In modern manufacturing, the application of glass filled nylon injection moulding technology is becoming increasingly widespread, becoming an indispensable part of many industrial and consumer product manufacturing processes.
This article aims to comprehensively introduce the specifics of using glass filled nylon in the injection molding process.
By exploring the unique properties of glass filled nylon, we will understand how to effectively utilize this material for injection molding
What Is Glass Filled Nylon?
Glass-filled nylon is a composite material made by combining nylon with short glass fibers.
Polyamide, commonly known as nylon and abbreviated as PA, is a crystalline polymer characterized by its strong polarity, tendency to form hydrogen bonds between molecules, and reactive nature under specific conditions.
It possesses excellent mechanical properties, including wear resistance, oil resistance, self-lubrication, good moldability, and corrosion resistance.
However, the strong polarity of PA leads to high water absorption, which affects its electrical properties and dimensional stability.
Additionally, PA’s heat resistance and low-temperature impact strength could be improved. You can explore more about nylon injection molding here.
This material leverages the excellent inherent qualities of nylon and enhances its overall performance by embedding short glass fibers.
Adding 30% glass fibers to nylon significantly improves its mechanical properties, dimensional stability, heat resistance, and aging resistance, with fatigue strength being 2.5 times that of unreinforced nylon.
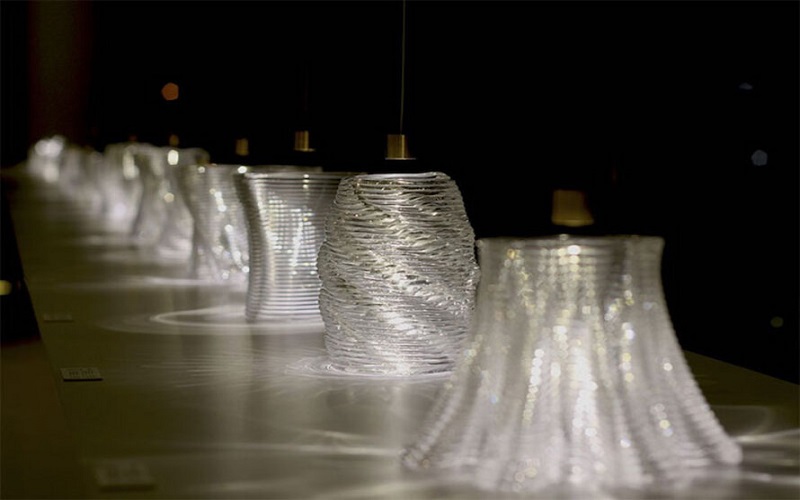
Properties of Glass Filled Nylon Materials
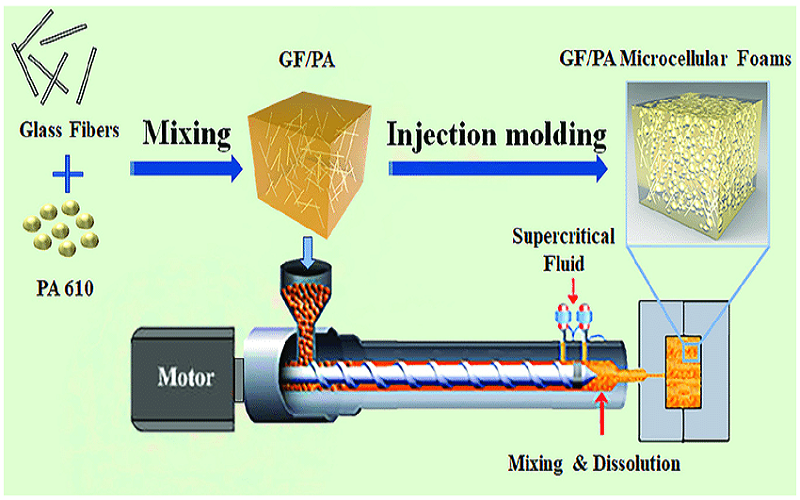
Glass-filled nylon has characteristics that improve upon the limitations of pure nylon material.
Pure nylon has significant moisture absorption, poor dimensional stability, and undergoes a glass transition around 120°C, limiting its continuous-use temperature to only around 105°C.
However, glass reinforced nylon materials can overcome these drawbacks.
They can reduce the water absorption rate of nylon granules, enabling them to function in high temperature and high humidity environments.
Additionally, they further enhance surface hardness, tensile strength, bending strength, and wear resistance.
For instance, 30% glass fiber-reinforced Nylon-6 and Nylon-66 have tensile strengths of around 170 MPa, surpassing common light metals like zinc and magnesium, and are close to aluminum.
The table below displays the performance characteristics of glass-filled polyamide composites (Nylon 66 with 30% glass fibers).
Density | 1.34g/cm³ |
Melting point | 260°C – 280°C |
Tensile strength | 170 – 230 MPa |
Modulus of elasticity | 7,000 – 10,000 MPa |
Heat deflection temperature | 250°C – 280°C |
Water absorption | 1.2% – 2.5% |
Advantages of Injection Molded Glass Filled Nylon
Injection molded glass-filled nylon offers a range of advantages, making it a popular choice for a variety of industrial and consumer applications.
Increased Strength and Rigidity
The addition of glass fibers significantly enhances the strength and rigidity of nylon plastic, making it an ideal choice for parts that require high structural integrity.
Additionally, its tensile strength is close to its yield strength, which is more than double that of ABS plastic.
Improved Thermal Stability
Compared to pure nylon, glass-filled nylon has better thermal stability, with the heat deflection temperature increased to 250°C (for reinforced Nylon-66) under a load of 1.86 MPa.
This means it can withstand higher temperatures without deforming.
Enhanced Wear Resistance
This material is more wear-resistant and impact-resistant than standard nylon, beneficial for parts that need to endure mechanical stress or friction.
Lower Moisture Absorption
After fiber reinforcement, nylon’s water absorption rate is reduced, enabling it to function in high temperature and high humidity environments, and improving the dimensional stability of glass-filled nylon plastic products.
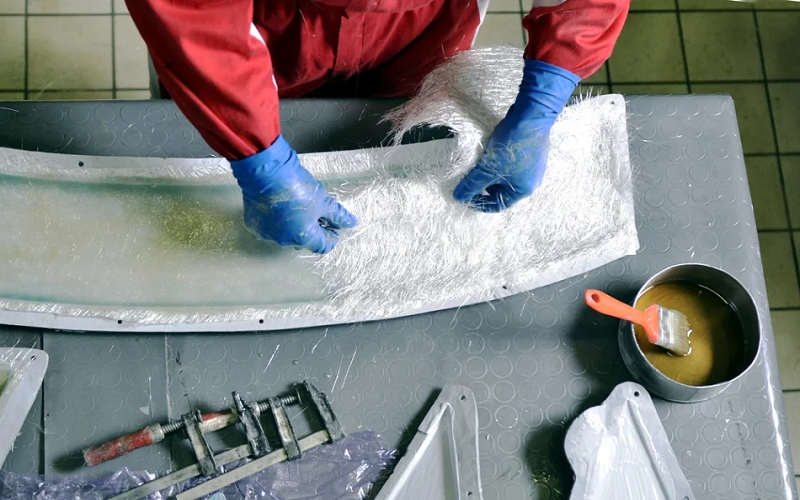
Limitations of Glass Filled Nylon Injection Molding
Despite the many advantages of glass filled nylon, there are still some limitations during the injection moulding process of this material.
During glass filled nylon molding, glass fibers can protrude onto the surface of the plastic product, causing a rough surface and leaving defects such as stray fibers and bloom.
To avoid these issues, plastic additives can be used to improve the compatibility between glass fibers and resin, reducing the separation of fibers from the resin and thus minimizing the exposure of fibers.
Additionally, glass fibers tend to orient along the flow direction during injection, enhancing mechanical properties and shrinkage in that direction, which can lead to product deformation and warping.
To counter this, the design of the mold should consider the placement and shape of the gates reasonably. Technically, increasing the mold temperature and slowly cooling the product in hot water after removal can help.
Finally, the higher the proportion of glass fibers added, the greater the wear on the plasticizing elements of the injection molding machine.
It is advisable to use bimetallic screws and barrels for better durability.
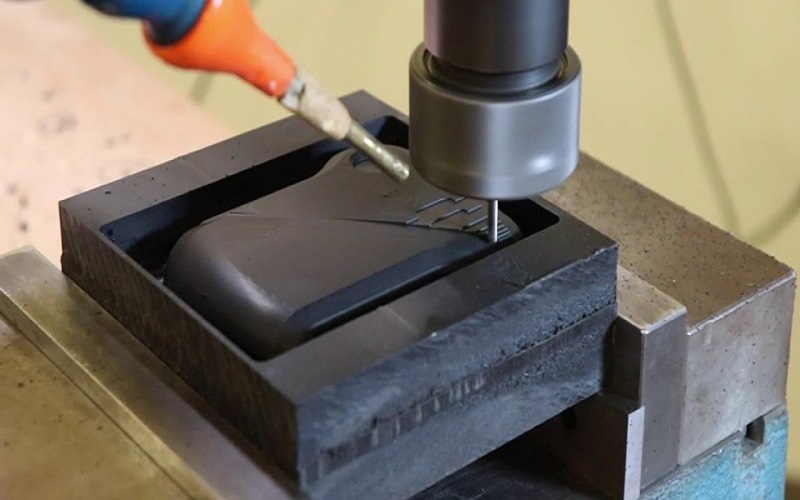
Injection Molding Glass Filled Nylon Process
In the glass-filled nylon injection molding process, nylon is first blended with glass fibers to enhance its strength and durability.
During this process, the nylon is melted into a liquid state.
This molten glass filled nylon is then precisely injected into the cavity of a specially designed double-sided mold to form the required shape.
After the nylon cools and solidifies within the mold, the finished part is ejected and collected in a bin, ready for any necessary post-processing, such as trimming or polishing.
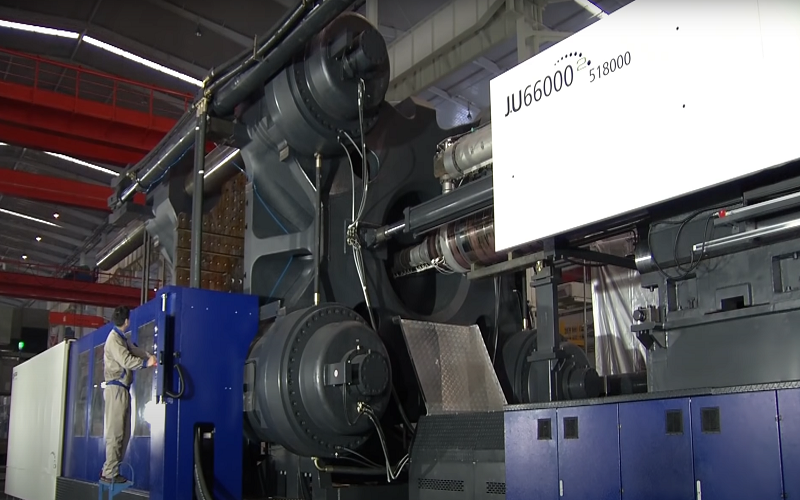
“Floating Fiber” Problem In Glass-Filled Nylon Molding
The issue of “fiber float” in glass-filled nylon injection molding, where glass fibers become exposed on the surface of the finished product, forming white, rough, radiating marks that degrade surface quality, several measures can be taken.
The reason behind fiber float is the incompatibility and different densities of glass fibers and plastic, which tend to separate.
The plastic melt accumulates on the surface due to friction from the screw, nozzle, runners, and gates during flow, and glass fibers promote crystallization in the crystalline material of nylon.
Rapid crystallization leads to quick cooling; quick cooling makes it hard for resin to bind and cover the glass fibers, leading to exposure.
To solve this problem, three main approaches are generally adopted:
Improve Compatibility Between Nylon and Glass Fibers
Adding compatibilizers, dispersants, and lubricants to the material can enhance the compatibility between glass fibers and nylon resin.
This improves the uniformity of the dispersed phase, increases interfacial bond strength, and reduces the separation of glass fibers from the resin, thereby mitigating the exposure of fibers.
Increase Mold Temperature and Injection Speed
Raising the mold temperature significantly enhances the reduction of resistance during melt flow, preventing the accumulation of glass fibers.
Increasing the injection speed can reduce the relative velocity difference between glass fibers and resin, further lowering the likelihood of fiber accumulation.
Reduce Screw Speed
When plasticizing glass fiber-reinforced plastic, the screw speed should not be too high to avoid excessive frictional shear forces that exacerbate the fiber float phenomenon.
This is particularly crucial when using longer glass fibers, as partial breakage can lead to uneven lengths, resulting in inconsistent strength throughout the part and unstable mechanical properties of the product.
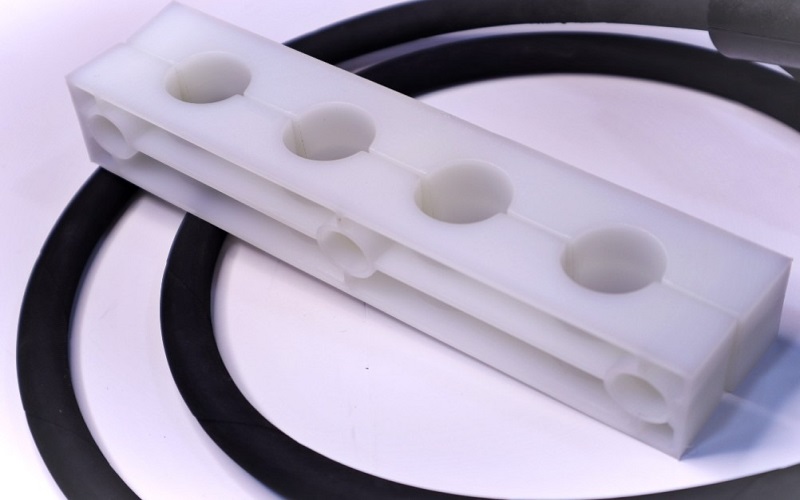
Applications For Glass Filled Nylon Injection Molding
Using glass-filled nylon in injection molding projects enhances the wear resistance of parts and improves their chemical resistance (except when exposed to strong acids and bases).
Therefore, it is often used for manufacturing robust and durable parts, making it an ideal choice for functional prototype designs and end-use applications.
Here are some of the main application areas for glass-filled nylon injection moulding:
- Construction
- Production Equipment
- Electrical Components
- Automotive Parts
- Aerospace Components
Additionally, glass-filled nylon is also a commonly used material in 3D printing .
The molding of nylon can be achieved through various 3D printing technologies, with the choice of technology depending on the requirements of the molding process and the final use of the parts.
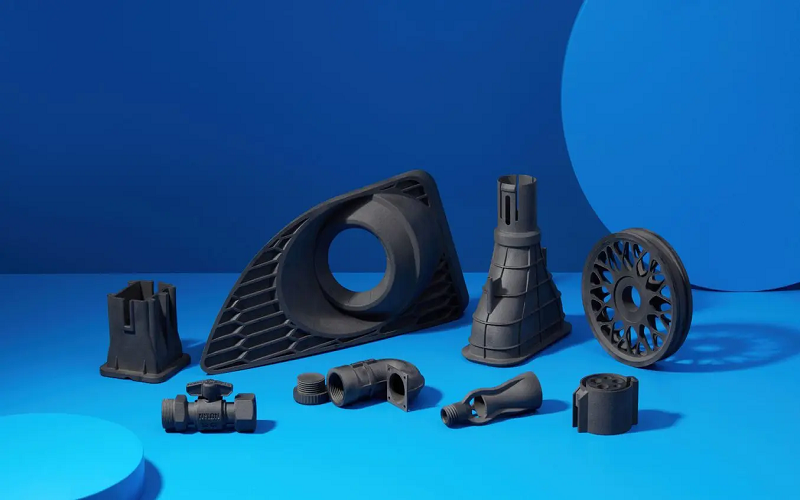
FOWMOULD's Plastic Injection Molding Service
As a leading enterprise in the injection molding field in China, FOWMOULD is committed to providing customers with one-stop injection molding services.
FOWMOULD’s physical factory is equipped with the latest injection molding equipment and houses a diverse team of professional designers and engineers, capable of offering efficient and professional production services.
In addition to this, FOWMOULD also undertakes customized projects using thermoplastic materials.
For injection-molded parts that require extremely high rigidity and strength, FOWMOULD offers glass-filled nylon as a material option.
If you are looking to start a project with glass-filled nylon injection molding, please contact us. FOWMOULD will be your best partner!
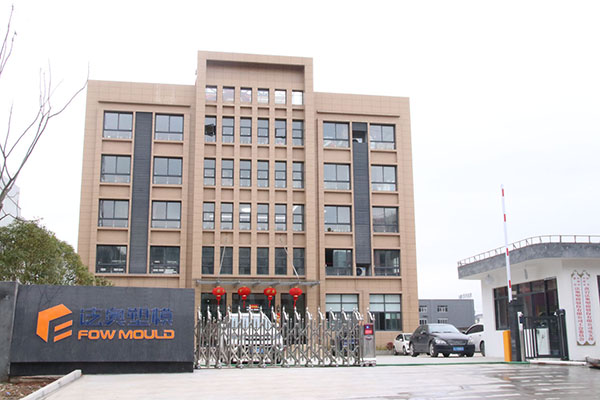