Polypropylene (PP) and Nylon are two widely used synthetic materials, each with unique properties and advantages. PP is known for being lightweight, while Nylon is renowned for its abrasion resistance.
Both nylon and polypropylene are considered inexpensive materials, but polypropylene is significantly cheaper than nylon. Choosing the right material for a final product involves understanding these distinct characteristics.
Let us delve into the properties of Nylon and PP, and examine their performance in different applications, to make more informed and reasonable material choices for specific projects.
What is Nylon?
Nylon is a versatile synthetic polyamide thermoplastic synthesized through polymerization, involving diamines and dibasic acids or lactams, and belongs to the polyamide family, including PA6, PA66, and PA12. Their chemical equations are different, so their monomer structures, types of polymerization reactions, and by-products are different.
Known for its mechanical strength, elasticity, and chemical resistance, nylon is widely used in automotive components, textiles, consumer goods, electrical parts, and industrial machinery.
Nylon’s strong heat resistance makes it suitable for applications in industries requiring heat resistance, such as the medical and food and beverage industries.
Its adaptability is further enhanced by its ease of processing through injection molding, extrusion, and blow molding, as well as its ability to be blended with other materials, making it essential in modern manufacturing and product design.
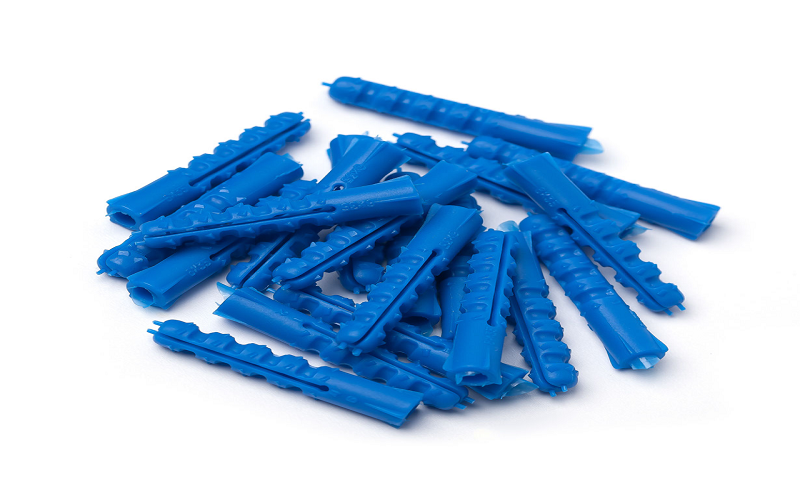
What is Polypropylene?
Polypropylene is a synthetic resin, a thermoplastic polymer produced by the polymerization of propylene monomers, which are usually opaque. It is a type of saturated polymer with specific chemical characteristics.
The chemical formula of polypropylene is (C3H6)n.
There are several types of polypropylene: homopolymerized polypropylene, block copolymerized polypropylene and random copolymerized polypropylene.
This substance has a variety of characteristics, such as its low density, which makes it one of the lightest general-purpose plastics, and its high chemical, heat, and impact resistance.
It is widely used in various industries due to its comprehensive performance and cost-effectiveness.
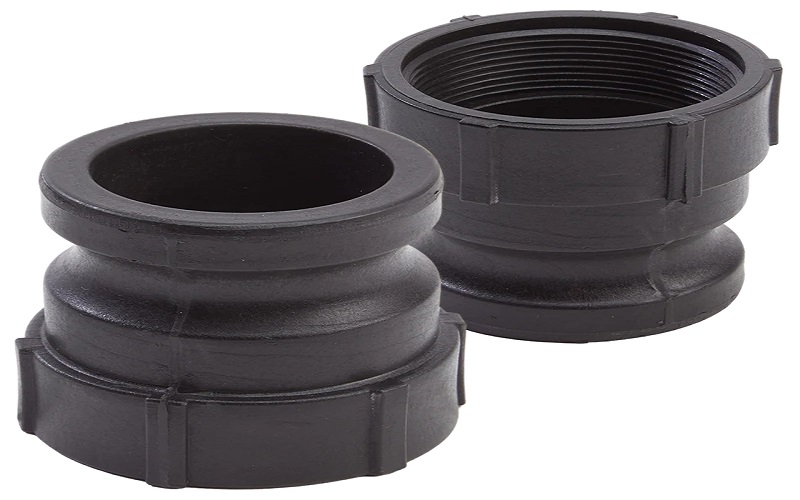
Basic Properties Comparison of Nylon and PP
Nylon (Nylon) and polypropylene (PP) are two common thermoplastics used in a wide variety of industrial and consumer applications.
Each of these two materials has its own distinctive characteristics and demonstrates unique advantages in different applications.
When comparing the properties and uses of both polypropylene and nylon, it becomes evident that each material is suitable for specific purposes due to their unique properties.
Property | Nylon | Polypropylene (PP) |
Density | 1.14 – 1.15 g/cm³ | 0.90 – 0.91 g/cm³ |
Tensile Strength | 75 – 90 MPa | 30 – 40 MPa |
Elongation at Break | 20 – 30% | 200 – 600% |
Elastic Modulus | 2.5 – 3.2 GPa | 1.7 – 2.0 GPa |
Melting Point | 220 – 260°C | 160 – 170°C |
Heat Deflection Temperature | 180 – 220°C | 100 – 120°C |
Water Absorption | 1.0 – 1.5% (24 hours) | <0.01% (24 hours) |
Thermal Expansion Coefficient | 80 – 100 µm/m°C | 100 – 200 µm/m°C |
Coefficient of Friction | 0.25 – 0.30 | 0.35 – 0.45 |
Chemical Resistance | Good against bases, oils, and most organic solvents | Excellent against acids, bases, salts, and most organic solvents |
Electrical Insulation | Good, but decreases with moisture absorption | Excellent and unaffected by moisture |
Processability | Injection molding, extrusion, blow molding | Injection molding, extrusion, blow molding, thermoforming |
Advantages of Nylon vs Polypropylene
Nylon:
Nylon is a high-performance polymer known for robust mechanical strength, excellent abrasion resistance, and significant elongation, ideal for heavy-duty and dynamic parts. Its chemical resistance and self-lubricating properties enhance stability in harsh conditions.
Nylon offers heat resistance, fatigue resistance, and shock absorption, while being lightweight and easy to process. It provides good electrical insulation and moisture absorption, preventing static buildup.
Nylon’s versatility and durability suit applications in automotive, aerospace, textiles, consumer goods, and industrial machinery, from gears and bearings to electrical components and apparel, crucial in modern manufacturing and design.
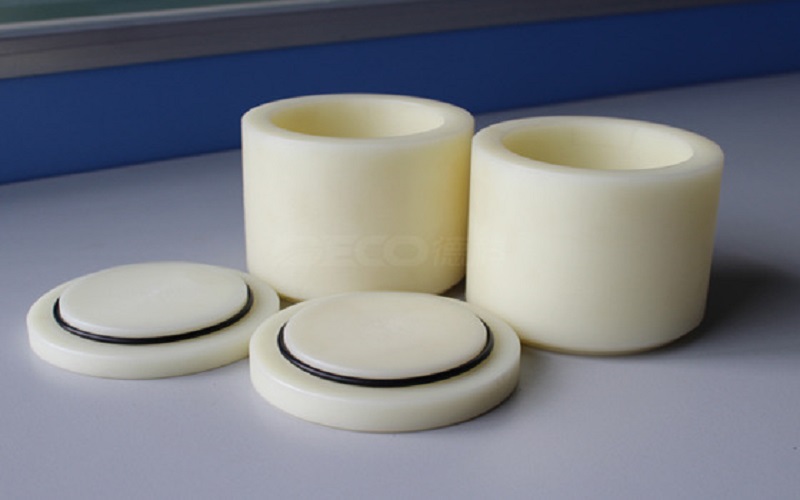
Polypropylene:
Polypropylene (PP) is a lightweight polymer prized for its chemical resistance and high impact strength, making it ideal for packaging and automotive parts.
Its flexibility, moisture resistance, and excellent performance under diverse conditions also extend to industrial applications. PP offers exceptional electrical insulation and heat resistance, crucial in various settings. Its UV-resistant properties in ropes highlight durability.
Easy processing and recyclability enhance cost-effectiveness and sustainability, making PP indispensable across industries from consumer goods to construction.
Its unique properties, including resistance to chemicals, make it suitable for heavy-duty applications like fishing lines and laboratory settings, distinguishing it from nylon.
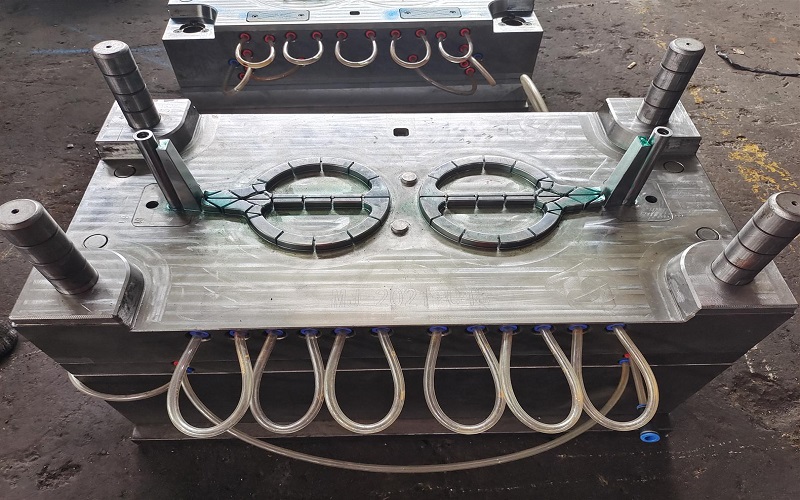
Polypropylene vs Nylon: Industrial and Household Applications
Due to their unique advantages and limitations, nylon and PP play a vital role in various industries. The main industrial and household applications include:
Applications of Nylon
Nylon is a particular synthetic polyamide thermoplastic known for its versatility and is used in various applications such as gloves, guitar strings, wheels, electric connectors, and medical devices.
Automotive industry: gears, bearings, fuel system components;
Electrical and electronic appliances: cable sheathing, connectors;
Textiles: nylon fibers, carpets;
Industrial equipment: conveyor belts, seals;
Consumer goods: kitchenware, sporting goods;
Construction materials: pipes, fasteners etc.
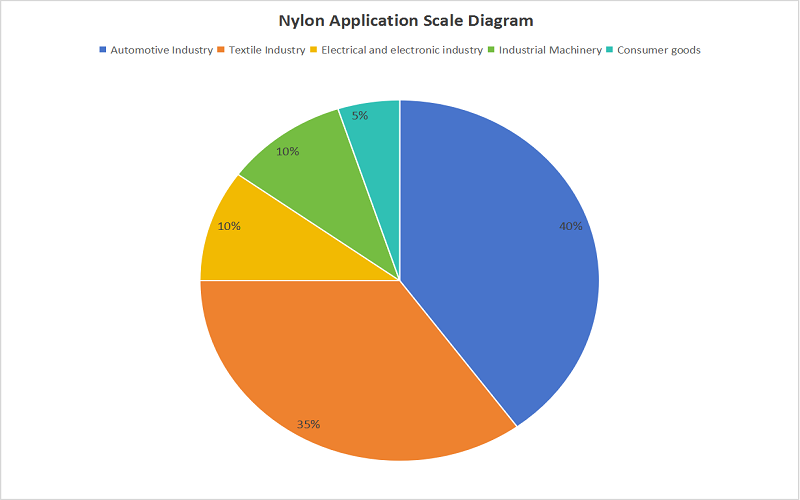
Applications of Polypropylene
Polypropylene is one of the synthetic polymers with advantageous properties and suitability for different applications in various industries.
Packaging: food packaging, containers;
Automotive industry:bumpers, interior parts;
Household appliances:housings components;
Electrical and electronic appliances: wire sheathing, insulation materials;
Building materials: pipes, floor tiles;
Consumer goods: furniture, toys;
Agriculture: greenhouse films, irrigation pipes etc.
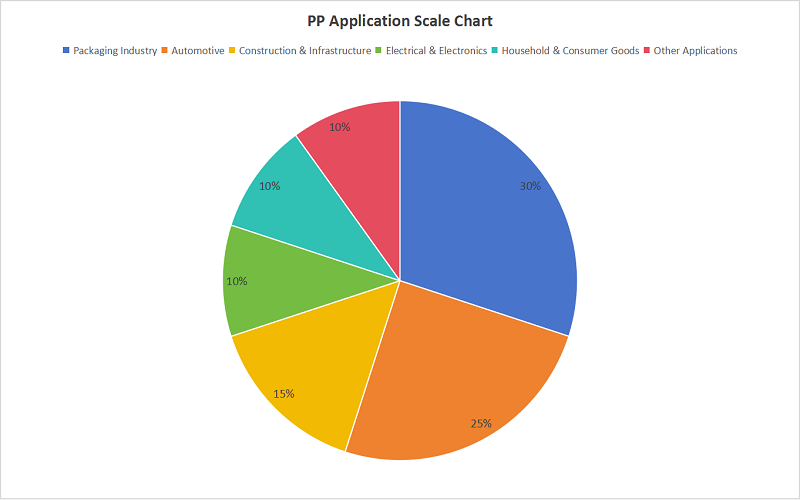
Nylon vs Polypropylene: Cost
Nylon:
Higher cost: Nylon is typically more expensive to produce than polypropylene due to the complexity of the manufacturing process and the high price of raw materials.
Performance value: Although more costly, nylon’s superior mechanical strength, he
at resistance and durability justify its cost in applications where these properties are needed.
Polypropylene (PP):
Lower cost: Cost-effective with lower production and material costs.
Cost-effective: easy to process, recyclable, low density reduces total cost of ownership and is well suited for large-scale and cost-sensitive applications.
In summary, nylon excels in high-performance applications despite its higher cost, while polypropylene offers significant cost advantages in applications with modest performance requirements.
The choice should find a balance between cost and performance needs.
Is Nylon a plastic or fabric?
Nylon, in both plastic (polyamide) and fabric forms, is widely used for its strength, durability, heat resistance and chemical stability in automotive parts, industrial components and consumer products.
In automotive applications, nylon plays a vital role in engine parts, fuel systems and electrical connectors, improving efficiency by reducing weight.
As a fabric, nylon fibers are lightweight, strong and abrasion-resistant, making them ideal for apparel, upholstery and outdoor items such as tents and backpacks.
Its quick-drying and mildew-resistant properties also make it useful in sports and outdoor activities. In home décor, nylon is commonly used in carpeting and upholstery fabrics for its durability and ease of maintenance.
All in all, nylon’s dual function as a plastic and a fabric underscores its importance in modern manufacturing and design, covering a wide range of key applications in automotive, industrial, fashion and home furnishings.
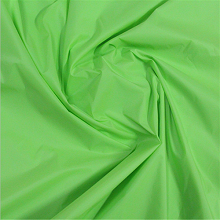
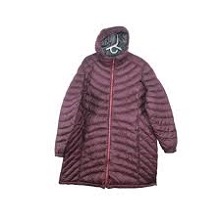
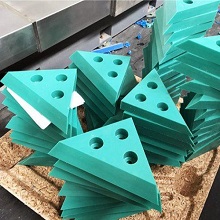
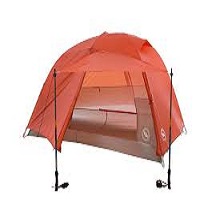
Is Polypropylene Better than Nylon ?
Each of these two materials has its own merits, and a simple comparison of which one is better cannot be achieved without considering the specific product requirements.
Nylon is ideal for applications needing high mechanical strength, abrasion resistance, heat resistance, and self-lubrication, such as automotive gears, machine parts, and high-strength fibers.
PP is better suited for applications requiring light weight, chemical resistance, low water absorption, and cost-effectiveness, like food packaging, chemical containers, household appliance housings, and medical packaging.
Typically, polypropylene is cheaper than nylon. Therefore, if you prefer a more cost-effective option, consider polypropylene. Polypropylene is suitable for products that do not require high strength or for outdoor applications.
Therefore, the selection of materials should be evaluated based on specific application scenarios and performance requirements in order to find the most suitable solution.
Conclusion
FOW Mould offers a comprehensive selection of materials, including but not limited to Nylon and Polypropylene, a partner for your diverse material needs.