In our daily use of plastic bottles and takeaway boxes, we always find a plastic recycling symbol with a triangle of arrows on the bottom.
It’s not hard to notice that the symbols marked with “1” for PET and “5” for PP are especially common.
But what are the characteristics of these two materials? What differences exist between them? And which material is better?
In the following content, we will embark on a technical exploration of “PP vs PET” to find answers to these questions.
What Is Polypropylene?
Polypropylene, abbreviated as PP, is a thermoplastic resin made by polymerizing propylene.
It appears as a white, waxy material that is transparent and light, with a high melting point of 167°C.
Polypropylene is a non-toxic, odorless, tasteless, milky white highly crystalline polymer with a density of only 0.90–0.91 g/cm3, making it one of the lightest varieties among all plastics.
Based on the arrangement of the methyl groups, it is classified into three types: isotactic polypropylene, atactic polypropylene, and syndiotactic polypropylene.
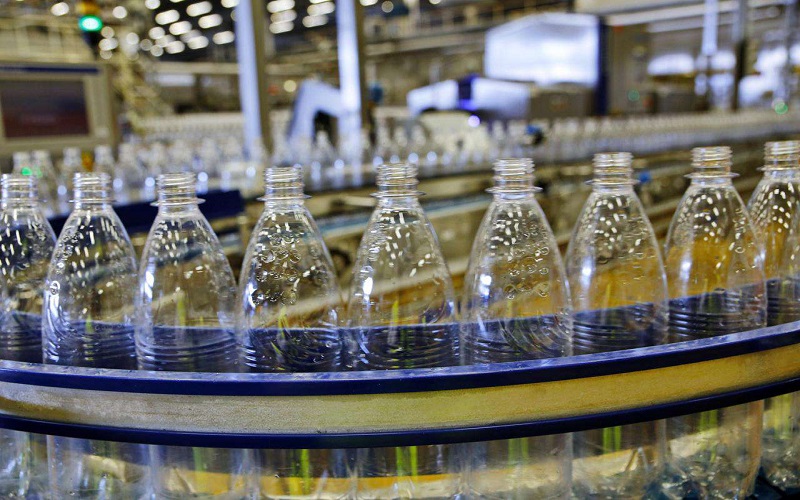
What Is PET?
Polyethylene Terephthalate (PET or PETE) is part of the polyester family of polymers and, together with PBT, is collectively referred to as thermoplastic polyester, or saturated polyester.
It is produced either through the transesterification of dimethyl terephthalate with ethylene glycol or by synthesizing bis-hydroxyethyl terephthalate through the esterification of terephthalic acid with ethylene glycol, followed by a polycondensation reaction.
Typically, it is a milky white or light yellow, highly crystalline polymer with a smooth and glossy surface.
It is a common type of resin encountered in everyday life and can be categorized into APET, RPET, and PETG.
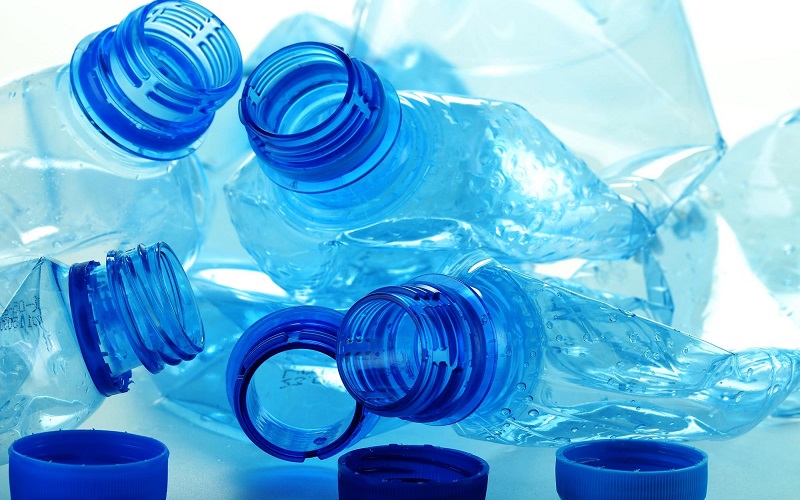
PP vs PET:Physical and Chemical Properties
To determine the quality of a material, it is first necessary to understand its properties.
Therefore, let’s introduce the characteristics of PP and PET from multiple aspects:
Mechanical Properties
PP exhibits excellent rigidity and resistance to flex fatigue. Hinges made from PP can withstand more than 70 million cycles of folding without breaking, although its impact strength at low temperatures is poor.
PET, on the other hand, has minimal wear and high hardness, possessing the greatest toughness among thermoplastic plastics. It has good creep resistance, fatigue resistance, and dimensional stability.
Thermal Properties
Polypropylene has good heat resistance.Polypropylene injection molding products can be sterilized at temperatures above 100°C.
Without external force, they do not deform at 150°C.
PET also has decent heat resistance, maintaining good physical and mechanical properties over a wide temperature range, with a service temperature of up to 120°C.
Chemical Stability
Polypropylene is very chemically stable. Except for being eroded by concentrated sulfuric acid and nitric acid, it does not react with most chemicals.
However, certain halogenated compounds, aromatics, and high boiling point hydrocarbons can cause it to swell.
PET material is resistant to weak acids and organic solvents but not to hot water soaking or alkalis.
Electrical Properties
PP has excellent high-frequency insulation properties. Because it hardly absorbs water, it also maintains good electrical insulation in humid environments.
Although PET has excellent electrical insulation properties, even at high temperatures and frequencies, its resistance to corona discharge is inferior.
Processing Characteristics
PP plastic has good processing characteristics and can be manufactured using various methods such as injection molding, extrusion molding, blow molding, and foaming.
PET resin, due to its slow crystallization rate, has poor processing performance and must be thoroughly dried before forming; otherwise, it can affect product quality.
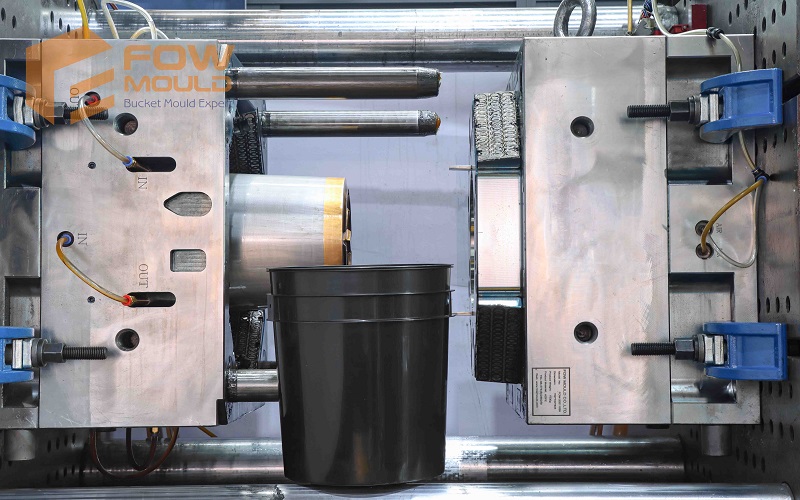
To clearly demonstrate the performance of PP and PET plastics, we have compiled a data table for your reference:
| PP | PET |
Chemical Formula | (C3H6)n | (C10H8O4)n |
Density (g/cm³) | 0.90 – 0.91 | 1.31 |
Melting Point (℃) | 164 – 170 | 250 – 255 |
Water Absorption (%) | 0.03 – 0.04 | 0.06 – 0.129 |
Tensile Strength (MPa) | 30.0 – 39.0 | 140 – 160 |
Bending Strength (MPa) | 42.0 – 56.0 | 70 – 100 |
Elongation at Break (%) | 200 – 400 | 50 – 150 |
PP vs PET:Pros And Cons
Polypropylene is valued for its lightweight, hygienic properties, and excellent heat and chemical resistance, making it suitable for food packaging and medical applications.
However, its susceptibility to weathering and lack of rigidity can limit its use in outdoor or structural applications.
PET , known for its high transparency and strong barrier properties, is ideal for transparent packaging and preserving the quality of consumables.
While PET boasts high mechanical strength and is recyclable, its sensitivity to heat and slow crystallization rate make it less suitable for high-temperature applications and can complicate the molding process.
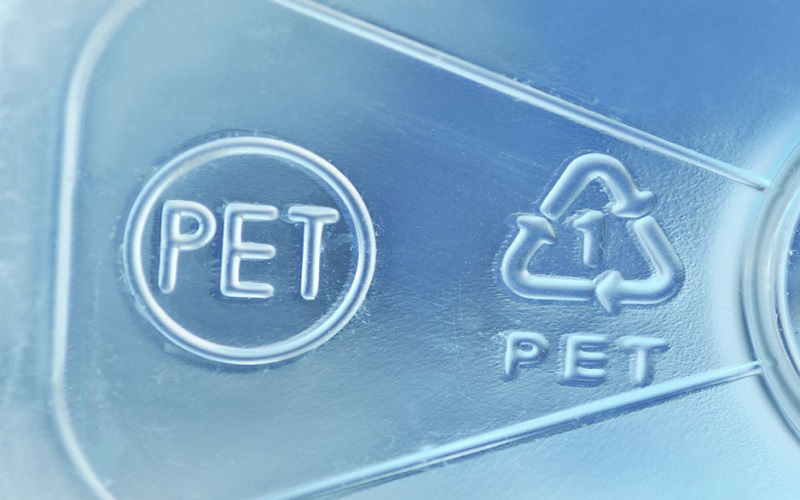
PP vs PET:Health and Safety Concerns
It is widely acknowledged that “1” PET and “5” PP are the principal materials used in our daily plastic products, which raises questions about their safety: Is pp plastic safe? Is PET toxic?
It is therefore crucial to thoroughly investigate the safety of these two materials to fully understand their impact on our health and well-being.
Initially, PP is odorless, tasteless, and non-toxic, generally considered a safe plastic material.
Under normal usage conditions, polypropylene does not leach harmful substances into food or beverages, making it a popular choice for food containers, baby bottles, and kitchen utensils.
PET material, on the other hand, is safe at room temperature. Its transparency and stability make it an ideal choice for beverage bottles and other packaging materials.
It’s important to note that both PP and PET are food-grade plastics, with PP being notably heat-resistant and the only plastic recommended for microwave heating.
However, PET bottles may leach harmful substances like DEHP when exposed to high temperatures, used for a prolonged period, or when containing overheated liquids.
Therefore, caution should be exercised regarding the usage conditions and duration when utilizing plastic products.
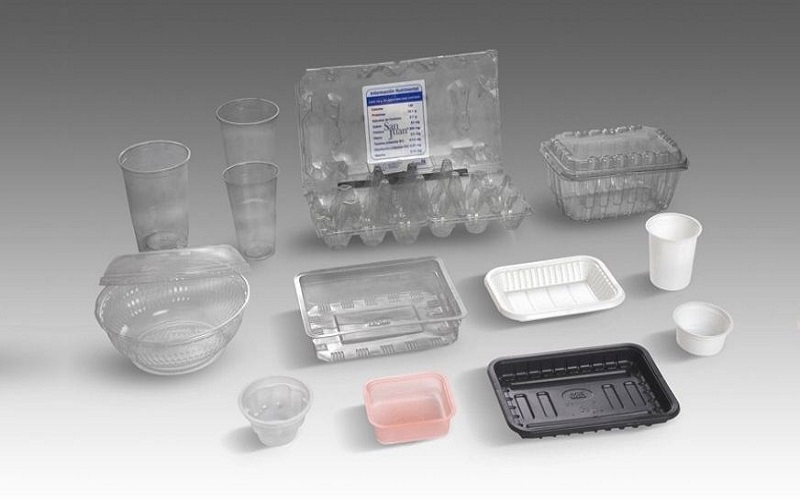
PP vs PET: Applications
PP resin consumed in woven products, such as plastic woven bags, tarpaulins, and ropes, has always accounted for a high proportion in China injection moulding enterprises.
PP injection-molded products are mainly used in small household appliances, daily necessities, toys, washing machines, automobiles, and turnover boxes.
Due to the excellent properties of polypropylene fibers, their application is increasingly widespread in decoration, industry, and apparel sectors, for example, in clothing and carpets.
PP pipes, known for their high-temperature resistance, easy pipe connection, and recyclability, are primarily used in buildings, agriculture, and chemical piping systems.
PET , on the other hand, is mainly used for bottle-grade polyester (widely used for packaging various beverages, especially carbonated drinks), polyester film (primarily for packaging materials, films, and tapes), and polyester fibers for textiles.
In addition, glass fiber-reinforced PET is suitable for the electronics, electrical, and automotive industries, used for various coil skeletons, electrical components, and electronic casings.
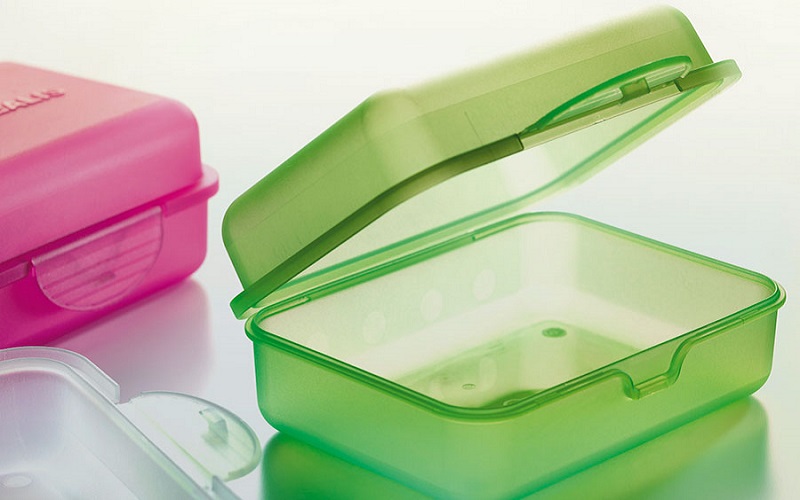
How To Choose Between PP and PET?
Under normal circumstances, PET material is more robust, durable, and heat-resistant compared to PP material.
For products that require higher durability, such as bottles and jars, PET material may be more suitable.
Additionally, PET material is more transparent than PP material, giving it an advantage in the production of transparent or semi-transparent products.
However, PP is softer, lighter, and easier to process and mold than PET.
For the production of soft and lightweight products, such as bags and clothing, PP material might be more appropriate.
Therefore, the question of which material, PP or PET, is better does not have an absolute answer; it depends on the specific requirements.
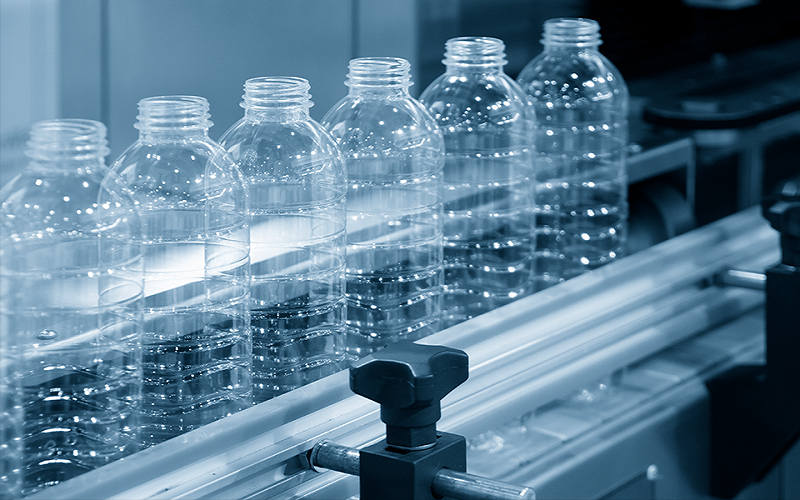