In today’s fast-paced manufacturing world, efficiency and precision are paramount. One technology that has revolutionized production is rapid injection molding.
This innovative method blends the speed of prototyping with the scalability of mass production, offering manufacturers a competitive edge.
As industries push for faster turnarounds without compromising on quality, rapid injection molding becomes a go-to solution. Its relevance spans across multiple sectors, helping businesses meet tight deadlines while maintaining the high standards required for complex products.
In a recent exploration by 3ERP, the numerous advantages of rapid injection molding are meticulously examined, highlighting its transformative impact on manufacturing processes.
This innovative approach not only accelerates production timelines but also significantly reduces costs, offering a competitive edge in today’s fast-paced market.
By integrating rapid injection molding, companies can achieve enhanced precision and scalability, ensuring high-quality outputs with shorter lead times.
This method stands out as a pivotal solution for industries aiming to optimize their production cycles and respond swiftly to market demands.
What is Rapid Injection Molding?
Rapid injection molding is an accelerated version of traditional injection molding, designed for quick production of plastic parts using pre-engineered molds.
Unlike conventional methods, this process focuses on reducing tooling time while maintaining the precision of the final product.
Typically, this method is employed during the prototyping phase or for producing small to medium production runs.
Key Components Involved in Rapid Injection Molding:
- Mold Base:Provides the foundation for creating the part, holding the mold cavity in place.
- Core and Cavity Inserts:The custom-designed elements that shape the injected material into the desired form.
- Injection System:Ensures proper injection of molten material into the mold.
- Cooling Channels:Speeds up the cooling process, vital for rapid cycle times.
- Ejector System:Removes the final part from the mold after it cools and solidifies.
How Does Rapid Injection Molding Work?
The rapid injection molding process follows a structured series of steps, ensuring speed and accuracy from design to production.
- Step-by-Step Guide on the Rapid Injection Molding Process:
- Design and Prototyping:A 3D model of the desired part is created using CAD software.
- Mold Creation:The mold is designed and produced using high-speed machining or 3D printing techniques.
- Material Injection:Molten plastic is injected into the mold at high pressure, filling the cavity.
- Cooling:The part is rapidly cooled using integrated cooling channels to maintain a fast cycle time.
- Ejection:Once the part solidifies, the mold opens and ejects the finished piece.
- Post-Processing:Additional steps, such as trimming or surface finishing, may be performed based on product requirements.
What Technologies Are Utilized in Rapid Injection Molding?
Several advanced technologies support the rapid nature of this injection molding process, enabling manufacturers to create highly accurate parts in a fraction of the time required by traditional methods.
One of the most critical innovations in this space is 3D printing for mold creation.
Using materials like high-strength resin or metal, manufacturers can quickly prototype mold components.
This technology enables cost-effective and rapid design iterations, making it ideal for short production runs.
Additionally, high-speed CNC machining plays a pivotal role in creating mold inserts with precise tolerances, ensuring that every part meets strict quality standards.
Why Choose Rapid Injection Molding?
Rapid injection molding offers a variety of benefits, making it an appealing choice for manufacturers. The core advantages revolve around speed, precision, and the ability to produce high-quality parts in shorter lead times compared to traditional injection molding.
One of the standout reasons to choose rapid injection molding is its flexibility. This process enables companies to experiment with different materials, design iterations, and product variations quickly, allowing for faster adjustments and improvements without the lengthy setup times of traditional methods.
How Does Speed Influence Production Cycles in Rapid Injection Molding?
Speed is one of the key differentiators of rapid injection molding, and it directly impacts production cycles. Compared to traditional injection molding, which can take weeks or even months to create a mold, rapid injection molding significantly reduces lead time.
Depending on the complexity of the part and the process used, molds can be designed and produced in as little as a few days.
- Speed Benefits of Rapid Injection Molding:
- Reduced Lead Times:Quick mold production allows for faster product launches.
- Faster Iterations:Adjustments to designs can be made swiftly, enabling rapid prototyping.
- Shorter Cycle Times:Each production cycle is faster due to the precision engineering of molds and efficient cooling systems.
This speed advantage is especially beneficial for industries that demand fast turnaround times, such as consumer goods and electronics, where product lifecycles are shorter, and time-to-market is crucial.
How Does Precision Impact the Quality of Products in Rapid Injection Molding?
Precision is a hallmark of rapid injection molding. With advanced technologies like high-speed machining and 3D printing, manufacturers can achieve tight tolerances and complex geometries that would be difficult or time-consuming with other methods.
The precision of the molding process directly influences the quality and consistency of the final products.
By using exact mold designs and accurate material injection, rapid injection molding minimizes defects, ensuring that each piece meets the required specifications.
This precision also leads to better product performance, especially in applications where detailed features or intricate designs are essential.
What Are the Main Benefits of Rapid Injection Molding?
Rapid injection molding offers a range of advantages that make it an attractive option for both prototyping and short-run production.
- Cost-Effectiveness:Rapid injection molding reduces the costs associated with traditional mold production. With quicker lead times, less material waste, and fewer iterations, manufacturers can save significantly on initial costs.
- Enhanced Material Properties:The precision of rapid injection molding allows for optimized material properties, ensuring that each part performs as expected.
- Customization Options:This process enables rapid design iterations, making it easier to produce customized or complex parts.
- Reduced Waste:Efficient mold design and accurate material injection help minimize material waste, contributing to more sustainable production practices.
Which Industries Benefit Most from Rapid Injection Molding?
Many industries have adopted rapid injection molding due to its speed, precision, and flexibility. These sectors require quick turnarounds and high-quality products to remain competitive in the market.
- Automotive Industry:Rapid injection molding is used for creating components like dashboards, interior panels, and small mechanical parts.
- Healthcare Industry:The process is ideal for producing medical devices, surgical tools, and diagnostic equipment where precision is critical.
- Consumer Goods:From electronics to home appliances, rapid injection molding is employed to manufacture custom parts with short production cycles.
- Specific Applications in Each Industry:
- Automotive:Prototyping and producing small mechanical components for faster vehicle development.
- Healthcare:Quick production of surgical instruments and custom medical devices.
- Consumer Goods:Creating parts for electronics, gadgets, and everyday products.
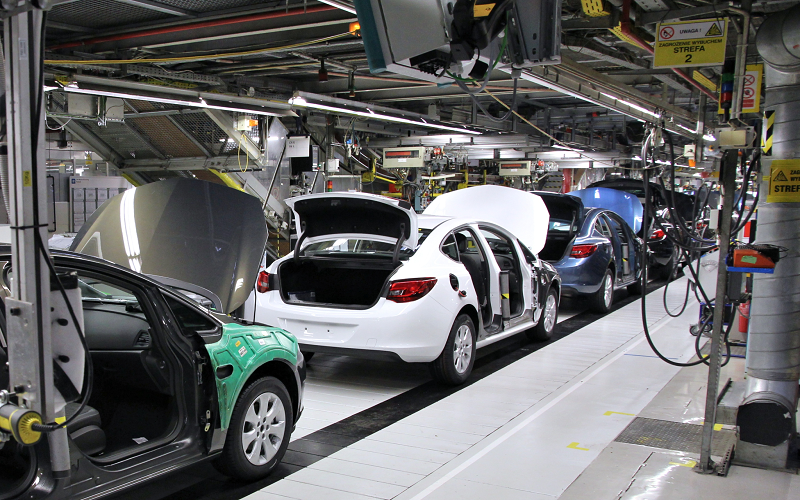
Key Considerations When Implementing Rapid Injection Molding
Before adopting rapid injection molding, manufacturers should consider several factors that can impact the success of the process.
- Design Requirements:Ensure that the part design is optimized for the rapid injection molding process, considering factors like wall thickness and gate placement.
- Material Selection:Different materials may perform better depending on the part’s requirements, so it’s essential to choose the right plastic or resin.
- Production Volume:Rapid injection molding is ideal for small to medium production runs. Manufacturers should evaluate whether the process aligns with their production needs.
- Factors to Consider:
- Design Complexity:The more intricate the design, the more care needed in mold production.
- Material Compatibility:Certain plastics may offer better durability or flexibility, depending on the application.
- Cost Implications:While cost-effective, manufacturers should still assess whether rapid injection molding aligns with their budget.
What Design Aspects Are Crucial for Rapid Injection Molding?
Design is a critical aspect of the rapid injection molding process, as optimizing the design can improve efficiency and product quality.
- Key Design Tips:
- Wall Thickness Considerations:Maintain uniform wall thickness to prevent warping or weak points in the final product.
- Gate Placement:Proper gate placement ensures even distribution of material during injection, reducing the likelihood of defects.
What Materials Are Best Suited for Rapid Injection Molding?
Choosing the right material is essential for achieving the best results in rapid injection molding. Different materials offer unique properties, making them more suitable for specific applications.
- Advantages of Common Plastics Used:
- ABS (Acrylonitrile Butadiene Styrene):Excellent impact resistance and toughness.
- Polycarbonate (PC):High transparency and durability.
- Nylon (Polyamide):Strong and resistant to wear, ideal for mechanical parts.
How to Optimize the Rapid Injection Molding Process?
Optimization is key to ensuring both efficiency and quality in the rapid injection molding process. By fine-tuning various aspects of the procedure, manufacturers can maximize their return on investment while producing high-quality parts.
- Steps to Ensure Efficiency and Quality in Rapid Injection Molding:
- Mold Design Optimization:The mold design should be carefully planned to ensure consistent and reliable production. Using computer-aided design (CAD) software can help in refining features like gate placement and cooling channels to reduce cycle times.
- Prototype Testing:Before full-scale production, manufacturers should test the prototype to detect any flaws or potential improvements. This helps minimize costly mistakes during mass production.
- Feedback Incorporation:After testing, any feedback or adjustments should be promptly applied. Whether it’s refining the mold, adjusting material properties, or improving design elements, timely feedback integration enhances the final product.
What Are Common Challenges in Rapid Injection Molding?
Despite its many advantages, rapid injection molding comes with its own set of challenges. Being aware of these issues can help manufacturers avoid pitfalls and streamline the process.
- Common Challenges and Solutions:
- Mold Durability:Since molds are created more quickly, they may wear out faster than those made for traditional injection molding. Using high-strength materials for mold creation and ensuring proper maintenance can mitigate this issue.
- Material Shrinkage:During the cooling process, certain materials may shrink more than expected, leading to inaccuracies in the final product. Ensuring that mold designs account for potential shrinkage can help improve precision.
- Complex Designs:Intricate part designs can be more difficult to produce through rapid injection molding. In such cases, simplifying the design or using advanced technologies like 3D printing for mold creation may be necessary.
Future Trends in Rapid Injection Molding
As technology continues to evolve, rapid injection molding is expected to become even more efficient and versatile. Several advancements in materials, processes, and machinery are on the horizon, promising to further revolutionize the industry.
- Upcoming Advancements and Innovations:
- Improved Materials:Research into new plastics and resins will likely lead to more durable and flexible materials, expanding the applications of rapid injection molding.
- Automation:Increased automation in mold creation and production processes will help speed up production cycles and reduce human error.
- Sustainability:There is a growing focus on reducing waste and using eco-friendly materials in manufacturing. Rapid injection molding is expected to benefit from innovations in recyclable materials and energy-efficient machinery.
Comparing Rapid Injection Molding with Other Manufacturing Processes
Rapid injection molding is not the only manufacturing method available, and it is essential to understand how it compares with other popular techniques, such as CNC machining and traditional injection molding.
- Rapid Injection Molding vs. CNC Machining:While CNC machining excels at creating highly precise metal parts, rapid injection molding offers faster production times for plastic components. For manufacturers needing plastic parts in bulk, rapid injection molding is typically more cost-effective.
- Rapid Injection Molding vs. Traditional Injection Molding:Traditional injection molding is ideal for large-scale production but requires significantly longer lead times for mold creation. In contrast, rapid injection molding is best suited for prototyping and short production runs where speed is critical.
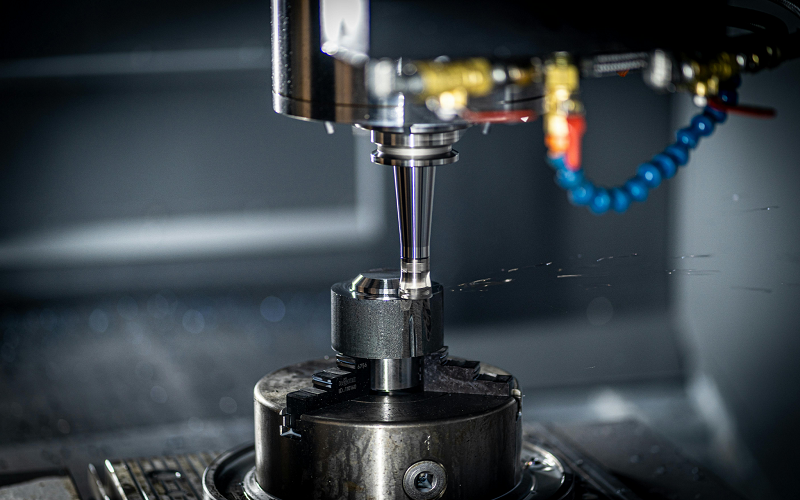
When to Choose Rapid Injection Molding Over Other Techniques?
The decision to choose rapid injection molding over other manufacturing methods depends largely on the specific needs of the project.
- Criteria for Selecting Rapid Injection Molding:
- Short Production Runs:When only a limited number of parts are required, rapid injection molding is more cost-effective and faster than traditional methods.
- Quick Iterations:Rapid injection molding allows for faster design changes and prototyping, making it ideal for projects requiring multiple iterations.
- Complex Plastic Parts:If the project involves producing complex plastic components with tight tolerances, rapid injection molding is often the best choice.
Conclusion
Rapid injection molding has carved a significant niche in modern manufacturing, offering unmatched speed and precision.
Its ability to quickly produce high-quality parts, especially for prototypes and small production runs, makes it an invaluable tool for industries like automotive, healthcare, and consumer goods.
As advancements continue to push the boundaries of this technology, manufacturers can expect even greater efficiencies, better materials, and more sustainable processes in the future.
By understanding when and how to implement rapid injection molding, businesses can stay competitive and meet the ever-evolving demands of their industries.