In plastic manufacturing, people often equate Acetal with POM, as they are essentially different names for the same material. Acetal, with its low friction coefficient and high wear resistance, makes it an ideal choice for producing high-precision and durable components.
Therefore, mastering the injection molding process of Acetal can not only optimize production efficiency but also significantly enhance product quality.
Next, we will delve into the characteristics of Acetal and its applications in injection molding.
What Is Acetal?
Acetal, also known as polyacetal or polyoxymethylene (POM), is a semi-crystalline engineering thermoplastic.
Acetal polymers are long chains of CH2O molecules with some copolymer monomers added.
Based on the chemical structure of the molecular chain, they are classified into two types: homopolymer acetal and copolymer acetal.
Among them, DuPont™ Delrin® is the most well-known brand of homopolymer acetal.
Acetal plastics exhibit high mechanical strength and rigidity, good sliding properties (low friction coefficient), and excellent wear resistance.
Due to acetal’s minimal water absorption and outstanding dimensional stability, it is often used as a metal replacement material.
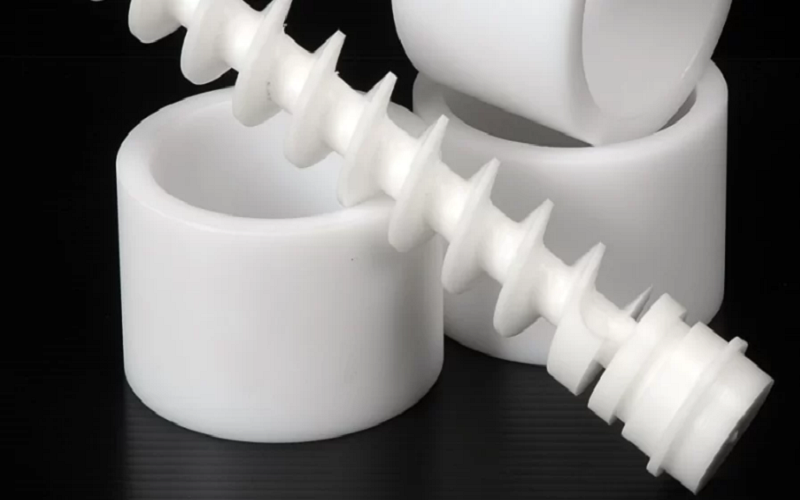
Properties of Acetal Material
Generally, Acetal polymers exhibit the following properties:
- High strength and rigidity
- Low moisture absorption
- Good impact strength
- Outstanding dimensional stability
- Excellent wear resistance and sliding properties
Table1 shows the performance data of Acetal materials:
Property | Homopolymer Acetal | Copolymer Acetal |
Density (g/cm³) | 1.41 | 1.42 |
Melting Point (℃) | 172-184 | 160-175 |
Hardness (Shore D) | 85 | 82 |
Tensile Strength (MPa) | 70 | 65 |
Modulus Of Elasticity(MPa) | 4623 | 3105 |
Coefficient of Friction | 0.35 | 0.3 |
Water Absorption (%) | 0.2 | 0.3 |
As one of the most versatile plastic materials, HDPE is widely used in packaging, piping, consumer goods, agriculture, construction, and electrical insulation due to its excellent chemical resistance and flexibility.
FDA, NSF, and USDA-approved food-grade HDPE plastic is the ideal material for various food and beverage containers.
Advantages of Acetal Injection Molding
To fully leverage the superior properties of acetal material, injection molding companies often utilize the acetal injection molding process for material processing.
Here are the notable advantages of acetal injection molding:
High Strength and Rigidity
Products made from injection-molded acetal exhibit high strength and rigidity, capable of withstanding high loads and stresses, making them suitable for manufacturing high-strength mechanical components.
Excellent Resistance
Acetal copolymer can withstand organic, inorganic solvents, and acids, maintaining stable performance over a wide temperature range, making it suitable for various industrial applications.
Outstanding Dimensional Stability
Due to its low moisture absorption, acetal injection-molded products can maintain dimensional stability under different environmental conditions and are less prone to deformation.
Low Friction and High Wear Resistance
Acetal features a low friction coefficient and excellent wear resistance, making it ideal for producing sliding and friction components, such as gears, bearings, and sliders.
High Surface Smoothness
Injection-molded acetal products have smooth, fine surfaces and do not require additional surface treatment.
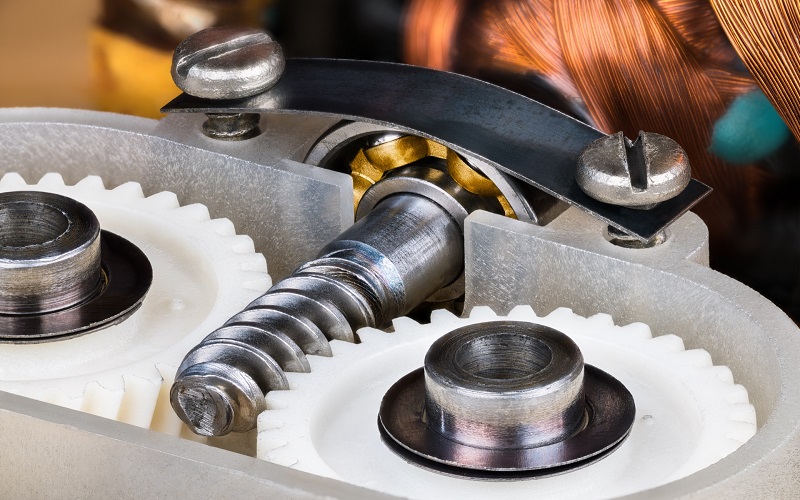
Disadvantages of Acetal Injection Molding
In addition to the numerous advantages, acetal injection molding also has some drawbacks and challenges.
Poor Weather Resistance
Acetal is prone to degradation under UV exposure, leading to color changes and performance deterioration.
Stabilizers are usually added to enhance its weather resistance.
Brittleness
Although acetal has high strength and rigidity, it can become quite brittle at low temperatures or when subjected to impact, which may cause the products to crack.
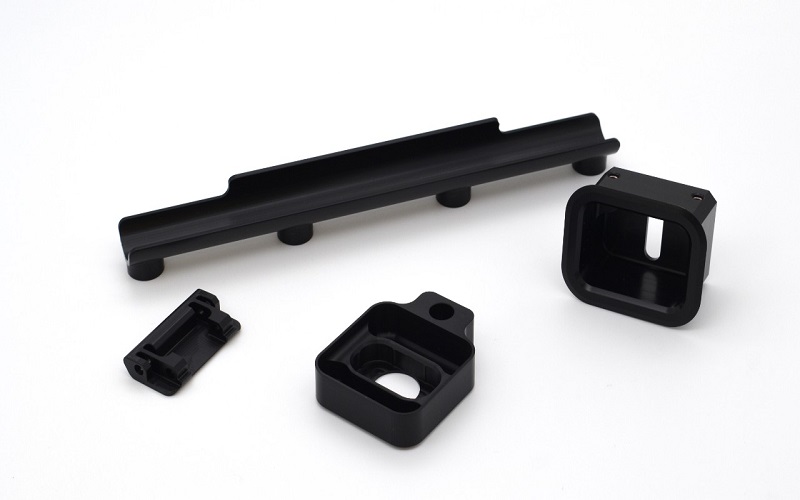
Considerations In Acetal Molding Process
When working with acetal in the injection molding process, several key factors need to be considered to ensure high-quality and reliable products.
Here are some important considerations will ensure successful molding and desired results:
Acetal Injection Mold Design
- Runner Diameter: Should be 3 -6 mm.
- Gate Length: Should be 0.5 mm.
- Round Gate Diameter: Should be at least 0.5 -6 times the product thickness.
- Rectangular Gate Width: Typically twice the thickness or more, with a depth of 0.6 times the wall thickness.
- Draft Angle: Should be between 40′-1°30′.
Pre-Drying Acetal Material
Although acetal material has low moisture absorption, it is recommended to pre-dry the acetal resin at 80°C to 100°C (176°F to 212°F) for 2 to 4 hours to ensure adequate drying.
Molding Temperature Control
Generally, the mold temperature should be controlled between 75°C and 120°C, and the melt temperature should be between 190°C and 230°C (374°F to 446°F).
Injection Pressure
The injection pressure mainly depends on the melt flow characteristics of acetal (POM), the thickness and width of the runner and gate, and the thickness of the plastic product. Typically, it ranges from 40 to 130 MPa.
Injection Molding Speed
The common practice is to use a moderately fast injection speed. A slower speed can cause flow marks, while a faster speed can cause jetting and shear overheating.
By optimizing these parameters, the quality and efficiency of Acetal injection molding can be significantly improved.
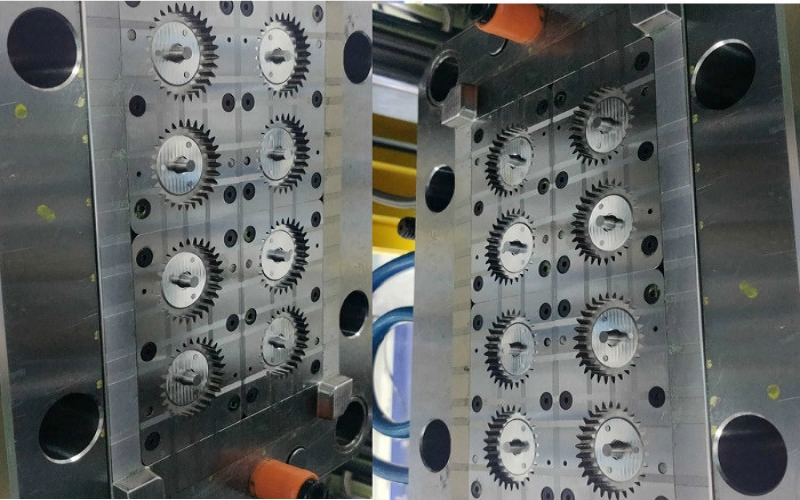
Applications of Injection Molded Acetal Parts
Typical applications for injection-molded Acetal include:
- Gears
- Bearings
- Bushings
- Rollers
- Pump and valve components
- Electrical insulators and connectors
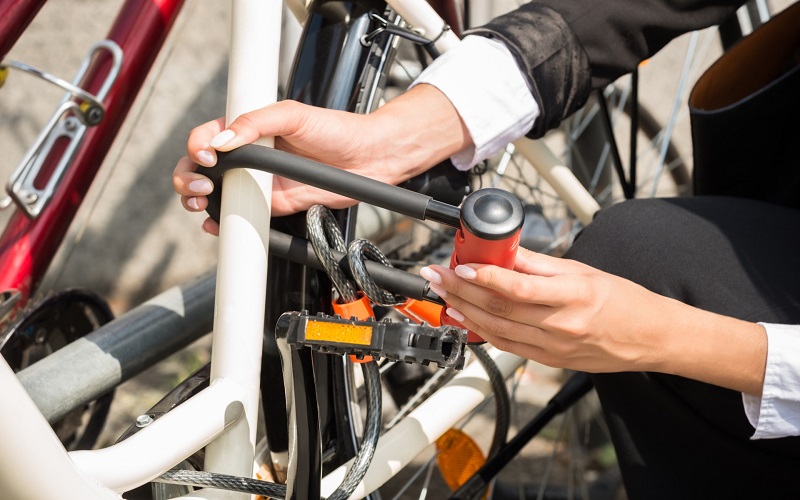
Custom Acetal(POM)Injection Molding Services
As a leading injection molding company in China, FOWMOULD is dedicated to providing customers with one-stop services from product design, mold manufacturing, to plastic molding.
We have assembled a professional manufacturing design team with extensive experience and established a physical manufacturing plant equipped with the latest injection molding equipment, offering cost-effective Acetal injection molding products.
If you want to learn about the feasibility of projects involving Acetal (POM), Delrin, or other plastics, contact us immediately for a free quote.
Conclusion
Injection-molded Acetal (polyoxymethylene) is typically a semi-crystalline thermoplastic that can be used for mechanical components such as bushings, bearings, gears, and sprockets.
Compared to metals and other plastics, Acetal’s low friction coefficient, stiffness, and excellent wear performance contribute to the durability and longevity of the products.
If you are considering using Acetal material in your project, do not hesitate to contact FOWMOULD for a free quote!