If you’re wondering how to create plastic molds, this guide will take you through a straightforward, detailed process.
You’ll learn about the necessary tools and materials, design principles, workspace setup, and techniques for building and curing your molds.
By following these steps, you’ll be equipped to produce high-quality plastic molds efficiently.
Key Takeaways
Essential tools and materials, such as high-quality metals and plastics, are critical for creating durable and efficient plastic molds.
The design phase utilizes CAD tools for precision, and thorough testing ensures molds produce high-quality plastic parts.
Regular maintenance and professional consultation can significantly enhance mold longevity and production quality.
Essential Tools and Materials for Mold Making
Starting a mold-making project requires the right tools and mold material. Common materials for plastic injection molds include aircraft-grade aluminum and hardened mold steels, which provide the durability needed for high-quality plastic parts.
Choosing the appropriate plastic resin type involves considering multiple sources to ensure favorable cured properties, ease of use, price, and regulatory compliance.
The primary elements of a plastic injection mold include metal plates. Additionally, there are complex machined components found on both the cavity-side and core-side.
Tools like CNC machines are used to achieve the precision required for these components. Free-standing molds are designed for production in any SPI standard plastic injection molding machine injection molding process injection molding machine, making them versatile and efficient.
Custom molds can be created using reusable molding materials like silicone mold and plaster. The quality of these components directly affects the quality of the plastic parts produced and the mold’s useful life expectancy.
Investing in high-quality tools and materials lays the foundation for creating exceptional molds that yield consistent and reliable results.
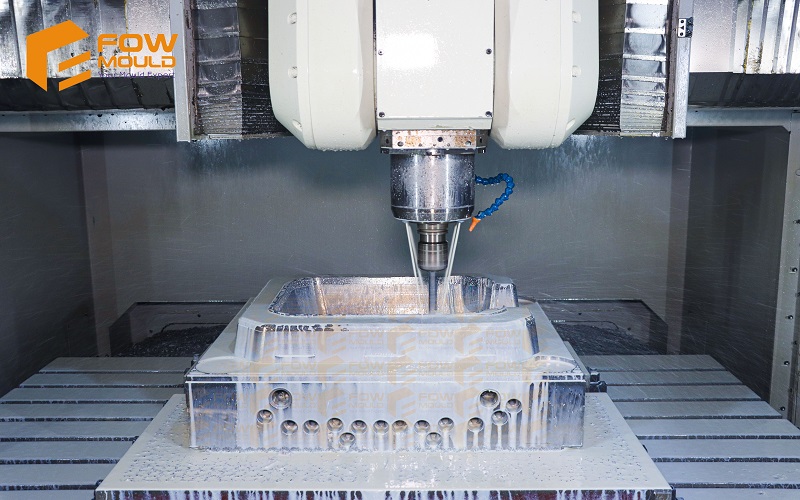
Designing Your Mold
Designing your mold requires precision and careful planning. Computer-aided design (CAD) tools help create accurate mold designs optimized for manufacturability.
These tools help in visualizing the desired shape and making necessary adjustments to ensure the final product meets the specifications.
Custom molds offer tailored solutions that meet specific manufacturing needs, enhancing efficiency and ensuring the production of high-quality plastic parts. Testing the mold with actual plastic items verifies that it produces parts meeting the desired quality standards.
Trial runs help identify issues such as incomplete fills or surface defects, ensuring the final product meets quality standards.
Accurate finishing of the mold is critical for ensuring that the final product meets design specifications.
Trimming excess material can enhance the aesthetics and functionality of the molded part. Focusing on these design aspects ensures molds that meet and exceed expectations.
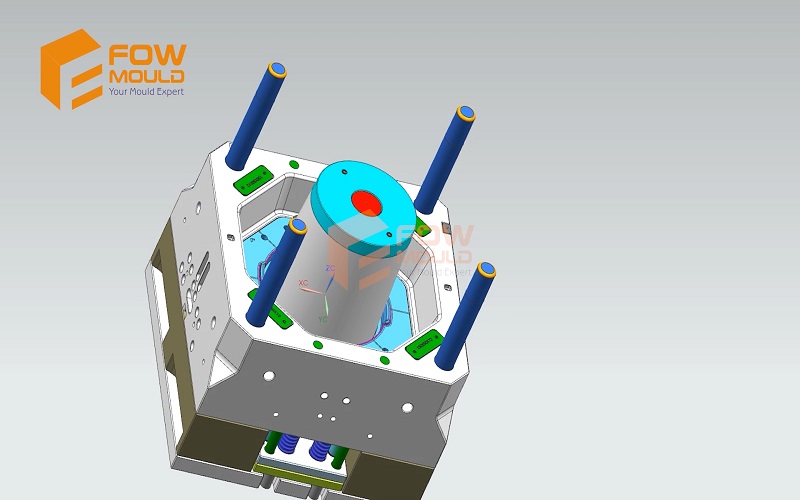
Preparing the Work Space
A dedicated workspace for mold making enhances both safety and productivity. Organizing tools and materials systematically in a specific area significantly boosts efficiency. Regular cleaning of the workspace helps to mitigate contamination, which is vital for high-quality mold production.
Contamination with oils or talc can lead to partial de-lamination of the mold, so maintaining cleanliness is essential for proper mold integrity. Wearing personal protective equipment, like gloves and safety glasses, is crucial when working with resins and chemicals.
Good lighting in the workspace prevents accidents and improves accuracy during mold preparation.
Creating the Mold Structure
Creating the mold structure involves several critical steps that determine the quality and durability of the final product.
Proper cooling line design in molds maintains dimensional precision and part appearance. Choosing appropriate materials affects the strength and durability of the final molded part.
The positioning of gate locations during mold design significantly affects the flow of material, impacting the quality of the finished product.
Incorporating draft angles into mold designs facilitates the easy ejection of parts without damage. Maintaining a 3-degree shutoff angle between mold components ensures durability.
Next, we’ll explore building the mold base and mixing and pouring the resin.
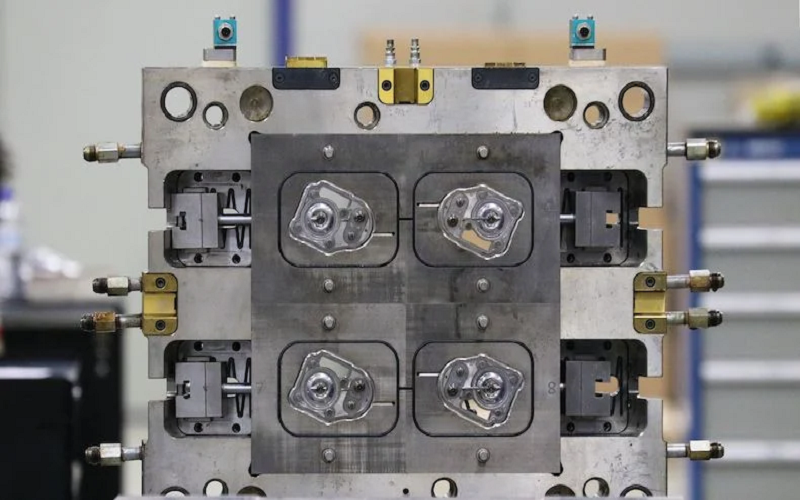
Building the Mold Base
Building the mold base is foundational in the mold-making process. Designers often use standard mold frames from reputable manufacturers like LKM, DME, and HASCO to save time. These frames provide a reliable starting point and ensure compatibility with various plastic injection molding machines.
Gate location and draft angles are crucial in mold base design. Proper gate positioning ensures an even material flow, vital for high-quality plastic parts. Incorporating draft angles facilitates the easy ejection of parts, preventing damage and ensuring the longevity of the mold.
Mixing and Pouring the Resin
Mixing and pouring the liquid resin requires precision and care. Thoroughly mixing the resin before pouring avoids imperfections. This step is crucial for achieving a uniform consistency in the final product.
Careful transfer of the mixed resin into the mold frame is vital for a successful pour. Ensuring proper packing of the mold frame helps eliminate air bubble formation during and after pouring. Following these steps ensures a high-quality mold that meets your specifications.
Curing and Removing the Mold
The curing process hardens the resin to take the shape of the mold. Different resin types have varying curing times and conditions for the best results. Precise timing during the curing process is critical to avoid issues such as incomplete curing or deformation.
Ensure the resin has fully hardened before gently prying the mold from the frame using tools or by hand. Next, we’ll explore the specifics of curing the resin and carefully removing the mold.
Curing the Resin
The initial curing stage for epoxy resin commonly lasts between 24 to 48 hours, during which it firms up but may remain somewhat pliable. Complete curing of epoxy resin can take anywhere from 3 days to a week, influenced by the specific resin formulation and its thickness.
Polyester resin generally cures within 24 to 48 hours under similar temperature conditions.
Optimal curing occurs in environments maintained at temperatures between 70°F to 85°F (21°C – 29°C) with low humidity.
Humidity levels below 80% are ideal for the curing process, as higher humidity can introduce air bubbles and affect the resin’s hardness. Proper airflow around the resin during curing helps expedite the hardening process and ensures a more uniform cure.
Carefully Removing the Mold
Wait until the mold is fully cured to prevent any deformation during removal. Using a gentle twisting motion can help in smoothly detaching the mold from the frame without causing damage.
Following these steps ensures the mold is removed without compromising its integrity.
Finalizing the Mold
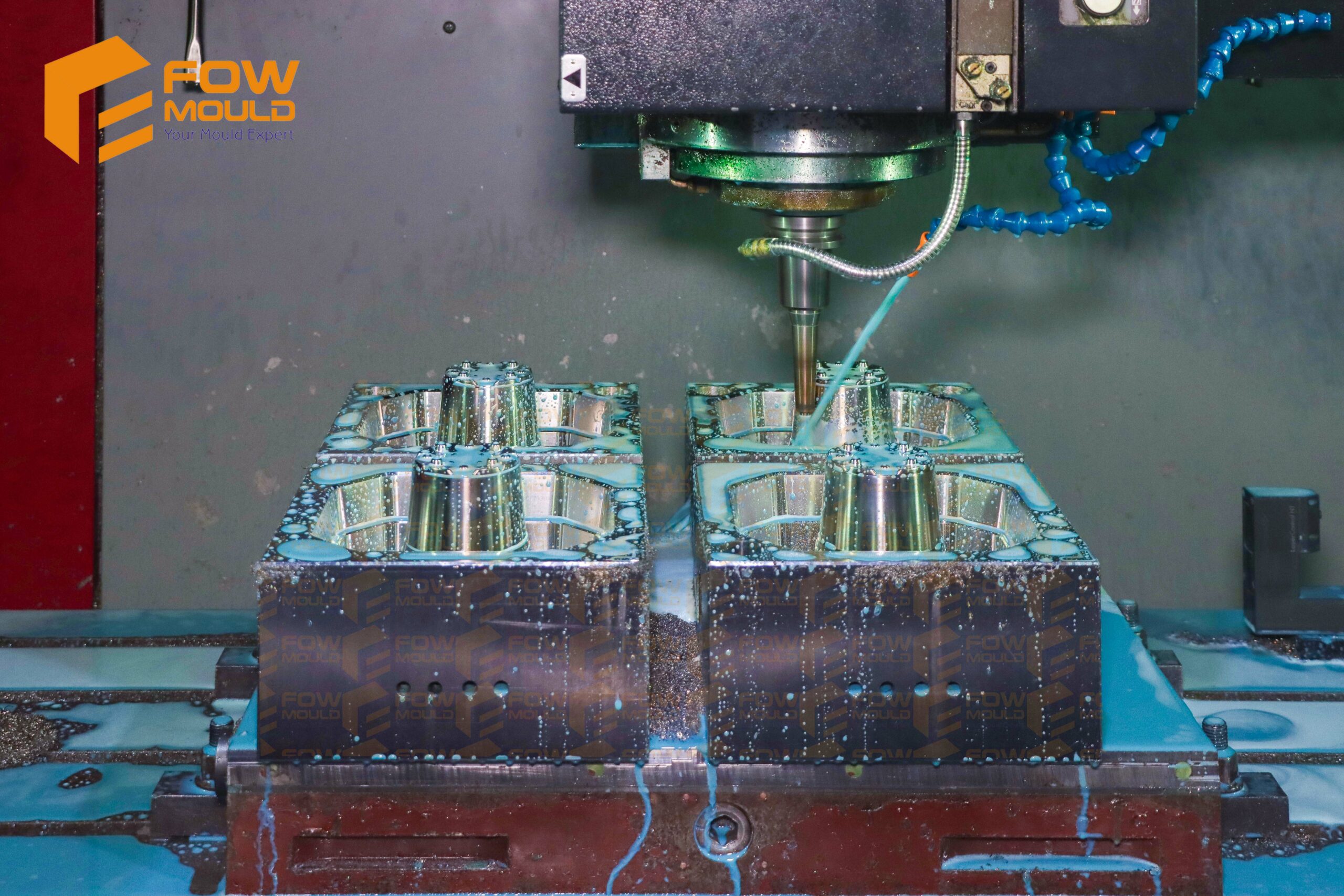
Finalizing the mold involves refining its features to ensure it meets the desired specifications. Enhancing the strength and assembly capabilities of molded parts ensures their durability. Adding ribs and bosses to the mold can significantly improve structural integrity and lead to higher quality, more reliable plastic parts.
Careful placement of these design features ensures they contribute effectively without complicating the mold design. Next, we’ll examine trimming excess material and testing the mold.
Trimming Excess Material
Using precision tools for trimming can enhance the accuracy of the mold edges and ensure a better fit for the final product. Precision tools provide a controlled trimming process, allowing for smooth edges and the desired shape of the mold.
Excessive pressure during the mold-making process may cause the finished mold to become hard and springy, preventing it from lying flat. Avoid excessive pressure to prevent mold distortions during trimming.
Testing the Mold
Quality of the mold is essential for high-quality custom plastic parts. Removing excess material is crucial for achieving the exact specifications needed for the molded parts. Trimming is essential to eliminate flash and achieve precise dimensions, which directly impacts the quality and functionality of the molded parts.
Mold testing involves checking the mold’s structure and functionality. Issues such as flash, venting problems, and cooling efficiency are evaluated during this stage to ensure the mold is ready for production.
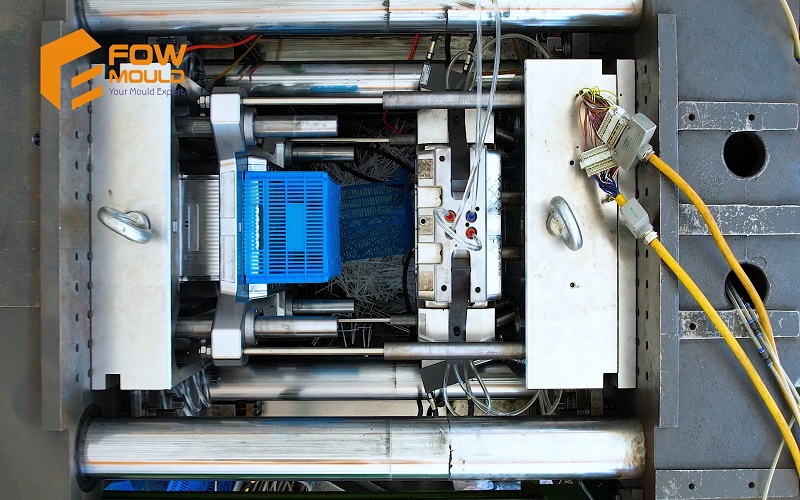
Advanced Techniques for Complex Shapes
Creating complex shapes requires advanced techniques and tools.
CNC machining allows for precise shaping of complex mold designs, enabling the creation of intricate features. Silicone molds are beneficial for producing detailed and flexible components, often used for complex shapes and multiple cavities.
Advanced molding techniques such as side actions and telescoping shutoffs are essential for creating undercuts in molded parts.
These techniques allow for greater design flexibility and the production of more intricate and detailed plastic parts.
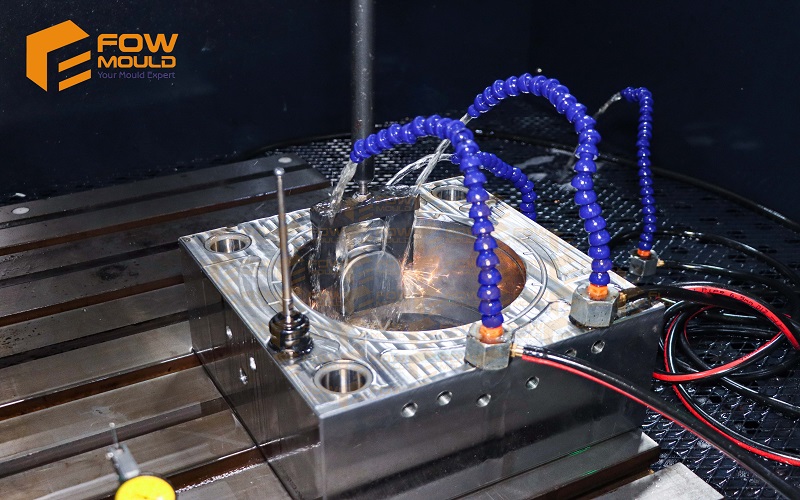
Maintenance and Longevity of Plastic Molds
Regular maintenance is crucial for the longevity of plastic molds. Regular cleaning of mold surfaces is necessary to eliminate any residue, such as plastic deposits. Maintaining detailed records of maintenance activities is essential for tracking mold performance.
Implementing preventive maintenance based on mold usage can proactively address potential issues.
Inspecting mold components for wear and damage, especially in high-stress areas, ensures the mold remains in good condition.
Using durable materials like P20, NAK80, and H13 steels can significantly extend the mold’s lifespan.
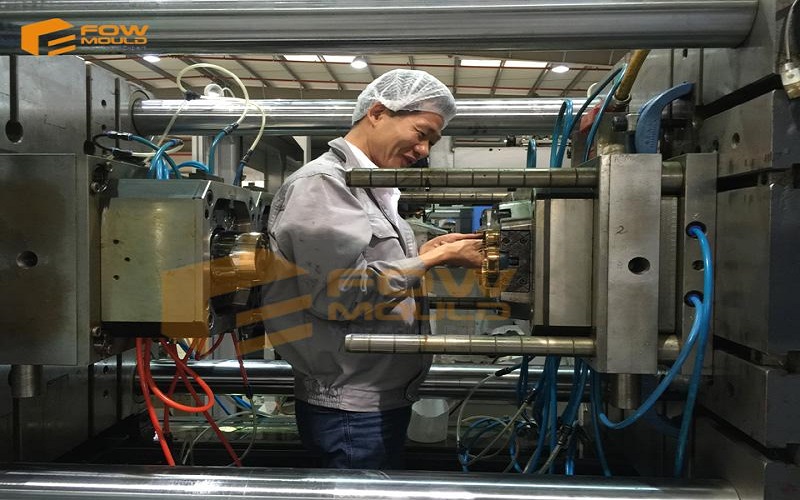
Cost Considerations in Mold Making
The cost of mold making varies based on several factors. The cost for injection molds can range from $100 for basic 3D printed molds to over $100,000 for complex steel molds intended for high-volume production. Mold costs are driven by the complexity of the design, production volume, and the materials used.
High-volume production often requires durable steel molds, which are more expensive but offer lower per-part costs when scaled. Using aluminum molds is a cost-effective option for mid-volume production, typically lasting several thousand shots.
Balancing cost with production volume and material choice is crucial for cost-effective mold making.
Common Challenges and Solutions in Mold Making
Mold making comes with its own set of challenges. Balancing wall thickness is important for uniform cooling and to minimize defects during the molding process. Managing undercuts is essential for ensuring that parts can be easily removed from molds without complications.
Effective mold design includes considerations of part geometry to ensure structural integrity and ease of production. Proper alignment of mold halves is crucial to avoid defects during operation. Regular checks of the cooling and venting systems help prevent issues like air traps and overheating.
Contact Professional Mold Makers
For large-scale production runs or intricate mold designs, consulting professional mold makers is advisable.
Their experience and resources ensure high durability and quality in the final product. Professional mold makers provide access to advanced technology and techniques that may not be available to individual mold makers.
Their expertise can lead to greater efficiency and speed, ensuring that projects are completed on time. Consulting with professional mold makers can ultimately save time and prevent costly errors.
Understanding mold-making complexities highlights the value of professional assistance in achieving desired outcomes.
Summary
The journey of creating plastic molds is filled with meticulous steps, from gathering essential tools and designing your mold to finalizing and testing it.
Each step plays a crucial role in ensuring the quality and durability of the final product. By following this guide, you can confidently embark on your mold-making projects, whether for custom plastic parts or high-volume production.
Remember, professional mold makers are always an option for more complex or large-scale projects.
Their expertise can save time and ensure high-quality results. So, dive into the world of mold making and bring your creative ideas to life with precision and excellence.
Frequently Asked Questions
What materials are commonly used for plastic injection molds?
Plastic injection molds are commonly made from aircraft-grade aluminum and hardened mold steels, offering the necessary durability and strength for producing high-quality plastic components.
Why is it important to use CAD tools in mold design?
Using CAD tools in mold design is crucial for creating precise and manufacturable designs, which ensures that the final product meets specifications and quality standards. This optimization minimizes errors and enhances efficiency in the production process.
How can I prevent air bubbles when pouring resin?
To prevent air bubbles when pouring resin, ensure thorough mixing of the resin and proper packing of the mold frame. This approach effectively minimizes air bubble formation during the process.
What are the benefits of consulting professional mold makers?
Consulting professional mold makers ensures high durability and quality in your products through their advanced technology and expertise, ultimately saving you time and preventing costly errors.
How does regular maintenance impact the longevity of plastic molds?
Regular maintenance significantly enhances the longevity of plastic molds by ensuring consistent performance and preventing wear and damage through thorough inspections and cleaning. Implementing detailed records of these maintenance activities further supports mold durability.