Metal injection molding refers to the innovative technology used to create complex metal parts in a variety of shapes and is also becoming a popular choice for industries such as aerospace, medical and consumer electronics worldwide.
If you’re considering using metal injection molding to develop custom products, the top 3 metal injection molding companies listed below would be a good choice for you.
Top 3 Metal injection molding Companies in China
1.Fow Mould
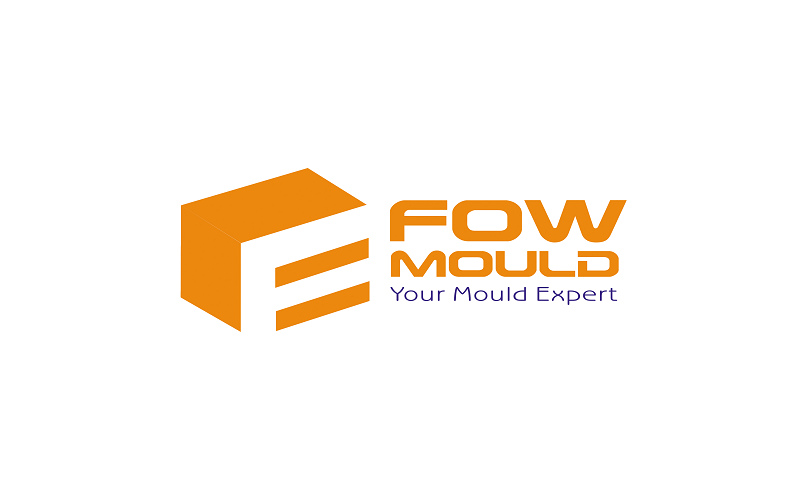
Year Established: 1978
Location: Zhejiang, China
Industry: Manufacturing
FowMould is a leading manufacturer in China with extensive expertise in metal injection molding. 40 years of experience has enabled them to produce metal parts that meet the needs of a wide range of industries.
Meanwhile, FowMould has established design and sales teams to ensure that each customer’s unique needs are met with maximum precision and dedication, always giving the customer a commitment to quality.
2.Shanghai United Metal Materials Co., Ltd
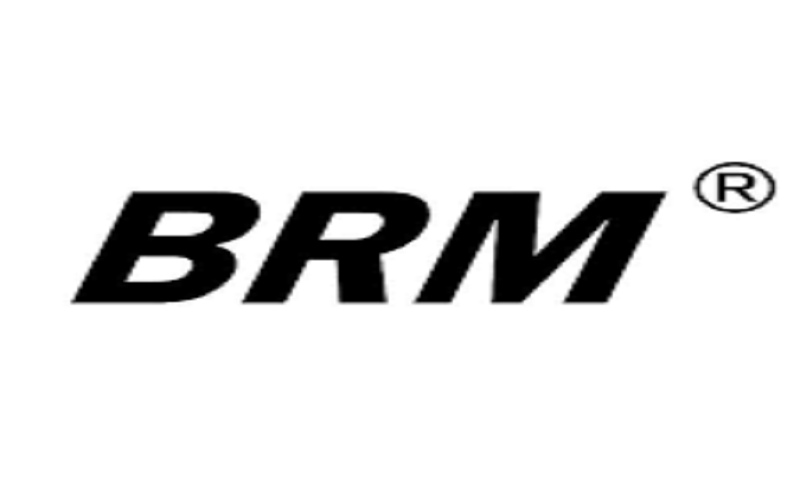
Year Established: 1997
Location: ShangHai, China
Industry: Manufacturing
Shanghai United Metal Materials, a pioneer in the metal injection molding manufacturing industry, has been at the forefront of metal component innovation since 1997. They have consistently demonstrated their ability to deliver top-notch products, with a strong presence in the electronics, automotive and consumer goods sectors.
Their focus on product development and precision in quality ensures that customers receive products that exceed expectations. Their longstanding presence in this industry is a testament to their commitment to quality and business ethos.
3.ABIS Mold(HK) Technology Co.,Ltd
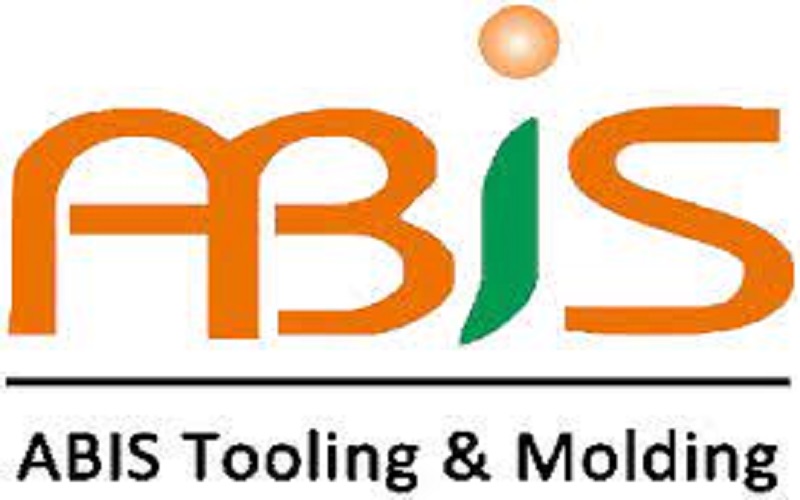
Year Established: 1996
Location: Shenzhen, China
Industry: Manufacturing
Certification:ISO9001:2015
Founded in 1996 in Shenzhen, China, ABIS is a major player in the field of metal fabrication. It has carved a niche for itself by customizing unparalleled metal fabrication solutions for various clients.
With a blend of cutting-edge technology and a team of experienced professionals, ABIS Moulding delves into the intricacies of metal fabrication, ensuring that every part they produce is of top quality.
These companies can be your alternatives, there are many more excellent metal injection molding suppliers in China, but the specific choice still depends on your project content and service requirements. Please read on to learn more about metal injection molding.
As the concept of sustainable development becomes increasingly prevalent, industries worldwide are in search of solutions that not only offer high precision but also maintain cost-effectiveness and scalability. It’s against this backdrop that Metal Injection Molding (MIM) was born.
Metal Molding signifies more than just a process; it marks a pivotal moment in metalworking. By tapping into the intricacies offered by injection molding to shape elaborate designs and marrying it with the inherent strength of metals, a distinctive approach for producing complex and durable components has been unveiled.
In this article, we will delve deep into this technique, exploring the mechanics, applications, and advantages of metal injection, shedding light on the mysteries of its manufacturing prowess.
What is Metal Injection Molding?
Metal Injection Molding (MIM) is an innovative metalworking process, representing a revolutionary technique that blends plastic injection molding, polymer chemistry, powder metallurgy, and metal materials science.
In this method, fine metal powders are combined with a polymer binder to produce a moldable feedstock. This feedstock is then subjected to injection molding and subsequent solidification to produce the final product.
To a significant extent, it has entirely transformed traditional manufacturing techniques, offering an optimal solution for streamlining the production of large quantities or intricately designed products.
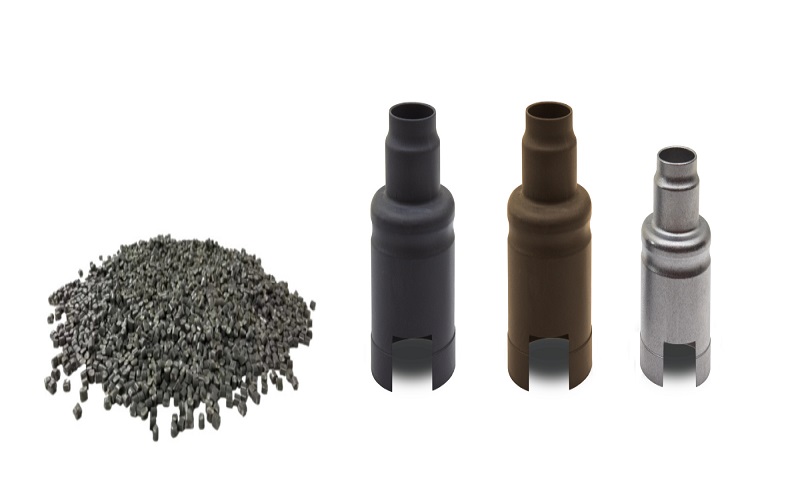
Processing Of Metal Injection Molding
Metal Injection Molding , a prevalent molding technique of the present times, stands as the prime choice for manufacturing intricate metal components that are both cost-effective and high in precision. The process encompasses the following key stages.
Stage1:Feedstock Preparation
Before initiating the molding process, material preparation is crucial. One begins by selecting fine metal powders, such as stainless steel, titanium, or nickel alloy, and combines them with a thermoplastic binder, typically made of wax or polymer. This mixture results in a feedstock with a consistency akin to that of molten plastic, laying the groundwork for molding.
Stage2:Injecting Molding
The prepared raw materials are injected into molds for the injection process. These molds are designed with the desired shape of the final part in mind,with molding temperatures generally ranging from 300° to 500°F (149°-260°C). Once cooled, the molded part (referred to as the “green part”) is ejected.
Stage3:Debinding
In this stage, the binder is removed from the green part, leaving behind only the metal. This can be achieved either through solvent debinding, where the binder is dissolved, or through thermal debinding, where it is heated and the binder evaporates.
Stage4:Sintering
Following this, the debound part undergoes a sintering process. It’s heated in a controlled atmosphere furnace to a temperature just below the metal’s melting point.
This step facilitates the fusing of metal particles, yielding a solid structure with dense properties.
During this phase, the part typically undergoes shrinkage, yet retains the shape imparted by the mold.
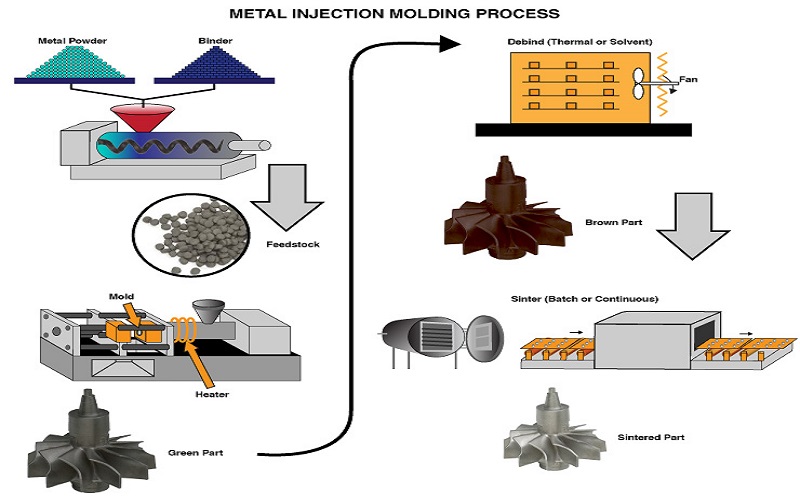
Material Selection In Metal Injection Molding
In the Metal Injection Molding process, selecting the appropriate material is crucial, as it significantly impacts the final product’s characteristics and applicability.
Among the options within the MIM technology are alloy steels, stainless steels, and heat-resistant materials.
- Stainless Steels: Frequently used due to their corrosion resistance and commendable mechanical properties. Common grades include 316L, 17-4PH, and 304L.
- Nickel Alloys: Noted for their strong heat resistance and corrosion resilience, these are often chosen for high-temperature applications. Alloys like the chromium-nickel-iron alloy 625 and Hastelloy are typical examples.
- Titanium Alloys: Renowned for their high strength-to-weight ratio, they are the preferred choice for aerospace and medical applications.
- Soft Magnetic Alloys: Suited for electromagnetic applications, these materials might include alloys such as Fe-Ni or Fe-Co.
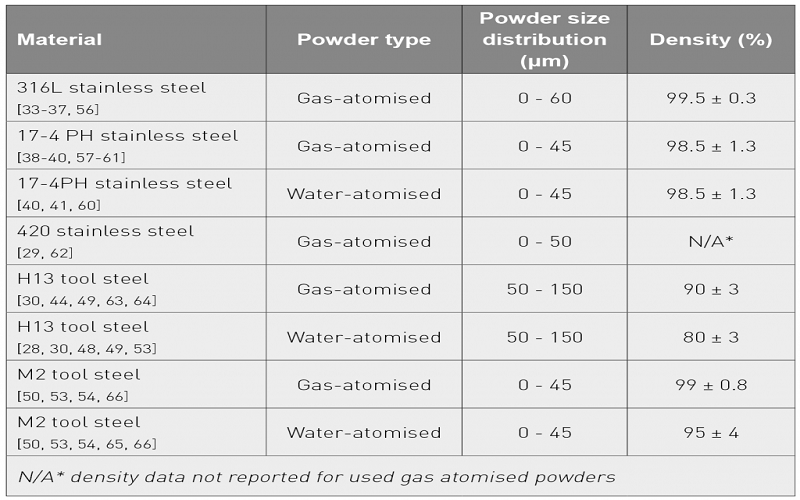
The Characteristics Of Metal Injection Molding
Metal Injection Molding is an innovative process that has emerged as a primary method for producing complex metal parts, bridging the gap between the versatility of plastic injection molding and the mechanical and thermal properties of metals.
A salient feature of MIM products is their sintering density, which usually reaches around 98% of the theoretical density. For instance, a stainless steel component produced via MIM, when subjected to appropriate sintering and post-treatments, can achieve compressive strengths in excess of 900 MPa, rivaling those of traditionally forged or machined counterparts.
Concurrently, during sintering at sufficiently high temperatures, the injection molded metal undergoes partial melting. For instance, stainless steel might be heated to temperatures ranging between 1350°C to 1400°C (2460°F to 2550°F).
Furthermore, the flexibility inherent in metal injection technology allows manufacturers to tailor-make specific alloy combinations to enhance particular properties, such as tensile strength, corrosion resistance, or thermal conductivity.
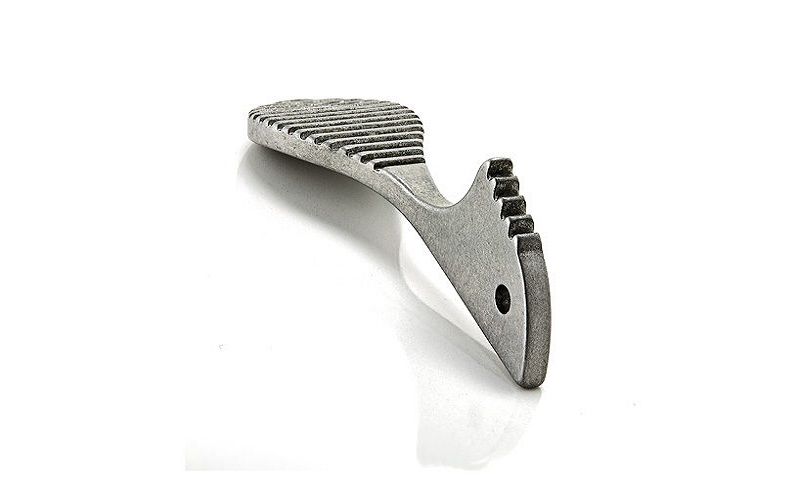
Benefits of Metal Injection Molding
The advantages of Metal Injection Molding (MIM) are particularly pronounced when compared to traditional metal manufacturing.
One of the standout features of MIM is its design flexibility. This process enables the production of parts with intricate details and shapes, something challenging to achieve with other techniques.
High precisionremains a hallmark of MIM, as the metal injection molding process ensures components are consistently manufactured within stringent tolerance limits.
MIM is especially suitable for large-scale production. By molding parts close to their final shape directly, wastage is minimized, reducing material costs and offering a cost-effective production approach.
Additionally, the repeatability of metal injection molding ensures high-precision product manufacturing even as production scales up.
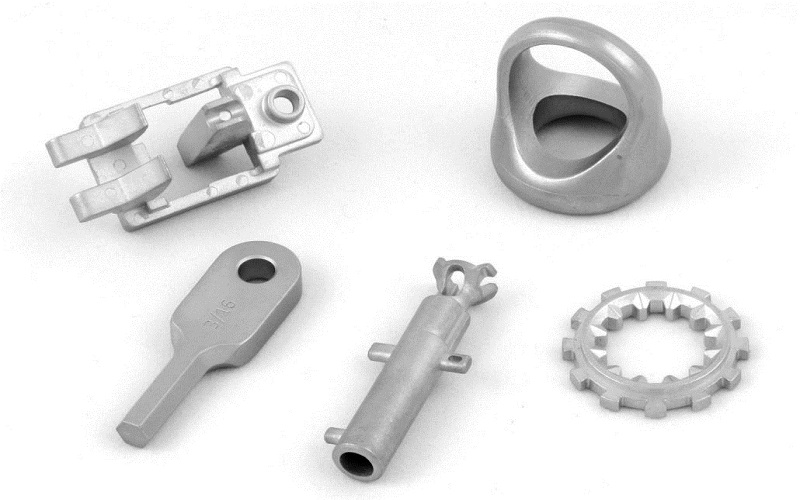
Applications of Metal Injection Molding
The versatile nature of metal injection molding makes it uniquely suited to produce complex and high-precision metal components for a wide range of applications in a variety of industries.
Medical Devices
Given the precision and biocompatibility requirements of the medical field, metal injection molding is often used to manufacture surgical tools, orthodontic brackets and implantable devices.
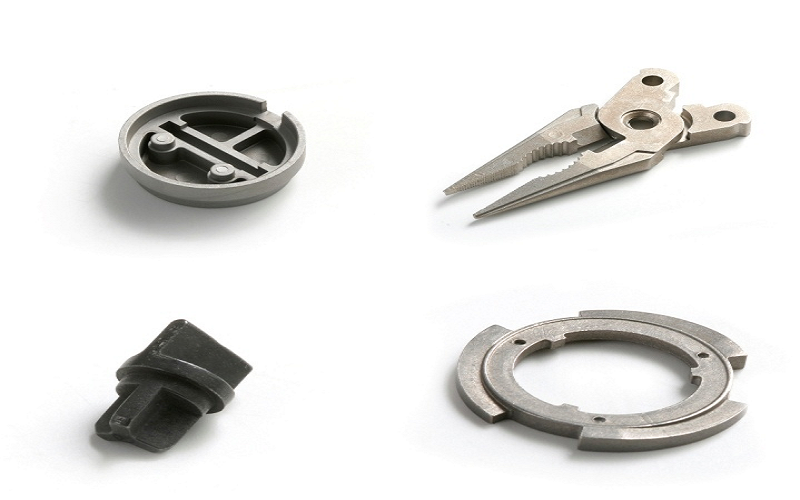
Consumer Electronics
As the trend toward miniaturization of electronic products grows, complex and small components are required. Components such as hinges, connectors and shielding housings are often the work of injection molded metals.
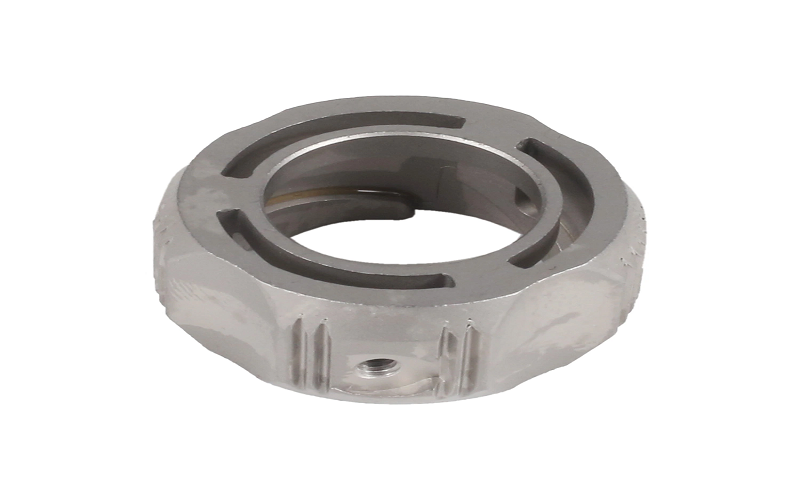
Automotive
To improve fuel efficiency and performance of drives, metal injection molding is used to produce lightweight and robust components such as fuel injectors, transmission parts and sensor assemblies.
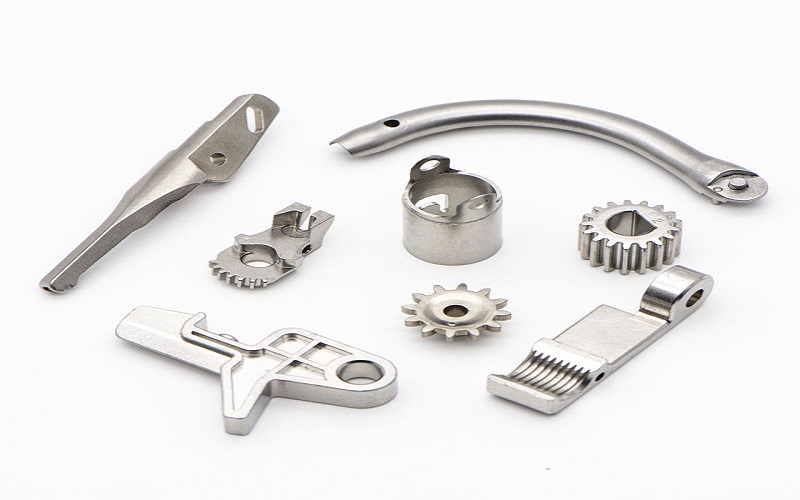
Aerospace
Given the stringent standards of the aerospace industry,mim injection molding provides components with high strength-to-weight ratios, such as critical parts like turbine blades or instrumentation components.
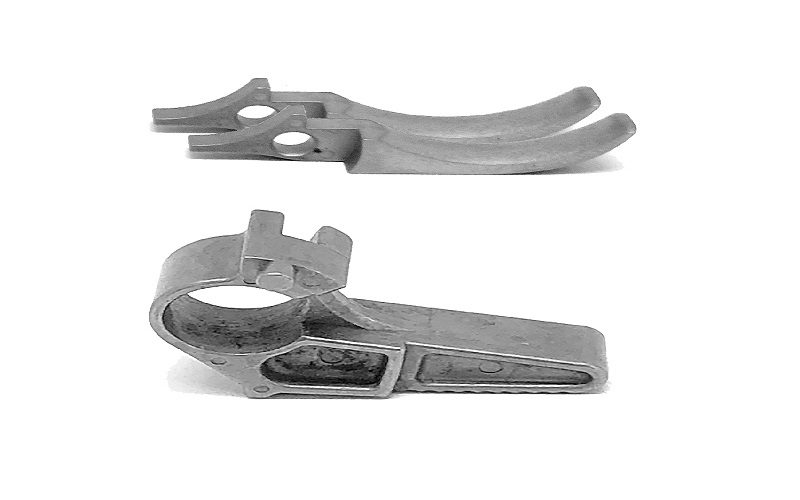
A Brief Comparison between Metal Injection Molding and Plastic Injection Molding
Both metal injection molding (MIM) and plastic injection molding are cutting-edge molding techniques. While they share similar processes, each boasts distinct advantages.
Plastic injection molding primarily employs thermoplastics or thermosets, serving a wide range of industries. This technique ensures smooth mold release and is versatile, accommodating both high-volume and low-volume production with significant design flexibility.
On the other hand, MIM primarily revolves around the fusion of metal powders with polymer binders. Additionally, MIM components require supplementary processes to eliminate binders and carry out sintering of the powder.
In practical production, the choice between these molding techniques hinges on material needs, desired product properties, and production volume.
Conclusion
This article centers around the concept of metal injection molding, how it works, areas of application and discusses the different attributes from plastic injection molding. To learn more about metal injection molding, contact FOWMould.
FOWMould has the manufacturing experience and proven manufacturing technology to provide you with dynamic and cost-effective injection molding solutions. Visit our website to learn more or request a free, no-obligation quote.