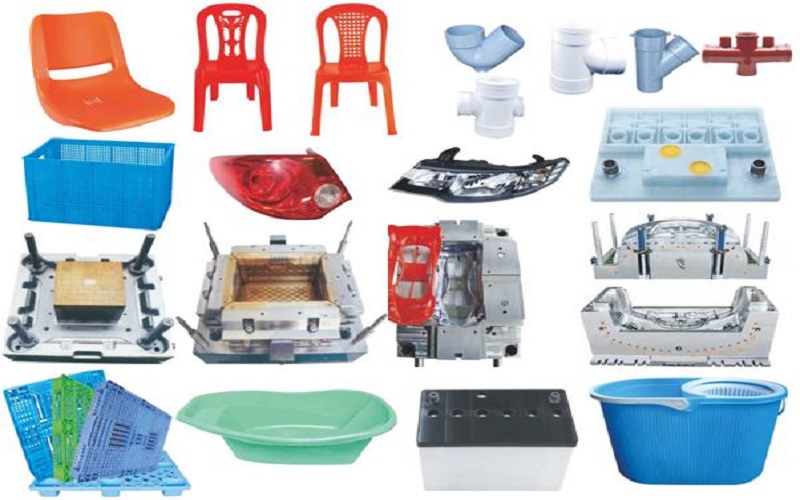
Advantages Of Using Injection Molded Plastic
Versatility
Injection moldable plastics are available in a diverse array of formulations, tailored to meet specific performance requirements such as rigidity for structural components, flexibility for soft-touch applications, or transparency for optical parts.
This adaptability makes them suitable for a wide range of industries, from automotive to consumer electronics.
Efficiency
These plastics enable fast processing times due to their optimized flow properties and rapid cooling characteristics, making them highly compatible with high-volume production.
This efficiency reduces cycle times and boosts throughput, offering manufacturers a cost-effective solution for large-scale operations.
Recyclability
Many thermoplastics, such as polyethylene and polypropylene, can be reground and reused without significant loss of properties, supporting sustainability efforts.
This recyclability not only minimizes waste but also aligns with the growing demand for circular economy practices, enhancing the environmental footprint of injection molding processes.
Future Trends of Plastic Molding Materials
The future of injection molded plastics is increasingly leaning toward sustainability, with a strong emphasis on biodegradable and bio-based plastics.
These innovative materials, derived from renewable sources like corn, sugarcane, or cellulose, offer the potential to significantly reduce the carbon footprint of injection-molded products. This shift aligns with the industry’s broader commitment to environmentally friendly solutions, driven by regulatory pressures and consumer demand for greener alternatives.
The focus on sustainability is also reshaping manufacturing processes, encouraging the adoption of energy-efficient techniques, waste-reducing designs, and closed-loop recycling systems to minimize environmental impact.
Looking ahead, advancements in material science—such as enhanced biodegradable polymers and high-performance bio-composites—promise to balance ecological benefits with the durability and versatility required for modern applications, paving the way for a more sustainable and responsible future in plastic molding.
Conclusion
Injection moldable plastics are the backbone of the injection molding industry, enabling the production of everything from everyday items to specialized components.
Their diversity and adaptability, combined with ongoing advancements in material science, ensure their continued relevance in modern manufacturing.
Selecting the right high performance plastics depends on the part’s requirements, balancing cost, performance, and processability.
Frequently Asked Questions
What are injection moldable plastics?
Injection moldable plastics are thermoplastics that can be repeatedly melted and reshaped, making them ideal for producing precise and complex plastic parts through the injection molding process. This versatility ensures their widespread application in various industries.
What are the key properties of injection moldable plastics?
Injection moldable plastics possess key properties such as thermal stability, mechanical strength, and versatility, which enable them to endure the heating and cooling cycles of the injection molding process and cater to diverse application needs.
Why are heat-resistant plastics important in manufacturing?
Heat-resistant plastics are crucial in manufacturing as they maintain structural integrity under high temperatures, making them ideal for demanding applications in the automotive and electronics industries. Their excellent thermal resistance ensures reliability and performance in challenging environments.
What are some common applications of injection moldable plastics?
Injection moldable plastics are widely utilized in automotive parts, electronic components, and consumer goods, encompassing items such as engine components, electrical connectors, kitchen utensils, and toys. Their versatility makes them essential in various industries.
What future trends are shaping the injection moldable plastics industry?
The injection moldable plastics industry is being shaped by a significant trend towards biodegradable and bio-based plastics, driven by a commitment to sustainability. This shift emphasizes the development of environmentally-friendly materials to reduce the industry’s environmental impact.