In the modern industrial field, the selection of materials has a significant impact on the performance and application range of products.
In recent years, polyphenylene sulfide (PPS) plastic, as an excellent alternative material, is leading an application revolution in various fields, making PPS the best substitute for metal materials.
Next, let’s delve into the main content of PPS injection molding together.
What Is Polyphenylene Sulfide?
Polyphenylene sulfide, abbreviated as “PPS”, is a crystalline new high-performance thermoplastic resin with phenyl sulfide groups in its molecular chain.
PPS has a density of 1.34 grams per cubic centimeter, with benzene rings and sulfur atoms alternating in a highly regular arrangement.
The benzene rings provide rigidity, while the sulfide bonds offer flexibility.
The molecular main chain possesses both rigidity and flexibility, facilitating crystallization with a crystallinity of up to 75% and a melting point of 285°C.
PPS plastic was initially discovered as a byproduct of a reaction in 1888, but it wasn’t until 1968 that Phillips Petroleum Company in the United States developed an industrial production process.
Further research and improvement enabled the maturation of PPS.
In 1973, PPS was officially produced on an industrial scale and was widely applied in various fields.
Notably, due to its inherent flame retardancy, PPS was identified by the National Aeronautics and Space Administration (NASA) as one of the optimal flame-retardant plastics, chosen as a specialized material, and even found applications in the aerospace field.
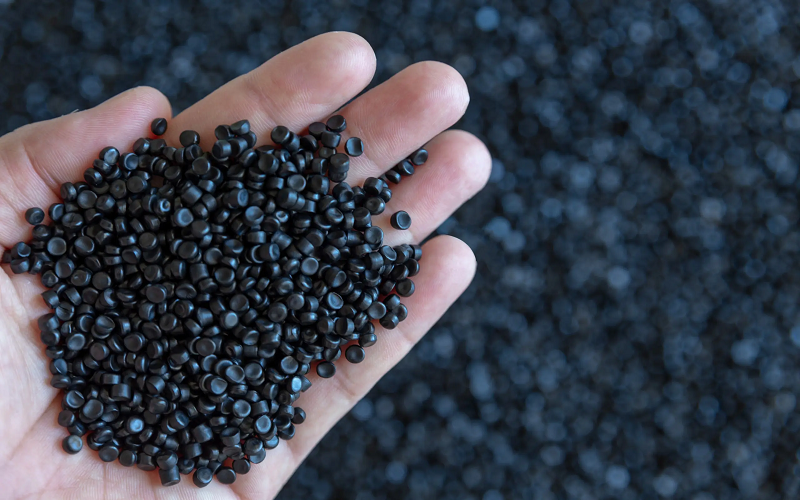
What Are The Properties Of PPS Material?
Due to the special molecular structure, polyphenylene sulfide inherently obtains excellent comprehensive performance.
High-Temperature Resistance
The melting point of PPS can reach 275~291℃, and its heat deflection temperature is 135℃, which can increase to 260℃ after reinforcement with glass fibers.
Radiation Resistance
In addition, PPS material exhibits good weathering and radiation resistance, remaining unaffected by multiple exposures to intense ultraviolet and gamma rays, as well as neutron radiation.
Chemical Resistance
Beyond strong oxidizing acids such as concentrated sulfuric acid and nitric acid, PPS can withstand corrosion from other acids, bases, and salts.
Besides ,it is insoluble in any organic solvent below 200℃, with a corrosion resistance nearly equivalent to that of polytetrafluoroethylene (PTFE).
Flame Retardancy
PPS is considered an inherently flame-retardant material, demonstrating outstanding flame-retardant properties and achieving a high flame-retardant rating without the need for added flame retardants.
Mechanical Properties
PPS possesses extremely high rigidity and surface hardness, with minimal decrease in rigidity under high humidity conditions.
It also has excellent creep resistance, fatigue resistance, and wear resistance.
Electrical Insulation and Dielectric Properties
Under high temperature and humidity conditions, PPS maintains a consistent volume resistivity, with minimal variation in its dielectric constant with changes in temperature and frequency.
Additionally, due to its low content of ionic impurities, it can be immersed in a solder bath at 260℃.
Dimensional Stability
PPS exhibits minimal dimensional change at high temperatures, showcasing excellent dimensional stability.
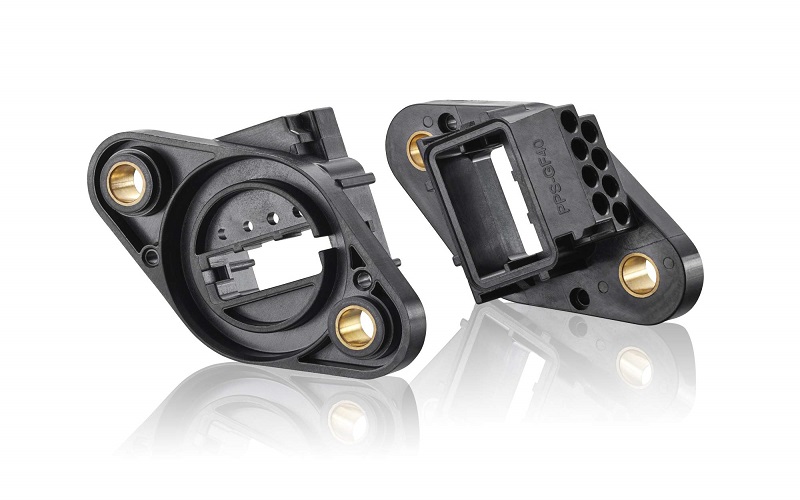
Modeling of PPS Plastic Products
A scientific and rational product design is a necessary factor for PPS plastic injection molding.
The design of PPS plastic products takes into consideration the material’s crystalline polymer nature.
Stress concentration can occur at areas where the product has changes in wall thickness or sharp corners, leading to issues such as stress cracking, dimensional changes, and strength reduction.
When designing the product, it is crucial to ensure that corners have rounded transitions and to avoid uneven thickness as much as possible.
Generally, the thickness of the product should not exceed 7-10mm.
A well-designed reinforcement rib can enhance the product’s rigidity, prevent warping, eliminate residual stress, and improve fluidity.
Increasing the number of ribs is generally more effective than increasing the height and thickness of the ribs.
Typically, the ribs are selected to be half the thickness of the product with rounded transitions, and the demolding angle of the ribs should be between 2-3°.
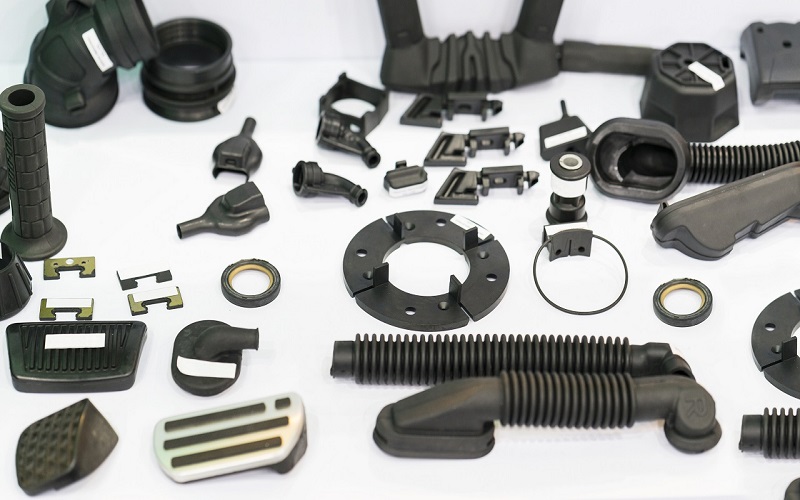
How To Design A PPS Mold?
Designing injection mold is a complex and detailed process that requires consideration of material properties, product design, processing conditions, and more.
Below are some key points for designing a PPS mould:
Mold Material
For PPS, the mold material should be selected based on a benchmark of 140-150℃, using suitable alloy materials such as SK, SKD, SKH, etc., with a hardness of HRC60-65 and surface plating.
Runner
The shape of the runner should preferably be circular or trapezoidal, with a runner taper of 2-3°. A cold slug well should be set at the end of the runner.
Gate
Since pps products have high hardness and low shrinkage rate, the gate should be set at the thickest part of the product section, with a gate diameter not less than 0.6mm.
Ejection
To ensure the surface smoothness and flatness of the product and facilitate demolding, the mold cavity, runner, and other parts should have high surface finish and ejection slope.
The ejection slope is generally 1-3°.
Venting
Bubbles inside PPS products can significantly degrade their performance.
Poor venting can lead to burn marks, discoloration, and surface roughness, affecting the appearance and quality of the product.
The mold must have reasonably placed venting grooves or venting holes. Alternatively, gaps between parting lines and ejection pins can be used for venting.
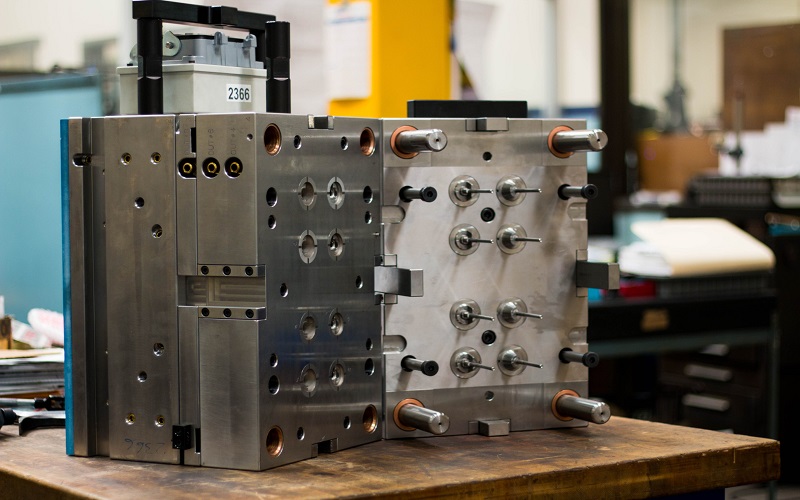
Conditions for PPS Injection Molding
During the PPS injection moulding process, the melt flow rate of PPS plastic is typically controlled at 20-150g/min (measured at 343℃ and 0.5MPa).
For the injection molding machine used in the process, a screw injection molding machine is generally selected.
You can refer to the specific molding conditions in the data sheet provided below:
PPS Injection Molding Parameters | |||
Cylinder temperature | 300~350℃ | Mould Temperature | 120~200℃ |
Injection Pressure | 65~130MPa | Back Pressure | 0.5-1.5MPa |
Screw Speed | 50-200rpm | Injection Speed | Medium Speed |
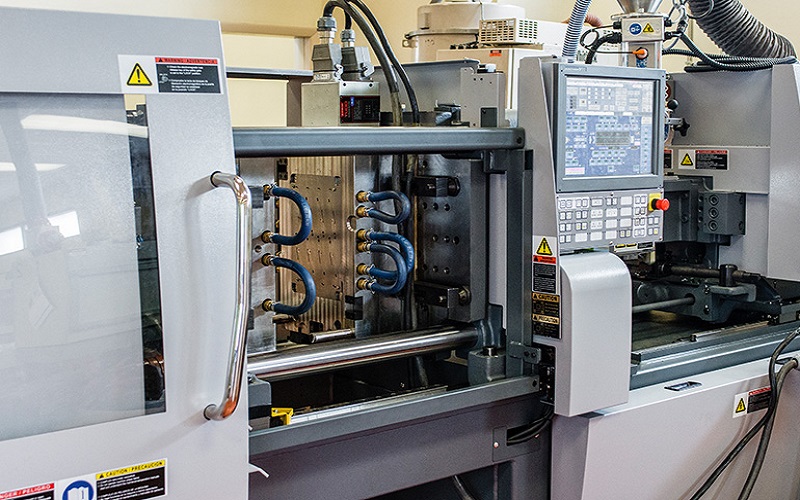
What Are The Applications Of Injection Molded PPS?
In recent years, the application scope of PPS molding has continued to expand, finding extensive use in industries such as automotive, electronics and electrical, petrochemical, and industrial machinery.
Automotive Parts
PPS can maintain stable performance in high-temperature environments, preserving mechanical strength and structural stability even at elevated working temperatures.
This makes injection-molded PPS a preferred choice in the automotive industry, suitable for manufacturing products such as temperature sensors, seat bases, and water chamber of radiators.
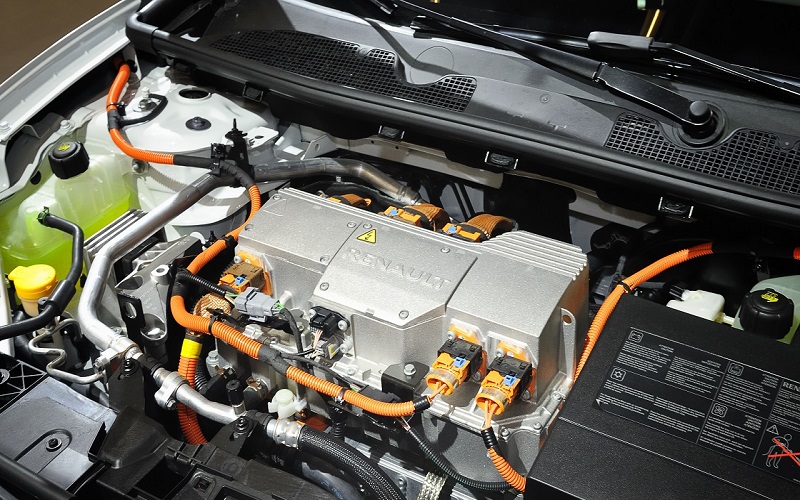
Electronics and Electrical
PPS demonstrates excellent electrical insulation properties, able to block the flow of current in electrical devices, and it also possesses high flame retardancy, reaching UL-94V-0 level without the addition of flame retardants.
For electrical and electronic components, particularly connectors, these characteristics are considered ideal for molding materials.
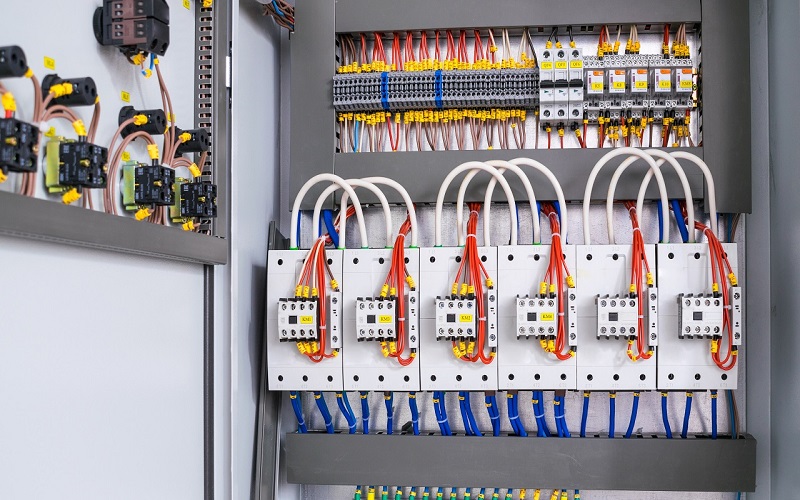
Mechanical Industry
The specific gravity of PPS plastic is around 1.34-2.0, which is only 1/9-1/4 that of steel and about half that of aluminum. In applications that require high-strength materials but aim to reduce weight, PPS plastic is highly competitive.
Therefore, in the mechanical industry, it is commonly used to make pump housings, gears, sealing gaskets, and other components.
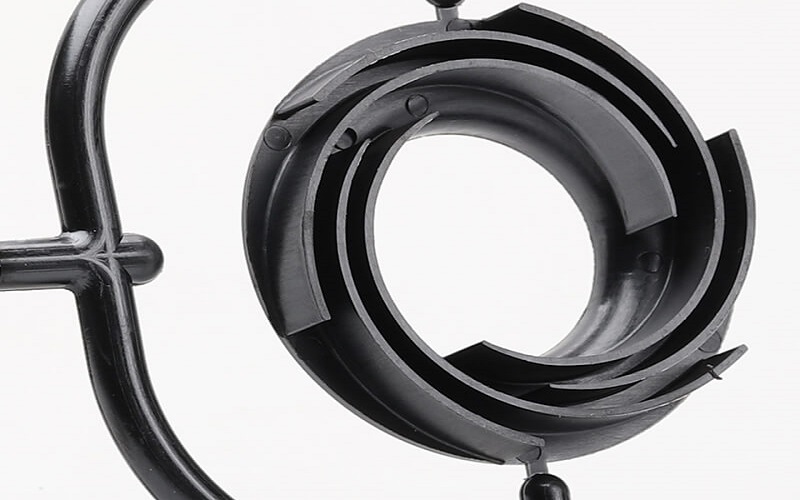
FOWMOULD - Specializing In PPS Plastic Injection Molding
FOWMOULD, established in 1978, is a representative of China’s outstanding plastic injection molding companies, dedicated to providing cost-effective manufacturing solutions.
With extensive experience and advanced technology, FOWMOULD offers high-quality, one-stop injection molding services to a wide range of industries.
Every aspect of the process, from product design to plastic molding, is handled by professional engineers and designers to ensure meticulous attention to detail and to create the most perfect PPS products using their expertise.
Currently, FOWMOULD’s commitment to quality and high-efficiency operations has enabled it to expand its business network to Europe, the United States, Russia, and around the world, earning acclaim from numerous customers.
Do not hesitate to contact us! Let FOWMOULD show you its unparalleled injection molding capabilities.
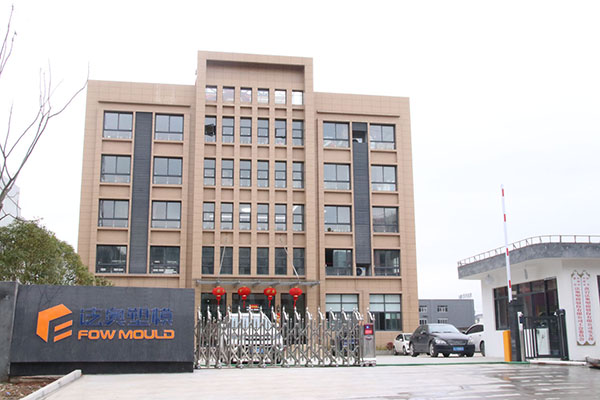