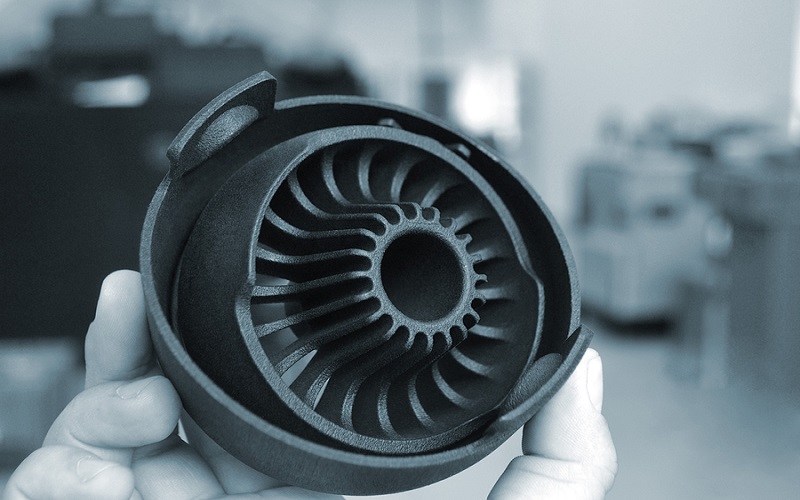
Share :
Share :
Injection molding is a procedure known for mass-producing plastic items in huge quantities. It’s most commonly utilized in procedures when the identical part is made thousands or millions of times in a row.
Over the years, the process has benefitted both manufacturers and buyers and it is considered a booming market because of its many advantages and high scope in the future.
This blog will focus on setting up an injection molding business by discussing the advantages and disadvantages of the process. So that you have an idea of setting up one and what factors are involved in it.
Injection molding is a method of producing a wide range of parts and objects from plastic. Even though the method was established in the nineteenth century, it is still one of the greatest ways to produce complicated parts while keeping costs down.
The molding machine can manufacture products according to desired specifications using custom-made molds, producing identical replicas that can be altered in a variety of ways.
Furthermore, injection molding is a very adaptable technique that can accommodate a wide range of materials and finishes, making it a popular choice across a wide spectrum of sectors with varying aims and criteria.
Injection molding machine production is used for some of the world’s most demanding manufacturing projects ranging from auto molds to home appliance plastic parts.
Plastic injection molding is a highly versatile way of creating plastic parts with several advantages over other plastic mold making technology. The technique is not only easier and more trustworthy than other approaches, but it is also quite efficient. Following are few advantages of this technique:
Plastic injection molding is known as the most prevalent and effective kind of molding for several reasons. In comparison to other ways, the procedure is exceptionally fast, and the high production output rate makes it even more efficient and cost-effective. The speed varies depending on the complexity and size of the mold.
Since the process has very little time between two cycles, a larger number of molds may be manufactured in a shorter length of time, potentially increasing the revenue and profit margins of the company.
Injection molding is capable of handling exceedingly complicated items and uniformity and the production of millions of nearly similar parts. Key design considerations should be considered to increase the efficiency of high-volume injection molding and the precision and quality of your products.
To maximize the efficiency of high-volume molding, the mould design must be carefully designed. Parts can be regularly produced and of high quality with the appropriate design.
According to molding professionals, certain key design aspects such as thickness, rib design, corner transitions, weld lines, and gate placement must be present during the injection process for it to perform well.
If tough and long-lasting parts are needed for a product, the plastic injection method is a unique alternative. In plastic injection molding, fillers can be used in the molds. The addition of fillers increases the strength of the molded item.
Regardless of the size of the generated parts, injection molded parts offer nearly infinite versatility.
The plastic within injection molds is pushed to more extent as compared to other molding methods because injection molds are subjected to extremely high pressures. Techniques like Computer-Aided Design (CAD) and Computer-Aided Manufacturing (CAM) also allow minute features and complicated designs to be incorporated into the part’s design and hence offer extremely tight tolerances. These factors generally depend on the part of the type of plastic used.
Plastic injection molding has been an automated process that uses machines for all types of work. During the process, computers and robots are controlled and managed by a single operator.
This automation aids in the reduction of production costs by lowering labor costs and thereby lowering overall overhead.
Furthermore, post-production labor is usually limited because the parts are usually extremely finished when they leave the factory.
One of the most important aspects of making plastic parts is selecting the correct material and color for the job. The choices are nearly unlimited due to the great variety of both. Over time, improvements in polymers have resulted in the development of a diverse range of resins from which to choose.
It’s critical to deal with an injection molder who has experience with a wide range of resins and applications. Factors like impact and tensile strength, modulus of elasticity, heat deflection, and water absorption are kept in mind while choosing a resin for a project.
A mold is required to start production using injection molding. Depending on the part’s size and geometries, making a mold can be costly. Mold can cost anywhere from a few thousand dollars to tens of thousands of dollars, depending on the intricacy of the mold.
To keep costs low, one can use soft molds made out of aluminum, which reduces the number of pieces that can be created before a new mold is needed. It is also recommended to outsource the mold-making process but it can lead to a slew of other issues.
Metal is used to make molds. Injection molds must be altered to make any changes to the final product. Making a part larger is as simple as removing extra material from the mold, and these alterations are commonly referred to as mold safe.
Changing the size of mold or deleting a feature necessitates re-inserting material into the mold, which is significantly more difficult, if not impossible. If you’re not sure about a part’s final dimensions or features, keep this in mind when designing it.
Before beginning manufacturing, you must first create the mold. This procedure should take anything from 5 to 12 weeks. If time is a constraint, proper management, and planning are required to carry out multiple tasks in less time. One can not deny that injection molding is the best place to start a plastic manufacturing business.
The plastic injection molding technique is an economical way for companies to reuse and optimize the already existing components. However, there are many factors that people consider before choosing an injection molding company as their supplier.
People think about bringing the best plastic injection molds to their company or replacing the current provider. Here are four crucial parameters and qualities for a good injection molding business:
A plastic injection molding service supplier should be able to achieve stringent industry manufacturing standards while also delivering the product on time. Most of the best injection molding companies follow a multi-step project design and development process and show people proof that their manufacturing method can match their requirements.
Furthermore, their manufacturing method should be able to consistently deliver high-quality products. People also inquire about ISO certification from a potential plastic molder, as this is an independent assurance that they satisfy industry quality requirements.
It is important to address some additional considerations with a competent plastic injection molding firm before choosing them. Consumers generally inquire about their injection molding experience and whether they can give any client referrals. It is also important to talk about their manufacturing capacity and delivery processes to see if they can meet your needs.
Locate a firm that can match the need for plastic mold components while also delivering them on schedule. The service provider should keep an open line of communication with you, their client, and address your demands at every turn. They should also be able to get the supplies they require for the plastic injection molding process without experiencing any delays.
As a result, it’s critical that your desired provider manages their workforce and handles customer jobs efficiently. This will assure on-time delivery and a high level of dependability for you.
It can be difficult to find a plastic injection molding firm that has a team of capable mold engineers. Mold engineers are important to produce the plastic components exactly as needed. A company with engineering expertise will be able to create plastic parts that will work flawlessly in a given application.
Furthermore, skilled specialists also assist consumers in determining the specifics of their project and managing it from start to finish.
While you can start a small-scale injection molding business with an investment lesser than $1 million, the odds of success are slim unless the company has a unique capacity to provide or builds a solid financial relationship with one or two customers.
Following are the preparation steps for opening an injection molding factory:
Make a firm commitment to a finished plan for the injection-molded plastic products your company will offer. The product’s dimensions and type of plastic will have a direct impact on the injection molding machine purchase selection.
Planning also involves determining how much funding is available for the injection molding plant’s startup, as this will have a direct impact on the size of the facility available and the size of the CNC injection molding machine your company can afford.
With the parameters for the types of final goods, you’ll need the machine to create, as well as the approximate budget available for production equipment. For this purpose, you should contact injection molding machines, industrial suppliers. The company can recommend which models are best suited to your organization’s demands.
To compare potential models, it is recommended to contact several companies. With all the options, you can decide which model your organization will purchase.
Obtain a production facility fit for the size and energy requirements of the model of injection molding machine your company has chosen by contacting a real estate agent with experience in industrial procurement. Place an order for an injection molding machine after selecting a production facility and finishing the lease or purchase agreement.
Obtain a contract from the best company bidding for the deal by contacting bulk plastic suppliers. Examine each supplier’s track record. A low bid will be useless if the company is unable to meet your raw material volume requirements.
Make several samples of your final injection molding products. Making these early samples will allow employees to become familiar with the machinery in a low-stress environment and work out any issues before starting the larger production runs. The samples will also be used as marketing prototypes for potential distributors. Now that the facility is up and running, it’s time to focus on marketing and production.
We hope that this blog helps you get insights into the scope of the injection mould design by exploring the advantages and disadvantages of the overall process. Several steps and parameters discussed should be kept in mind before grasping the opportunities as they are crucial for the success of your business.
Please contact us using the form below or emailing (harry@fowmould.com)