As two commonly used plastic materials in the industrial and consumer goods sectors, ASA and PC each have distinctive features and are widely applied across various fields.
ASA is renowned for its excellent weather resistance and mechanical strength, making it an ideal choice for outdoor applications.
On the other hand, PC is favored for its outstanding impact strength and high transparency, particularly in the automotive and medical industries.
This article revolves around the theme of “ASA vs PC,” engaging in a detailed comparison of the differences between ASA and PC materials.
It evaluates their performance, processing capabilities, safety, and environmental adaptability to assist readers in making the best choice based on their project requirements.
ASA
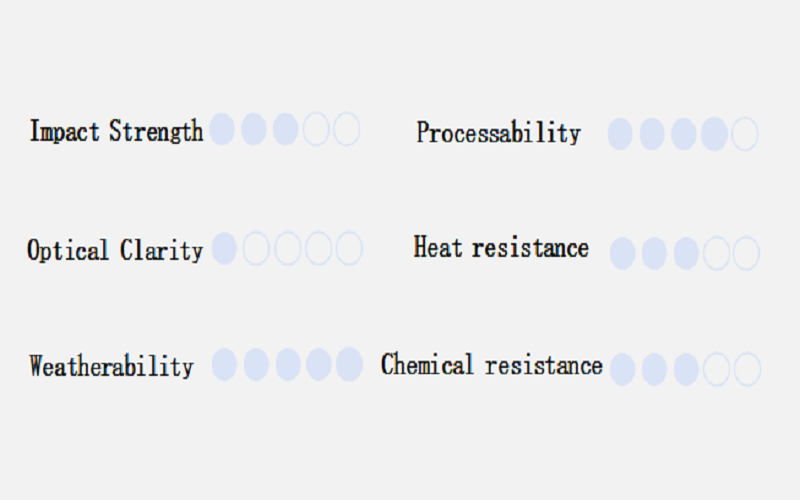
ASA is a ternary polymer composed of acrylonitrile, styrene, and acrylic rubber, belonging to the category of impact-modified resins.
In ASA, the use of acrylic rubber without unsaturated double bonds replaces the butadiene rubber with unsaturated double bonds found in ABS material, thus providing excellent anti-aging and weather resistance properties.
Secondly,ASA material possesses high tensile strength, impact resistance, and hardness, enabling it to withstand certain external forces and pressures without easily fracturing or deforming.
Additionally, ASA also exhibits good mechanical properties such as high strength and crack resistance.
It can be molded into various shapes through processing techniques like injection molding and extrusion.
Moreover, its surfaces are smooth and brightly colored, offering an appealing decorative effect.
PC
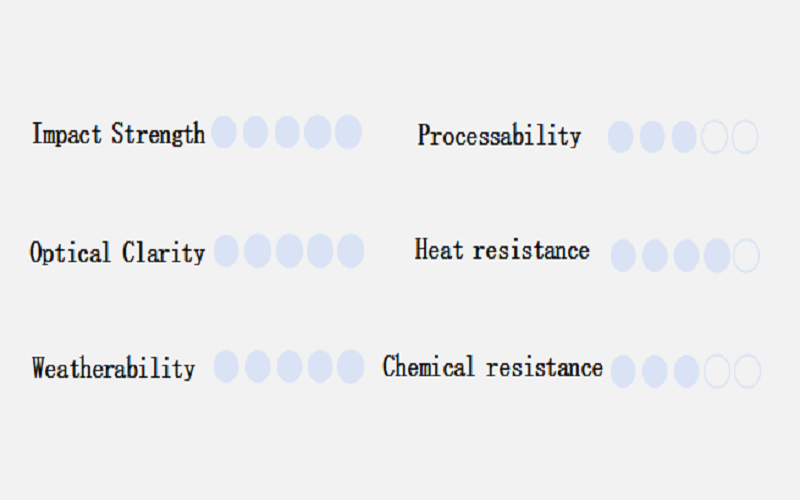
Polycarbonate (PC) material is a high polymer containing carbonate groups in its molecular chain.
It can be divided into different types, such as aliphatic and aromatic, based on the structure of the ester group.
A prominent feature of PC plastic is its excellent transparency, with a light transmittance of over 90%, coupled with very high strength and rigidity, as well as strong impact resistance.
Furthermore, PC material exhibits good chemical resistance and thermal stability.
It is resistant to common chemicals such as acids, alkalis, and oils, and is not easily corroded.
At the same time, PC material has a high heat deflection temperature, maintaining good stability even at temperatures up to 120% of its environmental threshold.
However, it has less than ideal hydrolytic stability, is sensitive to notches, and can yellow over time when exposed to ultraviolet light.
ASA vs PC:Advantages And Disadvantages
It is well known that ASA has a definitive advantage in weather resistance, offering better UV resistance and anti-aging properties compared to PC.
Unlike PC, which may yellow when exposed to sunlight over time, ASA can resist degradation, aging, and fading caused by UV exposure, and it does not decompose or discolor during high-temperature oxidative processing.
However, polycarbonate exhibits superior heat resistance compared to ASA.
The melting point of PC is about 250°C, with a heat deflection temperature of 135°C, and it maintains good mechanical properties within a temperature range of -100°C to +180°C.
Additionally, PC also has good electrical insulation properties and is the only product among the five major engineering plastics with good transparency.
In contrast, ASA possesses excellent anti-static properties, reducing the accumulation of dust on surfaces and minimizing soiling.
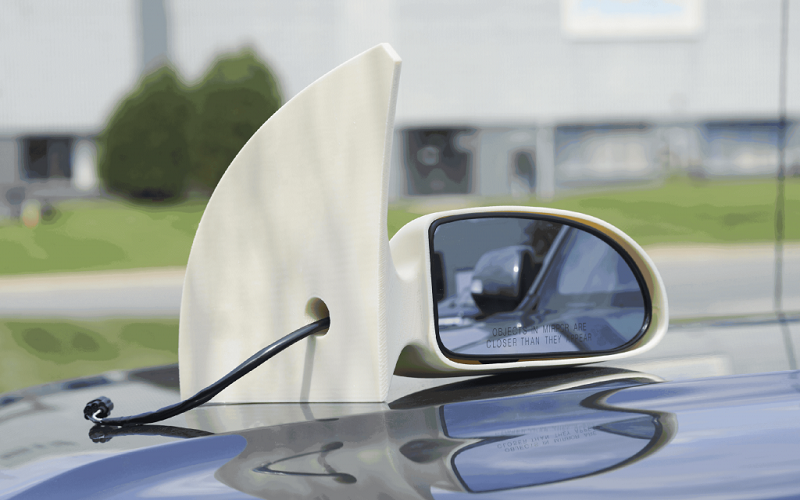
ASA vs PC:Application
As a popular material in 3D printing, ASA has a wide range of applications in outdoor applications, automotive parts, architectural modelling and many other fields.
- Outdoor Uses: Outdoor flower pots, gardening tools, signs, and billboards.
- Automotive Industry: Car exteriors, mudguards, and headlight covers.
- Building Materials: Architectural models, tiles, window and door frames, and exterior wall panels.
- Electronics Casings: Such as TV, computer, and mobile phone casings.
PC plastics, with their high impact resistance and transparency, are tailored to the individual needs of different industries, with polycarbonate molding products representing a combination of precision and cost-effectiveness.
- Medical Industry:Disposable dental tools, surgical masks, oximeters, and blood collection devices.
- Optical Applications: Optical lenses for cameras, microscopes, telescopes, and eyeglasses.
- Automotive Industry: Headlight covers, windows, rearview mirrors, dashboards, and lights.
- Protective Equipment: Riot shields and face shields.
In summary, ASA and PC plastics excel in different application areas.
ASA’s weather resistance makes it the material of choice for outdoor applications, while PC stands out in high-temperature applications and transparent materials due to its high impact resistance and clarity.
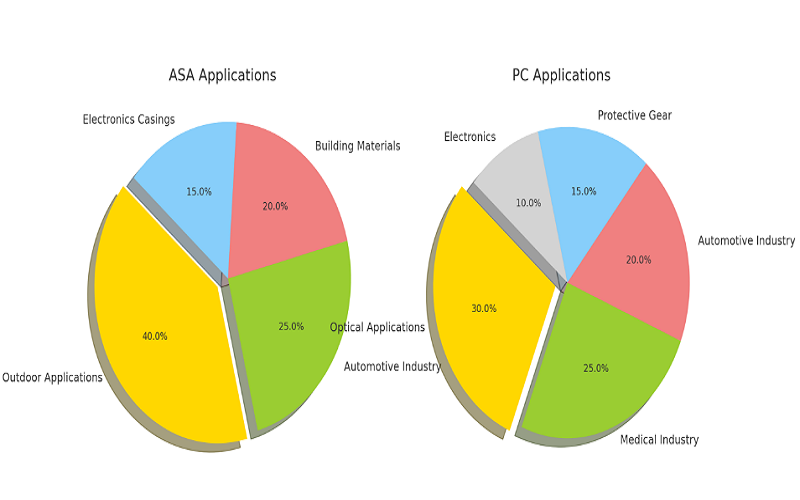
ASA vs PC:Safety Profile
ASA plastic is widely considered safe for production and use as it does not contain or release any harmful substances, and its excellent weatherability ensures a longer lifespan and preserved appearance of ASA products.
Moreover, its B1 fire rating meets basic residential fire safety requirements, providing protection for both buildings and occupants.
However, during 3D printing or exposure to high temperatures, ASA may emit a limited amount of volatile organic compounds (VOCs) and may warp, so caution is advised in such conditions.
Similarly, PC plastic is renowned for its transparency and high impact resistance, making it the material of choice for eyeglasses and protective face shields.
Yet, it’s important to note that PC may release BPA when exposed to high temperatures, a chemical that has raised health concerns, particularly for sensitive groups such as pregnant women, children, and the elderly.
Therefore, choosing BPA-free PC materials is crucial when designing products that come into contact with food or are regularly exposed to the human body.
For an in-depth understanding of the safety of polycarbonate, the article “Is Polycarbonate Safe?” provides comprehensive information.
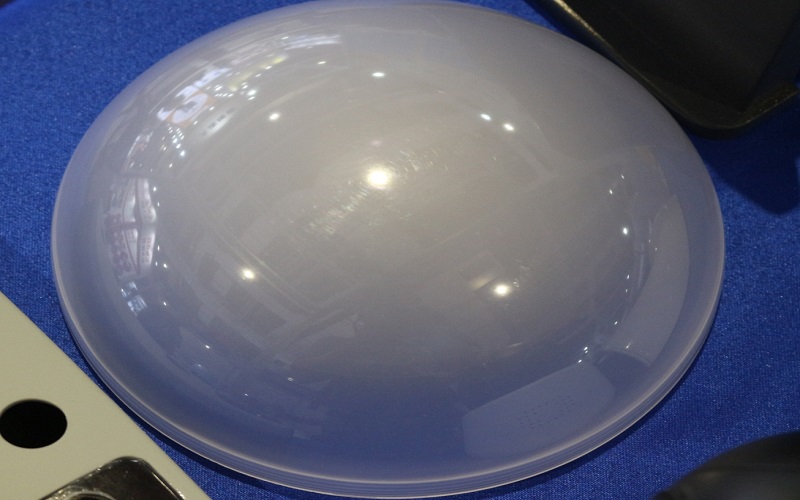
ASA vs PC:Are They Recyclable?
In the plastics recycling symbols, ASA and PC are usually marked with the number “7,” which indicates that they are recyclable.
However, compared to more commonly recycled eco-friendly plastics such as PET and PP, the recycling infrastructure for ASA and PC is not as widespread, making their recycling process more challenging.
Additionally, due to the presence of Bisphenol A (BPA), recycling of PC products must be handled with extra caution, leading to increased recycling costs and restricting the use of recycled PC materials.
For plastic manufacturers and consumers, although ASA and PC materials are safe and versatile, there are still some economic and technical barriers to recycling these materials currently.
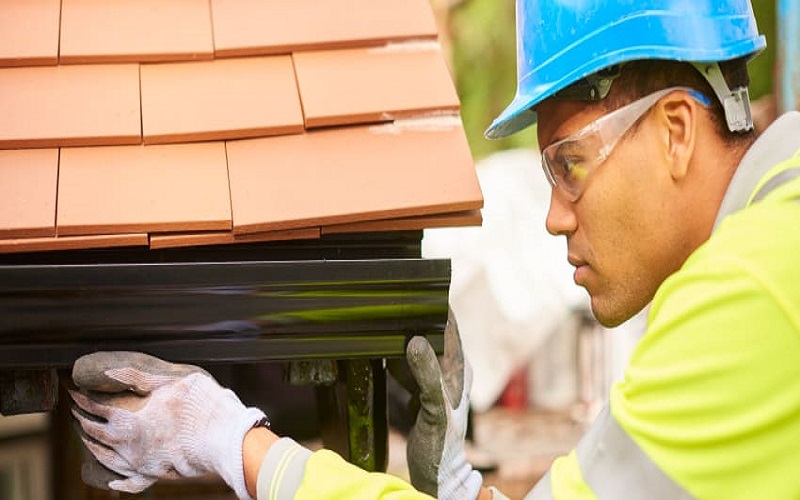
PC/ASA :Combination Of ASA And PC Material
Due to the compatibility between ASA resin and PC, blending ASA with PC creates a copolymer known as PC/ASA alloy.
This alloy not only inherits the excellent weather resistance of ASA, capable of withstanding UV rays and prolonged outdoor exposure, but also leverages the high impact resistance and strength of PC, enhancing the overall mechanical properties of the material.
The combined performance of this material makes it a popular choice across multiple industries, able to meet more complex and diverse design requirements.
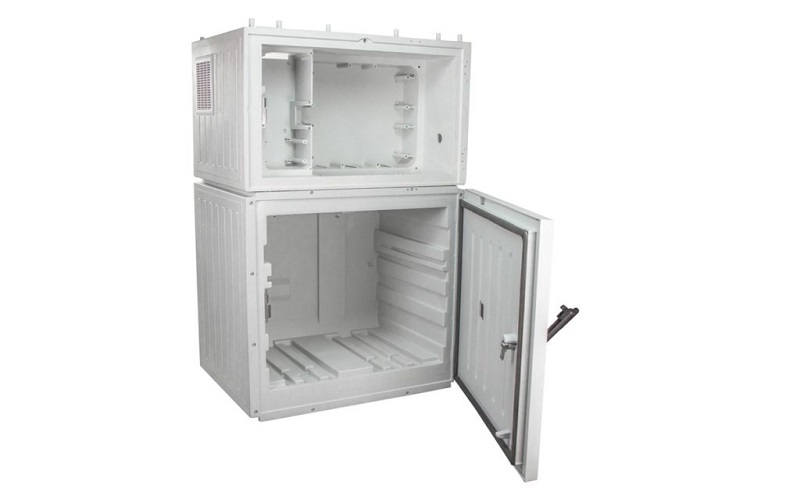
How To Choose Between ASA And PC?
When deciding between ASA and PC, it’s important to consider the specific needs of your project.
For example, ASA is better suited for outdoor applications due to its weather resistance and cost-effectiveness, while PC is ideal for situations that require high temperature tolerance and optical clarity.
Although recycling these materials currently presents challenges, it is believed that technological advancements will eventually overcome these obstacles.