Plastic shrinkage is a crucial physical phenomenon in the injection molding process, significantly affecting the final product’s dimensions and shape.
To achieve precise dimensions and avoid defects such as warping or sink marks, it is essential to understand and effectively compensate for shrinkage.
This article will delve into the phenomenon of plastic shrinkage in injection molding, with a focus on the shrinkage rates of common plastics such as ABS, PP, and PE.
Additionally, we will discuss the key factors influencing shrinkage and how manufacturers can effectively manage these factors to ensure consistent production of high-quality parts.
What Is Plastic Shrinkage?
Plastic shrinkage refers to the phenomenon where the volume or dimensions of plastic shrink during the injection molding process as it cools and solidifies from a liquid state.
This change in volume or dimensions is caused by the rearrangement and tightening of molecular chains.
Plastic shrinkage not only affects the dimensional accuracy of the final product but can also lead to injection molding issues such as warping, deformation, and sink marks.
Therefore, the study and control of plastic shrinkage in injection molding are crucial for ensuring the quality and dimensional accuracy of injection molded parts.
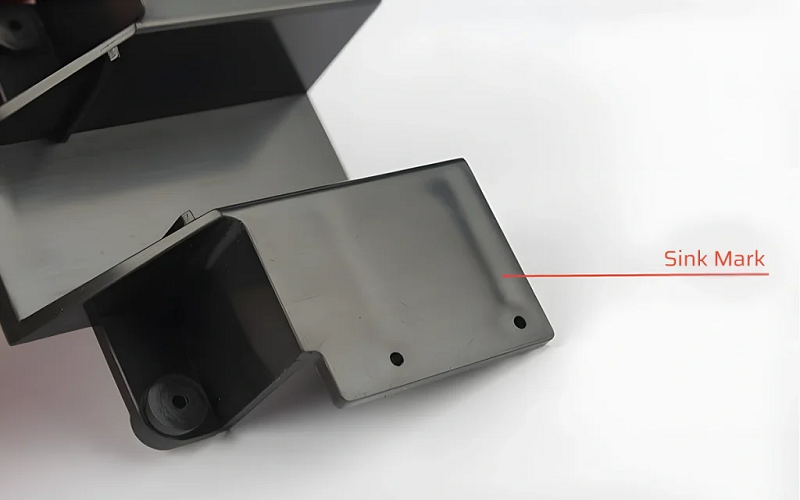
How To Calculate Plastic Shrinkage?
The degree of plastic shrinkage is typically measured by the plastic shrinkage rate, which is the percentage difference between the size of the molded part at molding temperature and the size after it has cooled to room temperature after being removed from the mold.
The specific formula for calculating shrinkage is as follows:
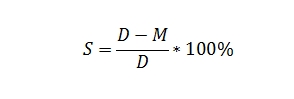
Where (S) represents the shrinkage rate, (D) represents the mold dimensions, and (M) represents the dimensions of the molded part.
The Shrinkage Values of Various Plastics
There are significant differences in the shrinkage rates of various plastic materials, mainly influenced by factors such as the type of plastic, crystallinity, molecular weight, and modifications.
- Thermoplastics
Thermoplastics generally have a shrinkage rate ranging from 0.5% to 5%. For example, ABS shrinkage typically falls between 0.4% and 0.7%, while PP shrinkage ranges from 1.0% to 2.5%.
- Thermosetting plastics
Plastics like epoxy resin and phenolic resin have lower shrinkage rates, generally between 0.2% and 0.5%.
- Reinforced plastics
Glass fiber-reinforced polyamides (PA6 and PA66) have lower shrinkage rates, usually between 0.1% and 0.8%.
- Special plastics
Plastics like fluoroplastics have higher shrinkage rates, reaching up to around 6%. Low-density polyethylene (LDPE) also has a high shrinkage rate, which can reach up to 5%.
Name | Min Value (%) | Max Value (%) |
ABS | 0.4 | 0.7 |
LDPE | 1.5 | 5.0 |
HDPE | 1.5 | 4.0 |
PP | 1.0 | 2.5 |
PC | 0.5 | 0.7 |
PA6 | 0.8 | 2.0 |
PA66 | 1.0 | 2.5 |
POM | 1.8 | 2.5 |
PPS | 0.1 | 0.3 |
PMMA | 0.2 | 1.0 |
What Are The Types Of Plastic Shrinkage?
- Linear Shrinkage
This is the most common form of shrinkage in plastic products during the injection molding process.
When molten plastic is injected into the mold and subsequently cools and solidifies, the dimensions of the product may change.
This type of shrinkage is typically related to the mold design and cooling conditions.
- Post-Molding Shrinkage
After the part is removed from the mold, it may continue to shrink during stabilization. This shrinkage occurs due to the release of internal stresses and further alignment of molecular chains.
- Directional Shrinkage
Some plastics may experience inconsistent shrinkage in different directions due to uneven cooling or mold design issues during molding, resulting in directional shrinkage.
- Post-Treatment Shrinkage
Certain plastics may undergo slight dimensional adjustments after post-treatment processes (such as heat or chemical treatment) due to changes in internal stresses.
- Moisture Absorption Expansion
For some hygroscopic plastics (such as nylon), expansion occurs upon moisture absorption.
While this is the opposite of shrinkage, understanding this expansion mechanism helps improve dimensional stability in plastic products.
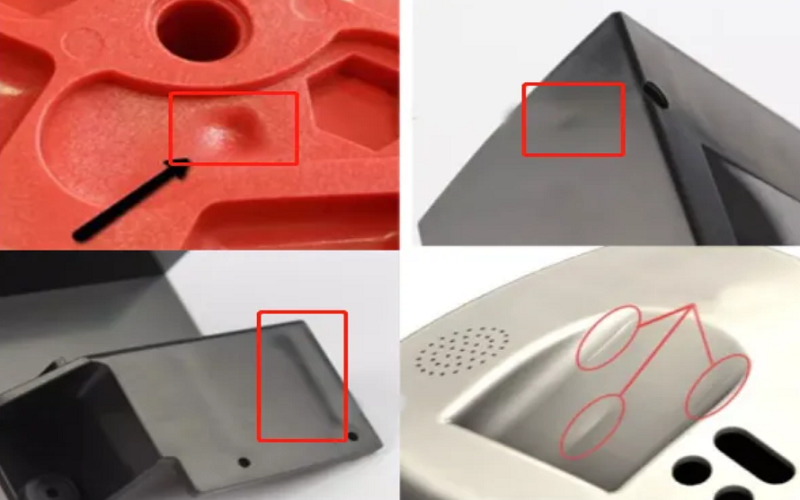
The Main Factors Influencing Shrinkage Rates
1.Plastic Types
Different types of plastics exhibit significant variations in plastic shrinkage rates.
For example, amorphous materials like PS, ABS, PC, and PVC have relatively low shrinkage rates, while semi-crystalline materials such as PP, PE, PBT, POM, and PPS tend to have higher shrinkage rates.
2.Part Shape and Wall Thickness
The shape and wall thickness of a part significantly affect the shrinkage rate.
Uneven wall thickness can lead to uneven shrinkage, which in turn may cause sink marks and warping.
3.Mold Structure
The design of the mold’s cooling system directly affects the cooling efficiency of the plastic, thereby influencing the shrinkage rate.
A well-designed cooling system can speed up the cooling and solidification process, reducing the overall shrinkage rate.
4.Process Parameters
Excessively high injection temperatures can reduce the viscosity of the plastic melt, accelerating the cooling and solidification process, which increases the shrinkage rate.
Similarly, excessive injection pressure can also increase shrinkage.
Additionally, the length of the holding time impacts the cooling and solidification of the plastic, which in turn affects the shrinkage rate.
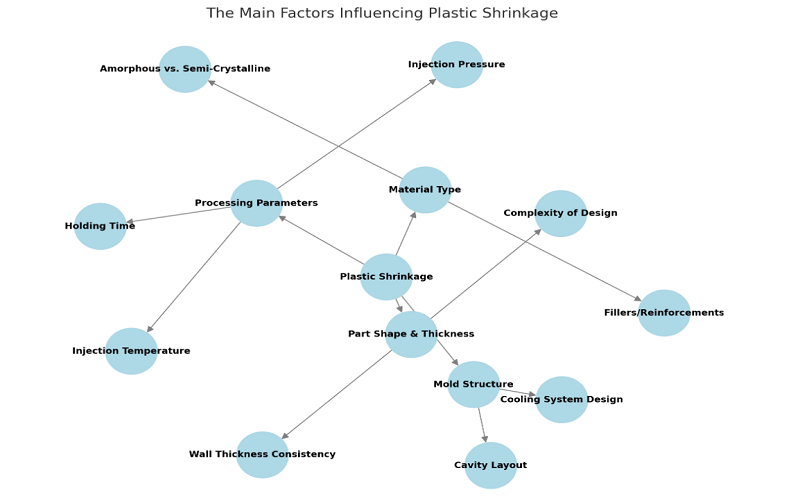
How Can Plastic Shrinkage Be Prevented?
In actual production, the following measures can be taken to better control the plastic shrinkage rate:
- Select appropriate plastic materials and understand their shrinkage characteristics.
- During the mold design phase, consider a well-designed cooling system to reduce plastic shrinkage through effective cooling.
- In the injection molding process, adjust the molding parameters according to the properties of the plastic and the mold design, carefully controlling temperature, pressure, and holding time.
- In plastic product design, ensure reasonable dimensions to avoid excessive size differences, which helps control the shrinkage rate.
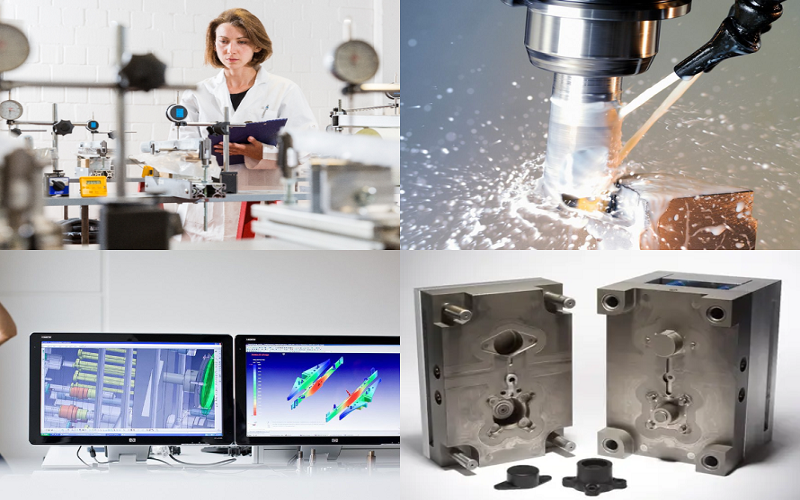
Conclusion
In summary, plastic shrinkage rate is a critical parameter in the production of plastic products, affecting their dimensional stability and surface quality.
To effectively control the shrinkage rate, it is essential to comprehensively consider factors such as material selection, mold design, and injection molding process parameters, making appropriate adjustments to ensure the quality and dimensional requirements of plastic products.