Low volume injection molding produces small quantities of plastic parts, making it ideal for testing products or creating custom components. In this guide, learn what low volume injection molding is, how it works, and its key benefits.
Key Takeaways
- Low volume injection molding is cost-effective and ideal for prototype testing and small batch production, reducing financial risks associated with large-scale manufacturing.
This process allows for design flexibility, enabling quick iterations and modifications with shorter lead times, which is essential for meeting evolving market demands.
Choosing the right materials and adhering to quality control standards are crucial for successful low volume injection molding, ensuring that final products meet performance requirements.
Understanding Low Volume Injection Molding
Low volume injection molding is a manufacturing process that typically produces between 100 to 10,000 pieces of low volume plastic.
This approach is particularly advantageous for industries that require flexibility and efficiency, such as aerospace, healthcare, defense, and consumer products. Manufacturers can test new products in the market without the financial risk associated with large-scale production using this method.
This process allows for rapid prototyping and small batch production, making it an ideal choice for businesses looking to innovate and respond quickly to market demands.
Many new product innovations may not succeed, and the cost of molds can be prohibitive. Therefore, producing small batches of injection molded parts to test the market can significantly reduce potential losses.
The Injection Molding Process
The journey of an injection molded part begins with resin pellets loaded into a barrel. These plastic pellets or granules are poured into a hopper before the process starts.
Once the resin pellets are loaded, machines melt, compress, and inject the plastic into the mold’s runner system. When sufficient material and pressure accumulate within the barrel, a ram activates. This action pushes the screw toward the injection mold, driving the plastic into the mold.
During this process, hot and cold runner systems guide the molten plastic, ensuring it flows smoothly into the plastic injection mold cavity surfaces.
The mold is held in place with clamping force during the plastic injection molding machine process, and components like the ejector system are installed into the mold.
The molten plastic then cools and solidifies to form the final part. The mold opens when the thermoplastic has cured and become solid. Then, ejector pins push the item out.
For low volume injection molding, cost-saving measures such as using relatively inexpensive mold steel and ordinary hot runner brands are often employed. This approach helps reduce tooling costs and makes the process more accessible for smaller production runs.
Why Choose Low Volume Production?
Low volume injection molding is an excellent choice for prototyping mature part designs and small batch production. It bridges the gap between prototyping and mass production, allowing for quick adjustments and iterations without the need for large-scale production commitments.
This approach is particularly beneficial when testing new products in the market or producing customized components for specific customer needs.
On-demand manufacturing is another significant advantage, facilitating the rapid production of parts and reducing the time from design to delivery.
Short-run production typically involves producing 1,000 to 10,000 parts, ensuring swift delivery and faster time to market. This approach is ideal for businesses with limited budgets or those producing products with inherently low usage volumes.
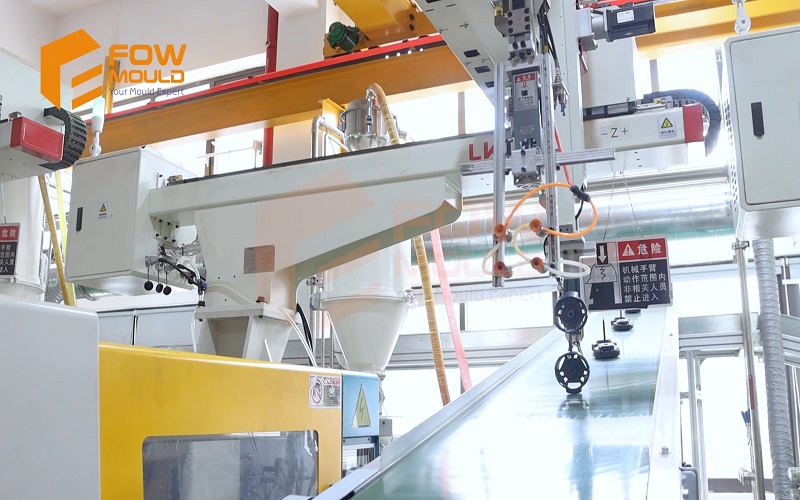
Key Benefits of Low Volume Injection Molding
Low volume injection molding offers a plethora of benefits that make it an attractive option for many businesses. One of the most significant advantages is cost-effectiveness.
By reducing the need for large upfront investments, this process allows companies to manage their budgets more efficiently. Additionally, the ability to make quick design changes without incurring substantial costs makes it a flexible solution for product development.
Moreover, the shorter lead times associated with low volume injection molding mean that businesses can respond more rapidly to market needs. This is particularly beneficial for small and medium-sized enterprises that require efficient and economical manufacturing solutions.
Let’s delve deeper into these benefits.
Cost-Effectiveness
Using low volume injection molding prevents significant financial commitments that are typically necessary for high-volume production. This process can diminish overhead costs significantly due to reduced waste and inventory risks.
On-demand manufacturing can further reduce overhead costs linked to warehousing and unsold products.
For businesses, this means a cost-effective solution that allows for the production of smaller quantities without the financial burden of large-scale operations.
This approach is particularly beneficial for startups or companies with limited budgets, enabling them to innovate and test new products without significant financial risks.
Flexibility in Design
One of the standout advantages of low volume injection molding is the flexibility it offers in design. This approach allows for multiple design iterations throughout the production process without incurring substantial costs. Swift alterations in part design can be made, ensuring minimal financial repercussions for design adjustments.
The ability to make quick and cost-effective design changes means that businesses can continuously refine their products to better meet market demands. Mold designs are often kept small to reduce costs, making this approach an excellent choice for companies looking to innovate without breaking the bank.
Shorter Lead Times
The process of low volume injection molding significantly shortens lead times, which is crucial for time-sensitive projects.
The overall production cycle is notably faster, leading to quicker availability of finished products for market testing. Modern manufacturing technologies play a pivotal role in enhancing the efficiency of low volume production processes.
For new product development, low volume injection molding allows for the use of simplified molds made from materials like aluminum, which can be completed in as little as 20 days. This rapid turnaround is invaluable for businesses looking to get their products to market quickly.
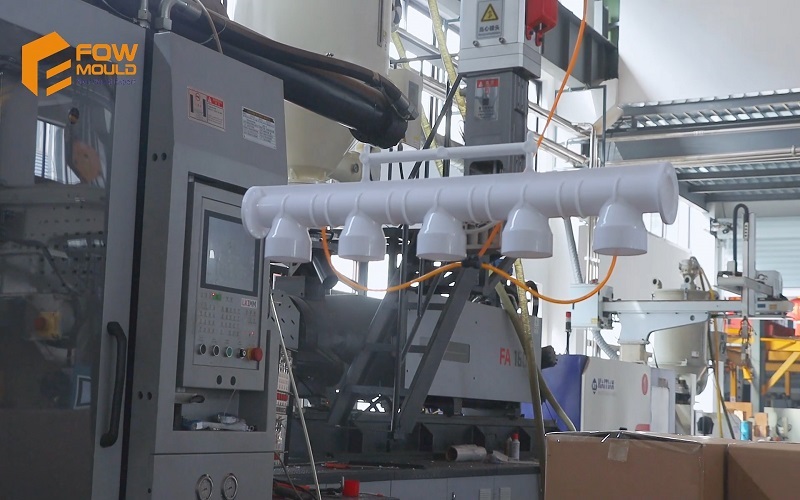
Material Selection for Low Volume Injection Molding
Choosing the right material is a crucial factor in low volume injection molding.
The selection process involves considering factors such as strength, thermal and chemical resistance, durability, and cost.
Commodity plastics or specialty plastics and polymer blends are appropriate choices for this method. Common materials used for injection molds include aluminum, P20 steel, and NAK80 steel.
Aluminum is often emphasized for its cost-effectiveness and design flexibility in low volume injection molds.
On the other hand, steel molds like P20 or NAK80 provide tighter tolerances and finer finishes, making them advantageous for higher volume production. The choice of material is influenced by the intended application and operating environment.
Common Thermoplastic Materials
Thermoplastics are plastic polymers that are pliable and moldable at high temperatures and solidify upon cooling.
Common thermoplastics used in low volume injection molding include ABS, PS, PE, and PP due to their versatility. When selecting thermoplastics, consider mechanical properties, exposure resistance, cost, pliability, density, impact resistance, and dimensional accuracy.
Commodity plastics like ABS and PP are generally less expensive than specialty plastics, which can be more costly due to their specific properties. With experience in over 700 types of resins, manufacturers can provide better material recommendations tailored to project needs.
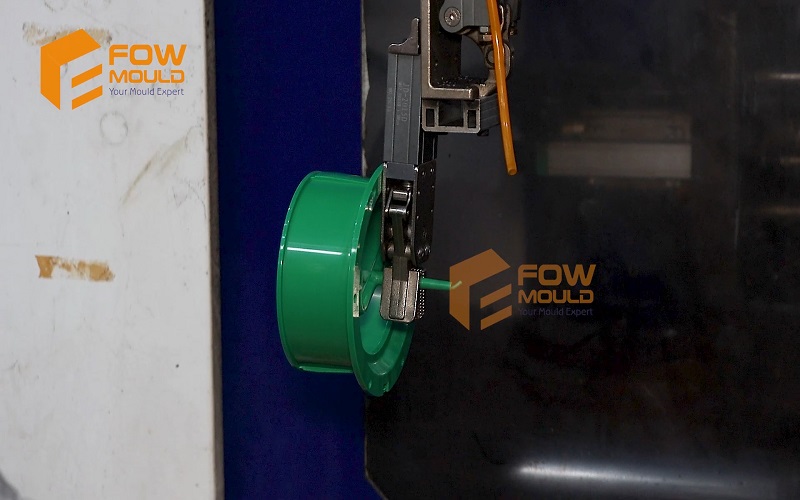
Impact of Fillers and Additives
Fillers and additives play a crucial role in enhancing the material properties of injection molded plastic parts. Additives can enhance thermal stability and improve impact resistance, contributing to the durability of injection molded parts.
For example, adding glass fibers to a plastic can significantly increase its strength and rigidity. These enhancements ensure that the final products meet specific performance requirements and can withstand the conditions of their intended applications.
Designing Parts for Low Volume Injection Molding
Designing parts for low volume injection molding requires careful consideration of several factors to ensure optimal results.
Key design considerations include maintaining appropriate wall thickness, incorporating draft angles for easier ejection, and using radii on corners to improve strength. During low-volume production, tooling-related issues requiring part design changes can be identified and resolved.
Quality assurance involves thorough inspection of parts to detect defects and ensure they meet established standards. Clear procedures for managing design modifications are essential to maintaining compliance with established standards.
Wall Thickness Guidelines
Maintaining consistent wall thickness is crucial for ensuring the structural integrity of injection molded parts. It helps avoid production issues such as air trapping and stress concentration.
As a general rule, wall thickness should be between 0.6 and 2mm to keep costs reasonable. Avoiding sharp corners in the design can prevent stress concentration and compromise part integrity.
Incorporating Draft Angles
Draft angles are essential for streamlining the ejection process and enhancing part durability. Incorporating draft angles in the design allows for easier ejection of parts from molds, reducing the risk of damage during the process.
The presence of draft angles contributes to the overall durability of the molded parts, minimizing defects and increasing product quality. This design consideration is crucial for effective low volume injection molding, ensuring efficient production and high-quality outputs.
Using Radii on Corners
Incorporating radii on corners in the design of injection molded parts can significantly improve both strength and moldability.
Rounded corners enhance structural integrity by reducing stress concentrations that can lead to fractures. This design approach reduces the likelihood of defects during the injection molding process, making parts easier to produce.
Using radii on corners results in stronger and more moldable components, leading to higher quality products.
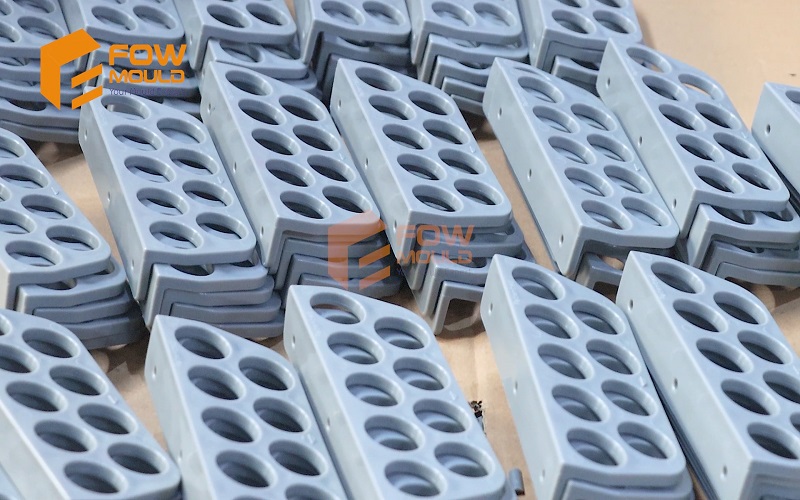
Mold Making for Low Volume Injection Molding
The mold quality is essential for achieving high-quality parts in low volume injection molding. It plays a crucial role in the overall process. Using aluminum molds can expedite production for mid-volumes, reducing costs and lead times significantly.
Aluminum tooling is a common choice due to its faster production times and lower costs compared to steel tooling.
CNC machining offers high precision in mold creation, which is essential for maintaining quality in low-volume production. This method allows for the use of various materials, making it adaptable for different production needs and specifications.
Aluminum vs. Steel Molds
Aluminum molds can be produced much faster than steel molds, typically taking only a few days compared to weeks for steel. This speed is advantageous for small batch production as it allows for rapid iteration and quicker turnaround times.
Additionally, aluminum molds are easier to work with, making them a preferred choice for low volume injection molding.
However, steel molds tend to be more durable, especially when used with abrasive materials. They provide tighter tolerances and finer finishes, making them suitable for higher volume production. While aluminum molds generally have a tolerance capability of +/- 0.005 inches, steel molds can achieve even finer tolerances.
Despite their higher initial cost, steel molds are an investment in quality and longevity.
Multi-Cavity Molds
Multi-cavity molds are designed to produce multiple identical parts simultaneously. This capability can significantly increase production efficiency by allowing several parts to be produced in a single cycle. For businesses looking to scale their production without the need for separate molds, multi-cavity molds offer a practical solution.
Using multi-cavity molds can also lead to significant reductions in production costs when producing larger quantities of parts. Maximizing output per cycle reduces the overall cost per part, making this approach cost-effective for low to mid-volume production runs. This efficiency is crucial for maintaining competitiveness in fast-paced markets.
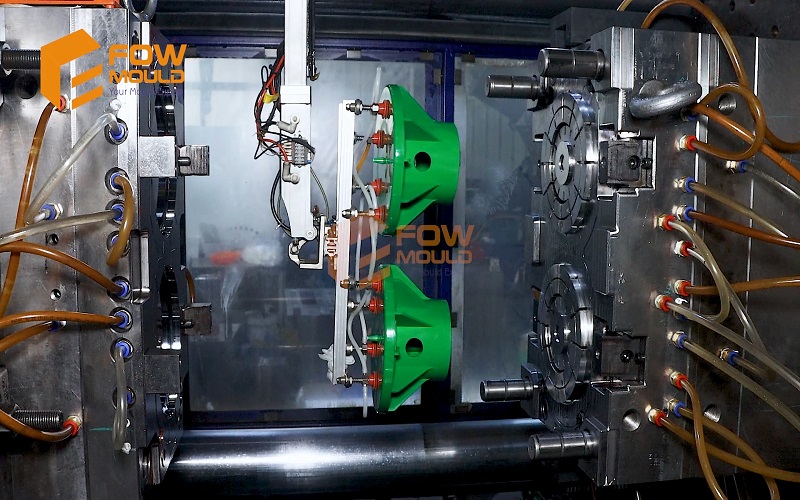
Prototyping and Tooling for Low Volume Injection Molding
Prototyping and tooling are essential steps in the low volume injection molding process, facilitating quicker market entry by allowing faster production and testing of prototypes.
Using rapid prototyping methods, such as 3D printing, can significantly lower the costs and lead times associated with mold production. This enables businesses to test and refine their designs efficiently before committing to large-scale production.
Midwest Mold, for instance, provides rapid prototyping and prototype injection molds, making it easier for companies to bring their innovations to life. These technologies enable businesses to ensure their products are market-ready faster and with greater precision.
3D Printing for Prototypes
3D printing allows for rapid prototyping without the need for expensive molds. This technology enables the rapid production of prototype molds, allowing for quick iteration of designs before final production.
Additive manufacturing techniques in 3D printing can create complex geometries that are difficult to achieve with traditional methods.
For businesses, this means the ability to test and refine their designs quickly and cost-effectively. 3D printing is particularly valuable when designs are not yet finalized and require frequent adjustments. This flexibility is crucial in the early stages of product development, ensuring that the final product meets all design specifications and performance requirements.
CNC Machining for Tooling
CNC machining is a reliable small quantity manufacturing method, versatile for various materials. This technique creates accurate molds, patterns, or dies for low volume production, ensuring high precision and quality in the final products.
Low volume production allows for design modifications without a major impact on costs or timelines. This adaptability is essential for businesses looking to innovate and respond to market demands quickly. CNC machining allows companies to produce high-quality prototypes and final products efficiently, meeting all design requirements and quality standards.
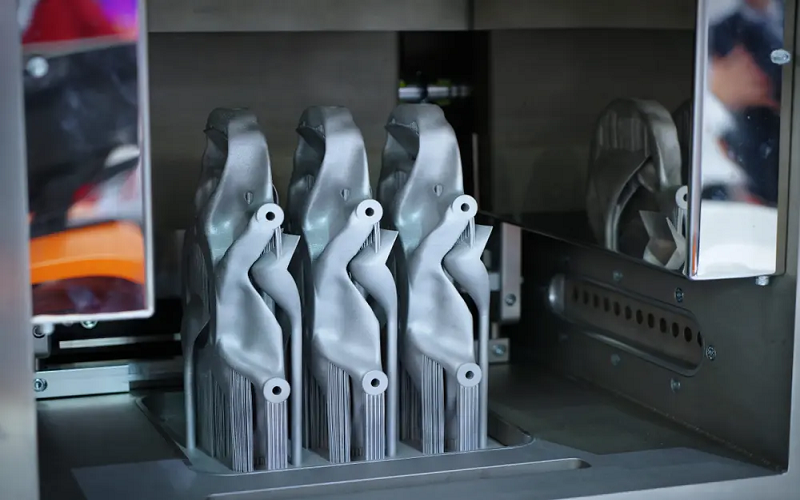
Quality Control and Post-Processing
Quality control and post-processing are critical components of the low volume injection molding process. Inspecting parts for defects and ensuring quality standards is essential for maintaining product integrity and performance.
Effective quality control measures guarantee that parts meet industry standards and customer expectations.
Post-processing activities, such as trimming, deburring, and surface finishing, can enhance the quality and usability of the final product. These steps ensure that the dimensions and aesthetics of molded parts meet the desired specifications, making them ready for market application.
Inspection Techniques
Adherence to industry standards ensures that all products meet the necessary quality benchmarks. Critical-to-Quality features in part design are dimensions crucial for part function that need special attention in design processes.
An Inspection Statement of Work (ISOW) provides information about issues with tolerances and moldability of features in the model.
Following industry standards is crucial for compliance and quality assurance in low volume injection molding. This adherence ensures that the final products are not only functional but also reliable and durable.
Post-Processing Steps
Trimming is a key post-processing activity that removes excess material and refines the shape of the molded parts. This step helps ensure that the dimensions and aesthetics of the parts meet the desired specifications. Secondary surface finishing operations can further enhance the appearance and functionality of molded parts after the initial production phase.
Post-processing activities such as trimming and surface finishing improve the quality and usability of molded parts. These steps are essential for delivering high-quality products that meet or exceed customer expectations.
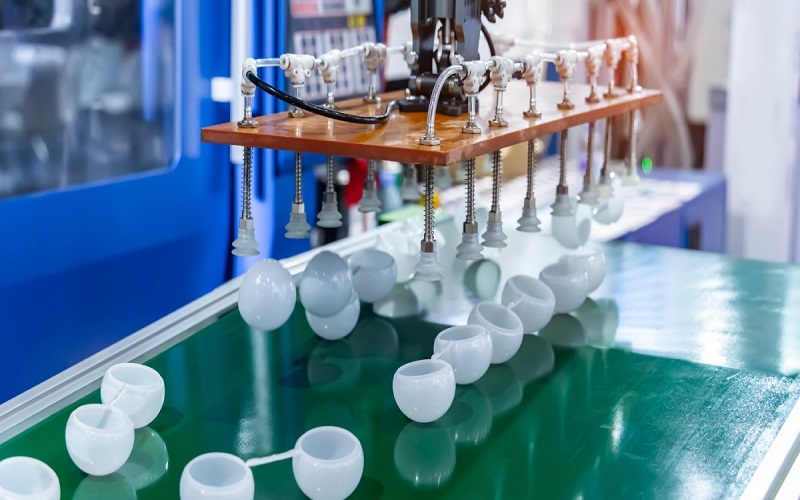
Applications of Low Volume Injection Molding
Low volume injection molding is effectively utilized in various industries, including aerospace, automotive, and consumer electronics, for creating custom parts.
This method is particularly useful in sectors like automotive for custom parts and in electronics for housing prototypes. Utilizing low volume injection molding can enable faster product launches compared to traditional methods.
This approach enables businesses to respond quickly to market demands and bring innovative products to market with greater efficiency.
Rapid Prototyping
Low volume production supports testing of new concepts in various industries before committing to full-scale manufacturing. Urethane casting offers advantages for rapid prototyping, including no upfront cost, reduced lead time, and the ability to promptly test design requirements.
Rapid prototyping is critical in product development as it allows for the fast creation and iteration of designs before moving to mass production. This approach ensures that rapid prototypes are thoroughly tested and refined, leading to higher quality and better-performing final products.
Small Batch Production
Small batch production offers key advantages, including cost-effectiveness and flexibility in manufacturing to meet changing market demands. Choosing the right materials for low volume injection molding is crucial, as it impacts product quality and performance.
Design considerations, such as ensuring manufacturability and quality, are essential aspects of achieving successful small batch production. Small batch production is applicable across various industries, with on-demand manufacturing helping to reduce excess inventory and respond promptly to market fluctuations.
On-Demand Manufacturing
On-demand manufacturing in injection molding is a method that enables low-volume, customized products and eliminates quoting delays. The main advantage of on-demand injection molding is that it reduces the need for large inventories and lowers storage costs. On-demand manufacturing provides real-time quotes and visibility of orders, satisfying immediate production needs.
This approach creates a more flexible supply chain, allowing businesses to respond swiftly to changing consumer demands without carrying excess inventory. Technologies such as Big Data analytics, software, and hardware for Industry 4.0 integration enhance on-demand manufacturing.
This method addresses pain points regarding lead time and communication, further benefiting inventory management.
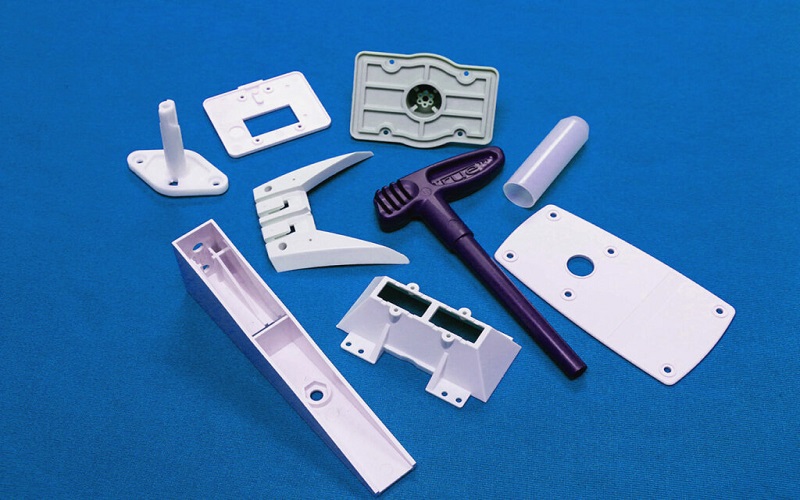
Choosing the Right Partner for Low Volume Injection Molding Services
Choosing the right partner for low volume injection molding services is crucial for achieving success. Identifying a suitable partner requires a deep understanding of their expertise and methodologies in low volume injection molding. Finding a low volume injection molding service provider can be challenging due to various factors.
A reliable partner should offer a wide range of prototyping services, mold flow analysis, responsive manufacturing, and part design. Additional manufacturing services that can enhance an injection molding partner’s offerings include CNC machining and injection molding.
Evaluating Capabilities and Expertise
When selecting a low volume injection molding partner, consider their experience, knowledge, and expertise. Companies capable of low to moderate production can offer prototypes quickly for testing, ensuring that products meet all design specifications and performance requirements.
A reliable partner should also provide a range of services, including prototyping, mold flow analysis, and responsive manufacturing. This ensures that all aspects of the production process are handled efficiently and effectively.
Ensuring Specification Compliance
Ensuring that a low volume injection molding company complies with design specifications is essential for maintaining product quality. Every adjustment to the design must be approved to maintain compliance with project requirements. This adherence guarantees that the final products meet all necessary standards and perform as expected.
A reliable partner will have clear procedures for managing design modifications and ensuring that all changes are thoroughly reviewed and approved. This approach helps maintain the integrity of the final product and ensures that it meets all customer expectations.
Prioritizing Efficiency and Quality
Utilizing the latest technologies in small batch injection molding enhances production efficiency and quality. An on-demand injection molding company should adhere to the best standards of efficiency and quality to produce small batches effectively. This ensures that the final products are of high quality and meet all customer requirements.
Prioritizing efficiency and quality ensures that products are delivered on time and meet all necessary standards. This approach is crucial for maintaining customer satisfaction and achieving long-term success.
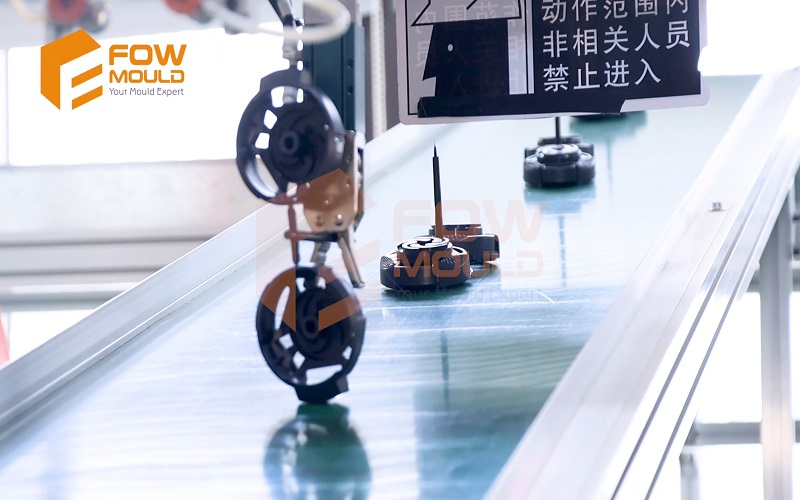
Alternatives to Low Volume Injection Molding
While low volume injection molding offers many advantages, there are alternatives that may be more suitable for certain applications. These alternatives include 3D printing, urethane casting, and thermoforming. Each method has its own set of benefits and limitations, making them suitable for different types of projects.
Understanding these alternatives allows businesses to make informed decisions about the most suitable manufacturing process for their needs.
3D Printing
3D printing offers no upfront investment in molds and provides a short lead time. Engineers and designers favor 3D printing for its ability to facilitate rapid iterations. This capability enhances the efficiency of product design. However, 3D printed parts typically exhibit layered surfaces, which can affect their appearance and function.
The surface finish of 3D printed parts can be improved through sanding and painting. This method is particularly valuable for creating prototypes when designs are not yet finalized and require frequent adjustments.
Urethane Casting
Urethane casting is often used for producing flexible parts and can be more cost-effective for small production runs. This method involves pouring liquid urethane into a mold to create parts, which can be faster than traditional injection molding. Urethane casting is particularly effective for creating detailed prototypes and small production runs quickly.
This process is ideal for creating parts with intricate details and can replicate high-quality finishes similar to injection-molded items. Urethane casting offers a practical alternative for businesses looking to produce small batches of high-quality parts efficiently.
Thermoforming
Thermoforming involves heating plastic sheets until they are pliable, then forming them over a mold. This process is suitable for producing large parts with relatively simple geometries. Thermoforming can be a cost-effective alternative for low volume production when intricate details and tight tolerances are not required.
This method is particularly useful for creating large panels and enclosures, making it a practical choice for certain applications. By understanding the benefits and limitations of thermoforming, businesses can choose the best manufacturing process for their specific needs.
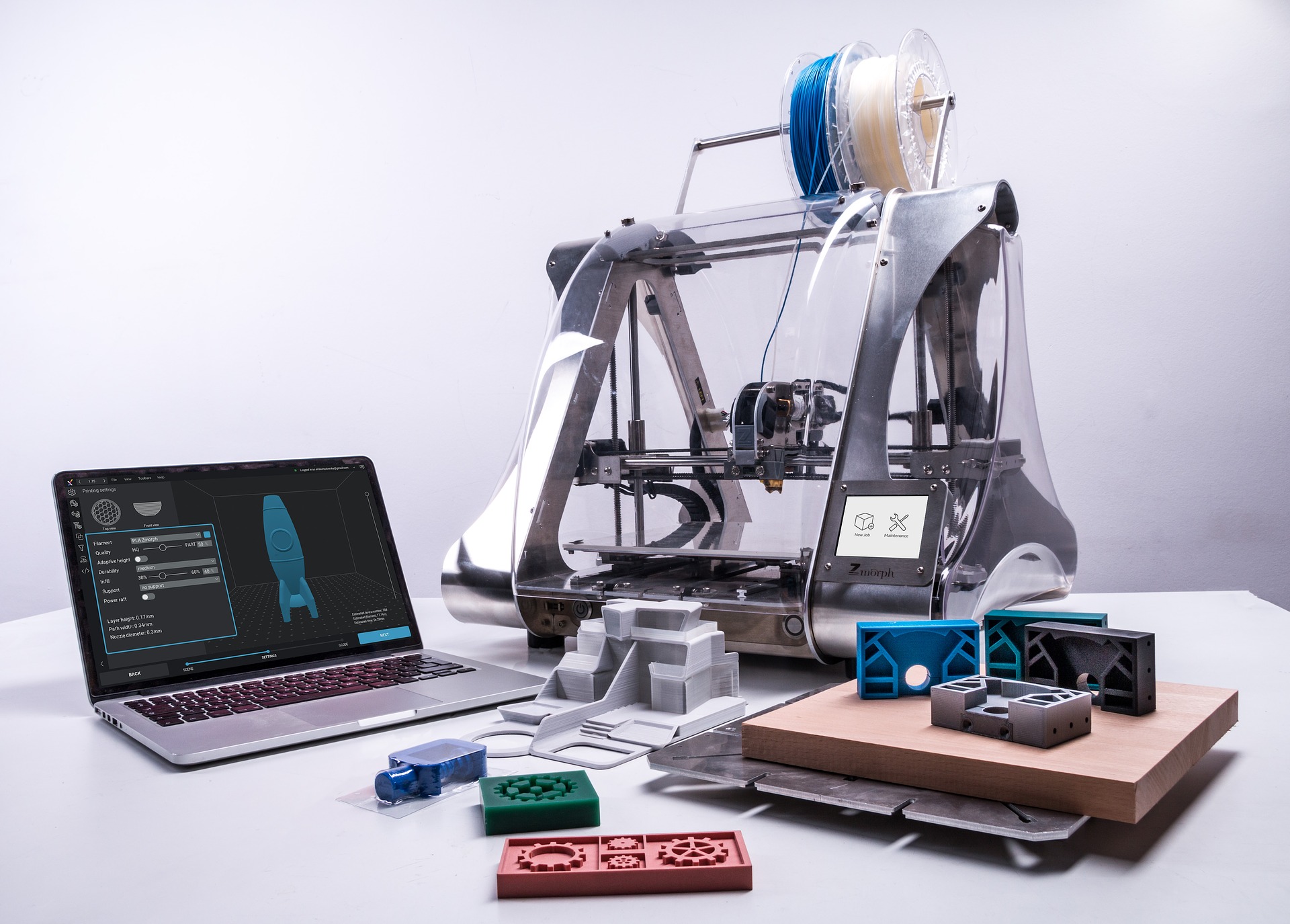
Summary
Low volume injection molding offers a cost-effective, flexible, and efficient solution for manufacturing small batches of high-quality parts. By understanding the injection molding process, choosing the right materials, and designing parts for optimal results, businesses can leverage this method to innovate and respond quickly to market demands.
Whether you’re looking to prototype new designs, produce small batches, or implement on-demand manufacturing, low volume injection molding provides the tools and techniques to achieve success. Embrace the potential of this innovative approach and propel your business forward with confidence.
Frequently Asked Questions
What is the typical volume range for low volume injection molding?
The typical volume range for low volume injection molding is between 100 to 10,000 pieces. This allows for flexibility in production while meeting specific project needs.
What materials are commonly used in low volume injection molding?
Low volume injection molding typically utilizes materials such as ABS, PS, PE, and PP, as well as specialty plastics and polymer blends. These choices ensure versatility and adaptability for various applications.
What are the benefits of using aluminum molds for low volume production?
Utilizing aluminum molds for low volume production is advantageous due to their quicker production times, cost-effectiveness, and design flexibility. These benefits make aluminum molds an optimal choice for efficient and adaptable manufacturing processes.
How does 3D printing benefit the prototyping process?
3D printing significantly enhances the prototyping process by facilitating rapid design iterations without the need for costly molds, thereby accelerating product development. This efficiency empowers designers to refine their concepts swiftly and effectively.
What post-processing steps are involved in low volume injection molding?
Trimming, deburring, and surface finishing are essential post-processing steps in low volume injection molding to improve the quality and usability of the final product. These steps ensure the parts meet desired specifications and functional requirements.