As the foremost among the five major engineering plastics, nylon is extensively used across various applications and is an indispensable raw material in the 3D printing and injection molding industries.
Therefore, injection molding manufacturer and 3D printing companies often compare it with other thermoplastic materials, including ASA, POM, and PEEK.
This article aims to delve into the differences between these materials and nylon, offering a comprehensive comparative analysis from multiple dimensions such as physicochemical properties, application fields, and cost-effectiveness.
ASA
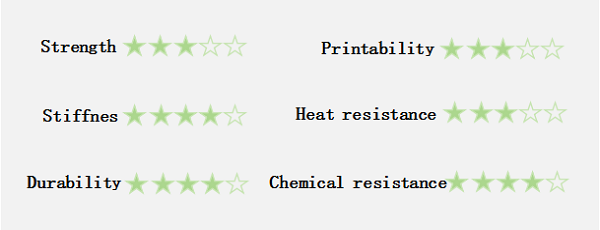
ASA is a terpolymer composed of Acrylonitrile (A), Styrene (S), and Acrylate (A), forming a tri-component graft copolymer.
Compared to ABS plastic, ASA significantly improves weather resistance by substituting butadiene rubber with acrylate rubber, which does not contain double bonds, resulting in a weather resistance about 10 times greater than that of ABS.
Moreover, ASA possesses good colorability; due to the excellent weather resistance of the resin itself, it can be dyed in various bright colors without fading easily.
Furthermore, ASA also has good mechanical properties, corrosion resistance, processability, and impact resistance, making it widely used in fields such as automotive and electrical engineering.
POM
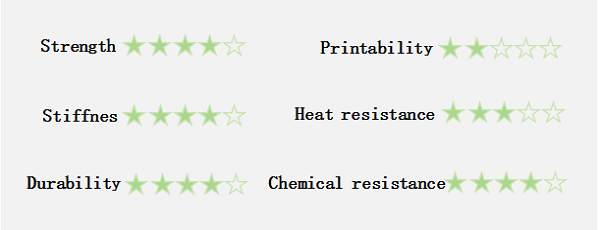
Polyoxymethylene , whose main structural unit is —CH2O—, is the third most widely used general-purpose engineering plastic, following polyamide and polycarbonate.
It can be used long-term within a temperature range of -40°C to 100°C, maintaining resistance to creep, fatigue, wear, and chemical corrosion even under harsh conditions.
These performance and cost advantages allow it to replace non-ferrous metals like brass, aluminum, and zinc in applications such as gears, electrical housings, and other automotive components, as well as in the high-end electronics and electrical industries.
It is known as “the metal among plastics,” with nicknames like “plastic steel” and “super steel.”
PEEK
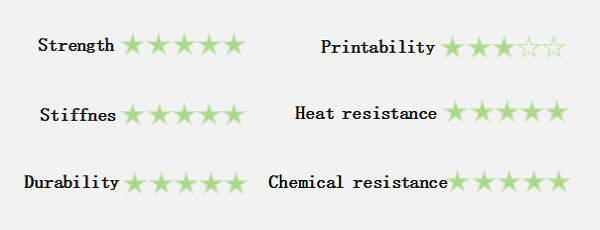
Polyether Ether Ketone, abbreviated as PEEK, is a semi-crystalline, linear aromatic polymer whose main chain is composed of repeating units containing one ketone bond and two ether bonds.
This structure endows it with exceptional heat resistance (over 260°C), outstanding mechanical properties, and chemical stability, allowing it to replace traditional materials like metals and ceramics in many specialized areas.
It is recognized as one of the best-performing polymers currently available.
Consequently, it is extensively used in a wide range of fields such as electronics and electrical engineering, aerospace, automotive, energy, and other industries, as well as in medicine.
Nylon

Polyamide (PA), commonly known as nylon, refers to a group of thermoplastic resins characterized by the presence of repeated amide groups—[NHCO]—in their molecular backbone.
Among them, polyhexamethylene adipamide and polyhexamethylene diamine adipate (nylon 6 and nylon 66, respectively) are the most widely used polyamide materials.
PA stands out for its impressive comprehensive properties, including mechanical strength, heat resistance, wear resistance, chemical resistance, and self-lubrication, coupled with a low coefficient of friction and inherent flame retardancy.
It is easily processed and well-suited for reinforcement modifications with glass fibers and other fillers.
As such, PA is an excellent material for replacing metals like steel, iron, and copper, finding extensive applications in various medical devices and knitwear.
Strengths and Weaknesses Analysis
In the Nylon vs ABS matchup,we find that Nylon has a definitive advantage in wear resistance and tensile strength.
However, as a material similar to ABS, ASA boasts UV resistance and superior weatherability, qualities that Nylon lacks.
Compared to Nylon, ASA also offers exceptional aesthetic performance, such as glossiness and color retention, whereas Nylon tends to fade over time under UV exposure.
When it comes to POM, it typically exhibits higher tensile strength and stiffness than Nylon.
This makes POM highly suitable for precision parts requiring high rigidity.
Nevertheless, Nylon may be a better choice in moist environments because, unlike POM, it does not degrade as easily with long-term water exposure and POM can become brittle.
PEEK, a high-end specialty engineering plastic, can withstand temperatures exceeding 250°C, a feat Nylon cannot match.
It has superior mechanical strength and modulus, and its chemical resistance is better than Nylon, making it applicable in harsh conditions such as aerospace, automotive, and medical industries.
However, PEEK’s high melting point demands stringent processing conditions and incurs higher costs.
In contrast, Nylon is easier to process and more cost-effective, making it a popular choice for a wide range of general applications.
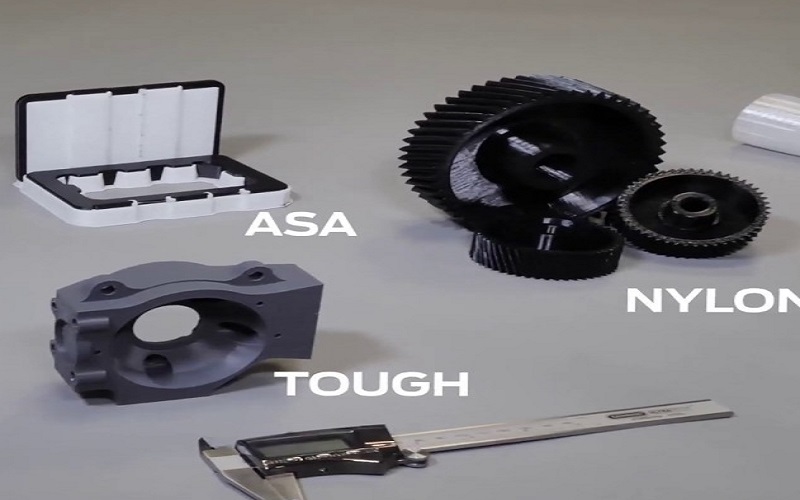
Scope Of Applications
Based on the unique properties of each material, they can meet specific technical and practical demands in their application fields to the fullest extent.
The UV resistance, surface smoothness, and the support of ASA injection molding processes make it the material of choice for outdoor and aesthetic applications.
Its high weatherability allows ASA plastic to have broad applications in automotive exterior parts, garden equipment, and outdoor billboards.
Simultaneously, ASA’s ability to maintain vibrant colors and resist surface aging in 3D printing applications significantly enhances the aesthetic value and lifespan of the printed products.
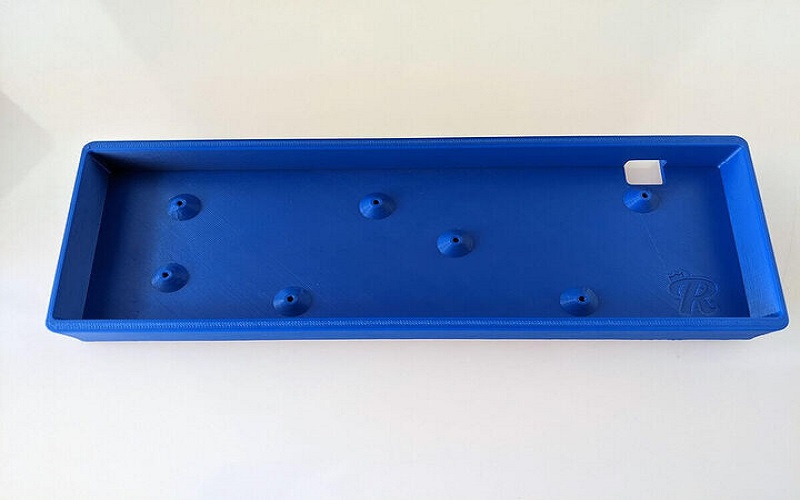
POM, often referred to as “the metal among plastics,” showcases unmatched advantages in manufacturing precision parts due to its high hardness, strength, and rigidity.
POM injection molded parts are indispensable in the automotive industry for creating high-precision motor gears, pump components, window lifters, as well as in precision instruments and various mechanical components.
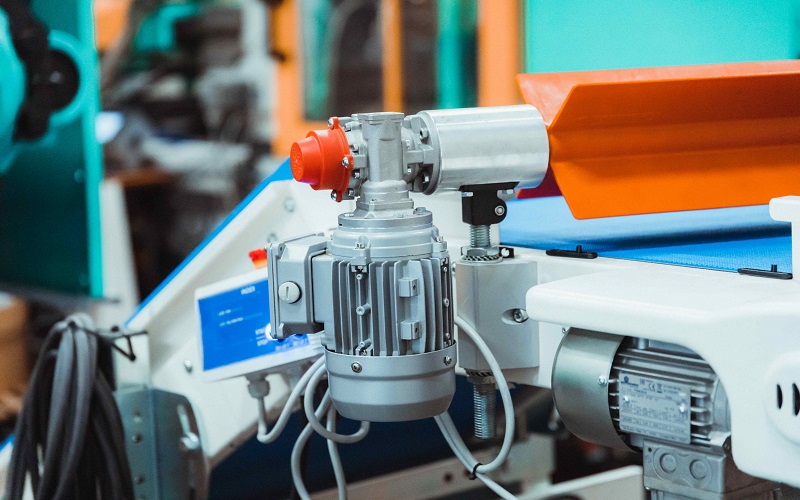
Facing the stringent requirements of the aerospace, medical, and energy industries, PEEK demonstrates its irreplaceable role with excellent high-temperature performance, outstanding mechanical strength, and chemical stability.
In the aerospace field, injection molding PEEK parts are used to manufacture components that withstand extreme environments; in the medical sector, it is commonly used for implants and surgical instruments; in the energy industry, PEEK can endure extreme temperatures and corrosive environments, ensuring the safe and stable operation of extraction equipment.
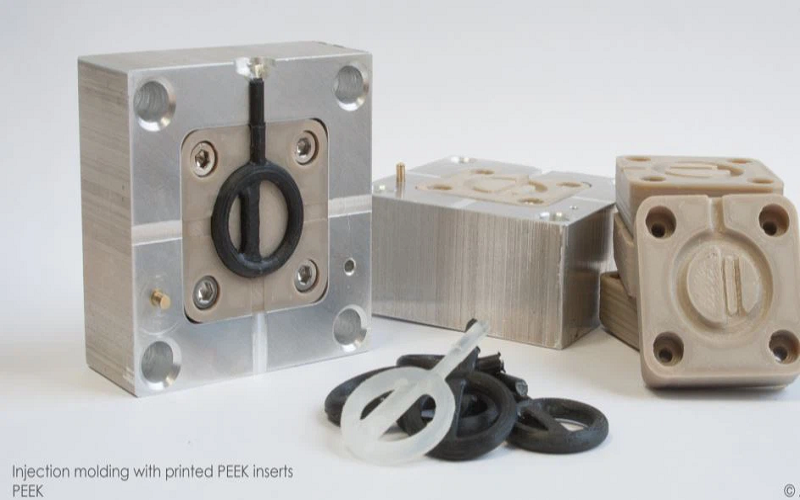
The versatility and cost-effectiveness of Nylon, through Nylon injection molding, make it a principal material for consumer goods and industrial machinery.
Nylon’s high strength, good wear resistance, and impact resistance make it the ideal choice for industrial gears, bearings, electronic device housings, and various sports equipment.
At the same time, the flexibility and durability of Nylon fibers also make them widely used in clothing and household textiles.
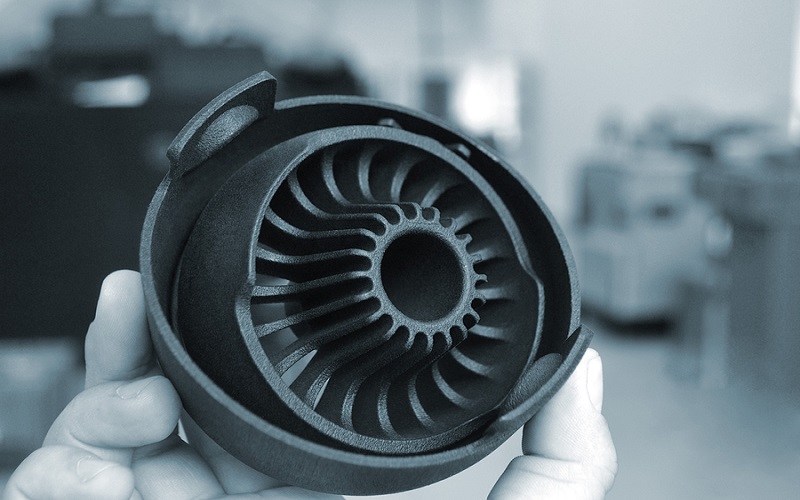
Security Assessment
As the demand for plastic products grows, the safety of materials like ASA, POM, PEEK, and Nylon gains focus.
ASA and Nylon release harmful chemicals upon burning, with ASA potentially emitting benzene and VOCs, and Nylon releasing ammonia, CO, CO2, and NOx, each carrying health risks.
To mitigate these risks, flame retardants are commonly added.
POM is notable for releasing formaldehyde, a carcinogen, during processing, requiring controlled manufacturing environments.
Compared to POM, Nylon’s processing emissions, like caprolactam, pose lower risks, making Nylon generally safer in terms of toxic emissions.
PEEK stands out for its high-temperature stability, minimizing the risk of harmful emissions in scenarios unsuitable for Nylon, thus offering a safer alternative for high-temperature uses.
Additionally, specific grades of PEEK and Nylon are designed to meet FDA and medical standards, ensuring their safe application in medical contexts.
To learn more about the safety of nylon materials, please read the article “Is Nylon Safe“.
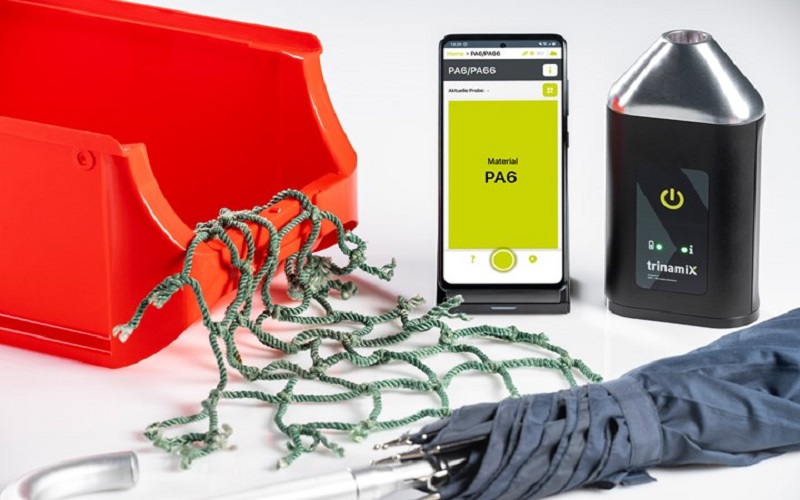
Environmental Impacts
From a recycling perspective, recycling and reusing ASA remains a challenge as it requires effective separation from other types of plastics.
Additionally, POM is not easily degradable in the natural environment, and its recycling process is relatively complex, necessitating specialized facilities and technology for effective recycling and reuse.
In contrast, Nylon is more recyclable than ASA and POM, especially Nylon 6, which can be chemically recycled back into monomers for reuse.
Although PEEK is not biodegradable, it is recyclable; however, its specialized application range limits recycling channels and opportunities compared to other more common plastics.
From an environmental standpoint, the production process of ASA may involve the use of acrylonitrile, posing potential risks to the environment and health.
POM’s situation is similar to ASA, as it releases formaldehyde during production, a harmful gas that can pose threats to worker health and the surrounding environment.
Overall, compared to the other materials, Nylon is more easily recycled and reused, especially with the chemical recycling technology of Nylon 6 offering new possibilities for the plastic recycling sector.
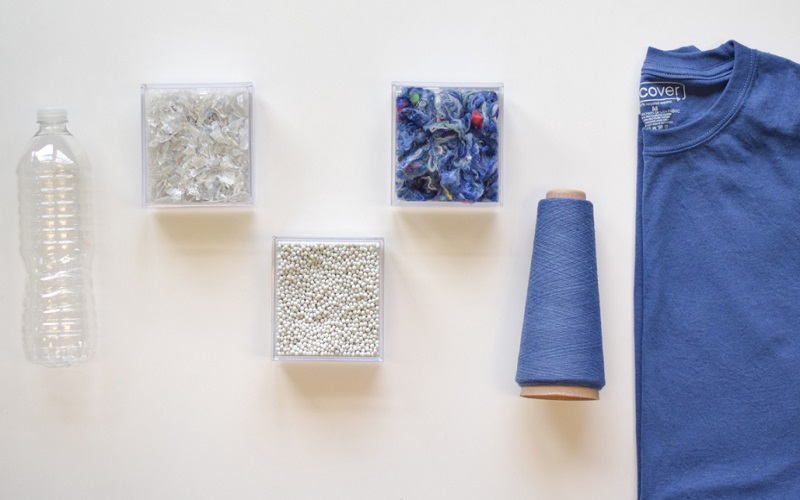
Conclusion
In summary, ASA, POM, PEEK, and Nylon each play significant roles in various application fields due to their unique characteristics.
ASA is suitable for outdoor weather-resistant applications, POM and PEEK excel in engineering applications requiring high mechanical performance, while Nylon, with its broad modification potential and excellent environmental recyclability, finds widespread use across numerous domains.
The correct material selection can significantly enhance the efficiency of your project.
If you’re looking for a professional plastic manufacturing supplier, FOWMOULD will be your best choice!