In the modern manufacturing sector, selecting the right material is crucial.
This is especially true when comparing PC-ABS alloy with ABS plastic two widely used materials, where understanding their differences is particularly important.
Although these materials share similarities in chemical composition, they exhibit significant differences in mechanical strength, heat resistance, and processing ease.
This article aims to delve deeply into the key performance differences between PC/ABS and ABS, providing clear guidance for clients looking to embark on new injection molding projects when faced with material choices.
What Is PC-ABS?
Polycarbonate is an outstanding thermoplastic engineering material known for its high temperature resistance, flame retardancy, excellent electrical insulation, and non-toxic, odorless nature.
However, pc plastic material also has its limitations, including high melt viscosity, poor flowability, a tendency towards stress cracking, weak resistance to organic chemicals, and a relatively high cost, which restrict its application in various fields.
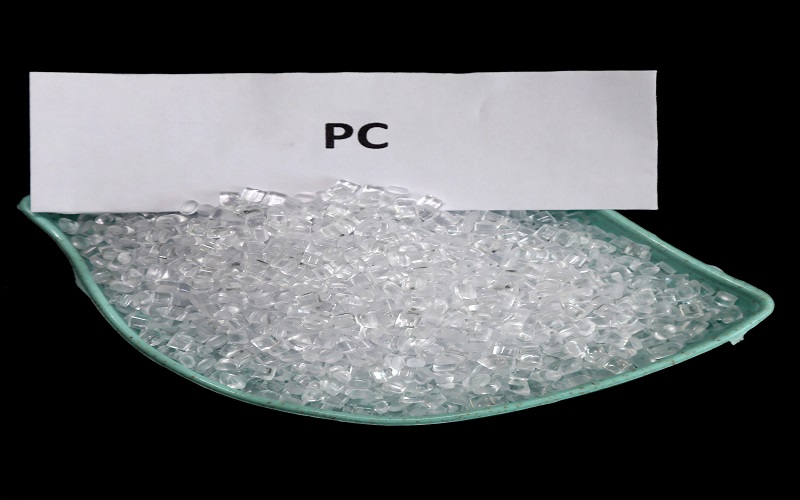
Acrylonitrile-Butadiene-Styrene (ABS) plastic combines the properties of three different monomers.
It exhibits good low-temperature impact resistance, chemical resistance, and moldability, and is comparatively affordable. Despite its advantages, abs plastic does have shortcomings in terms of flame retardancy, high-temperature resistance, and weatherability.
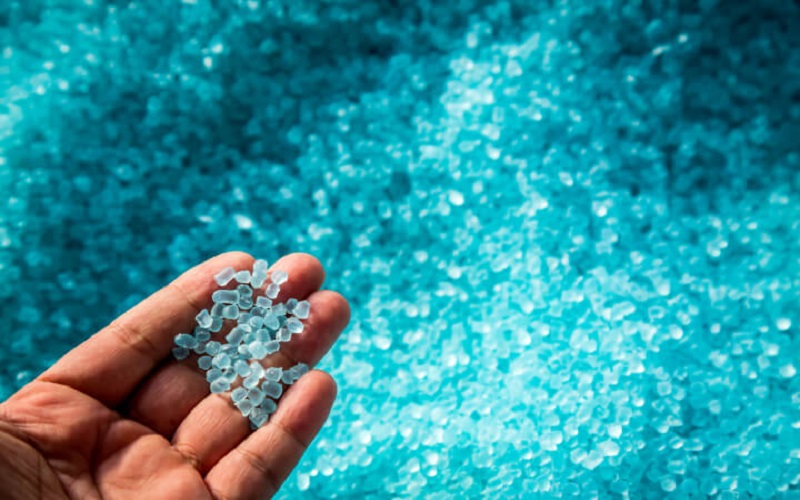
Therefore, there’s a growing interest in blending to enhance its properties and expand its application range.
PC/ABS, a combination of polycarbonate and acrylonitrile-butadiene-styrene copolymer and blend, is a thermoplastic plastic derived from the merging of polycarbonate and abs.
It amalgamates the superior qualities of both polymers, addressing some of the performance deficiencies present in PC and ABS.
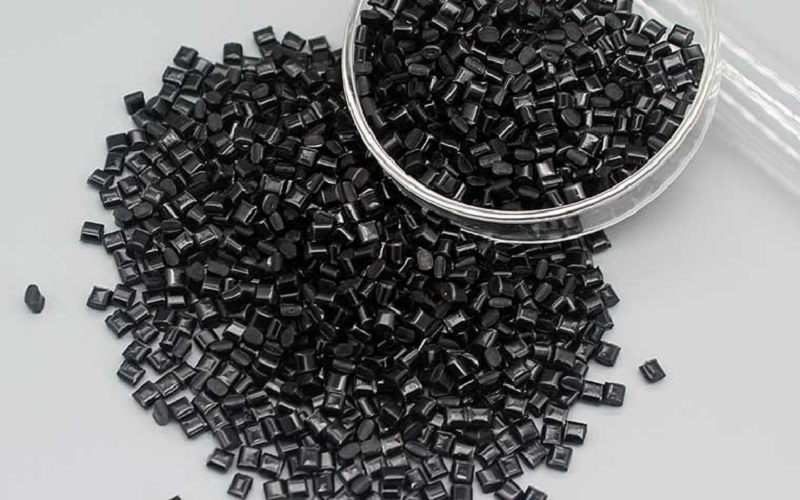
What Are The Properties Of PC-ABS Materials?
PC-ABS is a modified engineering plastic synthesized by blending. PC is polycarbonate and ABS is a copolymer of acrylonitrile (A), butadiene (B) and styrene (S).
Compared to pure PC, PC/ABS alloys have improved flowability and better processing performance, with reduced sensitivity to stress in the products;
Compared to pure ABS, PC/ABS exhibits significantly enhanced mechanical properties, heat resistance, and flame retardancy.
Here are some of the key properties of PC-ABS materials:
- general density is 1.05-1.20g/cm3
- high impact, high heat resistance, flame retardant, reinforced, transparent and other levels
- mobility is a little worse than HIPS, better than PMMA, PC, etc., good flexibility
- Excellent balance of mechanical properties
- Indoor UV stability
- Higher heat distortion temperature (80 ~ 125 ℃)
- Flame resistance (UL945VB)
- Good plating properties
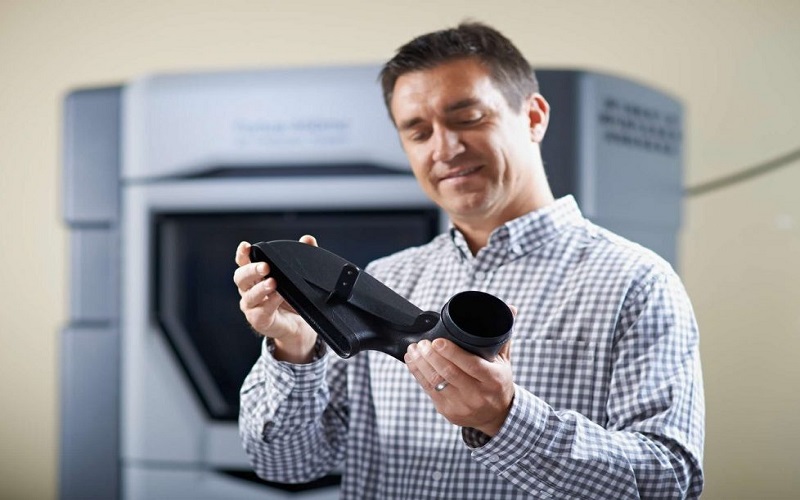
Some Disadvantages Of PC-ABS Plastic
Cost Comparison
In terms of cost, PC-ABS material is more expensive than either PC or ABS alone, offering better performance at a higher price.
It is costlier than ABS, which can be a significant consideration for cost-sensitive projects. However, it is less expensive than pure PC.
Therefore, for applications that require performance superior to ABS but cannot afford the cost of pure PC, PC-ABS emerges as a more economical choice.
Strength Characteristics
Regarding material strength, PC-ABS cannot match the robustness of pure PC. This limitation may be significant in applications that demand the utmost strength and rigidity.
However, compared to ABS, PC-ABS does offer markedly improved performance. Hence, it is a suitable option for applications that need to strike a balance between strength and cost.
Poor Flowability
One notable drawback of PC-ABS is its flowability, particularly when compared to ABS.
This reduced flowability can make the material more challenging to process, especially in complex mold designs or situations where high detail is required.
In such cases, there might be a need to adjust the processing parameters or even reconsider the mold design to accommodate the material’s characteristics.
This aspect of PC-ABS necessitates careful consideration in terms of manufacturing feasibility and design adaptability.
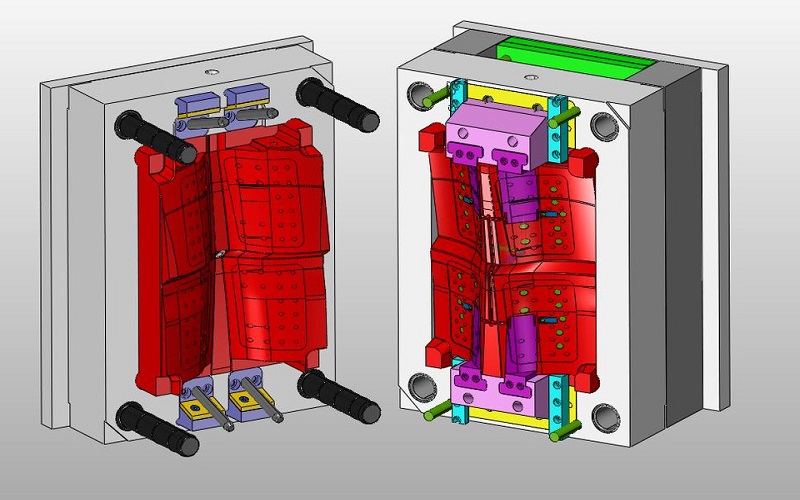
Performance Of ABS and PC-ABS In The Machining Process
ABS is renowned for its ease of processing and molding, favored by manufacturers due to its relatively low requirements for temperature and pressure during the manufacturing process. (Refer to “ABS Injection Molding” for injection parameters.) However, during the injection molding process, ABS components are particularly prone to cracking and warping, limiting their use in applications where dimensional stability and structural integrity are crucial.
On the other hand, PC-ABS, a blend that combines the comprehensive characteristics of Polycarbonate and ABS, possesses better mechanical properties, enhanced temperature resistance, and UV protection capabilities.
However, due to its higher melting point and sensitivity to processing conditions, machining PC-ABS can be more complex, requiring precise control during the manufacturing process. Thanks to the thermal stability of PC, warping in PC-ABS tends to be less than in ABS.
Therefore, when choosing between ABS and PC-ABS, it’s important to balance factors such as strength, heat resistance, and ease of processing, based on the specific requirements of the application.
PC-ABS Injection Molding Parameter Table | |||
Drying temperature | 90~110℃ | Drying time | 2~4h |
Melting Temperature | 230~300℃ | Mold Temperature | 50~100℃ |
Injection Pressure | 50-150MPa | Injection Speed | Fast |
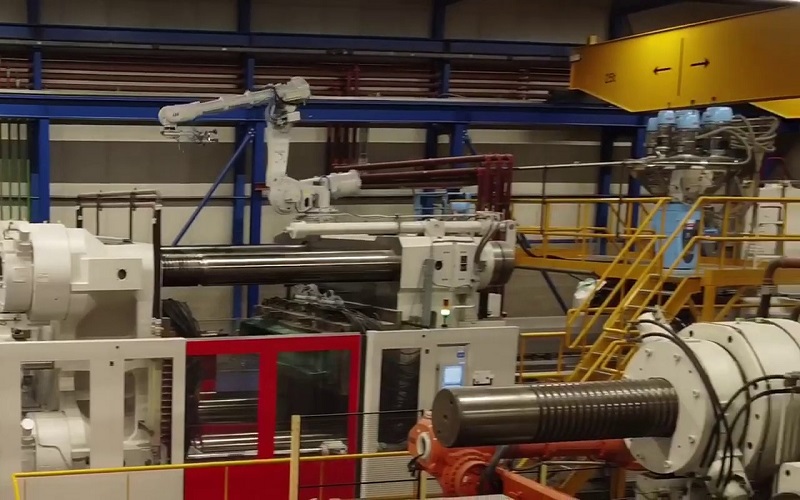
What Are The Common Applications Of PC-ABS?
ABS is widely used in the manufacturing of lower-quality components and toys due to its ease of processing and cost-effectiveness.
However, its limitations in strength and durability often restrict its use in more demanding, critical applications. PC/ABS, a blend of Polycarbonate and ABS, fills the gap where higher performance is required.
This material is commonly used in the manufacturing of components for electronics, automotive, and medical equipment,
where enhanced strength and flame retardancy are crucial.
The use of PC/ABS in these sectors is driven by the need for materials that can withstand harsher conditions and provide higher reliability, especially in safety-critical components.
PC/ABS alloys, known for their high transparency, strength, and wear resistance, are widely used in electronics.
They are typically used to manufacture the casings and internal structural components of laptops, mobile phones, tablets, and other devices.
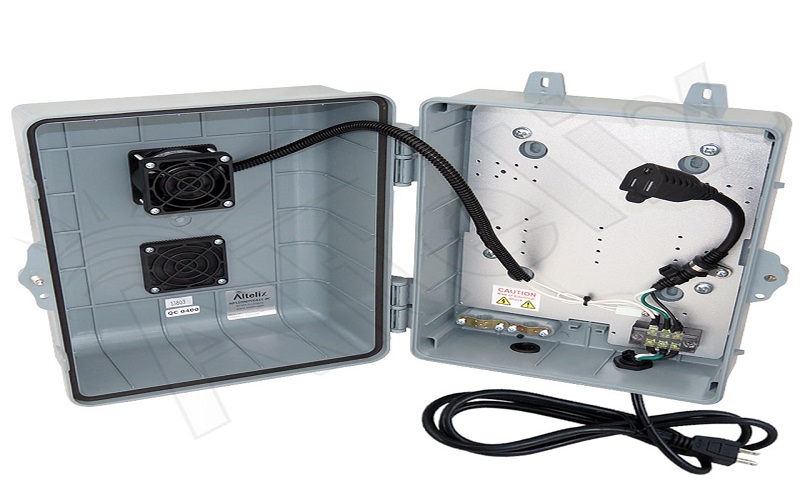
In the automotive industry, “Plastics instead of steel” has become the best solution to address the requirements of the automotive industry, and PC/ABS alloys are an important part of this.
The high strength, impact resistance, and dimensional stability of PC/ABS alloy materials make them ideal for manufacturing various car parts.
Components like bumpers, doors, and seats can be made using PC/ABS material.
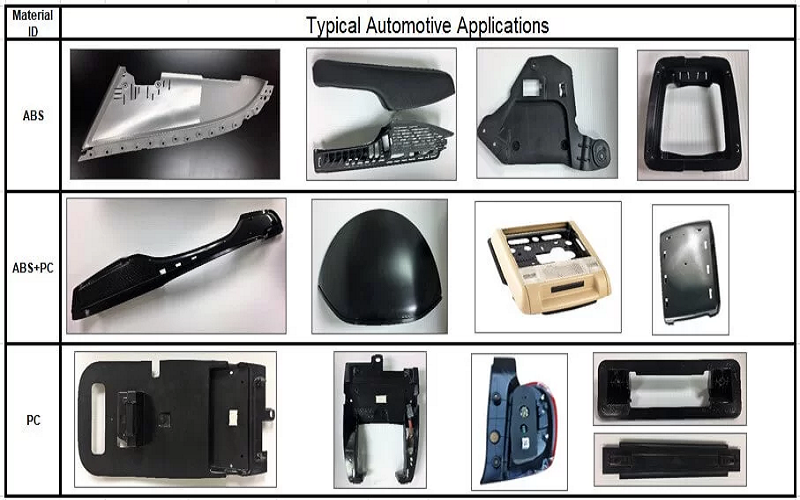
Additionally, PC/ABS alloy materials are also used in building materials, such as doors, windows, and glass curtain walls.
Conclusion
Both PC-ABS and ABS are very important materials in the thermoplastics field, and they play different roles depending on their unique properties and application environments.
If you want to know more about injection molding materials, please contact us.
FOWMOULD will provide you with a comprehensive range of plastic materials and professional one-stop injection molding services!