The comparison of ABS vs Delrin is often a crucial consideration in material selection.
ABS is renowned for its excellent impact resistance and ease of processing, commonly found in automotive parts, consumer electronics, and 3D printing.
In contrast, Delrin is distinguished by its superior rigidity, low friction coefficient, and exceptional wear resistance, making it ideal for precision mechanical components.
In this article, we will delve into the main differences between ABS and Delrin, including their performance characteristics, processing methods, application and environmental impact.
What Is ABS Material?
ABS plastic is a synthetic resin material composed of three monomers: acrylonitrile (A), butadiene (B), and styrene (S).
It appears as opaque, ivory-colored granules with a specific gravity of 1.05 and low water absorption.
The key characteristics of ABS include high strength, good rigidity, and excellent impact resistance.
Additionally, it offers good chemical corrosion resistance and heat resistance.
Due to its low production cost and ease of processing, ABS is highly favored by plastic molding manufacturers.
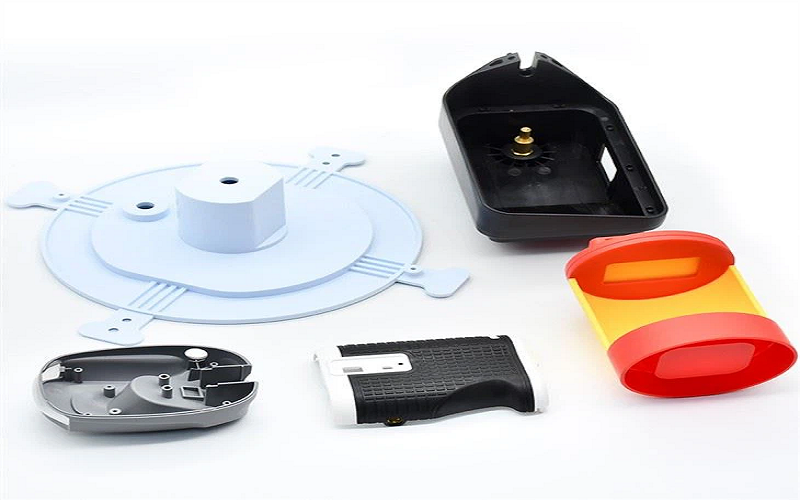
What Is Delrin?
Delrin, a homopolymer of polyoxymethylene, was first developed and introduced to the market by DuPont in 1956.
It features excellent low friction and wear resistance, along with rigidity and strength comparable to metals.
Compared to copolymer polyoxymethylene, Delrin offers higher tensile strength, rigidity, and creep resistance, with significantly enhanced impact resistance.
This makes it suitable for designing thinner, lighter parts while maintaining shorter molding cycles, thereby reducing overall costs.
It is the specified material for high-load mechanical applications by many industry leaders.
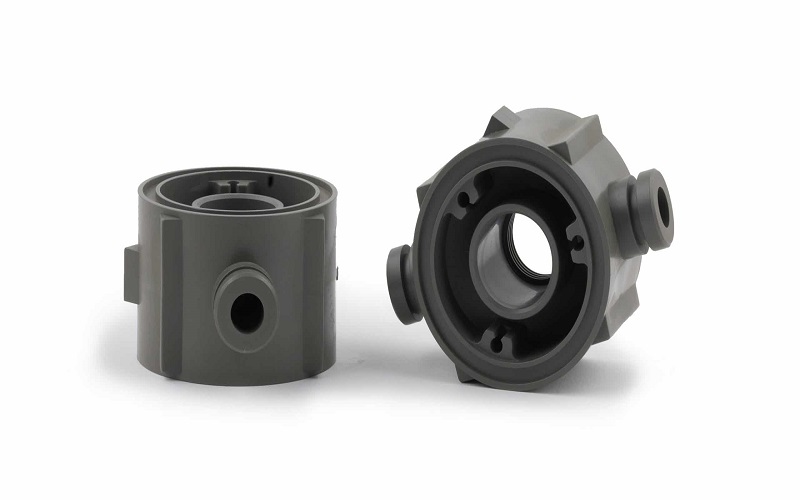
ABS vs Delrin:Properties
In terms of mechanical properties, ABS has good impact resistance and moderate rigidity, while Delrin exhibits higher rigidity and excellent wear resistance.
Regarding thermal properties, ABS has moderate heat resistance and can be used long-term within a temperature range of -40°C to 85°C.
In contrast, Delrin is more heat-resistant and does not easily deform at high temperatures.
In terms of chemical resistance, ABS has moderate resistance to chemicals, whereas Delrin offers better resistance to solvents and chemicals.
This table below shows data on the performance comparison between ABS and Delrin material:
Properties | ABS | Delrin |
Density(g/cm3) | 1.05 | 1.41 |
Melting Point(℃) | – | 175 |
Tensile Yield Strength(MPa) | 40-50 | 69 – 80 |
Tensile Modulus (GPa) | 2.0-2.5 | 2.8-3.5 |
Water Absorption(%) | 0.2 – 0.4 | 0.3 |
Shrinkage(%) | 0.4 – 0.7 | 1.8-2.1 |
Impact Strength (J/m) | 200 – 300 | 50-70 |
Heat Deflection Temp (℃) | 80-100 | 120-170 |
Friction Coefficient | Medium (0.4 – 0.5) | Low (0.2 – 0.3) |
ABS vs Delrin:Processing Methods
Due to their distinct characteristics, ABS and Delrin have significant differences in their processing methods.
ABS material boasts high impact strength and excellent mechanical properties, making it well-suited for various processing techniques such as injection molding, extrusion, and 3D printing.
ABS injection molding is one of the most common methods, ideal for mass-producing small ABS plastic parts.
ABS extrusion is suitable for producing continuous profiles or pipes, such as ABS piping, doors, and windows.
Additionally, ABS is one of the most stable materials for 3D printing, often used as a foundational material for 3D models.
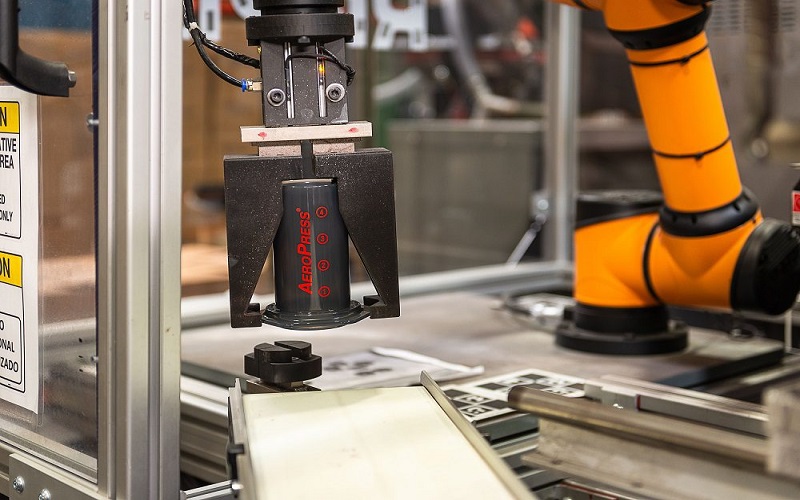
In contrast, Delrin is more challenging to process and is primarily used in injection molding and machining, suitable for manufacturing high-precision and high-strength components.
Delrin injection molding is one of its main processing methods.
Due to Delrin’s high rigidity and low friction characteristics, this method is ideal for producing precision mechanical parts such as gears, bearings, and sliders.
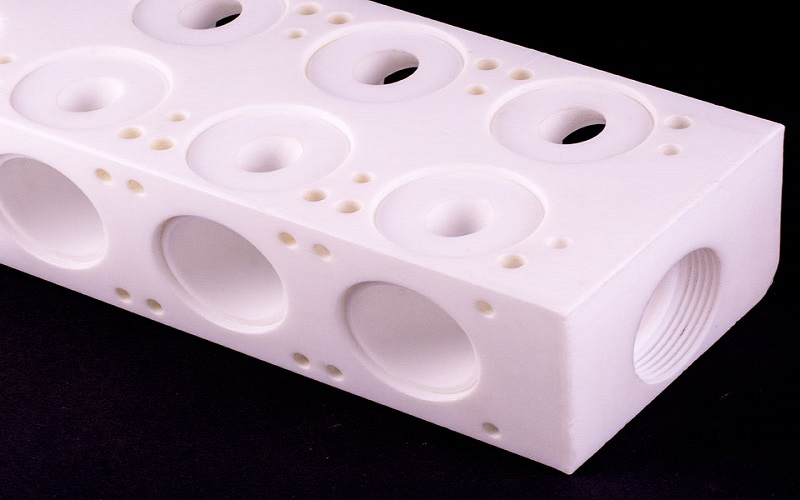
ABS vs Delrin:Applications And Uses
In terms of applications, ABS and Delrin have many similarities, but their specific uses differ.
ABS excels in applications that require lightweight, durability, and an attractive appearance, making it widely used in automotive parts, consumer electronics, household goods, and 3D printing.
On the other hand, Delrin is primarily used for high-precision and high-strength mechanical components, such as industrial machine parts, automotive fuel system components, medical devices, and high-performance electronic components.
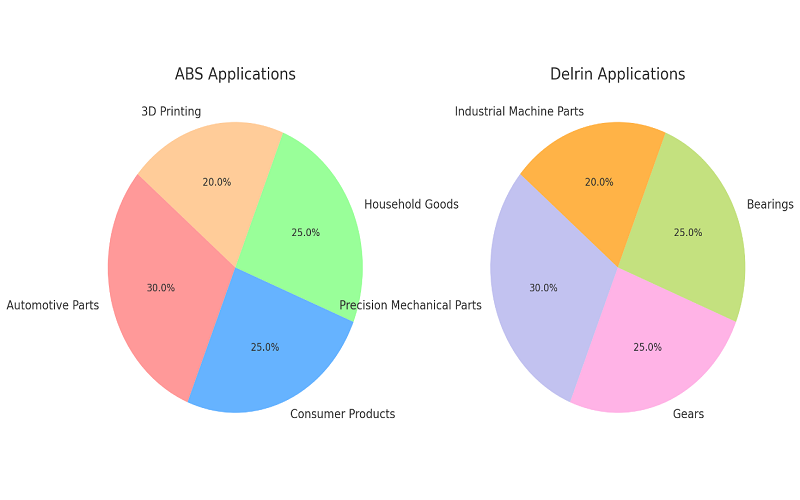
ABS vs Delrin:Environmental Impacts
Although ABS and Delrin are widely used, their actual recycling rates are low, and their production and disposal processes have potential negative environmental impacts.
The production of ABS involves petrochemical products, resulting in the emission of carbon dioxide and other greenhouse gases, which increases the carbon footprint.
Additionally, burning ABS releases harmful gases that negatively affect air quality.
From a plastic recycling perspective, ABS is a biocompatible and recyclable material, identified by recycling code #9.
However, the recycling rate for ABS products is relatively low, and the recycling process is complex.
If ABS waste is not properly managed, it can break down into microplastics, polluting soil and water bodies and affecting ecosystems.
Similarly, the production of Delrin involves petrochemical products and may release harmful chemicals such as formaldehyde, potentially polluting air and water sources.
Furthermore, Delrin has an even lower recycling rate than ABS, and the recycling process is costly, resulting in a low actual recycling rate.
Despite this, Delrin’s high durability and long lifespan reduce the need for frequent replacement, thereby lowering resource consumption and waste generation to some extent.
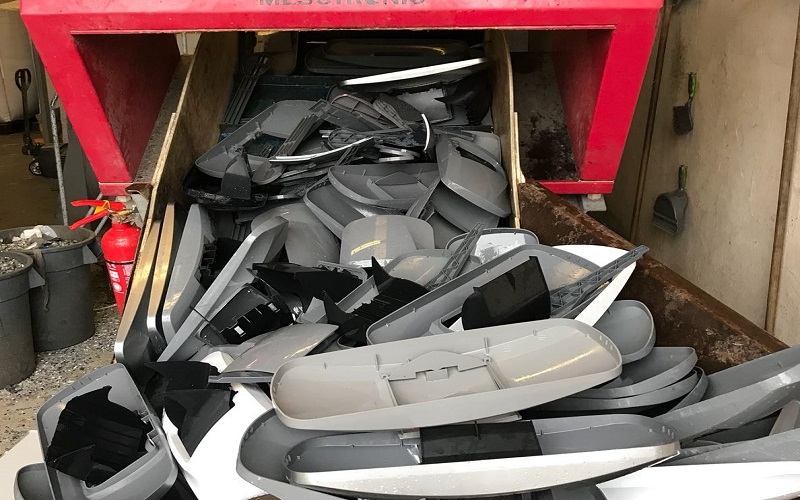
Which Is Safer, ABS Or Delrin?
When addressing the question, “Is ABS plastic safe?” the answer is affirmative: ABS plastic is safe.
It has good heat resistance and chemical resistance and does not release harmful substances under normal usage conditions.
Additionally, the widespread use of ABS in children’s toys further attests to its safety.
However, care must be taken in the disposal and recycling of ABS.
If ABS waste is not properly managed, it can break down into microplastics, polluting the environment.
Therefore, although ABS itself is safe, its lifecycle management needs to be cautious to minimize environmental impact.
In contrast, Delrin materials pose some potential risks. During the production of Delrin, formaldehyde and other harmful chemicals may be released, posing a threat to the environment and health.
Furthermore, Delrin can release harmful gases when subjected to high temperatures or burning, necessitating special attention in these scenarios.
To ensure safe use, it is essential to strictly control the production process of Delrin and avoid high temperatures and burning during use.
Despite these concerns, Delrin excels in many high-precision and high-strength applications, with its high durability and low friction properties making it ideal for many mechanical components.
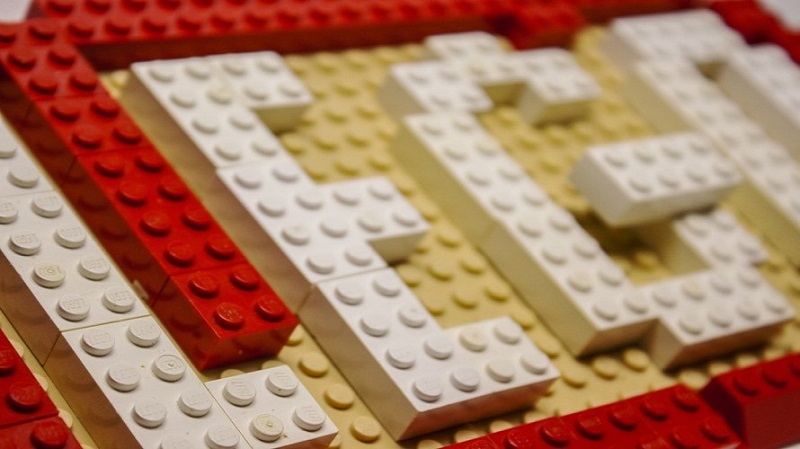
Conclusion
From the above content, we have learned about the differences between ABS and Delrin.
ABS plastic is safe under normal usage conditions, with excellent impact resistance, making it suitable for automotive parts, consumer products, and 3D printing.It is easy to process and cost-effective.
On the other hand, Delrin, despite certain risks during production and high-temperature use, is renowned for its exceptional rigidity, low friction, and excellent wear resistance.
This makes it ideal for precision mechanical components, gears, and bearings.
If you want to learn more about ABS and Delrin, please follow FOWMOULD. We will continue to publish more information about plastics.