Bracket Injection Molding are key components in many industries, including electronics, construction, and furniture. Due to the important role that brackets play in numerous applications, it is crucial to find a supplier that can provide high-quality products.
As one of the world’s largest manufacturing centers, China has thousands of companies engaged in bracket production and supply. If you are looking for custom brackets, the following list of China’s top five leading bracket manufacturers will help you choose a partner that meets your manufacturing needs.
Top 5 Bracket Injection Molding Companies in China
1.Fow Mould
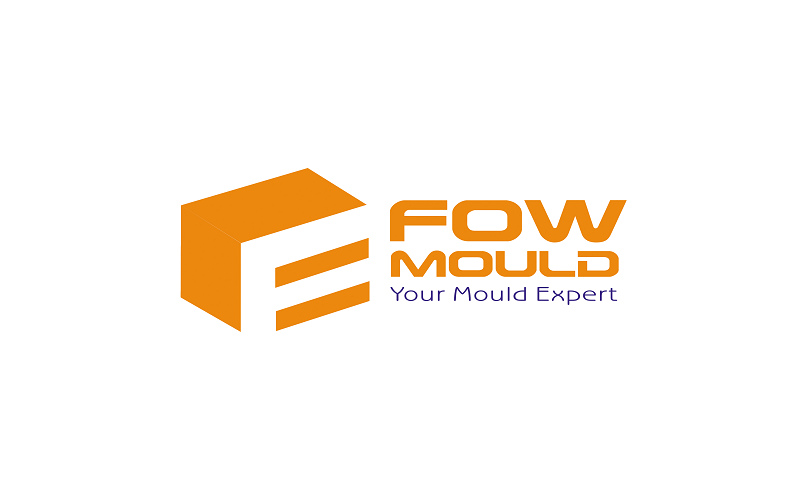
Year Established: 1978
Location: Zhejiang, China
Industry: Manufacturing
FowMould, a renowned plastic molding manufacturer in China, brings its expertise to the niche sector of custom bracket manufacturing. With our significant experience in injection molding, specifically with durable materials like polycarbonate, we have expanded our capabilities to produce high-quality, precision-crafted custom brackets. These brackets cater to a diverse array of industries, from electronics to construction, and everything in between.
Our strength lies not only in our manufacturing expertise but also in the human element that makes FowMould unique. We have a professional design team that works hand-in-hand with our clients, carefully translating their needs into functional designs. Our dedicated sales team ensures a smooth transaction and provides support at every step of the journey.
2.Dongguan Yubiao Hardware Co., Ltd.
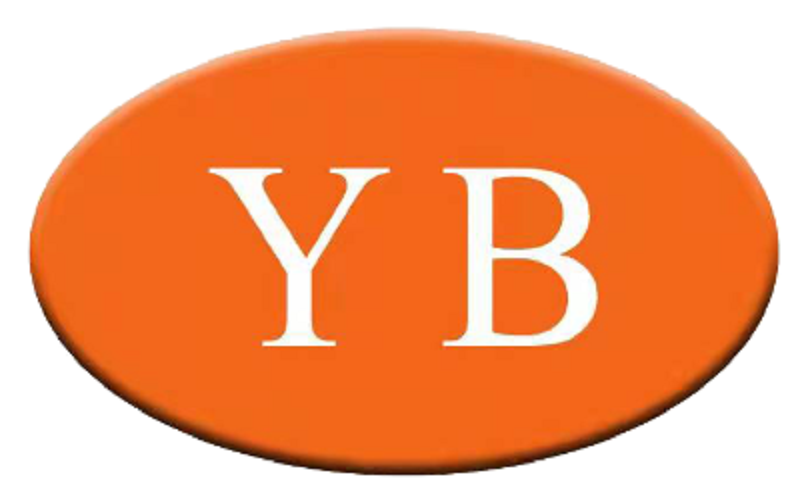
Year Established: 2000
Location: Dongguan, China
Industry: Manufacturing
Dongguan Yubiao Hardware Co., Ltd. has made significant strides in the bracket manufacturing industry over the last two decades. Established in 2000, the company aims to provide economical yet high-quality bracket solutions. Its team of qualified engineers and a robust R&D department are continually driving innovation forward.
The company is committed to designing and manufacturing top-notch products tailored to clients’ requirements and has positioned itself as a respected name in the bracket manufacturing sector worldwide.
3.Ningbo Haishu Skyou Industry Co., Ltd.

Year Established: 2006
Location: Ningbo, China
Industry: Manufacturing
Ningbo Haishu Skyou Industry Co., Ltd., established in 2006, has risen to prominence within the bracket manufacturing sector due to its commitment to delivering high-quality products. The firm’s commitment to innovation, supported by its experienced engineers and proactive R&D department, has ensured it remains at the forefront of bracket manufacturing.
Skyou Industry works in close collaboration with its clients to provide tailored solutions that meet their specific needs, ensuring durability and cost-effectiveness.
4.Shanghai Yunyan Prototype & Mould Manufacture Factory
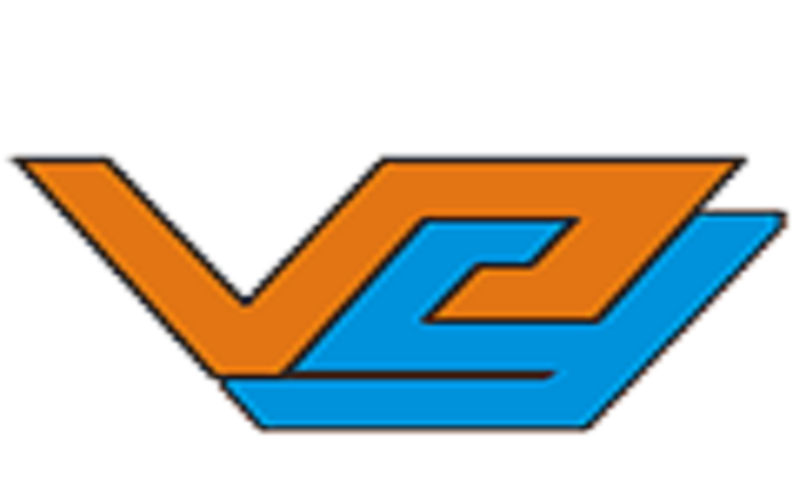
Year Established: 1997
Location: Shanghai, China
Industry: Manufacturing
Shanghai Yunyan Prototype & Mould Manufacture Factory has been a dominant player in the bracket manufacturing industry since its inception in 1997. The company is renowned for its commitment to delivering superior bracket solutions, and its team of engineers and an active R&D department are continually innovating to meet evolving market demands.
Shanghai Yunyan Prototype & Mould Manufacture Factory works closely with its clients, delivering custom solutions that ensure durability, affordability, and performance.
5.Guangdong Dongji Intelligent Device Co., Ltd.

Year Established: 2001
Location: Jiangmen, China
Industry: Manufacturing
Certification:ISO9001:2008
Guangdong Dongji Intelligent Equipment Co., Ltd. was established in 2001 and is a leading bracket manufacturer, providing high-quality solutions to meet various applications. They have experienced engineers and a strong R&D department, constantly pushing the company’s innovation to new heights.
They work closely with customers to design and manufacture customized bracket solutions that deliver quality, cost-effective, and durable products, solidifying their reputation in the global market.
These top 5 bracket manufacturers in China have distinguished themselves through their commitment to quality, innovation, and customer satisfaction. Whether you’re looking to manufacture your own product with custom parts or source high-quality brackets for your operations, these suppliers will be sure to deliver the best solutions.
With the development of injection molding technology, the manufacturing of custom brackets has become a cornerstone in many industries. However, for those who are new to the field of custom bracket production, it may feel like navigating through a complex maze.
This article aims to simplify the world of bracket injection molding, starting from the basic principles and mechanisms of this process, as well as why it has become the preferred method for manufacturing high-quality brackets. It will guide you through how bracket injection molding can benefit your business and enhance product integrity.
Continue reading below to delve deeper into this topic!
What is Bracket Injection Molding?
A bracket is crucial components for many structures and machines, requiring strength, precision, and durability. By utilizing the manufacturing process of injection molding, brackets of high quality can be produced using various materials.
Bracket injection molding is a complex manufacturing process that involves injecting molten material (usually metal or plastic) under high pressure into custom-made bracket molds. This enables large-scale production of brackets while ensuring stable quality.
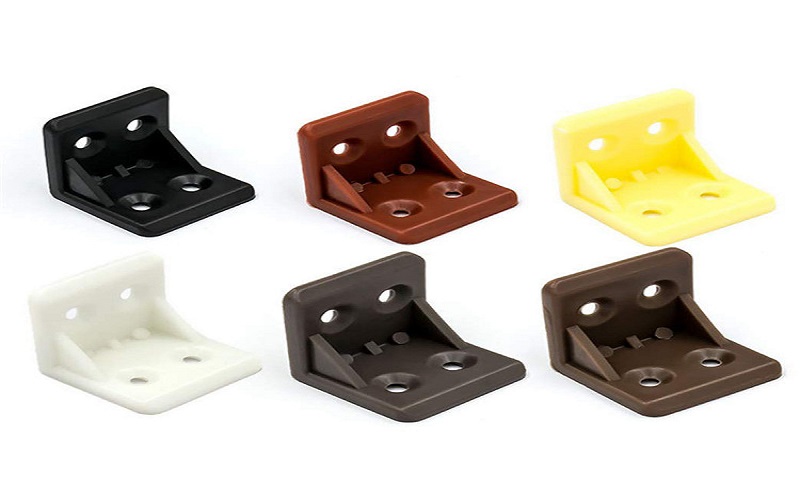
Why Opt for Bracket Injection Molding?
Bracket injection molding has gained popularity because it offers the perfect balance of durability, precision, and cost-effectiveness. As manufacturing technology continues to advance, this process will continue to play a vital role in driving innovation and efficiency across a wide range of industries.
Durability
When using injection molding technology to manufacture brackets, it ensures that the brackets have a uniform structure, thereby improving their overall durability and lifespan. This results in sturdy and durable products that are not easily worn out.
Cost-Effective
Although the brackets injection molding requires upfront costs for mold manufacturing, it is a cost-effective method for mass production due to its low unit cost. The highly automated process of injection mold production often results in lower labor costs compared to other manufacturing processes.
Precision and Consistency
With bracket injection molding, manufacturers can achieve high-precision bracket manufacturing. The mold determines the precise dimensions and shape of the bracket, ensuring product consistency and meeting exact specifications. This process is particularly advantageous when components need to be installed within a larger assembly with minimal margin for error.
Flexibility
Bracket injection molding allows for the use of various materials, including different types of plastic and metal. This flexibility enables the creation of brackets with specific properties, such as enhanced strength or resistance to heat or corrosion, depending on the application requirements.
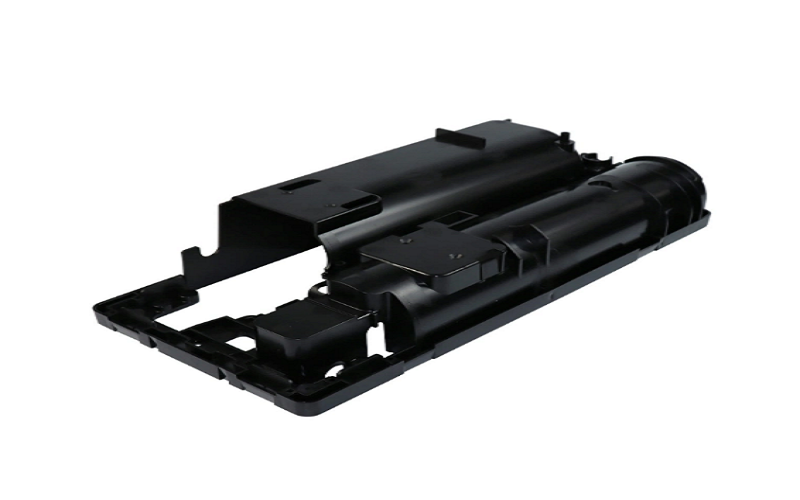
Diverse Material Choices in Bracket Manufacturing
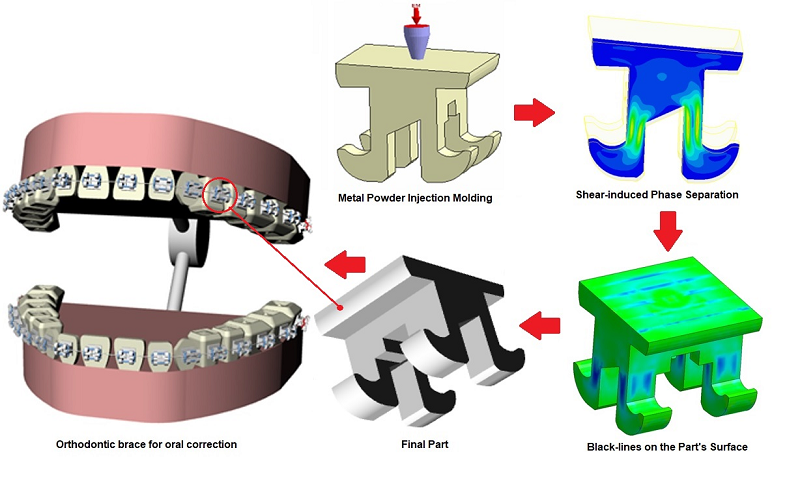
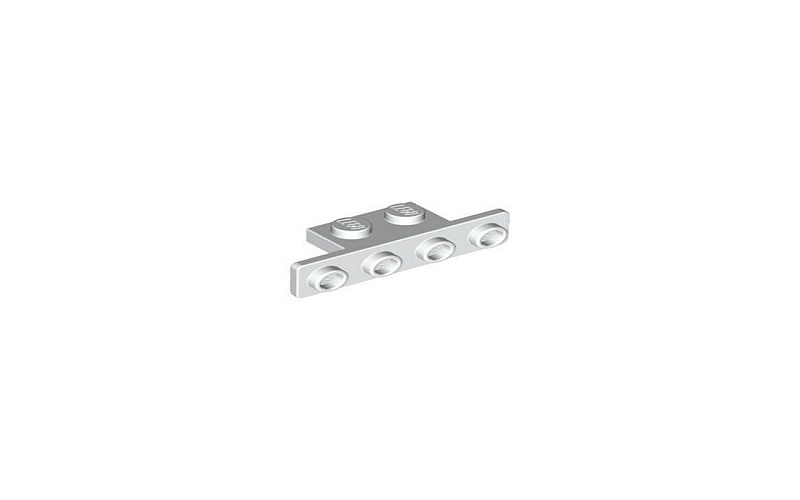
In the manufacturing process of brackets, the choice of materials is crucial. Each material brings unique performance, advantages, and disadvantages to the final product.Metal and plastic are the two most commonly used materials in bracket injection molding.
Metal brackets, typically made of steel or aluminum, are renowned for their strength and resistance to wear. These characteristics make metal brackets highly suitable for applications that require high levels of structural integrity, such as construction, heavy machinery, and the automotive industry.
They may also be more costly to manufacture due to the higher price of metal materials and the energy-intensive processes needed to mold them.
On the other hand, plastic brackets are highly favored for their lightweight, corrosion resistance, and ability to be molded into complex shapes. They are typically made from ABS, polycarbonate, and nylon.
However, plastic brackets may not provide the same level of strength as metal ones, making them unsuitable for some high-stress applications. They may also be more susceptible to damage from UV radiation and extreme temperatures.
Applications of Bracket Injection Molding
Bracket injection molding has a wide range of applications across numerous industries, given its advantages such as high production speed, accuracy, and material flexibility.
Automotive Industry
Bracket injection molding takes center stage for creating key components in the automotive industry. It is commonly used for installing engine, exhaust system, and radiator components. Additionally, the ability to incorporate complex functionalities directly into bracket design makes the components lighter and more integrated, helping reduce overall vehicle weight and improve fuel efficiency.
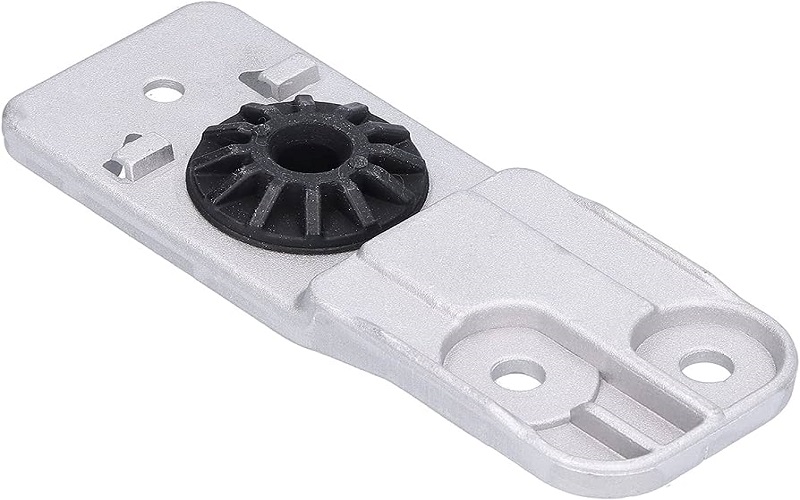
Electronics
In the field of electronic components, bracket injection molding is a popular choice for production due to its precision, consistency, and ability to use a wide range of materials, including flame retardant plastics. Inside equipment, bracket injection molding is often used to mount circuit boards or other components.

Consumer Products
In everyday consumer goods such as appliances, furniture, and toys, the use of brackets is ubiquitous. Bracket injection molding can provide an economical and efficient solution for mass production, while also allowing for the selection of different colors and surface treatments to enhance the aesthetic appeal of the final product.
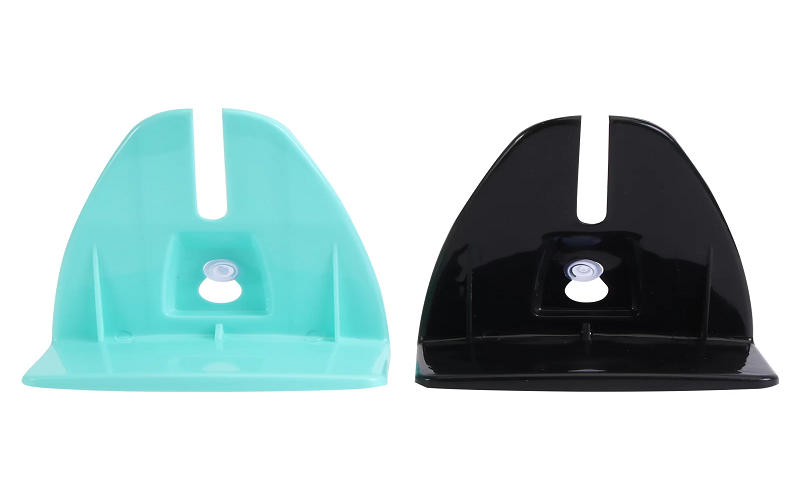
Medical Devices
Bracket injection molding is a vital technique utilized in the medical industry to securely fasten equipment and components in medical devices. This process is renowned for its exceptional precision and consistency, which are paramount in medical applications where even minor variations can have profound implications.
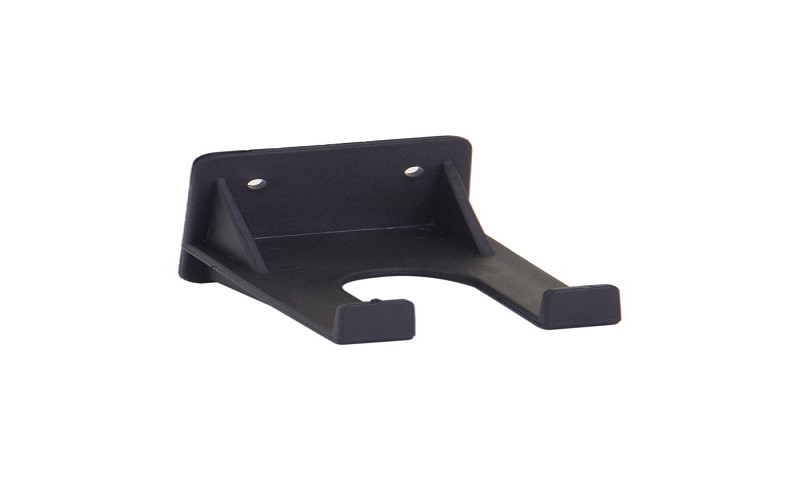
Construction industry
Brackets are used in a wide variety of applications in construction. They can be used as anchor points for wall systems, provide support for shelving, and enable the installation of accessories. Bracket Injection molded brackets is praised for their durability and customization options, allowing the product to fit the customer’s custom bracket needs.
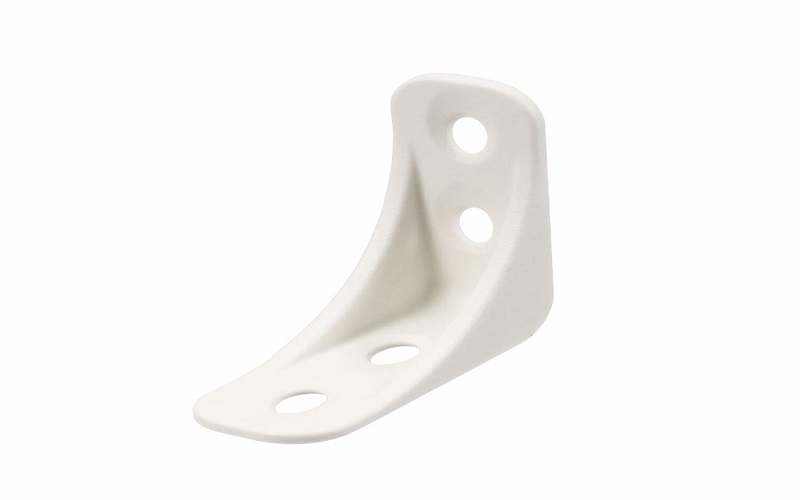
Common challenges in the Bracket Injection Molding
As a professional bracket manufacturer, FowMould has accumulated extensive experience in bracket injection molding. However, there are still some challenges in this process.
One of the main challenges of bracket injection molding is that the initial cost of making molds is high. It is essential to design custom molds for each bracket, which requires a significant investment.
In addition, there are certain design limitations due to material characteristics and the flow dynamics inside the mold. Complex geometries or overly thick sections may result in aesthetic and structural defects, such as sink marks.
Material selection is another key consideration, as not all materials are suitable for injection molding, and improper selection can lead to problems such as warpage or shrinkage.
Ensuring consistent output also requires rigorous quality control processes, considering that small variations in parameters such as temperature, pressure and cycle time can lead to significant inconsistencies in the final product.
Finally, mention must be made of environmental challenges such as waste generation during startup, shutdown and cleaning.
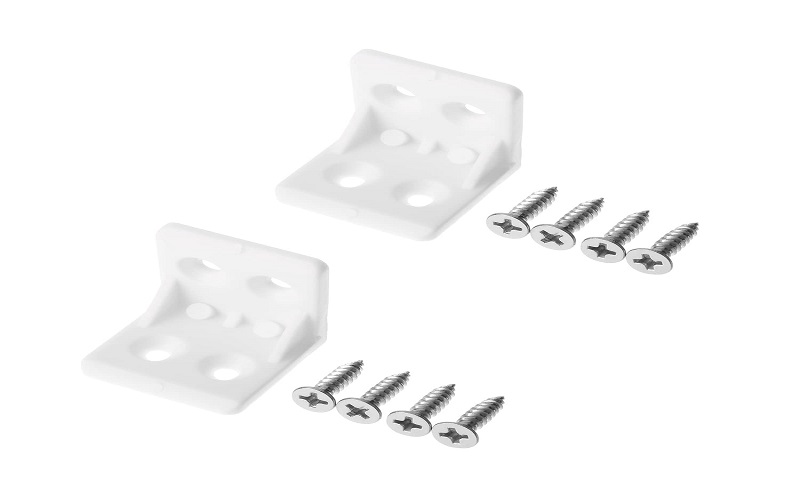
Successful Tips for Bracket Injection Molding
FowMould as an expert in the field of injection molding, not only provides customized injection mold support services, but also masters the techniques for achieving success in this complex process.
- Effective Design for Manufacturing (DFM)
First and foremost, we emphasize the “Design for Manufacturing” (DFM) approach to ensure optimal compatibility between mold design and injection molding processes, which can reduce manufacturing costs by up to 50%.
- Utilization of Multi-Cavity Molds
For large scale production, multi-cavity molds significantly enhance efficiency, allowing multiple brackets to be produced per cycle. This approach speeds up production, resulting in a more cost-effective and efficient process.
- Adjustment of processing parameters
Adjusting the optimal parameters for bracket injection molding, such as processing temperature, pressure, and cycle time, can reduce the defect rate to 60%.
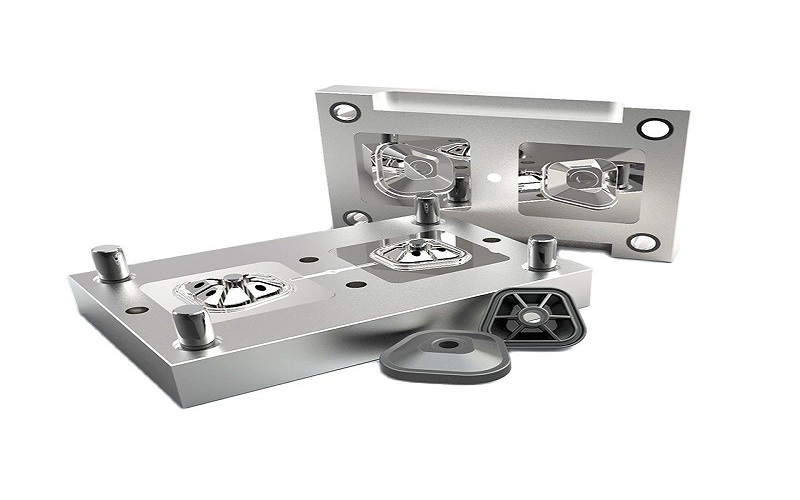
Fowmould-A trustworthy manufacturer of brackets injection molding
When it comes to custom brackets injection molding , FowMould is a reputable and authoritative institution that provides services to numerous industries in terms of accuracy, quality, and expertise. We have extensive experience in this field and have earned a reputation for consistently delivering excellence on every project.
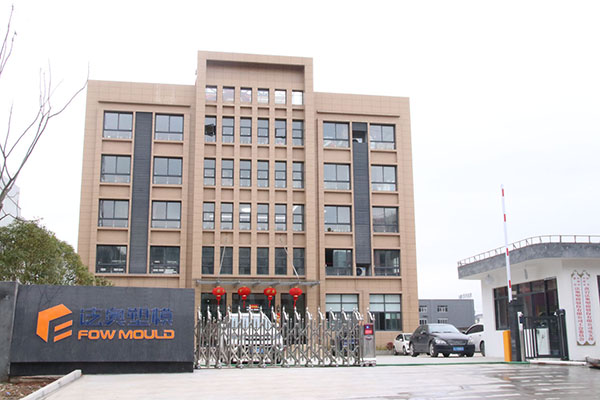
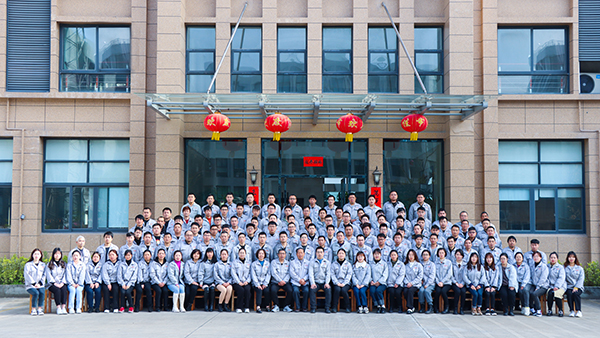
FowMould's Pledge to Excellence
Small Batch Customization
FowMould embraces the unique needs of each customer. They offer custom bracket services for small batch production, ensuring top-notch quality while meeting different requirements.
Good Reputation
Their good reputation is built on years of rich experience in injection molding. They have impeccable service, consistent product quality, and a commitment to meeting delivery deadlines. At the same time, they take pride in the trust they have established with their customers, which demonstrates their reliability as an injection molding manufacturer.
Extensive Injection Molding Experience
With the help of FowMould’s rich experience in injection molding, a team composed of professional engineers and technicians utilizes advanced equipment and the latest CAD software to manufacture flawless custom molds and high-quality brackets.
Conclusion
In summary,bracket injection molding have been widely used in various industries due to their precision, versatility, and cost-effectiveness. They provide consistency and high scalability. Whether it is small-scale production or large-scale production, they are efficient and practical solutions. In the fields of automotive parts, construction hardware, home goods, etc., they have brought infinite possibilities to global designers and manufacturers.
By choosing FowMould for your bracket needs, you are selecting a product that combines precision, versatility, and scalability. With their extensive experience in this field, they are committed to ensuring customer satisfaction by providing high-quality custom bracket injection molding that meet your unique requirements.