As two of the most produced plastics today, ABS and PVC are ubiquitous in our daily lives.
Whether in construction engineering, automobile manufacturing, or electronic product design, ABS and PVC play key roles.
However, choosing between these two materials for injection molding projects has become a focal issue for plastic manufacturing companies.
In the following content, we will compare in detail the composition, advantages and disadvantages of these two materials, as well as their outstanding performance in various fields.
In this regard, let’s watch this “ABS vs PVC” power competition!
What Is ABS?
ABS, standing for Acrylonitrile Butadiene Styrene, is a terpolymer made from the monomers acrylonitrile (A), butadiene (B), and styrene (S).
The manufacturing of ABS involves two methods: blending and grafting, resulting in ABS varieties such as medium-impact, high-impact, ultra-high-impact, and heat-resistant types.
Initially developed as a modification of PS plastic, ABS has emerged with the advantages of toughness, rigidity, and hardness.
Its usage is now on par with PS, but its application scope has far surpassed that of PS, making it an independent category of plastic.
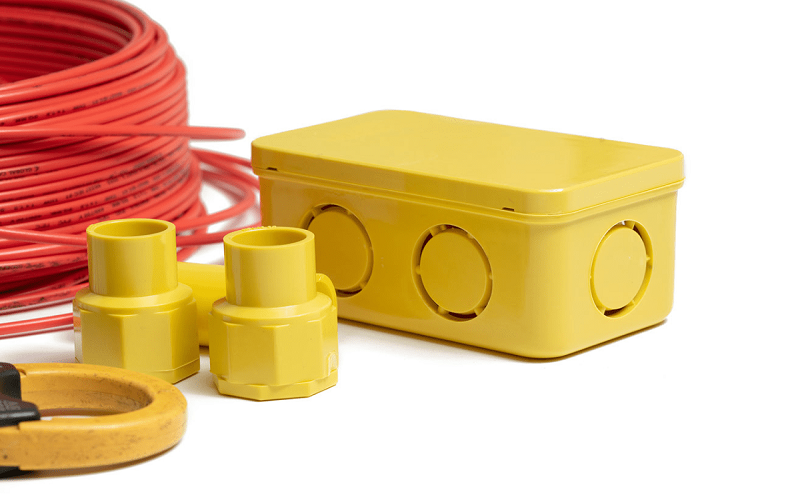
What Is PVC?
Polyvinyl Chloride, commonly abbreviated as PVC, is a polymer formed from the polymerization of vinyl chloride monomer through free radical polymerization reaction mechanisms, initiated by peroxides, azo compounds, or under the influence of light and heat.
Both homopolymers of vinyl chloride and copolymers of vinyl chloride are collectively referred to as vinyl chloride resin.
As China’s first and the world’s second-largest general-purpose synthetic resin material, PVC is distinguished by its excellent wear resistance, chemical corrosion resistance, comprehensive mechanical properties, electrical insulation, and ease of processing.
These characteristics have made PVC one of the most widely used plastic varieties in various application fields.
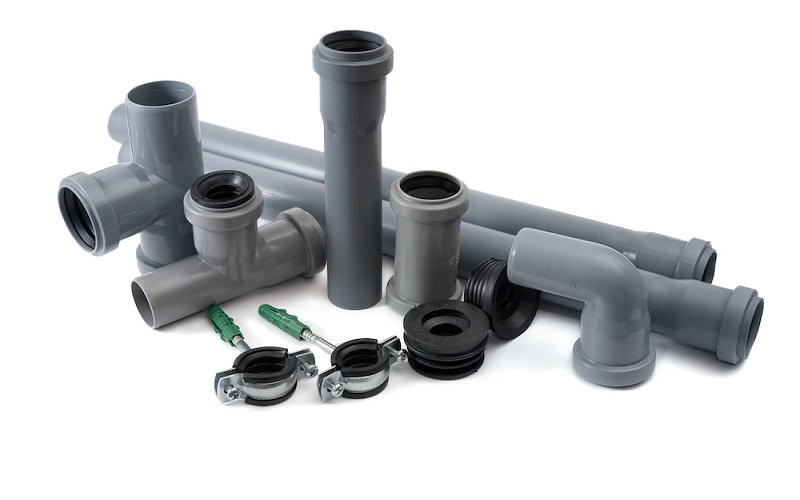
ABS vs PVC:Physical Properties
In evaluating ABS versus PVC , examining their unique physical properties is crucial to discern their suitability for different uses.
Below is an analysis of the essential physical characteristics of each material:
Property | ABS | PVC |
Density(g/cm3) | 1.02-1.08 | 1.38 |
Shrink rate (%) | 0.4-0.9 | 0.6-1.5 |
Melting Point(℃) | 170 | 212 |
Tensile Strength (MPa) | 30-50 | 60 |
Heat Deflection Temperature(℃) | 93-118 | 65-90 |
Young’s Modulus – Rigidity (MPa) | 2000 | 2900-3400 |
From the information provided, we can observe that ABS is characterized by its lower density and melting point, making it more suitable for applications that require lightweight materials and are easy to process.
In contrast, PVC stands out for its higher tensile strength and rigidity, making it appropriate for applications that demand higher mechanical strength and stiffness.
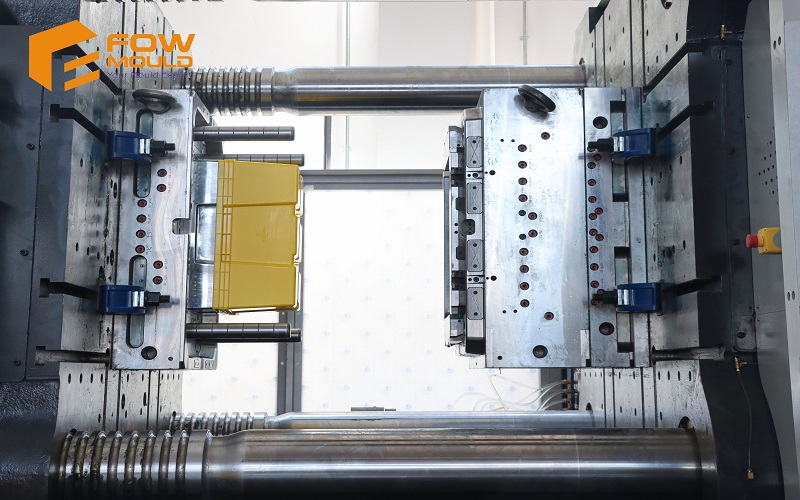
ABS vs PVC: Pros and Cons
When selecting the appropriate plastic material for our projects, ABS and PVC stand out as two common options.
Here’s a brief analysis of their pros and cons to understand their suitability in various application scenarios.
Pros of ABS
Colorability: ABS is opaque and ivory-colored, can be dyed in various colors, and has a high gloss, making it suitable for applications requiring an attractive appearance.
Good Mechanical Properties: ABS exhibits excellent wear resistance, dimensional stability, and oil resistance, making it suitable for bearings under medium load and speed.
High Heat Resistance: With a higher thermal deformation temperature than PA and PVC, ABS can be used long-term in temperatures ranging from -40°C to 85°C.
Cons of ABS
ABS has a high melt viscosity and poor flowability, with reduced weatherability, and is prone to discoloration under UV light.
Additionally, ABS can dissolve in ketones, aldehydes, and chlorinated hydrocarbons, and is susceptible to stress cracking when exposed to ice acetic acid and vegetable oils.
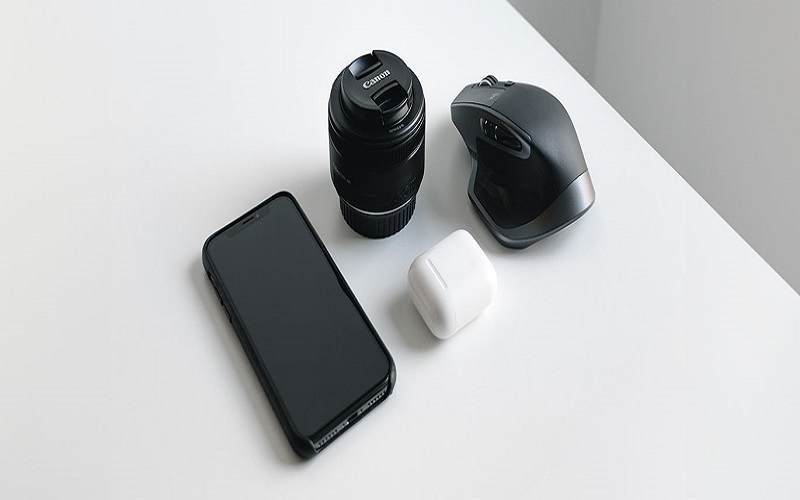
Pros of PVC
High Flame Retardancy: With a flame retardancy value over 40, PVC is suitable for environments requiring high safety standards.
Chemical Resistance: PVC can withstand strong corrosive chemicals such as concentrated hydrochloric acid, up to 90% sulfuric acid, 60% nitric acid, and 20% sodium hydroxide.
Strong Stability: Insoluble in water, alcohol, and gasoline, PVC has low gas and vapor permeability and can resist various concentrations of acids and alkalis at room temperature.
Cons of PVC
PVC has poor stability against light and heat.
UV rays and oxygen can cause photo-oxidative degradation of PVC, leading to a loss of flexibility and eventual brittleness.
This is why some PVC plastics become yellow and brittle over time.
Moreover, the processing of PVC heavily relies on the addition of stabilizers, lubricants, and processing aids, as PVC resin powder cannot be directly processed into any product without plastic additives.
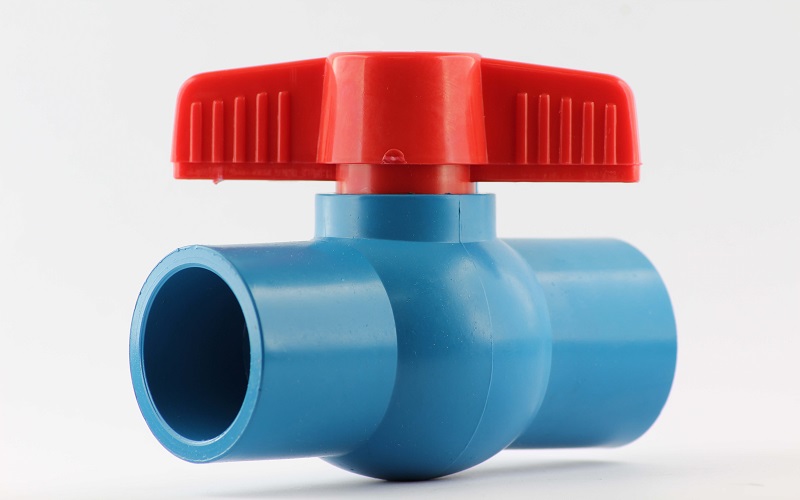
ABS vs PVC: Applications
After exploring the pros and cons of ABS and PVC , it’s intriguing to consider where these plastics are utilized.
This section outlines the primary applications and examples of these two polymers, showcasing their extensive impact on the plastic manufacturing industry.
ABS injection molding is known to be well suited for products with complex designs and high gloss surface requirements.
These include automotive parts (dashboards, interior trim and door handles), electronics housings (cell phones, remote controls and computer housings) as well as toys (Legos) and kitchen appliances.
At the same time, ABS is one of the most versatile materials available for 3D printing today.
Objects printed with ABS have slightly higher strength, flexibility and durability.
It is also a great material for prototyping and can be easily machined, sanded, glued and painted.
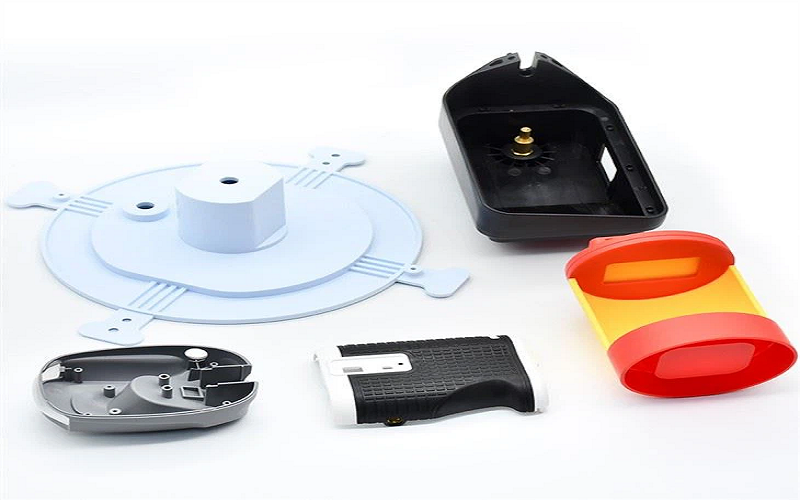
Despite PVC’s slightly inferior flow properties compared to ABS, it performs admirably in specific applications.
PVC piping is a staple in both industrial and residential plumbing, offering robust waterproof and corrosion-resistant solutions.
In the construction sector, PVC is frequently used for doors, windows, and as an energy-efficient material.
Thanks to its low production cost and ease of molding, PVC injection-molded products are prevalent in everyday consumer goods like plastic sandals and sports equipment, as well as in medical devices, including disposable medical instruments.
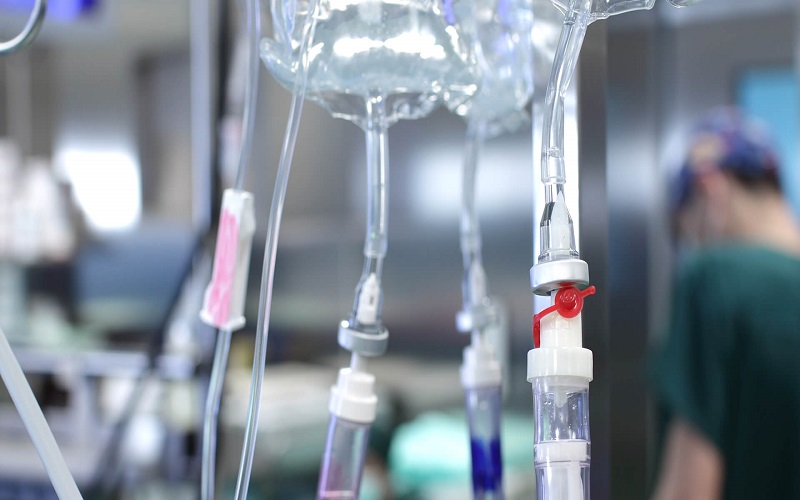
ABS vs PVC: Safety Concerns
As plastic products become increasingly common in everyday life, public concerns about product safety are growing.
Therefore, the discussion on the ABS plastic safety and PVC safety is becoming increasingly intense.
PVC itself is non-toxic and odorless, posing no irritation to human skin or the respiratory system.
However, the plasticizers added to enhance the flexibility of flexible PVC products, especially phthalates, may pose potential health risks.
On the other hand, ABS produced according to standard processes does not contain harmful heavy metals or plasticizers, making it relatively safer for use in toys and food-contact products.
It is worth noting that ABS releases toxic gases such as acrylonitrile and styrene when burned, so avoiding burning ABS in poorly ventilated environments is crucial.
A drawback of PVC is its poor thermal stability.
If products are left in high temperatures and direct sunlight for extended periods, they may decompose and release harmful hydrogen chloride gas, posing a threat to human health.
Therefore, when considering the use of PVC or ABS, it’s essential not only to take into account their physical and chemical properties but also the usage environment and safety requirements to ensure human health and environmental safety.
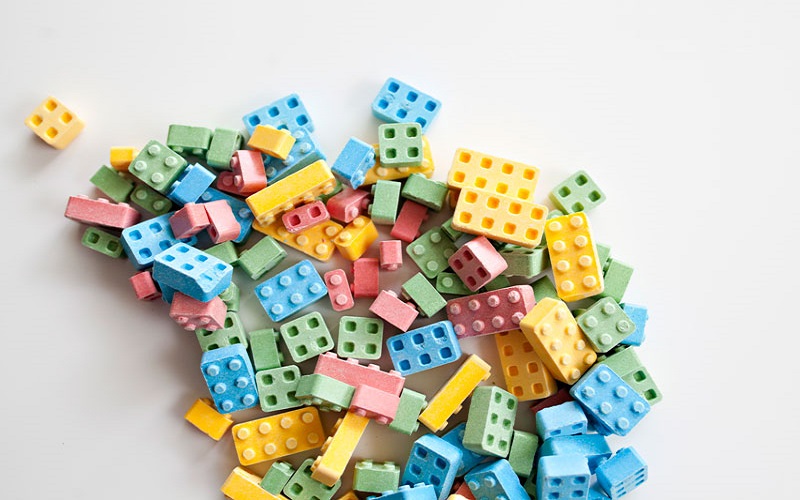
Conclusion
In summary, ABS and PVC each possess unique characteristics and versatile applications.
ABS is renowned for its toughness, impact resistance, and suitability for consumer electronics, automotive components, and toys, making it the preferred choice for applications demanding aesthetics and strength.
On the other hand, PVC’s stability and durability make it an effective solution for use in construction and medical devices, offering a reliable option for long-term stable use.
Choosing between ABS and PVC depends on the specific requirements of the application, with a need to balance factors such as mechanical properties and safety.
If you are seeking further advice on injection molding materials, please contact us!
FOWMOULD will be your most trustworthy injection molding expert.
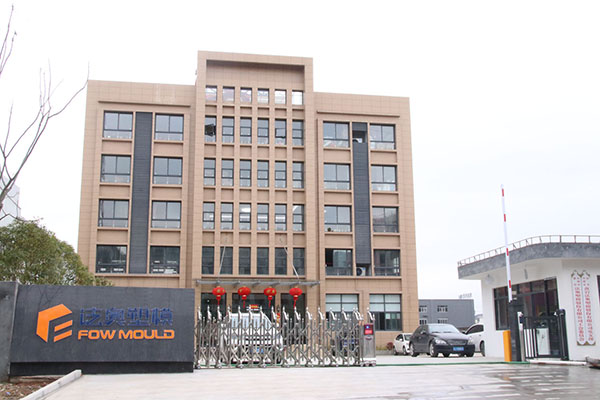