Ah, the world of plastic production! It’s a fascinating realm, isn’t it? One of the most common methods used in this industry is injection moulding. This manufacturing process involves injecting molten plastic into a mould, where it cools and solidifies to form the final part. The cycle time for this process can range from 15-120 seconds, depending on the size of the part and the complexity of the mould.
The injection moulding process is a marvel of precision and efficiency. It’s like a well-choreographed dance, where every movement matters. The plastic parts produced through this method have a consistent quality, which is crucial in industries where tight tolerances are a must. But, what makes this process tick? Let’s delve a bit deeper.
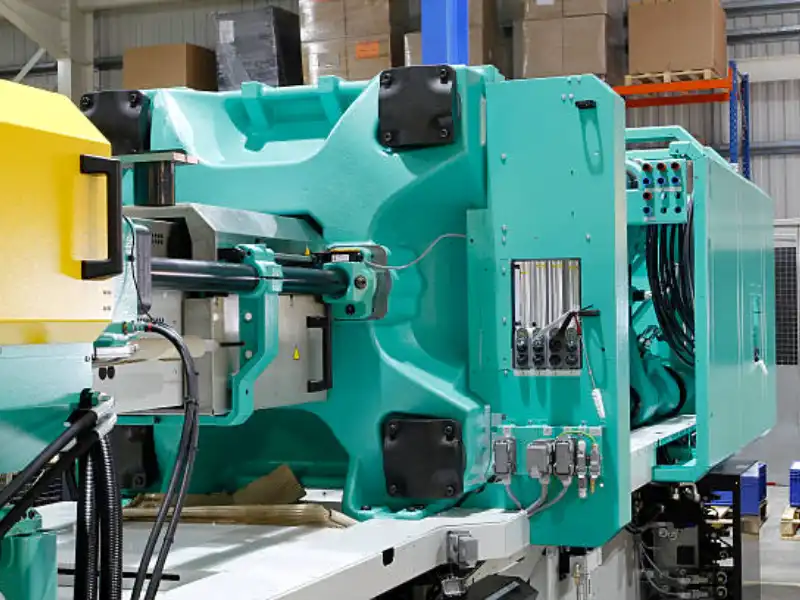
What is the Role of Tooling in Enhancing Injection Moulding Efficiency?
Tooling is the unsung hero of the injection moulding process. It refers to the moulds used to shape the plastic parts. These moulds are typically made from metals like steel or aluminium, and their design can significantly impact the efficiency and quality of the injection moulding process.
Good tooling can reduce cycle times, improve part quality, and even extend the life of the mould. It’s like the secret ingredient in a recipe that takes it from good to great! The role of tooling in injection moulding cannot be overstated. It’s a critical factor in achieving high volumes of production at a low cost, making it a key advantage of injection moulding.
Advantage 1: High Efficiency and Speed of Injection Moulding
One of the main advantages of injection moulding is its high efficiency and speed. Once the mould has been created and the injection moulder is set up, the process can produce a large number of parts in a relatively short amount of time. This is especially beneficial for industries that require high volumes of identical products.
The speed of the injection moulding process is largely due to its automated nature. Robotics and automation play a significant role in this, allowing for a repeatable process that can operate around the clock. This efficiency is a boon for industries like automotive and packaging, where time is of the essence.
Advantage 2: The Versatility of Materials in Injection Moulding
Injection moulding is like a chameleon—it can adapt to a wide range of materials. From thermoplastics and engineered materials to resins and even silicone, the possibilities are vast. This versatility is another significant advantage of injection moulding.
Different materials have different properties, and the ability to choose the right one for a specific application is crucial. Whether you need a part with greater strength, a specific surface finish, or resistance to certain conditions, injection moulding has got you covered. It’s like having a Swiss Army knife in your manufacturing toolkit!
Advantage 3: The Precision and Accuracy of Injection Moulding
Precision and accuracy are the hallmarks of injection moulding. This process can produce complex parts with intricate shapes and tight tolerances. It’s like a master sculptor, able to carve out the tiniest details with impeccable precision. This is particularly important in industries such as automotive and medical, where even the smallest deviation can have significant consequences.
The precision of injection moulding is largely due to the tooling and the controlled injection process. The mould is designed with the exact geometry of the final part, and the molten plastic is injected under high pressure, ensuring it fills every nook and cranny. The result? Parts that are as precise as they are beautiful.
Advantage 4: The Repeatability Factor in Injection Moulding
Repeatability is another key advantage of injection moulding. Once the mould is created and the process parameters are set, the injection moulding process can produce identical parts, time and time again. It’s like a well-oiled machine, churning out consistent results with minimal variation.
This repeatability is crucial in industries where consistency is key. Whether it’s producing millions of bottle caps or car parts, injection moulding ensures each part is virtually identical to the last. This level of consistency is hard to achieve with other manufacturing processes, making injection moulding a go-to choice for many.
Advantage 5: The Cost-Effectiveness of Injection Moulding
Let’s talk about money, shall we? Injection moulding is a cost-effective method for producing plastic parts, especially in high volumes. The initial cost of creating the mould can be high, but once it’s made, the cost per part is relatively low. It’s like buying in bulk—the more you produce, the cheaper each part becomes.
Furthermore, the automated nature of the injection moulding process reduces labor costs and overheads. The process can run 24/7 with minimal human intervention, thanks to robotics and automation. This cost-effectiveness is a significant advantage of injection moulding, making it an attractive option for businesses looking to balance quality and cost.
Advantage 6: The Flexibility of Design in Injection Moulding
Design flexibility is another feather in the cap of injection moulding. This process can produce parts with complex geometries, undercuts, and intricate shapes that would be difficult, if not impossible, to achieve with other manufacturing methods. It’s like a magician, pulling out a rabbit from a hat!
The design flexibility of injection moulding is largely due to the high pressure at which the molten plastic is injected into the mould. This pressure allows the plastic to reach every part of the mould, capturing even the smallest details. Whether it’s a tiny gear for a watch or a large panel for a car, injection moulding can handle it all.
Advantage 7: The Sustainability Aspect: Material Reusability in Injection Moulding
In today’s world, sustainability is more important than ever. And here’s the good news: injection moulding has a trick up its sleeve. The scrap generated during the process, such as runners and sprues, can be reground and reused, reducing waste. It’s like giving plastic a second chance at life!
Moreover, many of the materials used in injection moulding, such as thermoplastics, can be recycled. This material reusability is a significant advantage of injection moulding, contributing to its sustainability and making it a more environmentally friendly choice.
Advantage 8: The Wide Application of Injection Moulding Across Industries
The advantages of injection moulding have made it a popular choice across a wide range of industries. From automotive and aerospace to medical and consumer goods, injection moulding is everywhere. It’s like the star player on a football team, always in demand and always delivering results.
The wide application of injection moulding is a testament to its versatility, efficiency, and cost-effectiveness. Whether it’s producing a small plastic toy or a critical component for a spacecraft, injection moulding has proven its worth time and time again.
Injection Moulding vs. CNC Machining: A Comparative Analysis
Injection Moulding | CNC Machining | |
Efficiency | High efficiency, especially for high-volume production | Less efficient for high-volume production |
Cost | Lower cost per part for high volumes | Higher cost per part for high volumes |
Precision | High precision and consistency | High precision, but consistency can vary |
Design Flexibility | High design flexibility, can produce complex parts | Less design flexibility, some limitations on part complexity |
Material Versatility | Wide range of materials, including thermoplastics and silicone | Limited to materials that can be machined |
Injection Moulding vs. 3D Printing: Weighing the Pros and Cons
Injection Moulding | 3D Printing | |
Speed | Fast production speed, especially for high volumes | Slower production speed, especially for high volumes |
Cost | Lower cost per part for high volumes, but high initial tooling cost | Higher cost per part for high volumes, but low initial setup cost |
Precision | High precision and consistency | Precision can vary, depending on the printer and material |
Design Flexibility | High design flexibility, can produce complex parts | High design flexibility, can produce complex parts with ease |
Material Versatility | Wide range of materials, including thermoplastics and silicone | Limited to materials that can be 3D printed |
Addressing the Potential Disadvantages of Injection Moulding
No process is perfect, and injection moulding is no exception. There are potential disadvantages to consider, such as high initial tooling costs and limitations on part design due to the need for draft angles and ejection considerations. However, when weighed against the numerous advantages of injection moulding, these disadvantages often pale in comparison.
For instance, while the initial tooling cost can be high, the cost per part decreases significantly with high volumes, making injection moulding a cost-effective choice for mass production. Similarly, while there are some design limitations, the high precision, repeatability, and design flexibility of injection moulding often outweigh these constraints.
Conclusion: Why Injection Moulding is the Go-To Choice for Plastic Production
In conclusion, the advantages of injection moulding make it a go-to choice for plastic production. Its efficiency, precision, repeatability, cost-effectiveness, design flexibility, sustainability, and wide application across industries are hard to beat. It’s like the all-rounder in a cricket team, delivering on all fronts.
While there are potential disadvantages, they are often outweighed by the benefits, especially for high-volume production. So, whether you’re in the automotive industry, the medical field, or the world of consumer goods, injection moulding has something to offer. It’s a testament to the power of this process that it has stood the test of time, continuing to be a cornerstone of plastic production.
Get in Touch With FOWMould
At FOWMould, we pride ourselves on our expertise in injection moulding and our commitment to excellence. Our team of seasoned professionals is ready to guide you through the entire production process, answering any questions you may have about the advantages of injection moulding. We’re not just about making parts; but also about building partnerships and delivering solutions that meet your specific needs.
We’re always on the lookout for ways to improve our processes and stay at the forefront of the industry. That’s why we invest in state-of-the-art machinery and keep up with the latest trends in injection moulding. Our goal is to provide you with high-quality, cost-effective, and sustainable solutions for your plastic production needs.
Want to learn more about how FOWMould can help you leverage the advantages of injection moulding? Click here to visit our website and request a quote today. We’re excited to start this journey with you and show you why FOWMould is the go-to choice for injection moulding.