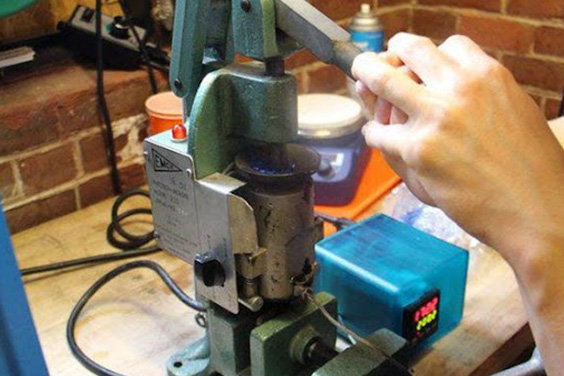
Share :
Share :
Injection molding is a step-by-step process that undergoes different stages, depending on the type of product being made. These steps don’t have to be identical, but they do follow a certain protocol that ensures the goal is attained with the lowest energy consumption and raw material wastage. This process from the start to the end is what is called the mold flow.
We are going to analyze the mold flow analysis, how it affects the general success of an injection molding process, how it shapes the plastic part design such as auto plastic parts, the applications it can be utilized for in the injection molding process, and the limitations and benefits it brings to the table. So stick around to get a full mold flow analysis guide.
Mold Flow Analysis (MFA) is a software that is used to simulate the flow of molten plastic material into the injection mold crate, allowing the manufacturer to elevate mold and part design in order to create products that are of the highest quality.
The MFA is quite the handy software that not only increases the chances of creating the best products that the molding process can produce but it also gives you a preview of what and how your end product will look and behave. This insight allows you the space and time to make adjustments beforehand in order to reduce wastage and create the best quality that the machine and the technology can manage.
The benefits of using mold flow analysis are unlimited, and only the surface has been scratched so far. They simply add a level of efficiency that is unrivaled, and this is why it has become a very important tool of manufacturing that every injection molding plant makes use of to increase its productivity. Getting the chance to simulate everything beforehand allows the luxury to make changes on the spot, and this leads to saving costs, time, and labor.
The mold flow analysis has brought a lot of benefits to the injection molding model. There is a reason why many manufacturers in the injection molding industry are turning to MFA in large numbers. The following are some of the benefits that are associated with the MFA software.
Most of the optimization is done through tooling, but in the event that these tools are not available, the only way to optimize the injection molding process is through the use of MFA software. The software will be able to point out the following important aspects of the production process.
MFA gives injection molding manufacturers the luxury of visualizing their end-products, and this allows them to make quick and immediate decisions on the spot. These informed decisions can help the production process greatly and could improve the quality of the end-product, making it turn out way better than the initial intentions.
Some of the areas that greatly benefit from this include the product mould design part, the process, and material selection, the tooling part, and all the other important processes that are necessary for the process to be taken to completion. With MFA, there’s no room for trial and error, everything is first calibrated to the optimum levels, and once the machines start running, the desired results are what you bet at the end of it.
When you have all the parameters, the materials, and the tools necessary to make the exact product that you want, injection molding becomes a seamless operation. MFA is the best way to achieve this level of perfection, and some of the areas that benefit from the use of this software include the following.
Injection molding has a wide selection of raw materials to choose from, especially plastic. But the headache starts when you try to find the most ideal for a particular kind of task. With an MFA software in tow, you can be able to quickly narrow down to the best raw material to use by getting a quick preview of how each of them would look like. These simulations go a long way to ensure that there’s minimal wastage involved.
Cycle times are a production killer, and every manufacturer in the world tries to find solutions around that. The same problem is experienced in injection molding, and this can be countered by the mold flow analysis leading to the optimization of cycle times up to 30%. This can greatly reduce the cost of production in a very huge way, making things multiple molded parts at the same time.
When making use of the MFA, you are able to make the right choices about everything, saving yourself the time and resources that would have gone down the drain if you chose to go the long route and experiment with things first. This helps you to choose the right tools, the right raw materials on the spot. All these combinations of conveniences are what make MFA a very reliable tool to have and to use in the injection molding process.
MFA makes it possible for specifications to take place. This includes the machine specification, the cooling processes, the cycle times, the DOE, and other processes and parts that come together to ensure that the injection molding process is handled to the very end. The predictive abilities of the MFA make it easy to detect product design defects, give you solutions to correct the defects ahead of time, to save resources, significantly speed up the general cycle times, ang then provide better plastic injection molding service. This is a level of specification that makes it easy for each part of the entire injection molding process to blend with one another seamlessly.
Mold Flow Analysis software comes in varying types, and each is designed to handle some specific tasks in the injection molding process. There are many that are being used widely today, and finding the right one can be a tall task, but the following are the most popular ones that have been embraced by most manufacturers.
Moldex is a very intuitive and easy-to-use flow MFA software that has been around for quite a while, improving over the years to become one of the top-rated CAD-based software that’s loved by all kinds of injection molding manufacturers around the world. The software comes in two versions; Moldex eDesign and Moldex Solid. Some of the benefits include the following.
Moldflow is a CAD based software that is designed for creating part designs and providing simulations that manufacturers can use to correctly predict how the end product will turn out. It is easy to use and comes with an intuitive interface, and setting it up is very easy. The following are the benefits of using Moldflow.
Sigma is what you go for when you want to simulate the entire mold from top to bottom. Just like the other software, Sigma is easy to use, and the setup process is also straightforward; even a beginner can be able to configure it within hours. It gives the manufacturer the control and ability to simulate the entire product they are making, allowing them to see if there would be any defect that requires correction before the actual production begins. The following are the benefits of using Sigma.
Mold flow analysis is a very important tool that has revolutionized the way injection molding is conducted. As technology is being integrated into injection molding more and more, there is also an improvement in the MFA software, and there are a lot more being created every day to meet the growing demand for better products. For more information on injection molding, check out our website and have any questions you may have answered by our team of experts.
Please contact us using the form below or emailing (harry@fowmould.com)