In the thin-wall molding process, thin wall molds serve as a crucial element, essential for the manufacturing of thin-wall products, typically referring to molds with a wall thickness of less than 1mm.
As the application range of thin wall products continues to expand, the design and manufacturing of thin-wall molds have become a key focus for engineers.
This article will provide a comprehensive exploration of the fundamental aspects of thin wall mold design and manufacturing, helping readers gain a thorough understanding of thin-wall mold technology.
What Is Thin Wall Mould?
Thin wall moulds refer to molds with a wall thickness of less than 1mm, specifically designed for producing thin wall structural components or products.
Due to their high precision and efficiency, thin wall molds enable high-speed and high-accuracy production.
They are suitable for manufacturing plastic containers, shells, caps, cups, plates, and other flat or three-dimensional thin wall structures.
Compared to standard molds, thin wall molds typically have more complex structures and impose stricter requirements on processing technology and equipment.
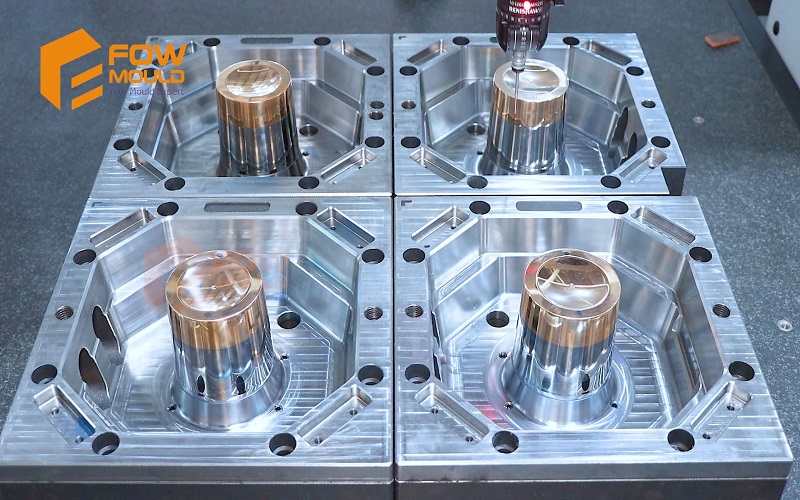
Why Choose Thin Wall Molds?
Thin-wall molds, with their high precision, complexity, and efficiency, can effectively reduce material waste, improve production efficiency, and lower production costs during the manufacturing process.
Compared to traditional metal cutting methods, thin-wall molds allow for more precise control over the dimensions and shapes of parts, avoiding unnecessary material consumption.
Additionally, the design and manufacture of thin-wall molds are meticulously optimized, enabling the rapid and efficient production of required parts.
This not only shortens the production cycle but also enhances production efficiency, resulting in significant cost savings for companies over the long term.
Finally, products produced with thin-wall molds exhibit better dimensional accuracy and surface quality, thereby improving the overall quality of the products.
Therefore, the numerous advantages of thin-wall molds make them an ideal choice for injection molding companies.
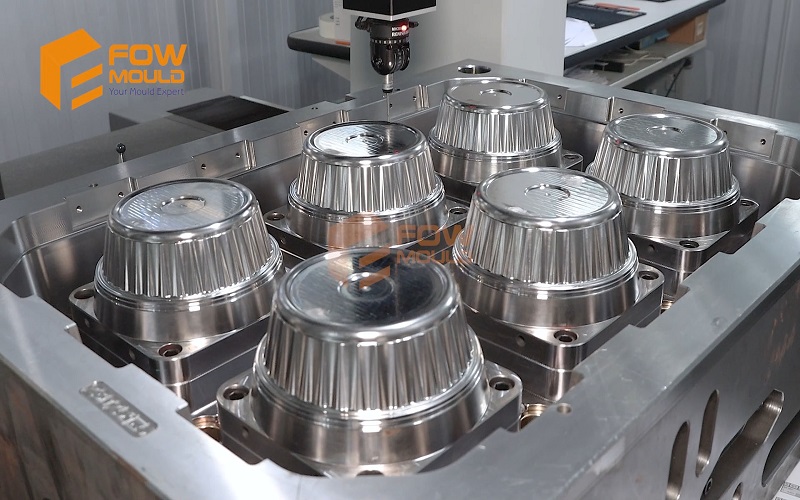
Which Materials Can Make Thin-walled Molds?
Due to the specific materials required in the manufacturing process of thin wall molds, it is essential to consider the hardness, wear resistance, and good machinability of the chosen steel.
Here are some types of steel suitable for thin wall molds:
- P20 Steel
P20 steel is a chromium-nickel alloy steel known for its excellent machinability and structural stability.
It also has high hardness and strength, making it an ideal choice for manufacturing thin wall molds.
- S136 Steel
S136 steel is a type of stainless steel with extremely high corrosion resistance.
In the production of thin-wall molds, it effectively prevents surface corrosion of the components, ensuring the longevity and quality of the mold.
- NAK80 Steel
NAK80 steel is a type of tungsten steel that boasts excellent wear resistance and cutting performance.
It is frequently used for making high-precision molds, meeting the requirements for high accuracy and long service life of thin wall molds.
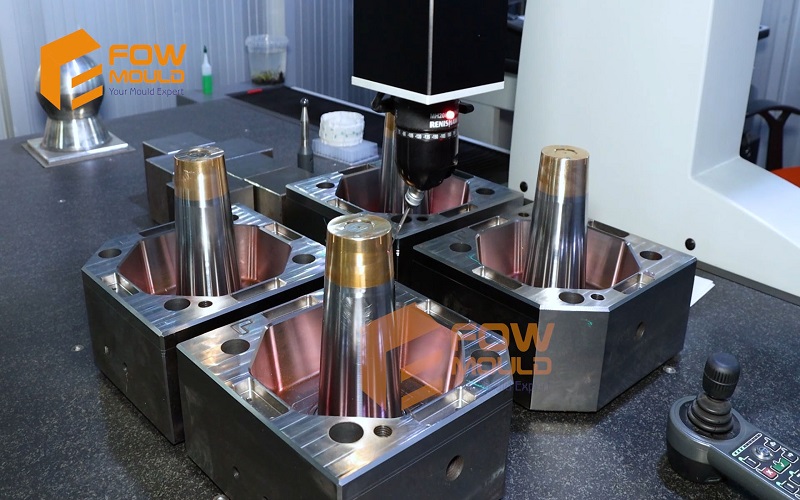
Manufacturing Process Of Thin Wall Mould
The manufacturing process of thin-wall molds involves several key steps and technical requirements to ensure the molds are efficient, precise, and durable.
Here are the main steps involved in the manufacturing process of thin-wall molds:
Design Analysis
Use CAD software to design the mold according to product requirements, including the mold’s structural design, dimensional accuracy, and surface quality.
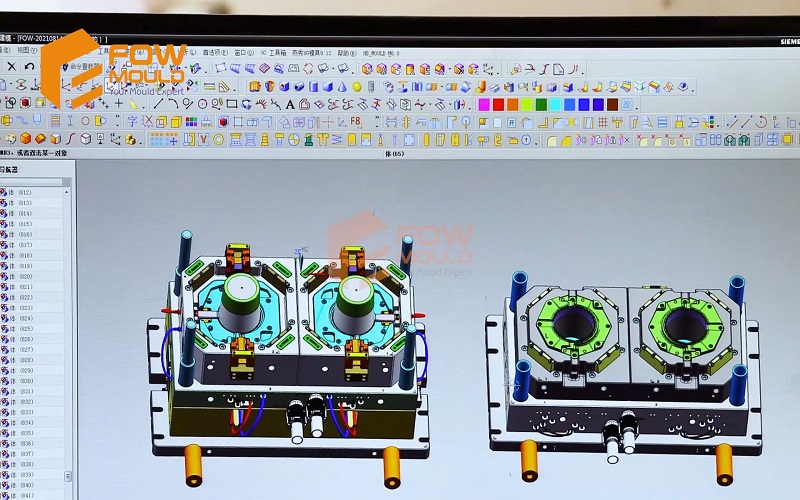
Machining
First, use milling machines, lathes, and other equipment for initial machining to remove excess material.
Then, use CNC machines for precision machining to ensure the mold’s dimensional accuracy and surface quality.
To improve the hardness and wear resistance of the mold, perform quenching and tempering treatments on the mold steel.
If further precision is required, use EDM for complex structures and fine details.
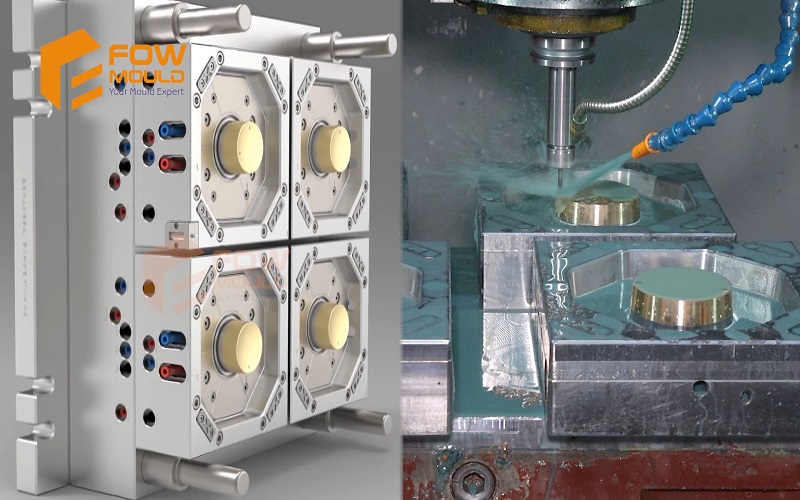
Surface Treatment
Polish, sandblast, or apply coatings to the mold to enhance its surface smoothness and corrosion resistance.
Assembly and Debugging
Assemble the processed components in sequence, and conduct a trial mold on the injection molding machine.
Check the mold’s performance, adjust mold parameters, and ensure the mold operates normally.
Quality Inspection
Conduct comprehensive quality inspections through dimensional and structural testing to ensure the mold meets design requirements and is free from design defects and safety hazards.
Design Principles For Thin Wall Molds
Mold design is a critical step in the production process of injection-molded thin wall products.
Below are the key principles for designing thin-wall molds:
Wall Thickness
Control of wall thickness is very stringent for thin-wall molds. Ideally, the wall thickness should be between 0.5mm and 1.0mm.
Mold Structure
The mold adopts an I-beam structure, with the cavity and core made of P20 or 2738 steel.
The sliders, guide slots, and inserts are made of 2316 or 718 steel.
The guide pins, guide bushings, sprue bushing, ejector pins, and return pins use SKD standard components.
The mold base utilizes a custom-made standard mold base.
Gating System
For plastics with good flow properties (e.g., PP), point gates can be used for the gating system design.
For plastics with moderate flow properties (e.g., ABS, acetal), gates should be designed in thicker areas of the part to allow the injection process to transition from thicker to thinner sections, reducing sink marks and warping.
Utilizing thin multi-gate or submarine gate designs can directly fill the cavity, reducing plastic pressure loss.
Additionally, hot runner technology can lower melt viscosity, achieving rapid filling.
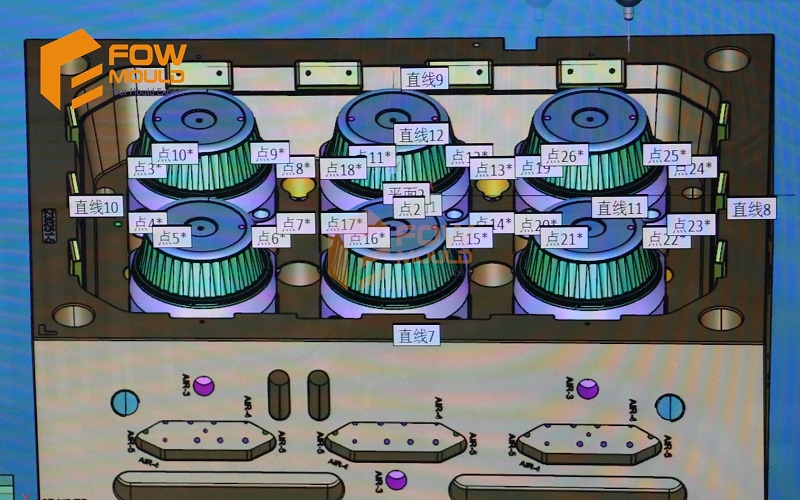
Cooling System
The design of the cooling system in thin-wall molds is extremely important.
To ensure the dimensional stability of thin-wall products, non-loop cooling lines can be used within the core and cavity modules to increase cooling length and enhance cooling effectiveness.
In necessary areas, high thermal conductivity metal inserts can be added to accelerate heat transfer.
Venting System
Thin-wall injection molds generally require excellent venting, preferably with vacuum capabilities.
Gases are typically vented through the core, ejector pins, ribs, studs, and parting lines.
The ends of the flow channels should also be adequately vented to prevent gas traps and burns.
Demolding Mechanism
Due to the thin walls of the parts and the presence of features like bosses and ribs, there may be deformation or damage during demolding.
Parts shrink less along the thickness direction, but high packing pressure reduces this shrinkage further. Ribs can cause sticking.
To avoid sticking and ejector marks, it is recommended to use more and larger ejector pins for part ejection.
Common Problems And Solutions For Thin Wall Mould
Due to factors such as mold design, material selection, and molding processes, many issues can arise in the production of thin-wall molds.
However, these problems can be effectively resolved through a series of improvement measures.
Issue | Cause | Solution |
Short Shots | Inadequate mold machining or poor venting | Correct the mold, improve venting measures |
Shrinkage | Uneven cooling or solidification shrinkage | Thicken the runners, increase injection pressure, extend hold time |
Flash | Poor mold closing or improper mold surface machining | Correct the mold, increase clamping force, adjust molding parameters |
Surface Marks | Stress marks caused by high core or ejector pin design | Reduce injection speed, decrease injection pressure |
Whitening (Stress Whitening) | Poor force distribution during ejection | Increase R angle at corners, increase draft angle, add or enlarge ejector pins |
Conclusion
In conclusion, thin wall molds play a crucial role in achieving high-quality and cost-effective plastic production. They are indispensable for thin wall injection molding.
If you need to customize a thin-wall mold, please contact us. FOWMOULD will be your most reliable injection mold supplier!
Whether it’s thin-wall plastic boxes, cups, or buckets, FOWMOULD can provide you with the most cost-effective manufacturing solutions, ensuring that your product quality and production efficiency are optimized.