In the plastic manufacturing industry, injection molding manufacturers often face the dilemma of “HDPE vs Delrin”, making it crucial to understand the differences between these two materials.
HDPE, a type of polyethylene, is a thermoplastic known for its high rigidity and high impact strength, commonly used for making bottles, pipes, and food storage containers.
Delrin is the brand name for acetal homopolymer, a highly crystalline engineering thermoplastic that offers excellent dimensional stability and low friction, making it suitable for high-load and high-impact applications such as mechanical gears and electrical insulators.
This article will delve into the differences between HDPE and Delrin, examining their performance, applications, and costs to better determine which material is best suited for specific needs.
What Is HDPE?
HDPE (High-Density Polyethylene) is a highly crystalline, non-polar thermoplastic polyolefin, produced through the copolymerization of ethylene.
It is lighter than water, flexible, and tough. HDPE has higher hardness, tensile strength, and creep resistance compared to Low-Density Polyethylene (LDPE), and it also boasts good wear resistance, electrical insulation, toughness, and cold resistance.
Its chemical stability is excellent, being insoluble in any organic solvent at room temperature, and resistant to acids, alkalis, and various salts.
However, HDPE has poor aging resistance and inferior environmental stress cracking resistance compared to LDPE, particularly under thermal oxidation which can degrade its performance.
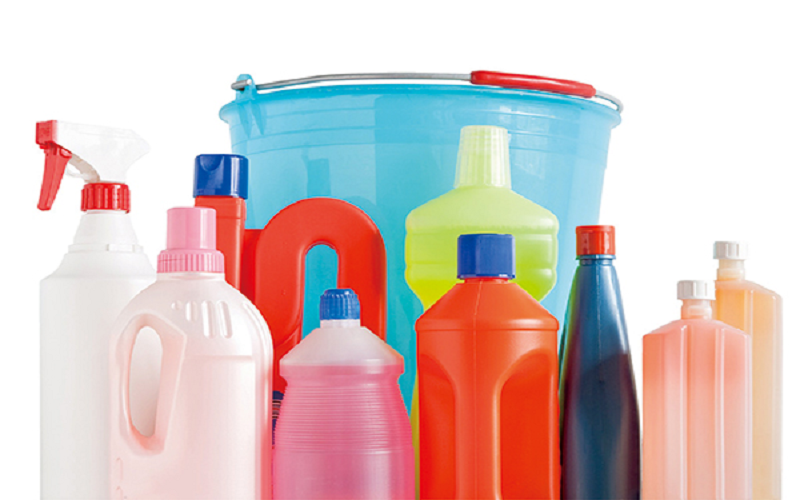
What Is Delrin?
Delrin is the brand name for DuPont’s polyoxymethylene (POM) product, which is a homopolymer.
It features high strength and rigidity, dimensional stability, low friction, and ease of machining, making it ideal for high-load mechanical applications such as gears and automotive door lock systems.
Compared to copolymer acetal, Delrin has a melting point that is approximately 10°C higher and a higher heat deflection temperature.
However, it is less resistant to hot water, alkalis, and weathering than copolymer acetal.
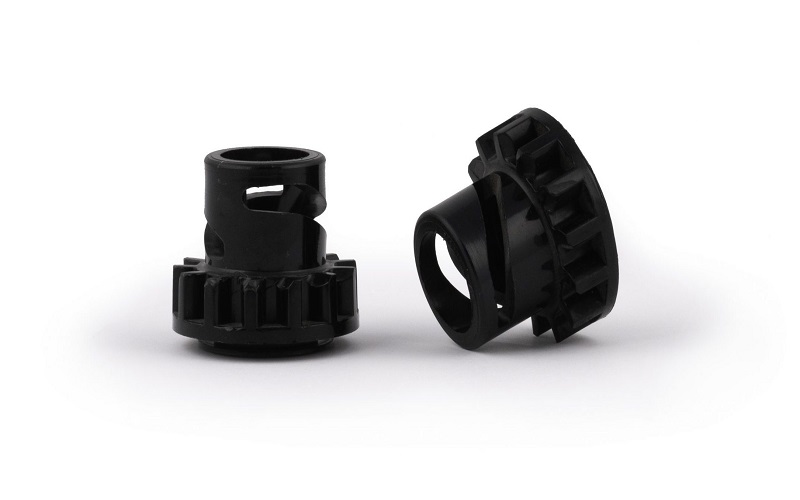
HDPE vs Delrin: Properties
HDPE is notable for its high toughness and impact resistance, along with excellent electrical insulation and chemical stability, and low water absorption. However, it has poor aging resistance.
In contrast, Delrin is known for its high strength and low friction coefficient, with exceptional wear resistance and dimensional stability, although its resistance to hot water, alkalis, and weathering is inferior to that of HDPE.
Here’s a detailed comparison table of the properties of HDPE and Delrin :
Properties | HDPE | Delrin |
Density(g/cm3) | 0.941~0.960 | 1.41 |
Melting Point(℃) | 142 | 175 |
Tensile Strength(MPa) | 20-28 | 60-70 |
Water Absorption(%) | <0.01 | 0.2-0.5 |
Shrinkage(%) | 1-3 | 1.8-2.1 |
Impact Strength (J/m) | 20-30 | 50-70 |
Heat Deflection Temp (℃) | 50-75 | 110-130 |
HDPE vs Delrin: Processing Methods
Due to the different properties of HDPE and Delrin, the manufacturing processes suitable for them also differ.
HDPE is suitable for injection molding, extrusion molding, blow molding, and rotational molding.
Among these, HDPE injection molding is particularly well-suited for mass production applications, enabling the creation of various shapes and sizes of products such as bottles, pipes, containers, and toys.
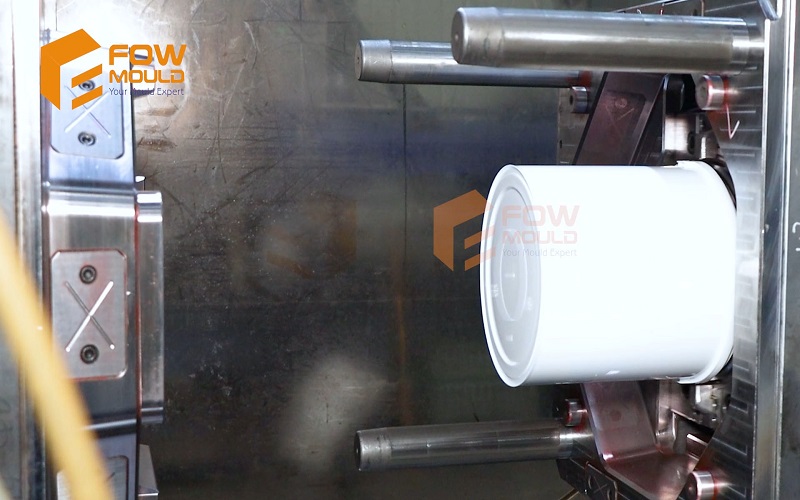
On the other hand, Delrin can be processed through injection molding and extrusion molding, as well as mechanical machining and compression molding.
Delrin can be machined into high-precision parts through processes such as turning, milling, and drilling, making it particularly suitable for small-batch production and custom parts.
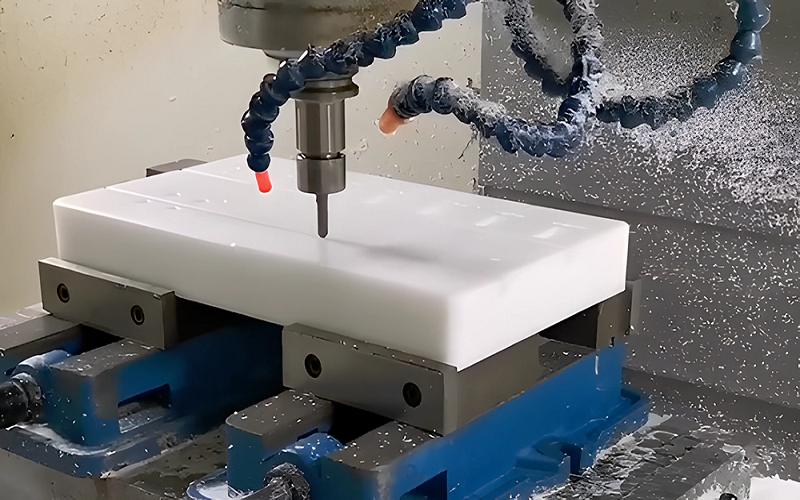
HDPE vs Delrin:Applications
As one of the most versatile plastic materials, HDPE is widely used in packaging, piping, consumer goods, agriculture, construction, and electrical insulation due to its excellent chemical resistance and flexibility.
FDA, NSF, and USDA-approved food-grade HDPE plastic is the ideal material for various food and beverage containers.
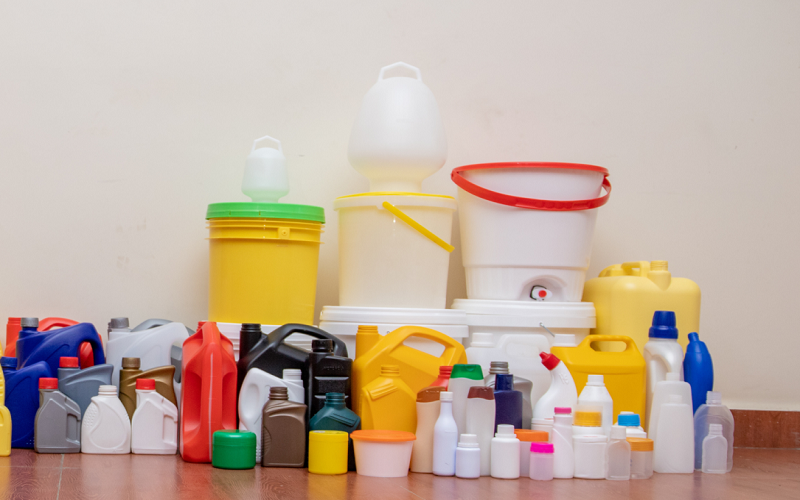
Delrin material is renowned for its high strength, low friction, and excellent dimensional stability.
These properties make Delrin an ideal material for high-load and high-impact applications such as gears, conveyor belts, bearings, rollers, and safety restraint devices.
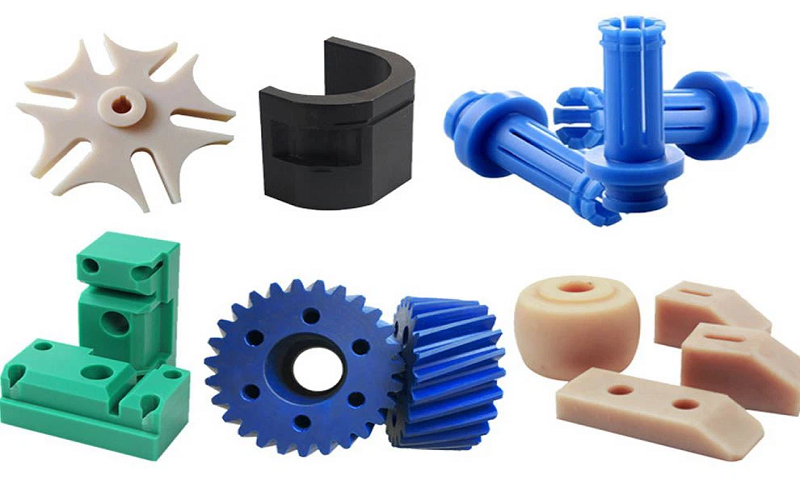
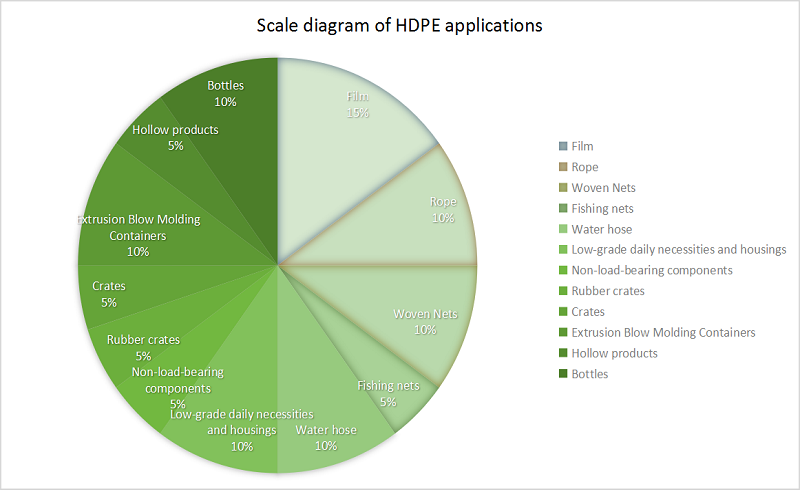
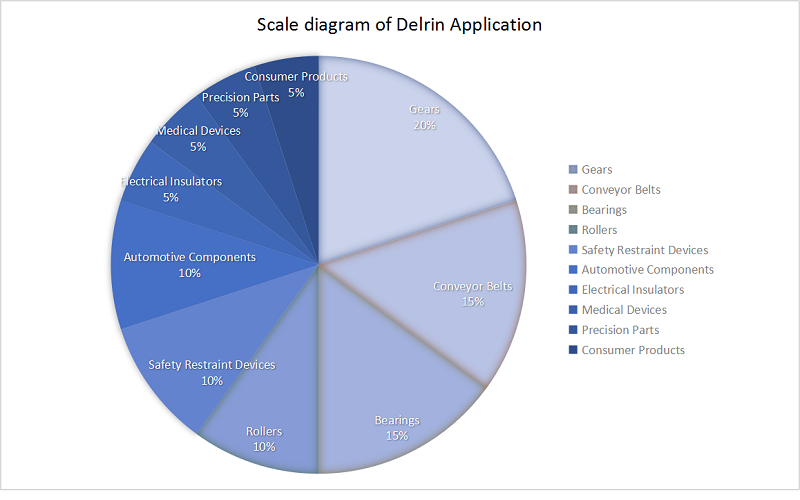
HDPE vs Delrin:Safety
As people become more concerned about plastic safety, the question “Is HDPE food safe?” has garnered significant attention.
In fact, HDPE is considered one of the best food-safe plastics. It is one of the most stable and inert forms of plastic, with corrosion resistance and low moisture absorption, making it an ideal choice for food storage applications.
Additionally, HDPE plastic is completely free of BPA, making it safe for human use under normal conditions.
In contrast, Delrin material is highly regarded in various industries for its high strength and low friction, making it the preferred material for high-load mechanical applications.
It is considered safe for use in mechanical and industrial fields.
However, Delrin can release formaldehyde at high temperatures, so it must be used with caution in food contact applications.
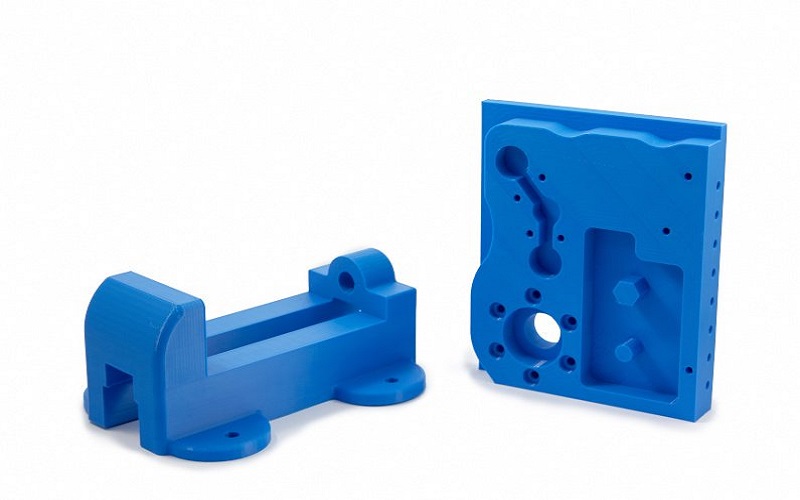
HDPE vs Delrin:Recyclability and Sustainability
Generally, both HDPE and Delrin are recyclable plastics, but they differ in terms of recycling and sustainability.
In terms of recycling efficiency, HDPE is relatively easy to recycle and is often marked with the recycling code “2.”
A European study has shown that HDPE plastics can be recycled up to 10 times.
Most recycled HDPE is made into composite wood or plastic lumber.
Additionally, the production and reprocessing of HDPE consume less energy, making it a relatively eco-friendly choice.
Delrin, used in high-load and high-precision applications, has a narrower range of recycled uses.
It requires specialized recycling facilities and has higher costs.
Additionally, Delrin can release formaldehyde at high temperatures, complicating the recycling process.
Strict temperature and environmental controls are necessary during recycling and reprocessing.
Despite these challenges, advancements in recycling technology can help Delrin achieve better resource utilization and environmental protection.
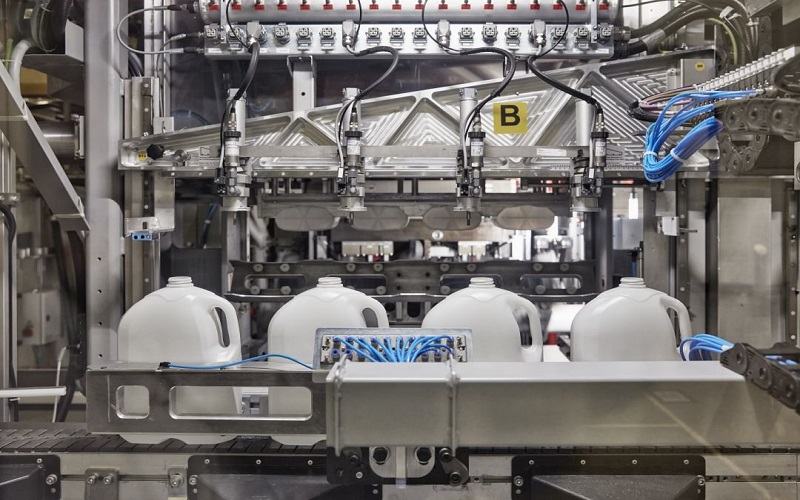
HDPE vs Delrin:Cost
When choosing between HDPE and Delrin, cost is also an important factor to consider.
Generally, the price of HDPE is around $1-2 per kilogram, while Delrin costs about $3-5 per kilogram.
Due to differences in production processes, HDPE is less expensive than Delrin.
For products with a smaller budget, high-density polyethylene is more cost-effective, while Delrin is a better choice for products requiring high load-bearing capabilities.
Conclusion
In the content above, we have thoroughly explored HDPE and Delrin materials, detailing their concepts, properties, applications, safety, and recyclability.
We conducted a comprehensive material comparison. If you are still unsure about choosing between HDPE and Delrin for your project, please contact FOWMOULD.
We offer one-stop injection molding services. Click below for more information on plastics and a free quote!