Chemical resistant plastic is essential in numerous industrial and commercial applications where exposure to harsh chemicals, solvents, and acids is common. From chemical processing to laboratory equipment and medical devices, these materials play a vital role in ensuring the safety and longevity of critical components.
This blog will explore the world of plastics resistant to chemicals, and introduce the elements to consider when choosing the right chemical-resistant plastic for your specific needs, including chemical compatibility, temperature, exposure time, durability, and chemical concentration.
Two Types of Recommended Chemical Resistance Plastics
Selecting the right plastic material for a specific application is crucial, especially when considering the chemical resistance of plastic. Standard performance plastics such as PVC, PP, and HDPE are cost-effective and have good resistance to a wide range of chemicals.
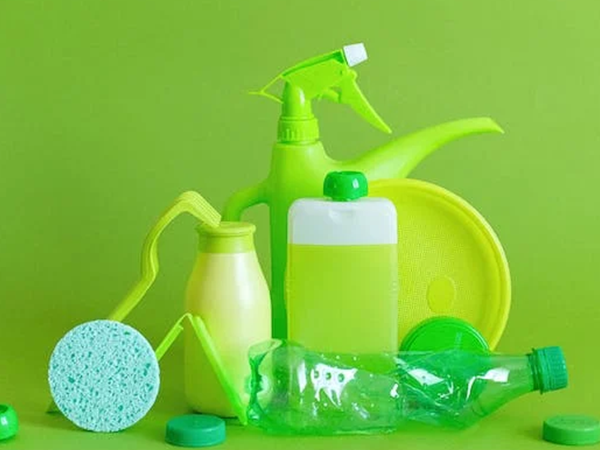
Standard Performance Chemical-resistant Plastics
Standard performance chemical-resistant plastics are typically less expensive and have good resistance to a wide range of chemicals. Here are some commonly used standard performance plastics.
- PVC (polyvinyl chloride) – PVC is a versatile and cost-effective plastic material with good chemical resistance to acids, alkalis, and some organic solvents. PVC is commonly used in piping, tanks, and linings.
However, the chemical resistance of PVC can vary depending on the specific chemicals it is exposed to and the concentration and temperature of those chemicals.
But there is still one thing that is noteworthy: PVC may not be suitable for use with some solvents or chemicals, such as aromatic hydrocarbons and chlorinated hydrocarbons, which can cause the material to degrade.
- PP (polypropylene) – PP is another popular plastic material that has excellent resistance to acids, alkalis, and organic solvents. PP is commonly used in chemical processing equipment, laboratory equipment, and storage tanks.
Some of the chemicals that PP is highly resistant to include hydrochloric acid, sulfuric acid, nitric acid, sodium hydroxide, and many organic solvents such as acetone, benzene, and toluene. PP is also highly resistant to moisture, making it ideal for use in wet environments.
However, it is important to note that PP may not be suitable for use with some highly concentrated oxidising acids, such as nitric acid above 90% or sulfuric acid above 70%.
- HDPE (high-density polyethylene) – HDPE is a tough and rigid plastic material with excellent chemical resistance to various acids, alkalis, and organic solvents. HDPE is commonly used in chemical storage tanks, piping systems, and outdoor applications.
Some of the highly resistant chemicals that HDPE uses include sulfuric acid, hydrochloric acid, sodium hydroxide, and many organic solvents such as benzene, toluene, and xylene. HDPE is also highly resistant to moisture and is often used in applications where water is present.
High-Performance Chemical-resistant Plastics
A high-performance chemically resistant plastic is typically more expensive than standard performance plastics. It has superior chemical resistance to a wide range of aggressive chemicals. Here are some of the commonly used high-performance plastics.
- PVDF (polyvinylidene fluoride) – PVDF is highly resistant to temperature changes and has a high melting point, making it suitable for use in high-temperature applications. It is a high-performance plastic material that has excellent chemical resistance to acids, alkalis, and organic solvents.
Some of the chemicals that PVDF is highly resistant to include hydrochloric acid, sulfuric acid, nitric acid, sodium hydroxide, and many organic solvents such as acetone, benzene, and toluene. PVDF is also highly resistant to UV radiation, ozone, and weathering, making it ideal for outdoor applications.
- PTFE or Teflon (polytetrafluoroethylene) – PTFE is a well-known high-performance plastic material that has excellent chemical resistance to acids, alkalis, and organic solvents. PTFE is commonly used in chemical processing equipment, laboratory equipment, and medical applications.
Some of the chemicals that PTFE is highly resistant to include hydrochloric acid, sulfuric acid, nitric acid, sodium hydroxide, and many organic solvents such as acetone, benzene, and toluene. PTFE is also highly resistant to UV radiation, and weathering, and is non-reactive to most chemicals.
Chemical | PVC | PP | HDPE | PVDF | PTFE |
Hydrochloric Acid | Good | Good | Fair | Excellent | Excellent |
Sulfuric Acid | Fair | Good | Good | Excellent | Excellent |
Nitric Acid | Fair | Good | Good | Excellent | Excellent |
Acetic Acid | Good | Good | Excellent | Excellent | Excellent |
Ammonia | Good | Excellent | Good | Excellent | Excellent |
Sodium Hydroxide | Good | Excellent | Good | Excellent | Excellent |
As shown in the chemical resistance chart for plastics, PVDF and PTFE offer the highest chemical resistance. At the same time, PVC and HDPE are suitable for low concentration chemical exposure. PP offers good chemical resistance across various chemicals, making it a versatile choice for many chemical-resistant applications.
Elements to Consider When Choosing Chemical Resistant Plastics
Determining thechemical resistance of plastic material requires careful consideration of several factors, such as exposure time and chemical concentration. Considering these factors, the appropriate plastic material can be selected to ensure reliable and safe performance in the intended application.
Material | Temperature Range | Exposure Time | Chemical Concentration | Exposure Area | Chemical Compatibility |
polyvinyl chloride (PVC) | -10°C to 60°C | Short-term | Low concentration of Acids, alkalis, organic solvents | Small to large | Good |
Polypropylene (PP) | -10°C to 100°C | Short-term | Low concentration of Acids, alkalis, organic solvents | Small to large | Good |
High-Density Polyethylene (HDPE) | -50°C to 80°C | Short-term | Low concentration of Acids, alkalis, organic solvents | Small to large | Good |
Polyvinylidene Fluoride (PVDF) | -40°C to 150°C | Long-term | High concentrationof Acids, alkalis, organic solvents | Small to large | Excellent |
Polytetrafluoroethylene (PTFE or Teflon) | -200°C to 260°C | Long-term | High concentration of Acids, alkalis, organic solvents | Small to large | Excellent |
Temperature
It’s vital to match the container’s material to the chemical’s temperature range to ensure it can withstand the conditions. One way to do this is to consult material datasheets or ask plastic manufacturers for advice. By taking these steps, you can avoid a “meltdown” and keep your chemicals safely contained.
For example, polypropylene (PP) can withstand temperatures up to 100°C, polyvinylidene fluoride (PVDF) can withstand temperatures up to 150°C. On the other hand, polytetrafluoroethylene (PTFE or teflon) can withstand temperatures as high as 260°C.
Exposure Time
How long plastics are left exposed to chemicals can determine to a large extent, the effect of the chemical on the plastic. Short-term exposure to a chemical may not significantly impact the plastic material, while long-term exposure may cause degradation, swelling, or chemical attack.
For example, high-density polyethylene (HDPE) can withstand short-term exposure to concentrated acids, while PVDF and PTFE are suitable for long-term exposure to aggressive chemicals.
Chemical Concentration
The concentration of the chemical is another crucial factor to consider when selecting a chemical resistant plastic. Some plastics may perform well in low chemical concentrations but may degrade or fail in higher concentrations. Therefore, it is essential to determine the concentration of the chemical and its compatibility with the plastic material.
For example, PVC, PP and HDPE can withstand low concentrations of acids and alkalis, while PVDF and PTFE are suitable for high concentrations of aggressive chemicals.
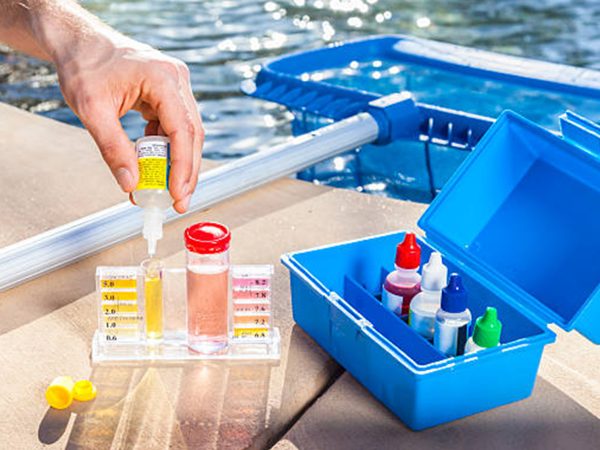
Exposure Area
The exposure area of the plastic material to the chemical is also an important factor to consider. Different plastics have different resistance to chemical exposure depending on the type and location of exposure.
For example, PVC is resistant to acid exposure in piping systems but may not perform well in exposure to concentrated acids in a storage tank.
Chemical Compatibility
Finally, it is essential to consider the compatibility of the plastic material with the specific chemical. Different plastics have different ways they react to chemicals. Some plastics may create a chemical bond with plastics. Some plastics may be incompatible with certain chemicals, leading to degradation or failure.
For example, polycarbonate (PC) may not be suitable for exposure to chlorinated solvents, while PTFE is highly resistant to a wide range of aggressive chemicals.
Choose Your Right Chemical Resistance Plastics
Chemical-resistant plastic materials have a wide range of applications in various industries, including construction, chemical, medical, food, automotive, and electronics. The appropriate material selection depends on the specific chemical resistance properties required for the application.
Food Industry
High-density polyethylene (HDPE) is commonly used for packaging food products due to its moisture, chemicals, and puncture resistance.
Polypropylene (PP) is another popular material for food packaging due to its high clarity and resistance to heat.
Polytetrafluoroethylene (PTFE) is also used in the food industry because of its non-stick properties and chemical resistance. PTFE is used to coat baking sheets, waffle irons, and other cooking equipment.
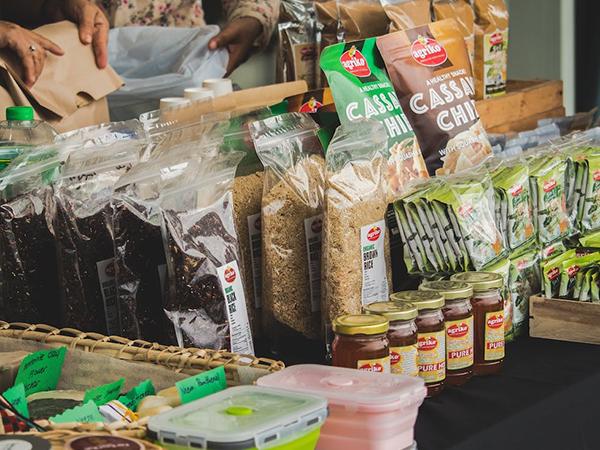
Medical Industry
Conditions such as sterilization compatibility, durability, plastics chemical resistance, and compliance with regulatory requirements is very important in choosing plastics for medical industry use.
Medical devices and equipment must be able to withstand various sterilization methods, such as autoclaving, gamma irradiation, and ethylene oxide gas sterilization. Materials such as PP and PE offer good sterilization compatibility and are commonly used in medical applications.
Take the PTFE material as an example, this plastic is used in medical devices such as catheters and implants because of its biocompatibility, low friction, and non-stick properties.
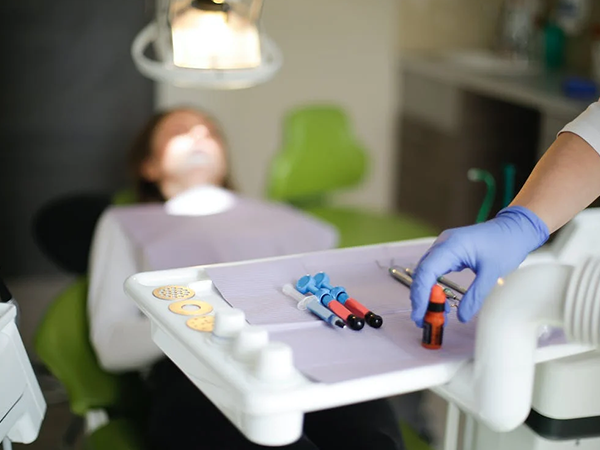
Construction Industry
Construction materials must be able to withstand exposure to the elements, including UV radiation, rain, and wind. Materials such as PVC and polycarbonate offer good weather resistance and are commonly used in construction applications.
It is important to verify that the selected acid resistant plastic material meets all relevant regulatory requirements.
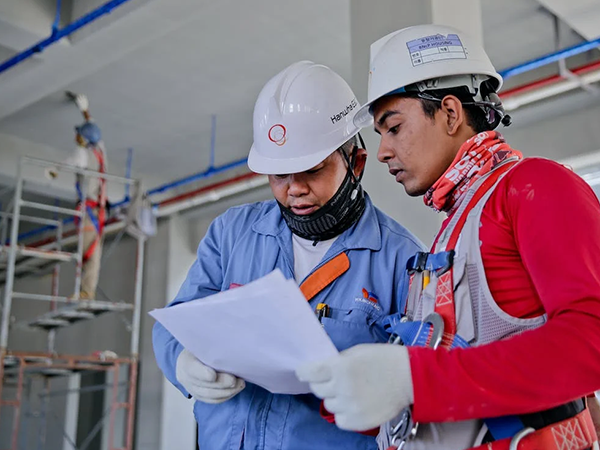
Benefits of Customizing Chemical Plastic Parts By Injection Moulding
Custom injection molding is a popular manufacturing process for producing high-quality and complex plastic parts in large quantities. The following are some reasons for selecting plastic injection molding to manufacture plastic parts.
Flexibility
Plastic injection molding is very popular in plastic fabrication because of the high degree of flexibility in terms of design, materials, and finishes. The injection moulding process can create parts with intricate designs and details that are difficult to achieve with other manufacturing methods.
Efficiency
Once the mold is created, the process can be automated, which reduces labor costs and increases production speed. Moreover, the injection molding process generates minimal waste, as any excess material can be reused or recycled.
Consistency
Injection molding offers consistent and repeatable part production, which is important for maintaining high-quality standards. Using omputer-controlled machines ensures that each part is identical to the previous one, regardless of the production volume.
Cost-Effectiveness
Plastic injection molding can be a cost-effective manufacturing process for producing high-volume parts. The initial cost of creating a mold may be high, but the cost per part decreases with higher production volumes. The use of automated processes reduces labor costs.
Quality
The injection molding process produces high-quality parts that have a smooth surface finish and tight tolerances. Additionally, computer-controlled machines ensure that each part meets the required specifications and finishes.
Choose FOW Mould as Your Chemical Resistant Plastic Manufacturer
FOW Mould is a leading company that has been in the business of manufacturing chemically resistant plastic all around the globe. The company is well equipped to bring injection molded product ideas into reality for a wide range of industries and applications.
FOW Mould can provide design, customisation and injection molding services for all plastic materials mentioned above, and can also enhance the corrosion resistance of other plastic materials by using additives, so customers have a high degree of freedom when selecting materials.
We understand that selecting suitable material for every project is critical, which is why we work closely with different clients to offer expert guidance and support throughout the process.
In addition to the standard range of materials, we also offer enhanced corrosion resistance through the use of additives, giving our customers greater flexibility and freedom in their material selection.
Conclusion
When selecting a chemical resistant plastic, it is important to consider factors such as the type and concentration of the chemicals involved and the temperature and degree of exposure of the plastic to chemicals. Other factors, such as cost, availability, and ease of processing may also be important.
Ultimately, the best choice for your specific application will depend on a combination of these factors and your unique requirements and constraints. FOW Mould company offers the best quality PVC, PP, HDPE, PVDF, and PTFE materials and customisation of other plastic materials suitable for different applications.
Contact FOW Mould today to learn more about our services and get a quote!